All published articles of this journal are available on ScienceDirect.
Nonlinear Numerical Analyses of a Fabricated Connection of Concrete-Filled Steel Column to Steel Beam Under Low-Reversed Cyclic Loading
Abstract
Introduction:
Based on FEM program ABAQUS, three-dimensional numerical models of a fabricated connection of concrete-filled steel column to steel beam under low-reversed cyclic loading were established by considering both nonlinearity of material and geometry. Effects of stiffen ring plate, axial compression ratio and backing plate on the hysteresis curves, skeleton curves, ductility coefficient and energy dissipation coefficient were analyzed respectively.
Methods:
Furthermore, parametric analyses with comparison were also conducted to discuss the mechanical characteristics and damage mechanism of the fabricated connection.
Results:
The results show that there are clear stress concentrations near the area of bolt holes in beam flange. The increase in width of ring plate and the shape change of ring plate from square to circle can both improve the ductility and the characteristics of hysteretic behavior. Besides, the backing plates have positive effects on the hysteretic characteristics, ductility and energy dissipation of the CFST column connections. Oppositely, the increase in axial compression ratio contributes negatively to both the bearing capacity and deformation performance of the connection specimens.
Conclucion:
It can be concluded that the fabricated connection displays good working performance relating to hysteretic characteristics, energy dissipation and ductility, which can be hopefully applied and provide reference to engineering practice.
1. INTRODUCTION
In the last thirty years, concrete-filled steel tubular (CFST) columns were widely employed as compression materials in high-rise buildings, long-span bridges, and underground structures due to the advantages of good performance, construction convenience, fine fire resistance as well as low construction cost [1, 2]. CFST columns are known to increase the strength and stiffness of the section by confining the concrete panel in the steel tube. With the application of CFST columns into engineering practices, different types of connections have been developed to connect flange beams to steel tube columns [3, 4]. According to the “specification for design and construction of a steel pipe concrete structure (CECS28:90),” beam-column connections should be fine and satisfy the design criterion of strong column and weak beam. The corresponding modes of load transfer and construction technology are two key aspects of connection design, as emphasized by Ricles and Gregory et al. [5, 6]. Researchers have conducted many studies on CFST column and beam connections. Numerical analyses are adopted by most researchers in analyzing the deformation capacity of CFST column-beam connections aside from cyclic loading tests.
The seismic performance of concrete-filled steel square tube column connection with H beams was investigated by Morino et al. [7]. The ductility and energy dissipation of concrete-filled steel square tubular column connections were discussed [8-11]. Moreover, both the characteristics of the stress concentration and plastic hinge in the embedded type of CFST column connections were reported by Beutel et al., Chiew et al., and Li et al. [12-14]. Based on previous engineering practice and research, the effects of geometric features of connections, axial compression ratio, and other factors on the performance, such as ductility and hysteretic characteristics of CFST column connections were discussed [15-20]. However, most presented types of CFST column connections are connected through a welding technique. This may lead to construction inconvenience and frameworks inefficiency, particularly for the complicated and structures. Meanwhile, fabricated beams with the connector of high strength friction grip bolt are promising for designing CFST column connections, which are easily operated and can satisfy the strength requirements in engineering materials. Moreover, research on CFST column connections with assembled beams without welding is limited both in theoretical analysis and experimental investigation.
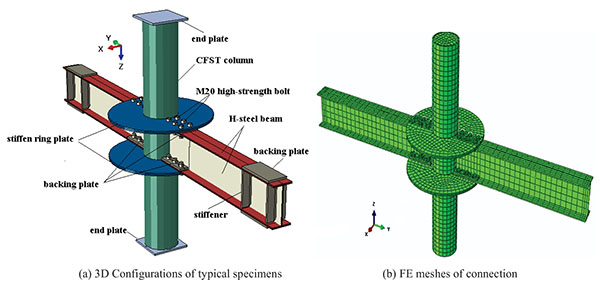
This work aims to investigate a new type of fabricated connection of concrete-filled steel column to steel beam by developing three-dimensional numerical models of the cross-shaped connection under low-reversed cyclic loading and carrying out parametric analyses to discuss the mechanical characteristics and the damage mechanism of the fabricated connection. Moreover, comparative analyses with experimental results are conducted to analyze the effects of the stiffen ring plate, axial compression ratio, and backing plate on hysteresis curves, skeleton curves, ductility coefficient, and energy dissipation coefficient.
2. MATERIALS AND METHODS
2.1. Numerical Model of the Proposed Connection
The computational model of the connections used in this research is shown in Fig. (1), in which both the three-dimensional configurations and the FEM meshes of connection are depicted. The detailed material properties of connections are listed in Table 1, and the strengths of concrete and steel are determined through tensional coupon tests. Six numerical specimens were developed according to the schedule of specimens listed in Table 2. Square ring plate was adopted in the specimen F12D3. The axial force for CFST column was of 5000 kN magnitude and applied through the axis of the steel tube. The cyclic loading according to a quasi-static cyclic displacement pattern was defined in terms of beam end displacement and was applied vertically to the H-beams based on the loading scheme in Fig. (2). The loading pattern was applied to each specimen until failure occurred.
Material | Material class | Young’s module (MPa) |
Poisson ratio | Yield strength of tension (MPa) |
Ultimate strength of tension (MPa) |
---|---|---|---|---|---|
Concrete | C60 | 3.6×104 | 0.2 | 35.738 | 64.39 |
Steel | Q345 | 2.1×105 | 0.24 | 310 | 448 |
Specimen | Backing plate | Column (mm) | H-beam (mm) | Axial compression ratio | Width of ring plate (mm) |
||
---|---|---|---|---|---|---|---|
Cross section | Length | Cross section | Length | ||||
H18D3 | with | ф180×8.00 | 1250 | 200×100×8×5.5 | 2080 | 0.3 | 180 (circular) |
H18W3 | without | ф180×8.00 | 1250 | 200×100×8×5.5 | 2080 | 0.3 | 180 (circular) |
H18D6 | with | ф180×8.00 | 1250 | 200×100×8×5.5 | 2080 | 0.6 | 180 (circular) |
H18W6 | without | ф180×8.00 | 1250 | 200×100×8×5.5 | 2080 | 0.6 | 180 (circular) |
H12D3 | with | ф180×8.00 | 1250 | 200×100×8×5.5 | 2080 | 0.3 | 120 (circular) |
F12D3 | with | ф180×8.00 | 1250 | 200×100×8×5.5 | 2080 | 0.3 | 127 (square) |
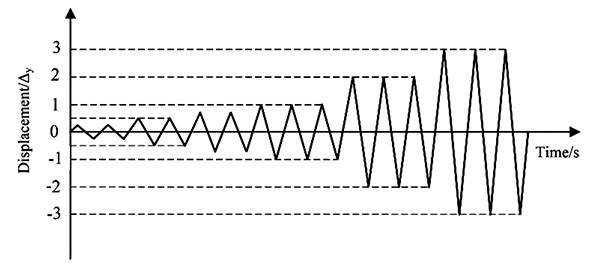
3. NUMERICAL RESULTS AND DISCUSSION
Fig. (3a-b) show the distribution of the Mises stress of connection H18D3 when the displacement load equals Δy. The stress amplitude in the beam flange is higher than that on the web. This is in accordance with the experimental description [21-23], which is measured in connection with the experiments through MTS servo loading system. A plastic zone is far away from the welding area due to the installation of the stiffen plate on the steel beam, and this can prevent the beam from rupture at the welding location. However, welding quality should be given importance during fabrication because the welding location still has stress concentration. The distribution of the Mises stresses of the CFST column in connection with H18D3 when the displacement load equals 3Δy is shown in Fig. (3c). As shown, an X pattern of stress concentration exists near the connection intersection. Moreover, the distribution of the Mises stress of the stiffen plate in connection with H18W6 when the displacement load equals 3Δy is shown in Fig. (3d). As shown, the stress variation along the axis of the steel beam is significant, and significant stress concentration exists near the contact area between the stiffen plate and the steel beam. Moreover, the improvement of the stiffen plate on the distribution of the forces of the connection, i.e., the existence of stiffen plate is helpful for the effective transfer of the load from the beam end to the CFST column.
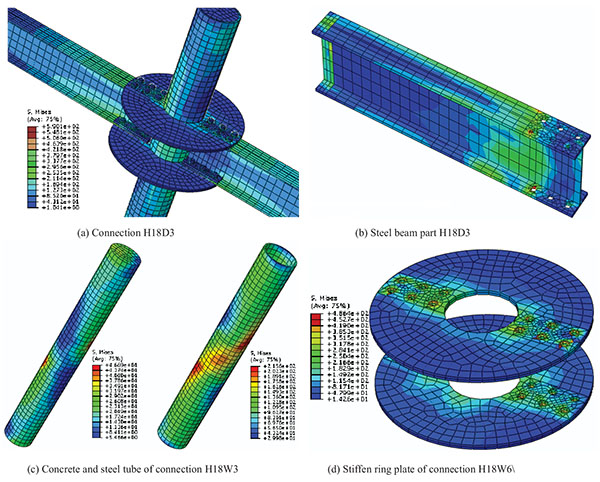
The comparisons of the P-Δ hysteretic curves between experimental data and computational results are shown in Fig. (4). The hysteretic characteristics of each specimen become more robust with the cyclic increase of displacements, indicating the fine deformation performance of the presented connections. Moreover, the increase in the width of the ring plate and the installation of the backing plate contribute positively to the bearing capacity of the connection specimens. For the idealization of the numerical model, without considering the initial imperfection of specimens due to fabrication, the hysteretic curves from the numerical results above are more regular than those from the experiments.
Fig. (5) shows the comparisons of the P-Δ skeleton curves between the experimental data and the computational results. Moreover, the increase in the width of the ring plate and the installation of the backing plate contribute positively to the bearing capacity of the connection specimens. Thus, the specimen with the square ring plate presents higher ultimate and failure loads than the specimen with the circular ring plates. Moreover, all specimens do not show significant degradation of stiffness and strength when loading reaches the ultimate state. That is, the working performance of this type of connection is good.
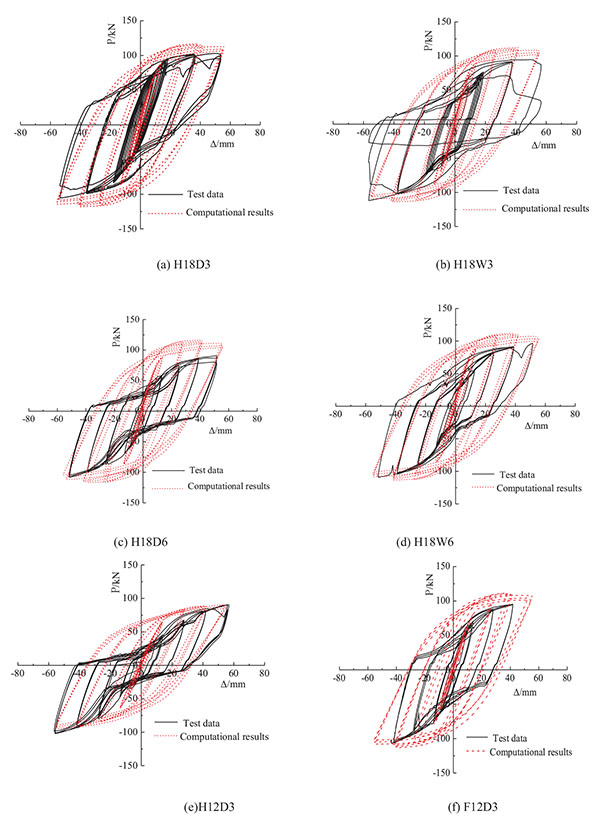
The comparisons of the typical index, including yield displacement, yield load, ultimate displacement, and ultimate load between experimental data, and computational results are listed in Table 3. Errors toward all typical indexes are minimal and within the acceptable scale. Given the idealization of numerical models without considering the imperfection of fabrication, the index errors of the yield state are less than those of the ultimate state. Integration of the comparisons of ductility coefficient and energy dissipation coefficient between the experimental data and the computational results are listed in Tables 4 and 5, which indicates that the connection presents good ductility and energy dissipation. All relating indexes satisfy the requirements of the building seismic code. Furthermore, all the index errors of the ductility coefficient and the energy dissipation coefficient between the experimental data and the computational results are minimal and within the acceptable scale.
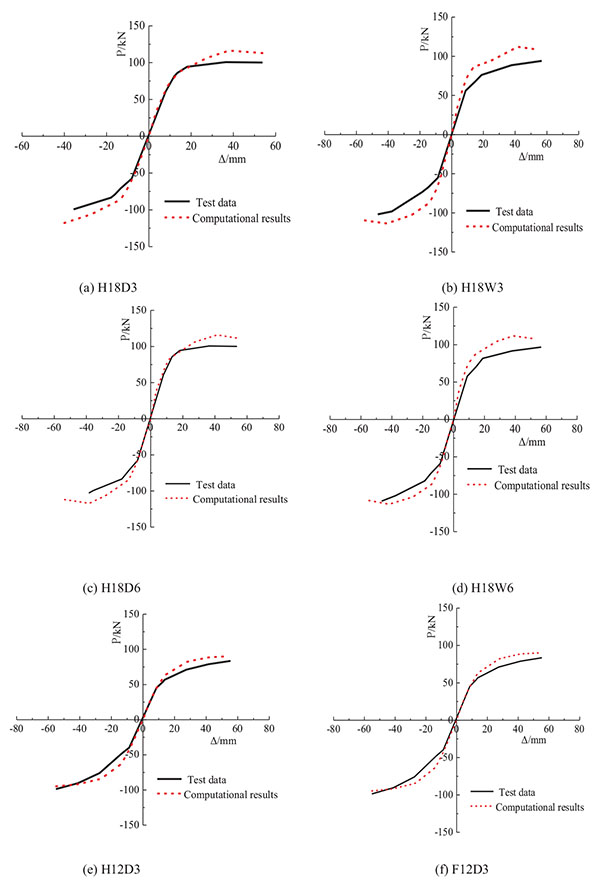
Specimen | Yield displacement (mm) | Yield load (kN) | Ultimate displacement (mm) | Ultimate load (kN) | ||||||||
---|---|---|---|---|---|---|---|---|---|---|---|---|
Test data | Numerical results | Error | Test data | Numerical results | Error | Test data | Numerical results | Error | Test data | Numerical results | Error | |
H18D3 | 17.92 | 15.2 | 15% | 92.71 | 89.75 | 3.2% | 58.33 | 55.04 | 5.6% | 99.84 | 112.59 | 13% |
H18W3 | 18.28 | 15.25 | 17% | 73.77 | 87.54 | 19% | 59.43 | 53.55 | 9.9% | 92.7 | 108.23 | 16% |
H18D6 | 16.98 | 13.34 | 21% | 93.69 | 83.11 | 11% | 54.52 | 53.87 | 1.2% | 100.57 | 111.11 | 10% |
H18W6 | 16.87 | 15.57 | 7.7% | 75.98 | 88.28 | 16% | 54.65 | 53.55 | 2.0% | 95.66 | 107.36 | 12% |
H12D3 | 14.76 | 13.65 | 7.5% | 59.02 | 61.97 | 4.7% | 59.49 | 54.03 | 8.7% | 83.11 | 90.21 | 8.5% |
F12D3 | 13.92 | 13.65 | 1.9% | 84.59 | 76.72 | 9.3% | 48.62 | 55.66 | 15% | 108.69 | 107.61 | 1.0% |
Specimen | Displacement ductility coefficient | Error | |
---|---|---|---|
Test data | Numerical results | ||
H18D3 | 3.27 | 3.62 | 10.09% |
H18W3 | 3.25 | 3.51 | 8.00% |
H18D6 | 3.21 | 4.04 | 26.85% |
H18W6 | 3.24 | 3.44 | 6.17% |
H12D3 | 4.03 | 3.96 | 8.44% |
F12D3 | 3.49 | 4.08 | 16.91% |
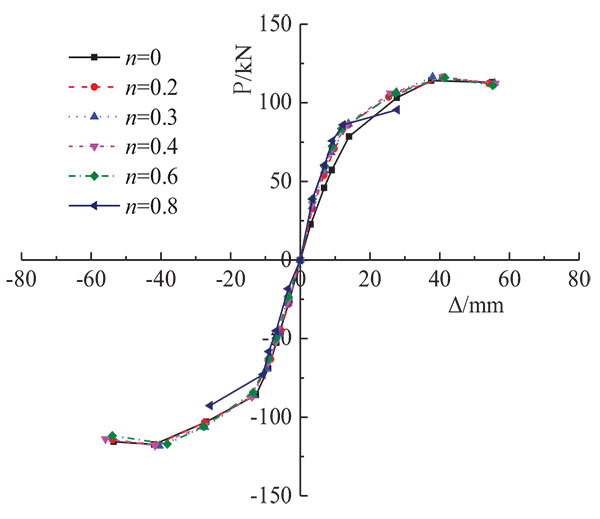
Based on the comparative analyses between the numerical results and the experimental data, further parametric analyses must be conducted using numerical extrapolation. The parameters are changed according to the specimen case H18D3.
Specimen | Displacement ductility coefficient | Error | |
---|---|---|---|
Test data | Numerical results | ||
H18D3 | 2.2149 | 2.4053 | 8.596% |
H18W3 | 1.9187 | 2.0486 | 6.771% |
H18D6 | 1.7571 | 1.8331 | 4.325% |
H18W6 | 1.752 | 1.8522 | 5.719% |
H12D3 | 1.6148 | 1.6613 | 2.88% |
F12D3 | 1.5106 | 1.6196 | 7.216% |
P-Δ skeleton curves under different compression ratio n are shown in Fig. (6). The increase of axial compression ratio has negative effects on the bearing capacity and the deformation performance of the connection specimens in accordance with what is displayed in the hysteretic curves above. Fig. (7) shows the P-Δ skeleton curves under different concrete strength. As shown, the working performance of the connection becomes worse when the steel tube has no concrete. That is, the existence of core concrete can significantly prevent the steel tube from buckling. Moreover, P-Δ skeleton curves under different tube thickness t are shown in Fig. (8). The bearing capacity increases with the increase of tube thickness. The influence of the tube thickness on the bearing capacity becomes negligible when the tube thickness reaches 8 mm.
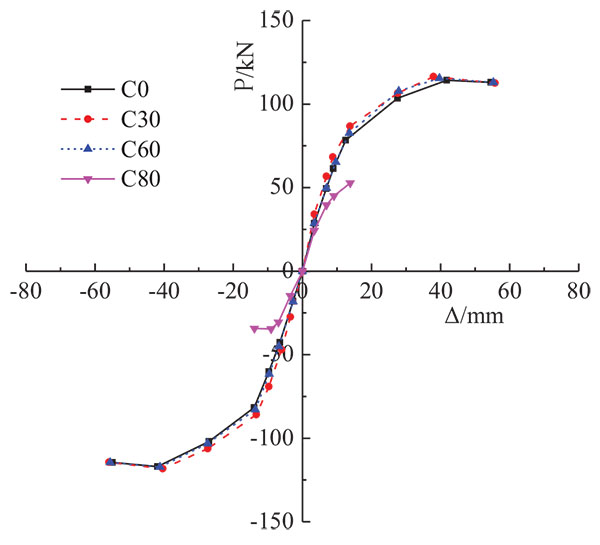
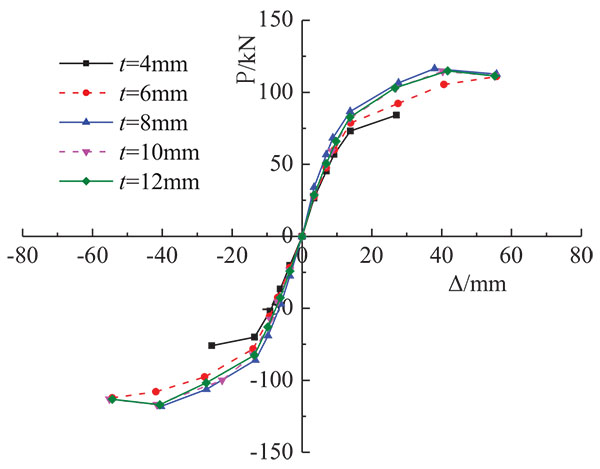
CONCLUSION
The present work investigated a new type of fabricated connection of concrete-filled steel column to a steel beam by developing three-dimensional numerical models of the cross-shaped connection under low-reversed cyclic loading. Parametric and comparative analyses with experimental results are also performed to discuss the mechanical characteristics and the damage mechanism. The fabricated connection is studied, and several conclusions are drawn, as follows:
- Clear stress concentrations exist near the area of the bolt holes and near the area of the beam flange for the given connection specimens. The corresponding constructional measures and installations with good quality should be given importance. The presented CFST column connection is of construction convenience and fine deformation performance compared with the CFST column connected through the welding technique and can satisfy the strength requirements as well.
- The increase of the width of the ring plate and the shape of the ring plate changing from a square to a circle can significantly improve the ductility and the characteristics of the hysteretic behavior of connection. The specimen with the square ring plate is of better deformation performance but lower bearing capacity than the ones with circular ring plates.
- The backing plates positively affect the hysteretic characteristics, ductility, and energy dissipation of the CFST column connections. They can be installed in the application to lessen cost and for construction convenience. However, the increase of axial compression ratio negatively affects the bearing capacity and deformation performance of the connection specimens.
- For the idealization of the numerical model, without considering the initial imperfection of specimens due to fabrication, the numerical results have minor differences from the experimental data but within acceptable errors. Further improvement and optimization of the numerical model must be conducted in future related research. The proposed type of connection can provide reference toward engineering practice and can be applied in future construction projects through further local optimization.
CONSENT FOR PUBLICATION
Not applicable.
CONFLICT OF INTEREST
The authors declare no conflict of interest, financial or otherwise.
ACKNOWLEDGEMENTS
This research was financially supported by a grant from the National Natural Science Foundation of China (No. 51578100) and a grant from the Fundamental Research Funds for the Central Universities (Nos. 3132014326 and 3132016216).
REFERENCES
[CrossRef Link]
[CrossRef Link]
[CrossRef Link]
[CrossRef Link]
[CrossRef Link]
[CrossRef Link]
[CrossRef Link]
[CrossRef Link]