All published articles of this journal are available on ScienceDirect.
The Effect of Specimen Shape on the Mechanical Properties of Sisal Fiber-Reinforced Concrete
Abstract
Introduction:
Fiber reinforced concrete is becoming popular in improving the quasi-brittle failure of concrete. Natural fibers such as sisal holds great promise in this regard. It has amazing tensile strength and is renewable. This paper presents the result of an investigation carried out on the effect of sisal fiber on the compressive strength, Split tensile strength, failure mode and Poisson ratio of Sisal Fiber-Reinforced Concrete (SFRC).
Methods:
A mix proportion of 1:1.92:3.68 and w/c ratio of 0.47 for a target compressive strength of 35 MPa was used. Sisal fiber was added at percentages of 0.5%, 1.0%, 1.5%, and 2.0% by weight of cement. The effect of specimen shape on the compressive strength of sisal fiber-reinforced concrete (SFRC) was reported. The compressive strength of cube (150mm X 150mm) and cylinder (150mm diameter and 300mm height) specimen was determined at 7 and 28 days, while Split tensile strength and Poisson ratio were obtained using cylindrical specimen (150mm diameter and 300mm height).
Results and Conclusion:
The result shows that the addition of sisal fiber slightly reduces the compressive strength of concrete, increases its split tensile strength up to 47.167% of the control specimen, arrests crack propagation and reduces its Poisson ratio. The correlation between the compressive strength of cylindrical and cube specimen was established with a ratio ranging between 0.82 - 0.73. The difference in the compressive strength was found to increase with rise in the percentages of sisal fiber. Based on the ratio and mechanical properties, 1.0% sisal fiber content was recommended as the optimum for reinforcing concrete.
1. INTRODUCTION
Concrete reinforced with fiber is a unique material which has found great relevance in the field of engineering with a wide range of possible applications in construction. It is made by incorporating uniformly distributed and randomly oriented short discrete fibers in a concrete mix. Concrete on its own is brittle with some other undesired properties such as low resistance to crack propagation, low impact and tensile strength [1]. The low tensile strength is as a result of internal micro-cracks at the concrete matrix interphase whose rapid propagation under applied stress results in quick failure [2], addition of fibers plays a crucial role in arresting these cracks, reducing its width thus resisting structural deformation [2, 3]. It also influences the mechanical strength, ductility and energy absorption of concrete [4].The durability of natural fibers such as sisal in a cement based matrix is greatly enhanced by using low alkali content cement, and modification of the mix by including additives such as silica fume, fly ash and slag. Surface treatment with NaOH and silica fume has also been reported to improve its long-term performance in an alkali medium [5]. In a study carried out by [6] subjecting sisal fiber to thermal treatment and Na2CO3 surface treatment significantly improved the durability and mechanical properties of concrete composite.
Regardless of the numerous additional benefits of including fibers in concrete, concrete is still relied upon for its compressive strength. There are generally two standard test specimen recommended for measuring concrete’s compressive strength viz: cubes and cylinders. The latter is the recommended standard specimen in the United States, Canada, France, Australia and New Zealand while Britain and most African countries adopts the former [7] Cubes have a smaller volume space (0.003375mm3) compared to cylinders of the same size (0.005301mm3) and do not require capping for testing as they are rolled over on their sides to get a plane loading surface. In real structures, the cylinder specimen seems more appropriate as they are casted and tested in the same position, unlike cubes that are turned on their sides [8].
Aspect ratio (height to diameter ratio) of test specimen is crucial for confinement effects during loading [8]. The greater the aspect ratio, the more the correction factor as the value of the compressive strength of cubes and cylinder of the same aspect ratio converges [9]. However, a higher aspect ratio for a single specimen implies lower confinement. Hence a cylinder specimen with an aspect ratio of 2 can resist smaller load compared with that of an aspect ratio of 1, assuming the adopted slope value is close to 45o.
In comparing the compressive strength of cubes and cylinder specimen, BS 1881-120 recommends multiplying the cube compressive strength by a factor of 0.8 to obtain the cylinder compressive strength of plain concrete for an aspect ratio of 1 while ASTM C42-90 recommended a correction factor of 0.87 [9]. However, this ratio may not always be precise especially when there are additional materials like fibers in the concrete matrix. Most studies on the effect of sisal fiber on the compressive strength of concrete adopt cubes as the test specimen [4,10].
The low resistance of crack propagation of concrete is improved significantly by incorporation of fibers. It also improves its tensile strength and deformation. Under axial stress up to about 40% of the compressive strength, the ratio of the transverse and longitudinal strain of normal strength concrete varies between 0.15 and 0.20 [11]. At stresses above 60%, microcracks begin to develop in a direction parallel to that of the applied stress. The microcracks result in an increase in the transverse strain as the applied stress increases. Fibers acting as crack arrestors can significantly reduce the propagation of these microcracks, and by extension the transverse strain. Leading to a reduction in Poisson ratio. Few studies [11-13] however reports the Poisson ratio of fiber reinforced concrete. Amorphous metallic fibers were reported to lower the horizontal expansion of concrete and reduced its Poisson ratio [14]. Similar reduction in Poisson ratio was noticed in steel fiber-reinforced, high-strength, Light weight concrete. The Poisson ratio was reportedly observed to reduce from 0.25 to 0.166 depending on aspect ratio and increasing volume fraction [12-15] studied the effect of sisal fibers on the Poisson ratio of cement mortal, it was reported that sisal had no significant effect on the Poisson ratio of cement mortal.
Since limited studies exist on the effect of shape on the compressive strength of Sisal fiber reinforced concrete and its Poisson ratio. This study aims to investigate the effect of shape on the compressive strength of concrete reinforced with sisal fibers using cubes and cylinders. The chosen sizes are believed to give a good representation of what is used in local and international construction industries for testing the compressive strength of concrete. The tensile strength and Poisson ratio of sisal fiber were also investigated.
2. MATERIALS AND METHODS
2.1. Materials
2.1.1. Properties of Cement
The tested physical and chemical properties of the cement used in this study are presented in Tables 1 and 2 respectively. The chemical content was obtained using an X-ray fluorescence device. The cement was found to fulfil the physical and chemical requirement of ASTM C 150 for use in making concrete [16].
Test | - | Result | ASTM C 150 Limits |
---|---|---|---|
Specific Gravity | - | 3.12 | - |
Specific Surface | - | 3197 cm2/g | Minimum 2800 cm2/g |
Water Demand | - | 25.65% | - |
Setting Time | Initial | 160mins | Not less than 45mins |
Final | 252mins | Not more than 375mins | |
Soundness | - | 0.3mm | - |
Compressive Strength (Mortar Prism) | At 2 days | 19.3 MPa | Minimum 12 N/mm2 |
- | At 28 days | 48.94 MPa | Minimum 19 N/mm2 |
Colour | - | Grey | - |
Parameter | Chemical Content (%) | ASTM C 150 Limits |
---|---|---|
SiO2 | 20.98 | - |
Al2O3 | 5.67 | - |
Fe2O3 | 2.374 | - |
MgO | 0.8 | Maximum of 6% |
SO3 | 3.45 | Maximum of 3.5% |
Loss of ignition | 2.85 | Maximum of 3.0% |
P2O5 | 0.407 | - |
Na2O | 0.4 | - |
CaO | 65.519 | - |
Sr | 0.176 | - |
2.1.2.. Properties of Fine and Coarse aggregate
Natural River sand with specific gravity and fineness modulus of 2.56 and 2.66 respectively was used in this study. The sand was obtained from Kivaa in Kenya and was within the limits of ASTM C 33 [17] as shown in Table 3.
Sieve Size (mm) | Percentage Passing (%) | ASTM C 33 Lower Limit (%) | ASTM C 33 Upper Limit (%) |
---|---|---|---|
9.5 | 100.00 | 100 | 100 |
4.75 | 98.04 | 95 | 100 |
2.36 | 94.08 | 80 | 100 |
1.18 | 75.64 | 50 | 85 |
0.6 | 39.36 | 25 | 60 |
0.3 | 22.79 | 5 | 30 |
0.15 | 3.71 | 0 | 10 |
The coarse aggregate used in this study was granite obtained from Ruiru in Kenya with a nominal size of 25mm- 9.5mm and specific gravity of 2.70. The grading limits according to ASTM C 33 [17] are presented in Table 4.
Sieve Size (mm) | Coarse Aggregates | ASTM C 33 Lower Limit (%) | ASTM C 33 Upper Limit (%) |
---|---|---|---|
37.5 | 100.00 | 100.00 | 100 |
25 | 99.76 | 90.00 | 100 |
19 | 79.23 | 40.00 | 85 |
12.5 | 36.75 | 10.00 | 40 |
9.5 | 12.10 | 0.00 | 15 |
4.75 | 0.53 | 0.00 | 5 |
2.36 | 0.00 | 0.00 | 0 |
2.1.3. Properties of Sisal fiber
Locally available sisal fiber from Juja in Kenya was used for this research. The tensile strength of sisal was measured using a Hounsfield Tensometer and its properties are presented in Table 5.
Fiber Property | Result |
---|---|
Length | 30mm |
Diameter | 0.10mm-0.13mm |
Aspect ratio | 230-300 |
Tensile strength | 371.3328 MPa |
Tensile Modulus | 12.432.23 GPa |
Shape | Straight |
MasterRoc MS 610 Silica fume slurry from Ultra-tech Kenya Limited was used in treating the sisal fibers. The fibers were immersed in the slurry for 10mins and left to dry at room temperature for 15 minutes [5]. The properties of the silica fume slurry are presented in Table 6. Commercially available superplasticiser was used to ensure good workability and compaction. Ordinary water available in the university premises was used for the preparation of the concrete mix and curing of the test samples.
Property | Description |
---|---|
Form | Slurry |
Colour | Grey |
Density | 0.55 - 0.70 kg/l |
Chloride Content | <0.1% |
2.2. Mix Proportion
The designed mix used in this study was 1:1.92:3.26 (cement: sand: granite) for a target strength of 35 MPa according to [18]. Batching was done by weight and the water-cement ratio was carefully selected to achieve a slump of 100mm, since sisal fiber was expected to affect the workability of the mix, different dosages of superplasticizer were tried to obtain the optimum without bleeding or segregation. The mix was incorporated with sisal fibers at 0.5%, 1.0%, 1.5% and 2.0% of weight of cement labelled respectively as M0.5, M1.0, M1.5 and M2.0.with the control (Plain concrete) as M0.0 Fig. (1). Mix proportion details are as presented in Table 7.
Sample | Cement | Fine Aggregate | Coarse Aggregate | Water | Superplasticizer | Sisal Fiber |
---|---|---|---|---|---|---|
M0.0 | 380 | 730 | 1400 | 203.67 | 1.9 | 0.0 |
M0.5 | 380 | 730 | 1400 | 203.67 | 1.9 | 1.9 |
M1.0 | 380 | 730 | 1400 | 203.67 | 1.9 | 3.8 |
M1.5 | 380 | 730 | 1400 | 203.67 | 1.9 | 5.7 |
M2.0 | 380 | 730 | 1400 | 203.67 | 1.9 | 7.6 |
3. SPECIMEN
Two specimen shapes (Cubes and cylinders) of respective size 150mm X 150mm according to BS EN 12390-2:2000 [19] and 150mm diameter and 300mm height as stated in ASTM C39 [20] were used for each compressive test. Cylinder samples of the aforementioned dimension were also used for split tensile tests. For each mix, three samples were casted in non- absorbent moulds for testing.
4. METHODS
4.1. Mixing Method
Mixing of concrete was done by dry mixing the cement, sand and granite for 3 minutes, after which 80% of water blended with superplasticizer was added to the dry mix. The wet blend was mixed for further 8 minutes before the remaining of water blended with superplasticizer was added to the mix and mixed thoroughly. About 50% of the sisal fiber were then manually added to mix with care being taken to ensure there was no balling of the fibers, mixing was carried out for further 2 minutes before the rest of the fibers was added. The concrete was ready for placing after 2 minutes of mixing. The concrete was placed in the moulds and compacted using a proctor vibrator. Once compacted, a steel float was used for levelling the specimen’s surface. The specimens were left undisturbed in the moulds for 24±3h before demoulding and placed in a curing tank in a curing room with regulated temperature of 21 oC ±2oC until 7 and 28 days of testing.
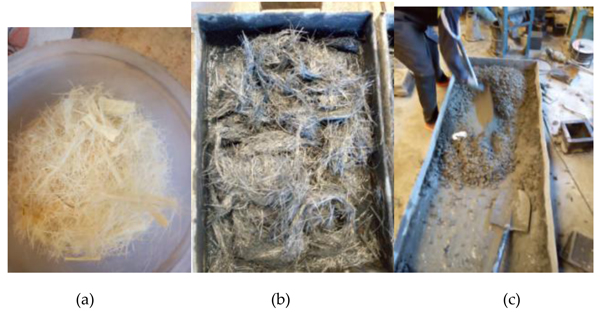
4.2. Testing Methods
- At the end of 7 and 28 days of regular water curing, the compressive strength of the cube specimens (150mmx150mm) was obtained in accordance with BS EN 12390-3:2002 [21] specifications (Fig. 2a), while that of cylinder specimens were tested in accordance with the specifications of ASTM C39 [20]. The average of three tested samples is presented.
- Split tensile tests was done on cylindrical specimen in accordance to ASTM C 496-04 [22] requirements. The average of three tested samples is reported.
- The Poisson’s ratio was measured using 2 bonded strain gages (PL-60-11-3LT series) placed circumferentially at diametrically opposite points at the mid-height of the cylinder specimen and connected to a data logger under axial compression in accordance with ASTM C469 [23]. All tests were done using a load controlled Servo-plus universal testing machine (Fig. 2b).
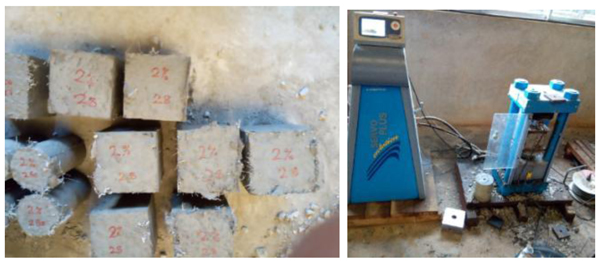
5. RESULTS AND DISCUSSIONS
5.1. Effect of Sisal Fibers on the Compressive Strength of Concrete
One of the most important indicators used in evaluating the performance of fiber reinforced concrete is its compressive strength. The average compressive strength of cube and cylinder specimen at 7 and 28 days are shown in Figs. (3 and 4). The compressive strength was observed to decrease with increase in the amount of sisal fiber added for 7 and 28 days for both specimen shapes (cubes and cylinders). At low fiber content (<0.5%) where the modulus of elasticity of fiber is less than that of the plain matrix (Ef/Em < 1), little reduction is expected in the compressive strength. The reduction can be expected to be as high as 25% and 30% respectively for a volume fraction of 2% to 3% [15]. Percentage reduction of 4.22%, 11.54%, 18.18%, 25.30% and 2.07%, 7.75%, 14.76%, 16.35% were obtained for M0.5, M1.0, M1.5, M2.0 in cubes and cylinders respectively when compared to M0.0 at 28days due to the modulus of elasticity of sisal fiber being less than that of the concrete matrix thus replacing stronger concrete constituent. A similar result was presented by [1], although there was an increase in compressive strength with curing time due to further hydration and improved bond between the fibers and concrete matrix.
This finding however contradicts an increase in compressive strength of SFRC up to 1.0% sisal fiber addition reported by [4]. Like all fibers, sisal has the tendency of reducing the workability of concrete and requiring higher effort for compaction [24],resulting in the risk of reduction in the compressive strength of concrete as the weight of the hardened concrete reduces. Numerical model proposed by [25] for fiber reinforced concrete using different mixing methods showed that the addition of fibers in a cementitious matrix will reduce the compressive strength, this is due to reported reduction in the workability of the fresh mix and the presence of voids in the hardened concrete. For there to be an increase in compressive strength, Sisal fiber will need to act as internal confinement for the concrete materials. This is achievable by raising the amount of fibers in the mix (which also present the risk of reduced workability). The increase in strength reported by some experimental studies could have been as a side effect of the reduction in the effective water-cement ratio for cement hydration in the bulk resulting in a better matrix of hydrated cement paste which raises the strength, and not by the direct action of the fibers. Fibers like steel with a high elastic modulus can however improve the compressive strength (Ef/Em > 1) [26]. Hence, the influences of sisal fiber on the compressive behaviour will probably reflect at the post cracking stage of the stress strain curve [27].
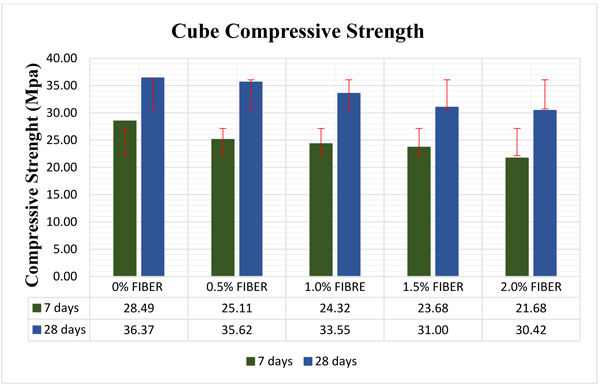
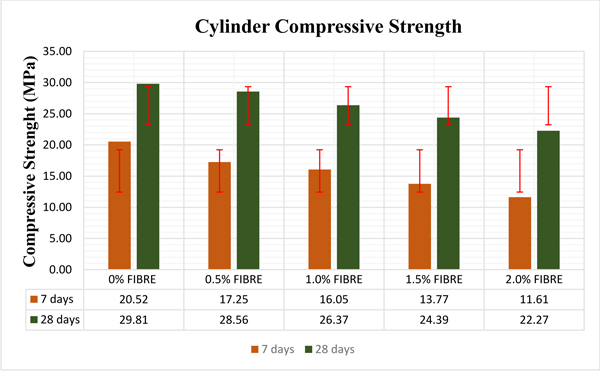
5.2. Effect of Shape on the Compressive Strength of SFRC
The research was carried out to study the effect shape has on the compressive strength of sisal fiber reinforced concrete. The compressive strength of plain concrete cube was observed to be higher than that of cylinders by 27.97% and 18.04% at 7 and 28days respectively. It could be deduced from the result that cube specimen give higher compressive strength [3, 8, 28]. The specimen with the highest sisal fiber content (M2.0) gave a cube compressive strength which was 21.14% and 29.68% greater than that of the cylinders at 7 and 28 days respectively. However, these finding doesn’t agree with that of fiber reinforced ultra-high performance concrete where the compressive strength of cylinder was reportedly higher than cube’s [29].
The ratio of the compressive strength of cylinder specimens (fcy) to the cubes (fcc) was between 0.72 and 0.54, with an average of 0.64 at 7 days as shown in Table 8, while the ratio of the compressive strength of cylinders (fcy) to cubes (fcc) was between 0.82 and 0.73, with a mean ratio of 0.79 at 28 days as depicted in Table 9. The difference in compression strength may be due to the applied axial force tending to align the fibers in certain planes. It tends parallel in cubes while in cylinders, which tend to align perpendicular to the axis of loading where it could help inhibit lateral bursting [30].
Mix | Specimen | compressive strength (MPa) | Sd | Cv | Cube: Cylinder Ratio | Cylinder: Cube Ratio |
M0.0 | Cube | 28.49 | 0.62 | 0.02 | 1.39 | 0.72 |
Cylinder | 20.52 | 1.03 | 0.05 | |||
M0.5 | Cube | 25.11 | 1.18 | 0.05 | 1.46 | 0.69 |
Cylinder | 17.25 | 0.15 | 0.01 | |||
M1.0 | Cube | 24.32 | 1.25 | 0.05 | 1.52 | 0.64 |
Cylinder | 16.05 | 0.44 | 0.03 | |||
M1.5 | Cube | 23.68 | 0.76 | 0.03 | 1.72 | 0.58 |
Cylinder | 13.77 | 0.51 | 0.04 | |||
M2.0 | Cube | 21.68 | 0.90 | 0.04 | 1.87 | 0.54 |
Cylinder | 11.61 | 0.51 | 0.05 |
Mix | Specimen | compressive strength (MPa) | Sd | Cv | Cube: Cylinder Ratio | Cylinder: Cube Ratio |
---|---|---|---|---|---|---|
M0.0 | Cube | 36.37 | 3.08 | 0.08 | 1.22 | 0.82 |
Cylinder | 29.81 | 0.41 | 0.01 | |||
M0.5 | Cube | 35.62 | 2.54 | 0.07 | 1.25 | 0.80 |
Cylinder | 28.56 | 0.85 | 0.03 | |||
M1.0 | Cube | 33.55 | 1.30 | 0.04 | 1.27 | 0.79 |
Cylinder | 26.37 | 0.76 | 0.03 | |||
M1.5 | Cube | 31.00 | 1.60 | 0.05 | 1.27 | 0.79 |
Cylinder | 24.39 | 0.90 | 0.04 | |||
M2.0 | Cube | 30.42 | 0.50 | 0.02 | 1.37 | 0.73 |
Cylinder | 22.27 | 0.22 | 0.02 |
From the decreasing cylinder to cube compressive strength ratio, it can be deduced that sisal fiber incorporation increases the effect specimen shape has on the compressive strength of concrete at both 7 and 28days. The ratio of the 28 days cube compressive strength to that of cylinders was however observed to be between 1.22 and 1.37, with an average of 1.28. The higher fcu is due to the development of tri-axial compression zones in cubes by virtue of the presence of restrained zones during uniaxial compression test which is absent in cylinders with an aspect ratio of 2 [31]. M0.5, M1.0, M1.5 gave respective fcy/fcc ratio of 0.80, 0.79 and 0.79 at 28 days which shows that the ratio of fcy/fcc for SFRC was in close agreement with the value 0.8 which was recommended by BS EN 12390-3.
Furthermore, the variation in the effect of sisal on the compressive strength of the cube and cylinder specimen can be discerned after further curing, the disparity in the compressive strength between the two shapes grows with increase in the percentages of sisal fibers at 7 and 28 days as shown in Figs. (4 and 5). Table. 10 shows the standard deviation (Sd) and coefficient of variation (CV) between the cube and cylinder for the same fiber content. Both the standard deviation and coefficient of variation increases with rising sisal fiber content at the same curing age. Certainly, incorporation of fibers reduces concrete’s density, raises its water absorption and void. The increase in voids generates more interface zone between sisal and the concrete constituent’s interfaces [32]. Consequently, SFRC has an increased number of permeable and micro crack regions than plain concrete, which further elucidate on the reduction in the compressive strength. Additionaly, the greater interface zone between the fiber and concrete aggregate impacts more on the restrained zones of concrete under uniaxial compression. The tri-axial compression zones in cube specimen aid its compressive strength, however, cylinders have their unrestrained zone situated away from their ends which is further compromised by the increased interface zone as a result of fiber content. As fiber content increases, the interface zone grows and the compressive strength of cylinders reduces, this explains the increase in the shape effect at higher fiber content. Overall, the incorporation of sisal fiber into concrete reduces its compressive strength and increases the influence shape has on the strength of concrete.
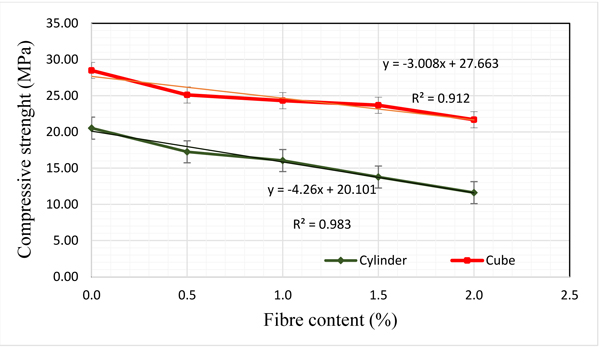
7 days Sd | 7 days CV | 28 days Sd | 28 days CV |
---|---|---|---|
5.631 | 0.230 | 4.636 | 0.140 |
5.556 | 0.262 | 4.992 | 0.156 |
5.850 | 0.290 | 5.075 | 0.169 |
7.007 | 0.374 | 4.672 | 0.169 |
7.118 | 0.428 | 5.765 | 0.219 |
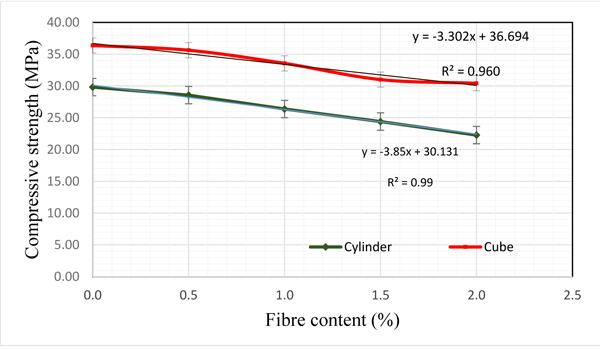
5.3. Split tensile test and Failure mechanism of SFRC
The results of the split tensile strength are presented in Table 11. It has long been known that the presence of fibers considerably improves the tensile strength due to the tensile stress transfer capability of the sisal fibers across concrete crack surfaces, known as crack-bridging [33]. The 28 days split tensile strength value was higher than those at 7 days due to further hydration and strength gain. At 28 days, a percentage increase of 29.60% and 47.17% was observed in the split tensile strength of M0.5 and M1.0 respectively compared to plain concrete, while on further addition of sisal fiber, M1.5 and M2.0 showed a declining percentage increase of 16.57% and 6.62%. Thus, the split tensile strength of SFRC at each curing age increases up to 1.0% beyond which it drops but remain higher than that of plain concrete.
7 days N/mm2 | Sd | Cv | % Increase | 28 days N/mm2 | Sd | Cv | % Increase |
---|---|---|---|---|---|---|---|
2.073 | 0.022 | 0.011 | - | 2.353 | 0.336 | 0.143 | - |
2.468 | 0.114 | 0.046 | 19.074 | 3.050 | 0.040 | 0.013 | 29.603 |
2.677 | 0.030 | 0.011 | 29.157 | 3.463 | 0.240 | 0.069 | 47.167 |
2.420 | 0.075 | 0.031 | 16.758 | 2.743 | 0.116 | 0.042 | 16.572 |
2.180 | 0.010 | 0.005 | 5.179 | 2.509 | 0.209 | 0.083 | 6.629 |
The least recorded tensile strength for SFRC at 7 and 28 days (2.180 N/mm2 and 2.509 N/mm2) was still higher than that of plain concrete (2.073 N/mm2 and 2.353 N/mm2) implying that incorporation of sisal increases the tensile strength of concrete for all percentages up to 2.0%.The maximum split tensile strength recorded was 3.463 N/mm2 for 1.0% fiber addition, the finding is in close agreement with the target tensile strength of 3.5 N/mm2 (for class 30/35). The improvement in the split tensile strength is due to the ability of sisal fiber to impact more ductility in the concrete, Load is transferred to the fibers at the crack site after the formation of cracks, and at this stage different behaviour may be exhibited depending on the strength, volume fraction and aspect ratio of the fiber. At sufficient fiber content, aspect ratio and strength, sisal fibers bridge across the possible cracks as shown in Fig. (7). Thus, sisal fibers acted as porous bridging elements across cracks, permitting the deposition of new hydration products and the subsequent infill/closure of the cracks [15]. Furthermore, unlike the brittle failure observed in plain concrete, fibrous concrete like SFRC demonstrates a pseudo-ductile tensile behaviour and enhanced energy dissipations capacities [27,34]. The observed trend in split tensile strengths of SFRC compared favourably with those of previous works [10,35].
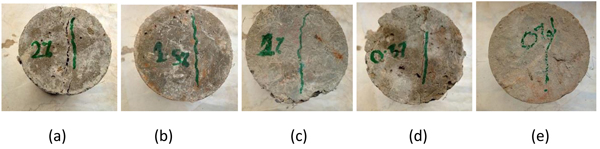
The increase in the tensile strength and post cracking performance of SFRC as shown in Fig. (8) can be achieved up to a certain fiber content known as critical volume fraction; Vf,cr [36-38, 33].
![]() |
(1) |

Where fct is the tensile strength of plain concrete; n1 is the ratio of the average fiber stress to the maximum fiber stress and equals to 1:n0 is the fiber orientation factor in the elastic range and equals to 0.405; σ_fu is the ultimate fiber stress. For the tested fibrous concrete mixtures, the ultimate fiber stress equals 399.44 MPa and the tensile strength of plain concrete is 2.353MPa giving a critical volume fraction of 1.45%. Hence, for the post-cracking tensile behaviour of the concrete mixtures with 1.50% and 2.0% volume of fibers, a lower tensile.
5.4. Failure mechanism of SFRC
Fig. (8) shows the failure mode of cube and cylinder specimen after compression test. The stopping load for all the specimen was set at 40% of the failure load. Cracks were observed to form in the longitudinal direction before the peak stress and propagate in the lateral direction as the applied load increases. Inclined shear failure cracks were formed at the beginning of the softening phase. The crack pattern was columnar for cylinders and non-explosive for cubes. It was noticed that the cracks formed were wider with higher numbers in the specimens without sisal fibers (M0), whereas, they were reduced for SFRC. The least number of cracks was noticed on M2.0. From the split tensile strength and the compressive mode of failure, it could be said that that sisal fiber plays a significant role in arresting crack formation and propagation in concrete.
The improved tensile strength and cracking performance of sisal fiber is important in the shear response of structural elements like concrete beams. The effect of using sisal fiber in concrete is quite similar to that of steel fibers reported by [39].Thus, fibers like sisal could be promising as a non-conventional reinforcement in shear critical beams by potentially reducing shear reinforcements and altering shear brittle failure into ductile flexural ones [33]. Unlike sisal however, steel fibers have already been used to partially reduce steel stirrups especially in sections where high transverse steel ratio with small spacing is required [40 , 41].
5.5. Poisson Ratio of SFRC
The ratio of the transverse strain to the axial strain known as Poisson's Ratio (Vc), Fig. (9) shows the variation of Poisson ratio with fiber content at 40% of ultimate stress.
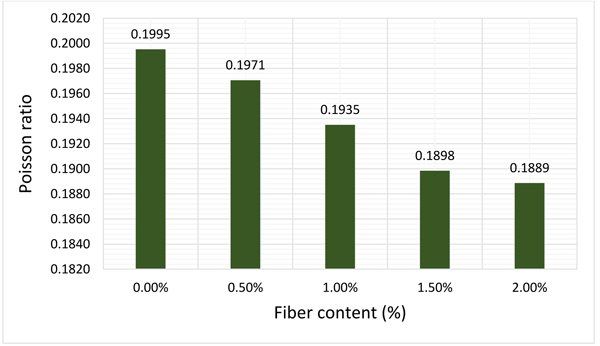
The measured value of Poisson ratio ranged between 0.200 and 0.189. Plain concrete had a Poisson ratio of 0.1995, for normal strength concrete, a value of 0.2 is usually adopted [42]. While SFRC shows a slight decrease in Poisson ratio as the fiber content increased. The reduction in the Poisson ratio demonstrates that the presence of sisal fibers in a concrete matrix arrests deformation, reduces expansion and stretch in the horizontal direction, resulting in less destructive external surface [12 , 14]. Similar reduction in poisson ratio of fiber reinforced concrete was reported by [43]. The relationship between Poisson’s ratio and fiber content follows the equation.
![]() |
(2) |
Where μf is the Poisson ratio of SFRC; μc the Poisson ratio of plain concrete and Vf is the fiber content.
CONCLUSION AND RECOMMENDATION
From this experimental investigation on the effect of specimen shape on the mechanical strength of SFRC, for a constant mix proportion of 1:1.92:3.68 and w/c ratio of 0.47, the following deductions can be drawn. The compressive strength of SFRC reduces with rising sisal fiber content, therefore sisal fiber cannot be used to enhance compressive strength of concrete. Despite the reduced strength, SFRC exhibited the ability to increase post-cracking ductility and energy dissipation. The variation in the compressive strength of SFRC cubes and cylinders increases with curing time and rise in the percentage of sisal fibers. The average ratio of the 28 days compressive strength of SFRC cylinders to cubes is 0.79. Hence, the relationship between cube and cylinder compressive strength presented in British standard can be applied to SFRC. Furthermore, Sisal fiber plays a crucial role in reducing the Poisson ratio of concrete and improving the split tensile strength. Based on the conclusion, an optimum sisal fiber addition of 1.0% is recommended for reinforcing concrete. M1.0 gave the highest split tensile strength, a cylinder to cube ratio in close agreement with that recommended in standards and a cube compressive strength of 33.55 MPa, which didn’t deviate excessively from the target design strength of 35 MPa.
CONSENT FOR PUBLICATION
Not applicable.
CONFLICT OF INTEREST
The authors declare no conflict of interest, financial or otherwise.
ACKNOWLEDGEMENTS
The authors will like to appreciate the African Union Commission, under the aegis of Pan African University, Institute for Basic Science, Technology and Innovation (PAUISTI) and AFRICA-ai-JAPAN project for funding this research.