All published articles of this journal are available on ScienceDirect.
Mechanism of Localized Corrosion of Steel Pipe Pile Foundation for Offshore Wind Turbines and Corrosive Action
Abstract
The wind turbine foundation serves as a permanent construction in the harsh marine corrosive environment, its anti-corrosion design is essential to the safe use of the wind turbine structure. At present, there is a significant controversy over the local corrosion mechanism (such as pitting corrosion, and crevice corrosion) and its diffusion mechanism in the academic circle. In the paper, the Faraday electrochemistry formula was used to compute the local corrosion degree of the steel pipe pile for the wind turbine and obtain the general corrosion equivalent. The local corrosion effect of the offshore steel pipe pile for the wind turbine was converted into homogeneous corrosion thickness loss of certain length, and then the ultimate strength of the offshore steel pipe pile foundation for the wind turbine was analyzed under the conditions of local corrosion. The result indicates that the maximum ultimate strength reductionof the steel pipe pile for the wind turbine induced by the local corrosion in the splash zone is 80.8% of the non-corrosive ultimate strength. The maximum ultimate strength reduction of the steel pipe pile for the wind turbine induced by the local corrosion in the continuous immersion zone is 63% of the non-corrosive ultimate strength. Once the local corrosion rate in the splash zone exceeds 10%, the ultimate strength of the steel pipe pile for the wind turbine will exhibit a negative exponential decrease. The local corrosion in the continuous immersion zone has a huge effect on its ultimate strength. There are no significant signs of the structural strength loss. The areas prone to local corrosion should be prioritized in anti-corrosion design of the steel pipe pile for the wind turbine.
INTRODUCTION
Offshore wind power resources serve as renewable green energy resources. Rapid development of the offshore wind power industry is the main direction for the development of clean energy. However, offshore wind power plants are in the marine environment and the hydrological, meteorological, and submarine geological conditions are complex making it difficult to construct offshore wind power plants. Particularly, the wind turbine foundation as the major structure is in the marine corrosive environment for a long period of time. Thus, anti-corrosion of the wind turbine foundation is one of the problems to be first solved in construction of wind turbines.
To solve the highly corrosive effect of the marine environment on the wind turbine foundation, many scholars have been studying the corrosion resistance of the offshore steel structures. For example, R. Jeffrey [1], et al. studied the corrosion rate of metal in the marine environment. J.H. Kim Kim J H [2], et al. studied the effect of alloy elements on the corrosion resistance of steel. X.-T. Wang [3], et al. studied the corrosion rate of the alloy steel by conducting corrosion tests for different types of alloy steel. J.-L. Ma [4] and S.M.A. Shibli [5], et al. studied the principle for alloy steel corrosion. B.-R. Hou [6] has conducted a great deal of experimental research on the characteristics of metal corrosion and systematically studied the marine corrosion theory. At present, there is some research on corrosion of various traditional maritime steel structures but there is little research on corrosion and protection of the offshore wind turbine foundation. And there is nearly no research on the rules of effect of corrosion on the wind turbine foundation. Particularly, the academic circle have a significant controversy over the local corrosion mechanism (such as pitting corrosion and crevice corrosion) and its diffusion mechanism . In addition, the detailed and complete experimental data of local corrosion of steel structures is sorely lacking. So that, there is no convincing mathematical model for the local corrosion
Traditionally, the effect of local corrosion was considered by converting the local corrosion into an equivalent homogeneous corrosion through certain standards such as equal area loss, equal strength loss etc. However, there is a significant controversy over the definition of “equivalent homogeneous corrosion thickness”. TSCF [7] (1984) obtained an equivalent thickness computational formula involving multiple parameters such as boundary conditions, steel plate dimensions, bending rigidity, quality etc. based on the bending test and theoretical derivation after pitting corrosion occurred to the steel plate. As the equivalent corrosion thickness method is still open to discussion in correctness and application scope, and it is inconvenient for use because of too many influencing factors. R.E. Melchers [8, 9] (2004-2005) created extreme value distribution (Generally Gumbel distribution) for the maximum pit depth of the steel structure corrosion based on the pitting corrosion test in the seawater continuous immersion zone. Based on the “phenomenological model”, he proposed the probabilistic model of maximum pit depth. Subsequently, based on the measured corrosion data, he found that the pitting corrosion with larger corrosion pit depth was subject to normal distribution. Hence, he proposed a double-probability density model to describe the maximum pit depth of pitting corrosion. However, the double-probability model of pitting corrosion studied by Melchers was local corrosion of under the anaerobic environment. It was inconsistent with the local corrosion of the offshore steel pipe pile for the wind turbine. Thus, how to correctly and simply deal with the effect of local corrosion in reliability computation for the marine structure has been increasingly becoming one of the research highlights in recent years.
1. CORROSION MECHANISM OF STEEL PIPE PILE FOUNDATION FOR OFFSHORE WIND TURBINES AND EQUIVALENT TREATMENT METHOD FOR LOCAL CORROSION
The types of corrosion of the steel pipe piles for the wind turbine in the marine environment can be divided into homogeneous corrosion and local corrosion. It is generally considered that homogeneous corrosion is one of the major causes of damage to offshore steel pipe pile for the wind turbine. Local corrosion includes pitting corrosion, crevice corrosion, impingement corrosion, cavitation corrosion, and galvanic corrosion. Occurrence of such corrosion behaviours is often associated with structural design or steel smelting. However, in fact, corrosion of steel pipe piles is not homogeneous in the marine environment. Irregular shapes such as corrosion pits, corrosion salient points etc. will be present on the surface following local corrosion (such as pitting corrosion).
Because the lack of the existing local corrosion models, there is no complete and reliable mathematical models are available for selection. In the paper, the Faraday electrochemistry formula is used to compute the corrosion degree of the steel pipe pile for the wind turbine and obtain the general corrosion equivalent. The local corrosion effect of the offshore steel pipe pile for the wind turbine is converted into homogeneous corrosion thickness loss of certain length for computational analysis of the ultimate strength of the offshore steel pipe pile foundation for the wind turbine under the conditions of corrosion.
Faraday's law: Electrochemical corrosion cells are formed in the corrosive medium as a result of metal inhomogeneity; the metal is dissolved at the anode of the cells and deposited at the cathode. The Expression is:
![]() |
(1) |
Where, m is the mass of the corroding metal (/g), M is the molar mass of Fe (/ g/mol), Q is the corrosion electricity(/ C), z is the number of electrons, and F is the Faraday constant, F=96500 C/mol.
In Faraday's law, the local corrosion salient points are not considered to be corroded. They still exist in the form of steel but have no bearing capacity. Thus, these corrosive salient points should be subject to equivalent corrosion treatment.
2. COMPUTATIONAL MODEL OF LOCAL CORROSION ACTION OF STEEL PIPE PILES FOR OFFSHORE WIND TURBINES
In term of local corrosion, we mainly consider the ultimate strength reduction resulting from local corrosion of the steel pipe pile foundation for wind turbines in the splash zone and continuous immersion zone. The local corrosion of the steel pipe pile for the wind turbine is simulated by equivalent reduction of the wall thickness of the steel pipe. The Faraday's electrochemical law is used to compute the corrosion equivalent of the steel pipe pile sections and obtain the equivalent local corrosion rate.
2.1. Computational Model
The single steel pipe pile foundation for the wind turbine in Donghai Bridge offshore wind power plant is taken as an example. The large scale general finite element analysis software ANSYS is used to establish a three-dimensional finite element model for the wind turbine foundation and groundwork. As shown in Fig. (1), the total length of a single steel pipe pile is 65m, diameter is 4.0m, wall thickness of steel pipe pile is 50mm, seabed insertion depth is 40m, average seawater depth is 15m.
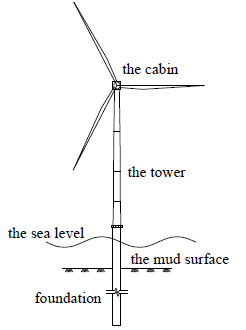
The Pipe59 units are used as the steel pipe piles above the sea mud level. The Pipe16 units are used as the steel pipe piles below the sea mud level. For the foundation soil body, the COMBIN39 nonlinear spring element is used to express the P-y curve for interaction between the steel pipe pile and the soil around pile. Based on the checking calculation result of the axial bearing capacity of the pile foundation, the axial bearing capacity is much greater than the vertical load. Thus, it is considered that no displacement occurs in the axial direction. The bottom of the pile foundation is axial fixed, and the outside of the pile foundation is radial spring. Based on the dimension ratio of the steel pipe piles, the computational models and grids are divided as shown in Fig. (2).
2.2. Calculation Parameters
2.2.1. Environmental Parameters
Average seawater depth is 18m, seawater density is 1030kg/m3, wind speed is 38m/s at 8m above the seal level, significant wave height is 5.8m, significant wave period is 7.4s,flow rate on the sea surface is 1.73m/s, middle flow rate is 1.37m/s, and bottom flow rate is 0.95m/s. It is the soft clay at 10m below the mud surface.
2.2.2. Material Parameters
The steel pipe piles use low-alloy high-strength steel Q345E with yield strength of 345MPa, much lower than soil strength. Thus, the linear material model can be used. Elasticity Modulus is 2.1×105MPa, Poisson's ratio is 0.3, and low-alloy steel density is 7.85×103kg/m3.
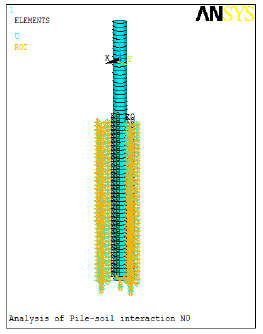
2.3. Working Condition of Calculation
The accidental seismic load conditions, extreme load conditions, normal load conditions should be considered in calculation of the groundwork design load for the offshore wind power. In consideration of the minor combined effect of the accidental seismic load and corrosion of the wind turbine foundation, the paper is intended to study the effect of corrosion on strength and stability of the pile foundation structure under the conditions of extreme loads and normal operation. The extreme load condition is the combined effect of the extreme loads transferred from the upper structure plus other extreme loads applied on the foundation structure. The normal operation load condition is the combined effect of normal operation loads transferred from the upper structure plus other normal operation loads applied on the foundation structure. The loads corresponding to various working conditions are shown in Table 1.
Load on Pile Top | The Horizontal Force /KN |
The Vertical Force /KN |
Bending Moment /KN·m |
---|---|---|---|
Extreme Load Condition | 208 | 4700 | 13324 |
Normal Operation Condition | 2005 | 4700 | 112332 |
2.4. Simulation of Local Corrosion Action
In accordance with the international standard ISO 12944-2, the corrosion degree of the splash zone is Im2. It is the zone with the highest corrosion degree in the marine environment. The impact of the splashed bubbles in the spindrift on the surface of the pile foundation accelerates the damage to coating and the passivating film of the metal surface and forms the source of pitting corrosion. Based on mechanism of the corrosion crack propagation of the steel pipe pile for the wind turbine, the corrosion crack propagates towards the interior of the structure along the metal crystal boundary under the action of the reciprocation stress following formation of a corrosion source on the surface of the pile foundation. Moreover, the oxygen supply is sufficient in the section. Oxygen depolarization facilitates corrosion of steel structure. The wind and large temperature difference promotes the rapid development of corrosion of the pile foundation structure. Based on the tests for the low-alloy steel in a certain sea area in the East China Sea conducted by Institute of Oceanology, Chinese Academy of Sciences, the annual average corrosion rate in the splash zone can reach 0.3-0.8mm/a.
Local corrosion is simulated by means of equivalent reduction of the local wall thickness of the steel pipe pile in the splash zone. The middle part (5m above the sea level on average) of the steel pipe pile in the splash zone is used to simulate local corrosion. The local corrosion length is 0.1m. Formula (1) is used to compute the corrosion equivalent. The steel pipe pile of 0.1m length is subject to an equivalent corrosion rate for reduction of the wall thickness of the steel pipe pile. If the local corrosion rate is 5%, the equivalent steel pipe wall thickness will be reduced by 8%. If the local corrosion rate is 10%, the equivalent steel pipe thickness will be reduced by 20%. If the local corrosion rate is 15%, the equivalent steel pipe thickness will be reduced by 36%, as shown in Table 2. Considering that the maintenance period of the corrosion protection system in the splash zone is generally not over 20 years, the research for a larger corrosion rate is not required.
Corrosion Rate /% |
2 | 5 | 10 | 12 | 15 |
Equivalent Reduction Rate /% |
2.4 | 8 | 20 | 25 | 36 |
Equivalent Wall Thickness /mm |
1.7 | 4 | 10 | 12.5 | 18 |
3. ANALYSIS OF THE LOCAL CORROSION ACTION IN THE SPLASH ZONE
Finite element computation was performed for the strength of the steel pipe piles for the wind turbines with different local corrosion rates in the splash zone under the ultimate load using the software ANSYS. The computational result was compared with that of the steel pipe pile for the wind turbine without corrosion under the ultimate load.
The analog computational results of different local corrosion rates of the steel pipe piles for the wind turbines under the ultimate load could be obtained on the basis of the finite element computation. The steel pipe pile at a length of 10m above the sea level was taken for contrastive analysis of the results. Node numbering was performed from the pile head in sequence. It was divided into ten sections. The site with local corrosion was between No. 4 Node and No.5 Node. The corrosion length was 0.1m. The internal stress and strain of the steel pipe pile under various local corrosion rates were compared as shown in Figs. (3 and 4).
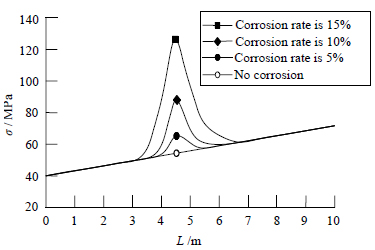
Based on the analog computational result of the local corrosion in the splash zone, the effect of the local corrosion action on the overall ultimate strength of the steel pipe pile for the wind turbine was analyzed as follows:
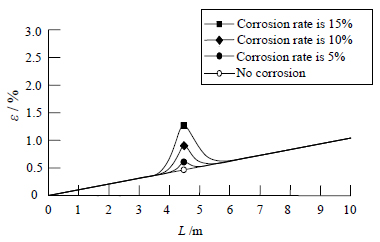
1) When the local corrosion rate Γ<10%, the stress of the corroded site was less than the maximum stress 92.2 Mpa of the non-corroded steel pipe pile under the ultimate load. Local corrosion will not affect the overall strength and stability of the structure of the wind turbine foundation.
2) When the local corrosion rate Γ=10%, the stress of the corroded site σ=91.8 Mpa, which approximated the maximum stress 92.2 Mpa. The second largest stressed area occurred.
3) When the local corrosion rate Γ>10%, the stress at the corroded site exceeded the maximum stress under the non-corrosion conditions. The ultimate strength of the structure of the wind turbine foundation would be affected. When Γ=15%, the stress of the corroded site σ=132 Mpa, the strain of the corroded site was 3.8 times the strain under the non-corrosion condition and the reduction in ultimate strength was 80.8% of the ultimate strength under the non-corrosion condition. The ultimate strength of the pile foundation structure reducing with the local corrosion rate in the splash zone is shown in Fig. (5). It was thus clear that corrosion hardly affected the steel pipe pile for the wind turbine before the local corrosion rate reached 10%. The ultimate strength of the steel pipe pile for the wind turbine exhibited a negative exponential decrease if the local corrosion rate exceeded 10%. In view of this, the concealed local corrosion of offshore steel pipe pile for the wind turbine should be specially considered in anti-corrosion design. An enhanced corrosion protection area should be provided.
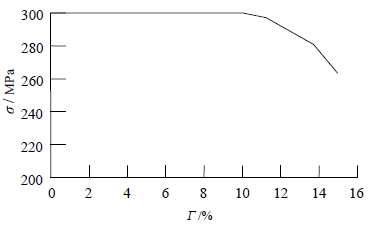
4. ANALYSIS OF THE LOCAL CORROSION ACTION IN THE SPLASH ZONE
For local corrosion of the offshore steel pipe pile for the wind turbine in the continuous immersion zone, full consideration should be given to the mechanical characteristics of the offshore steel pipe pile for the wind turbine under the ultimate load, i.e. the reduction in ultimate strength under the conditions of corrosion and coupling of the structural stress of the steel pipe pile. The stress and strain of the foundation of a single steel pipe pile for the wind turbine also occurred at the site with the maximum bending moment in the absence of corrosion. In term of the local corrosion of the steel pipe pile for the wind turbine in the continuous immersion zone, the worst conditions of the effect on the structural ultimate strength should be taken into consideration. The simulated local corrosion site of the steel pipe pile for the wind turbine in the continuous immersion zone was located at 1m above the sea mud level. The local corrosion length was 0.1m. The wall thickness of the steel pipe pile for the wind turbine was subject to equivalent reduction treatment as indicated in Table 2. Finite element computation was performed for the ultimate strength of the pile foundation structure in the continuous immersion zone in the presence of local corrosion. The computational result was compared with that of the steel pipe pile for the wind turbine in the absence of corrosion.
Finite element analogy computation of the local corrosion of the steel pipe pile for the wind turbine in the continuous immersion zone was performed to obtain the analog computational results of different local corrosion rates of the pile foundation. A length of the steel pipe pile of 10m above the corrosion site and a length of the steel pipe file of 10m below the corrosion site were taken respectively for ease of analysis. The nodes were numbered in a top-to-bottom sequence. The corroded site was located between No. 10 Node and No. 11 Node. The local corrosion length was 0.1m. The analogue computational results of local corrosion of the steel pipe pile for the wind turbine in the continuous immersion zone were compared. The curve for the internal stress developing with the local corrosion rate is shown in Fig. (6).
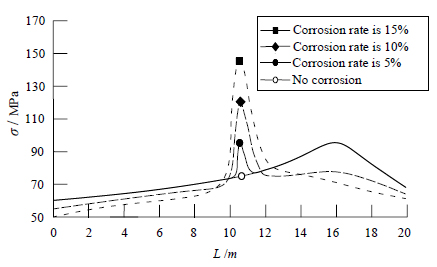
Based on the comparisons of the stress of the sections of the steel pipe pile for the wind turbine under different local corrosion rates, it was clear that:
1) When the local corrosion rate Γ<6%, the structural stress σ of the pile foundation of the corroded site was less than the maximum stress of the steel pipe pile in the absence of corrosion. No changes occurred to the maximum stress of the pile foundation structure following corrosion. The local corrosion did not affect the ultimate strength of the pile foundation structure.
2) When the local corrosion rate Γ=6%, the stress σ of the corroded site approximated the maximum stress of the pile foundation structure in the absence of corrosion. Then, the maximum stress of the steel pipe pile would deflect and move to the corroded site with the increasing of the corrosion rate, as shown in Figs. (7 and 8).
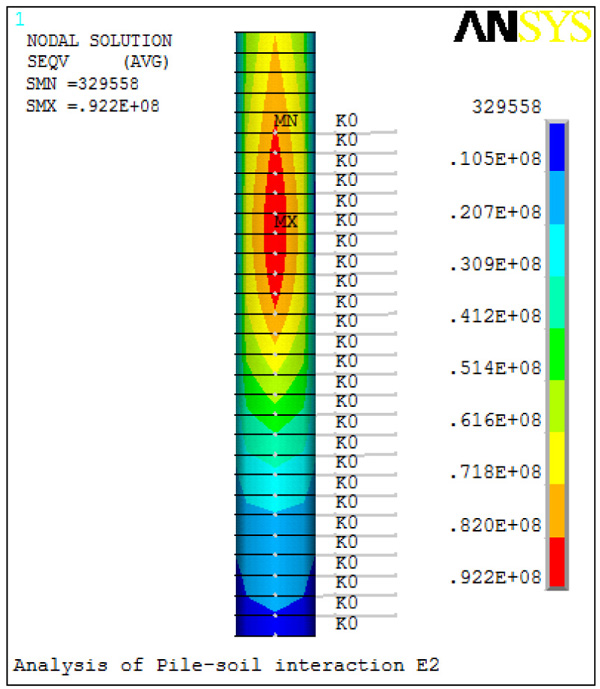
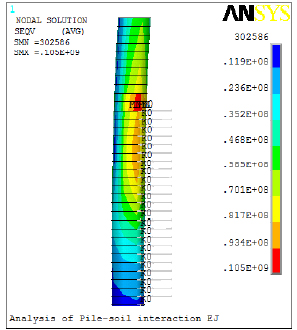
When the local corrosion rate no less than 6%, the ultimate strength of the pile foundation structure would be reduce sharply with the increase of the corrosion rate. When the corrosion rate Γ=15%, the ultimate strength of the pile foundation structure would be reduced to 63% of the ultimate strength in the absence of corrosion. Reduction in ultimate strength of the pile foundation structure under various corrosion conditions is shown in Fig. (9). It was thus clear that the local corrosion of the steel pipe pile for the wind turbine in the continuous immersion zone had a huge effect on its ultimate strength. There were no significant signs of the structural strength loss. The areas prone to local corrosion should be prioritized in anti-corrosion design of the steel pipe pile for the wind turbine.
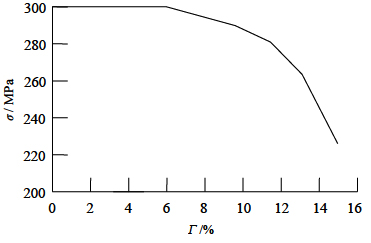
CONCLUSION
1) The Faraday electrochemistry formula is used to compute the local corrosion degree of the steel pipe pile for the wind turbine and obtain the general corrosion equivalent. The local corrosion effect of the offshore steel pipe pile for the wind turbine is converted into homogeneous corrosion thickness loss of certain length for computational analysis of the ultimate strength of the offshore steel pipe pile foundation for the wind turbine under the conditions of local corrosion.
2) The corrosion hardly affects the steel pipe pile for the wind turbine before the local corrosion rate reaches 10%. The ultimate strength of the steel pipe pile for the wind turbine exhibits a negative exponential decrease if the local corrosion rate exceeds 10%. Hence, the concealed local corrosion of offshore steel pipe pile for the wind turbine should be specifically considered in anti-corrosion design. An enhanced corrosion protection area should be provided.
3) The local corrosion in the continuous immersion zone has a huge effect on its ultimate strength. There are no significant signs of the structural strength loss. The areas prone to local corrosion should be prioritized in anti-corrosion design of the steel pipe pile for the wind turbine.
4) The result indicates that the maximum reduction in ultimate strength of the steel pipe pile for the wind turbine induced by the local corrosion in the splash zone is 80.8% of the non-corrosive ultimate strength. The maximum reduction in ultimate strength of the steel pipe pile for the wind turbine induced by the local corrosion in the continuous immersion zone is 63% of the non-corrosive ultimate strength.
CONFLICT OF INTEREST
The authors confirm that this article content has no conflict of interest.
ACKNOWLEDGEMENTS
The authors gratefully acknowledge the financial supports from the Natural Science Foundation Project of Chongqing under grant No.CSTC2013JJB0003 and the Specialized Research for the Doctoral Program of the Ministry of Education under grant No.20125522110004. We appreciate all institutions and individuals that have provided support for this paper.