All published articles of this journal are available on ScienceDirect.
The Effect of Cassava Starch on the Durability Characteristics of Concrete
Abstract
Background:
Concrete is a common material used in the construction of marine structures, such as bridges, water treatment plants, jetties, etc. The use of concrete in these environment exposes it to attack from chemicals like sulphates, chlorides and alkaline, thereby causing it to deteriorate, and unable to perform satisfactorily within its service life. Hence, the need to investigate the durability properties of concrete has become necessary especially when admixtures are used to modify some of its properties.
Objective:
This research work investigates the effect of Cassava Starch (CS) on the durability characteristics of concrete.
Methods:
The durability properties investigated in this work are water absorption, sorptivity, resistance to sulphates, sodium hydroxides and chloride penetration. The specimens were prepared by adding CS by weight of cement at 0.4, 0.8, 1.2, 1.6 and 2.0% respectively. The concrete specimens were cured for 28 days, tested for compressive strength before ponding in ionic solutions of sodium hydroxide, sulphuric acid and sodium chloride. Six (6) concrete mixes were prepared, five of which were used to evaluate the effect of CS on the durability characteristics of concrete.
Results:
The slump values reduced with the increasing dosage of CS due to the viscous nature of the CS paste. Generally, the addition of CS in concrete tends to improve the resistance of concrete to sulphate and chloride attack due to the ability of the muddy-like starch gel to block the pore spaces of hardened concrete, hence, reduces the rate at which water and other aggressive chemicals penetrate the concrete. In addition, the retarding ability of CS impedes the formation of mono-sulphate aluminates during cement hydration, thereby making the concrete less susceptible to sulphate attack.
Conclusion:
The addition of CS to concrete by weight of cement generally improved the durability characteristics of concrete, while the relative performances of the concrete mixes showed that CS 2.0 gave a better resistance to chloride penetration and sulphate attack.
1. INTRODUCTION
The use of concrete as a construction material is common because of its properties, cheapness and ability to be moulded into the desired shape. Certain environments such as marine and seawater, soils containing sulphates, water and waste treatment environments, expose concrete surfaces to sulphates, chloride and alkaline attacks. This can cause a deterioration of concrete, causing a reduction in the durability properties of concrete. Therefore, concrete structures need to be protected for it to serve the purpose for which they are built throughout its service life. Susilorini et al. [1] reported that sulphate attack on concrete is characterized by its mass and strength loss. This occurs when mono-sulphate aluminate hydrate crystals formed during second-order cement hydration becomes unstable and results back into larger sized crystals which leads to cracking and deterioration of cementitious materials when subjected to sulphate attack Mindess and Young [2]. The process of the first order and second order cement hydration is described in Equation 1 and 2 respectively.
![]() |
(1) |
Tricalcium aluminate + gypsum + water = Ettringite + Heat
![]() |
(2) |
Tricalcium aluminate + Ettringite + water = Mono-sulphate aluminate hydrate
The resistance of concrete to sulphate attack will depend on the use of sulphate resisting cement and/or the use of retarding admixtures to inhibit the formation of the mono-sulphate aluminate hydrates within the concrete mass. Besides, concrete structures are also attacked by the ingress of chlorides into its pore structure. The chlorides cause the oxidation of reinforcing bars in concrete, thereby leading to corrosion. The penetration of chlorides into concrete can be controlled either by providing a good cover to reinforcing bars or by reducing the interconnectivity of the pore spaces in concrete which depends on its sorptivity. According to Pitroda [3] and (Pitroda & Umrigar) [4], sorptivity is an important parameter in measuring the resistance of concrete to aggressive environments. A high sorptivity value shows that the concrete pore spaces are well connected and vice versa. This means that the diffusion of an aggressive chemical will be high in concrete having high sorptivity.
Cassava Starch (CS) is a carbohydrate polymer that is composed of two molecular components: linear amylose and branched amylopectin, Fig. (1) shows the chemical structure of the amylose and amylopectin in CS.
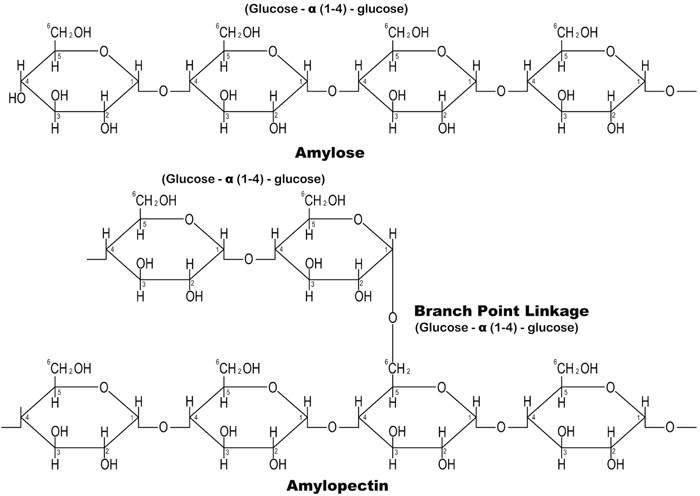
Compound | Abbreviation | % weight | Limits (BS EN 197-1) |
---|---|---|---|
Calcium oxide | CaO | 61.48 | > 50 |
Silicon oxide | SiO2 | 25.79 | > 25 |
Aluminium oxide | Al2O3 | 5.60 | 3-8 |
Iron oxide | Fe2O3 | 2.34 | 0.5-6 |
Sulphur | SO3 | 2.60 | ≤ 3.5 |
Potassium oxide | K2O | 1.00 | 0.2-1.3 |
Phosphorus pentoxide | P2O5 | 0.52 | - |
Chloride | Cl | 0.23 | - |
Titanium | Ti | 0.21 | - |
Strontium | Sr | 0.14 | - |
Property | Abbreviation | % Weight | Limits (BS EN 197-1) |
---|---|---|---|
Tricalcium silicate | C3S | 13.25 | 13.25 |
Dicalcium silicate | C2S | 63.96 | > 42.5 MPa |
Tricalcium aluminate | C3A | 10.88 | 3.10 -3.15 |
Tetracalcium aluminoferrite | C4AF | 7.12 | 25 – 35% |
- | - | 95.21 | 95 - 100 |
The interaction between the Amylose-Amylopectin improves the viscosity and textural properties of starch, which include cohesiveness and adhesiveness. A viscous and thickening gel is formed when starch is dissolved in hot water by allowing the hydrogen bonding sites (the hydroxyl, hydrogen and oxygen) to engage more water Tako et al. [6]. This eco-friendly and cheap material has various applications in construction as reported by various researchers. Oni et al. [7]. reported that CS could be used to increase the workability retention time of concrete. Abalaka [8] and Okafor [9] concluded that starch improved the compressive strength of concrete. Akindahunsi and Schmidt [10] also noted that the creep behaviour and shrinkage characteristics of concrete mixed with starch were improved. Hence, this research aim to evaluate the effect of cassava starch on the durability properties of concrete by exposing it to chloride, sulphate and alkaline environments.
2. MATERIALS AND METHOD
2.1. Materials
Fine Aggregates (FA), Coarse Aggregates (CA), Ordinary Portland Cement (OPC) type 1, Cassava Starch (CS), Naphthalene based superplasticizer, and water were used for this investigation. The fine and coarse aggregates used in this study were obtained in Kenya. Its properties conformed with the requirements of ASTM C33 [11]. The nominal size of the granite used was 20mm, with a bulk density of 1473.86 kg/m3 and a specific gravity of 2.41. The river sand (Bulk density - 1513.2 kg/m3, Specific gravity - 2.41 and Fineness modulus - 2.40) was air-dried before use. The cement used during the study was sourced in Kenya and it conformed with the requirements of BS EN 197-1 [12]. Table 1 shows the chemical composition of the cement in this study.
Table 2 shows the clinker constituents of the cement as determined by Bogue’s equation.
C3S is responsible for the early strength of concrete while C2S contributes to the long-term strength of the concrete. C3A is majorly responsible for the set properties of cement and acts as a sink for retarders when used in concrete. Table 3 shows the physical properties of the cement used to carry out the experiment.
The superplasticizer was added at 0.75% by weight of cement in the concrete to maintain its work ability due to the deduction of 10% mixing water used for the activation of CS. Fig. (2) shows the dried CS powder which was procured in Ile-Ife, Nigeria.
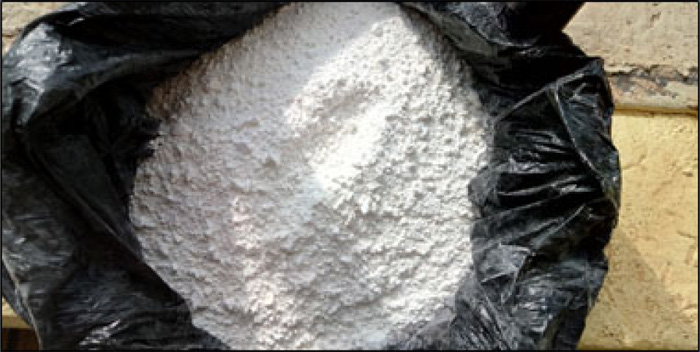
Property | Value | Limits (BS EN 197-1) |
---|---|---|
Compressive strength at 28 Days | 46.23 | > 42.5 MPa |
Specific surface area | 4145 cm2/g | > 42.5 MPa |
Specific gravity | 3.11 | 3.10 -3.15 |
Consistency | 32.75 | 25 – 35% |
Initial setting time | 155 | ≥ 60 minutes |
Final setting time | 248 | ≤ 375minutes |
Colour | Grey | - |
2.2. Methods
2.2.1 Characterisation and Activation of Cassava Starch
CS was dried in sunlight before characterisation and activation. The particle size of CS was determined with the aid of a Laser Diffraction Particle Size Analyser (LDPSA). It measures the sizes of fine materials such as clay muds and starches using a light scattering method. The proximate analysis of CS was determined following the method proposed by the Association of Official Agricultural Chemists, AOAC [13], and carried out at the Department of Animal Production laboratory, University of Nairobi. The starch solution for each concrete batch was prepared by dissolving the CS powder in hot water at a temperature between 70oC and 100oC as proposed by Akindahunsi and Uzoegbo [14], cooled to room temperature and added to the concrete. The water used for the activation was 10% of the mixing water. Fig. (3) shows the activated starch.
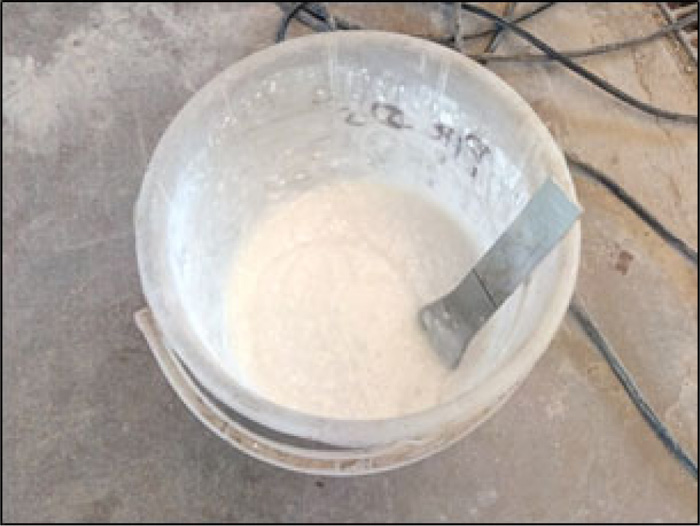
2.2.2 Concrete Mmix Design and Specimen Preparation
The specimens for each batch of concrete were prepared in accordance with the method described in BS EN 8500-2 [15]. The highest proportion of CS addition was limited to 2.0% by weight of cement (50g per kilogram of cement). This is in line with clause 5.2.6 of BS EN 206 [16] which stipulates the maximum dosage of the use of admixtures in concrete should be limited to 2.0% by weight of cement. Table 4 shows the details of the mix used in the study.
The specimens were cured by complete immersion in an open air water tank at room temperature (250C ± 1) for a period of 28 days before ponding in the test solutions for the evaluation of durability. The curing process is shown in Fig. (4). An average of three identical samples were used to determine the durability properties of concrete.
Mix No. | Cement (kg/m3) | W/C Ratio | Fine Aggregate (kg/m3) | Coarse Aggregate (kg/m3) | Cassava Starch Content (kg/m3) | Super-plasticizer (kg/m3) |
---|---|---|---|---|---|---|
CS 0.0 | 436 | 0.49 | 668.4 | 1002.6 | 0.00 | 3.27 |
CS 0.4 | 436 | 0.49 | 668.4 | 1002.6 | 1.74 | 3.27 |
CS 0.8 | 436 | 0.49 | 668.4 | 1002.6 | 3.49 | 3.27 |
CS 1.2 | 436 | 0.49 | 668.4 | 1002.6 | 5.23 | 3.27 |
CS 1.6 | 436 | 0.49 | 668.4 | 1002.6 | 6.98 | 3.27 |
CS 2.0 | 436 | 0.49 | 668.4 | 1002.6 | 8.72 | 3.27 |
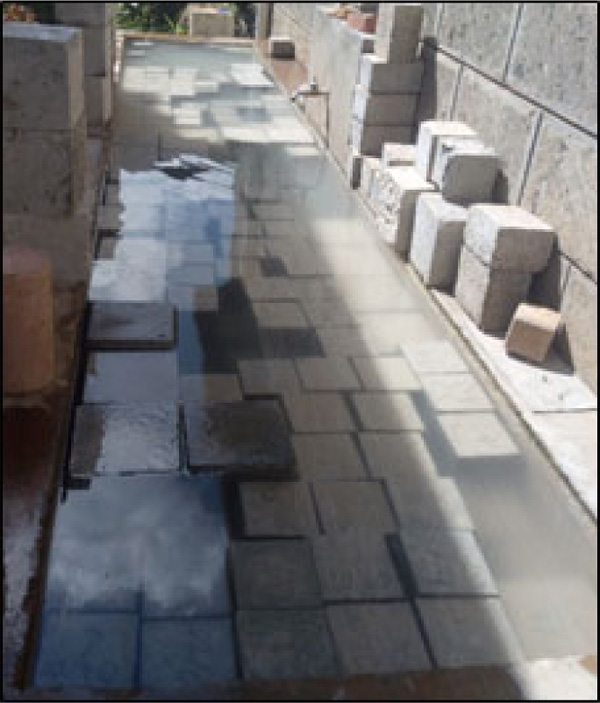
2.2.3 Workability, Water Absorption and Sorptivity Tests.
The workability of the fresh concrete mix was determined using the slump tests. The tests were carried out in accordance with BS EN 12350-2 [17]. The water absorption of CSMC was determined using 150 mm cube sizes following the procedure specified in BS 1881-122 [18]. The sorptivity for the specimen for each treatment level was determined using 100 ± 6 mm diameter specimens of thickness 50 ± 5 mm after curing for 28 days with a method described in ASTM C1585-13 [19]. The reported values of the initial and final rates of water absorption are an average of three (3) measurements. Fig. (5) shows the sorptivity test carried out on the samples.
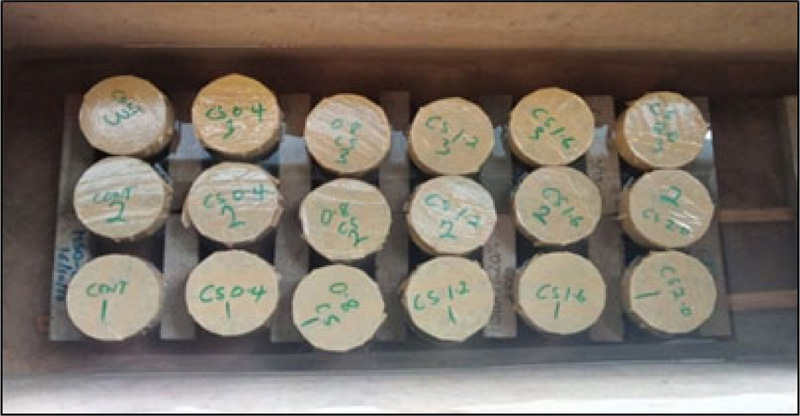
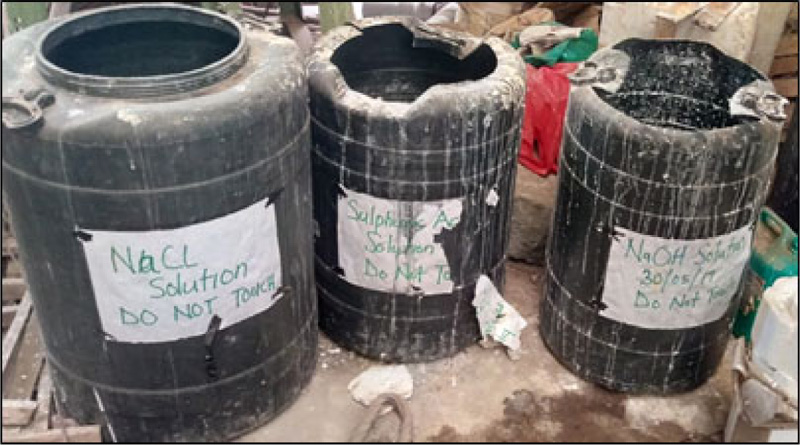
2.2.4 Chloride Penetration Test
The chloride penetration was determined using the grey colourimetric method of detecting free and water-soluble chlorides. The specimens were ponded in a 3% Sodium Chloride (NaCl) solution for a period of 45 and 60 days after initial curing for 28 days. The cylinder specimens were longitudinally split into two using a universal testing machine before spraying the surface with a 3% Silver Nitrate (AgNO3) solution. Equation 3 shows the reaction between the Silver Nitrate and Sodium Chloride.
![]() |
(3) |
Hence, the chloride penetrated area will show white precipitates of silver chloride as seen in equation 3 while the uncontaminated area will show a dark brown appearance Kim et al. [20] and Real et al. [21]. The chloride diffusion coefficient was determined using the equation proposed by Collepardi et al [22], where x is the chloride penetration, D is the diffusion coefficient and t is time elapsed. This equation is based on the solution obtained from Fick’s second law of diffusion under non-steady state conditions and boundaries in a semi-infinite solid.
2.2.5 Sulphate and Alkaline Attack Test
100 mm cubes were weighed after 28 days of curing and ponded in a sulphuric acid solution of pH 3.0 and for a period of 45 and 60 days to determine its resistance to ingress of sulphate ions into the concrete. Another set was ponded in sodium hydroxide solution of pH 12.0 for a period of 45 and 60 days to determine its resistance to hydroxyl ions. The specimens were subjected to wire brush at 7 days interval to remove the corroded products from the surface. The pH of the solution was measured periodically with the aid of a pH meter. The specimens were surface dried, weighed and tested for compressive strength to determine the weight and strength loss after 45 and 60 days of ponding in agreement with the method adopted by Duraman et al. [23], which gives the intensity of sulphate ion attack on concrete. Fig. (6) shows the ponding of the concrete admixed with CS.
3. RESULTS AND DISCUSSION
3.1. Characterisation of Cassava Starch
The result of the particle size analysis of CS is presented in Table 5.
Constituent | Value (%) |
---|---|
Mean size | 15.27509µm |
Median size | 14.24354µm |
Specific surface area | 4921.8cm2/g |
From the analysis, The specific surface and the mean size of CS grains were 4921.8cm2/g and 15.275µm respectively. The result compares well with the findings of Petnamsin et al. [24] but higher than that of Akindahunsi and Uzoegbo [14], who both reported an average mean particle size of 15µm and 14.294µm respectively. The specific surface area of CS (4921.8 cm2/g) which is higher than the cement (4145 cm2/g) shows that the starch is finer than cement. CS will affect the cement in such a way that its granules will be adsorbed onto the cement, hence, leading to retardation during the induction period of cement hydration. This process slows the reactivity of C3A which is majorly responsible for the set properties of cement, while reducing the formation of ettringite in concrete. The reduction in the rate at which ettringite is formed also reduces the formation of mono sulphate aluminates, hence makes concrete more resistant to sulphate attack. The proximate analysis for the chemical composition of CS used for this research is presented in Table 6.
Constituent | Value (%) |
---|---|
Dry Matter (DM) | 88.21 |
Ash | 0.52 |
Ether extract, EE (Fat) | 0.59 |
Crude protein (CP) | 1.77 |
Crude Fibre (CF) | 0.63 |
Soluble carbohydrates (NFE) | 96.49 |
The chemical composition of cassava starch agrees closely with the report of Chinma et al. [25], thus confirming the starchy nature of the material used in this research. The starch content of the material is represented by the soluble carbohydrate content of 96.49%. This contains hydroxyl groups in its amylose and amylopectin structure which are partly responsible for the retarding effect of starch granules by reducing the reactivity of C3A when added to concrete and hence reduces the formation of undesired hydration products such as ettringite and unstable mono-sulphate aluminates. These products contribute to the susceptibility of concrete to sulphate attack.
3.2. Workability of CSMC
The slump of the different mixes of concrete containing different percentages of CS is presented in Fig. (7).
A decrease in the slump of CSMC observed as the CS content increased was increased, while other mix variables were kept constant. The slump of the CSMC (CS 0.0, CS 0.4, CS 0.8, CS 1.2, CS 1.6 and CS 2.0) were 98 mm, 75 mm, 64 mm, 34 mm, 29 mm, and 18 mm respectively. Based on these values, CS 0.0 has high workability, which is suitable for tremie placing like piling works where vibration is not suitable. CS 0.4 and CS 0.8 have medium workability which is suitable for normal reinforced concrete works. CS 1.2 and CS 1.6 have low workability which is suitable for mass concrete foundation, while CS 2.0 has very low workability, which is also suitable concrete used in rigid pavements Shetty [26]; Wilby [27]. The reduction in the workability of CSMC can be linked to the reduction in the flow characteristics of the resulting mix due to the viscous and thickening nature of the activated starch. Starch thickening occurs when starch is activated through gelatinization. This result agrees with the findings of Tan et al. [28]. Another factor is the water-absorbing nature of CS which will reduce the ratio of water to cement in the mix. A decrease in the water-cement ratio is expected to reduce the porosity of concrete while increasing its strength Shetty [26]; Day [29]. However, the absorption capacity of CS has to be optimized to ensure that there is enough water to aid full hydration of cement.
At 1.6% and 2.0% addition of CS, the resulting concrete is characterized by low and very low workability. The CS 1.6 and CS 2.0 mix will require extra work to achieve good compaction when compared with the other mixes. Low workability can lead to porous concrete. However, the likelihood of starch to form mud cake especially at 1.6% and 2.0% addition of CS can reduce the interconnectedness of pore spaces within the concrete, hence a decrease in concrete permeability. The results observed compare positively with the findings of Akindahunsi and Uzoegbo [14] but disagrees with Abalaka [8], Okafor [9] and (Joseph & Xavier) [30] who reported an increase in workability due to the use of ungelatinised starch in concrete.
3.3. Water Absorption of CSMC
The result of the water absorption of CSMC is presented in Fig. (8).
The results showed a gradual decrease in the water absorption capacity of CSMC from 1.48% for the control mix (CS 0.0) to 1.35% at 1.2% addition of CS by weight of cement before increasing for CS 1.6 and CS 2.0 concrete mixes. This decline represents a 9.45% decrease in the water absorption capacity of CSMC at 0.8 and 1.2% addition of CS in concrete respectively. The decrease in the water absorption can be linked to the reduction in micro-cracks within concrete due to the improved bonding between the aggregate and cement in concrete admixed with CS and the ability of the muddy-like starch paste to retard the flow of water into the pore spaces. However, the increase in water absorption at 1.6 and 2.0% addition of cassava starch can be directly linked to less dense concrete achieved at those percentages. This tends to increase the pore spaces in concrete which increases the ingress of water into the concrete until the spaces are saturated.
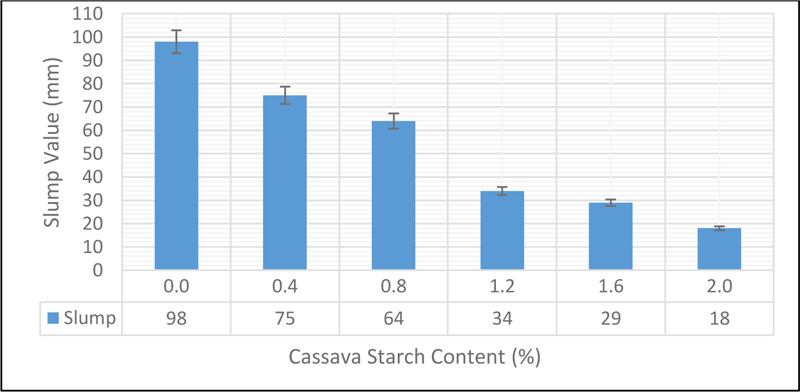
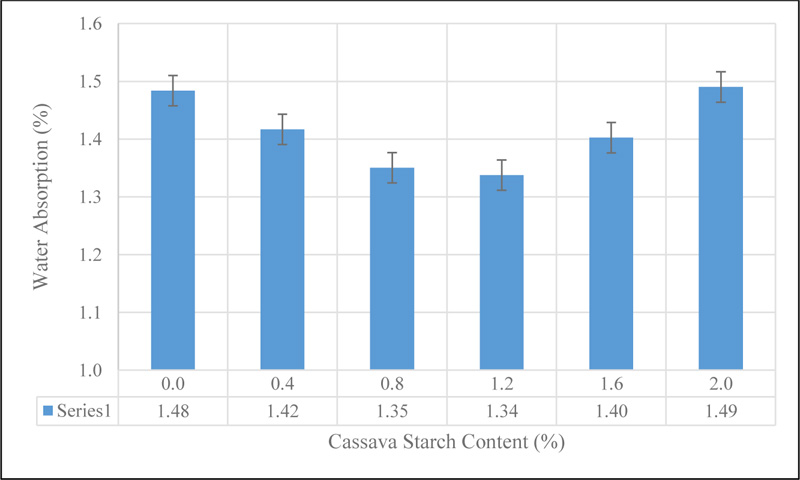
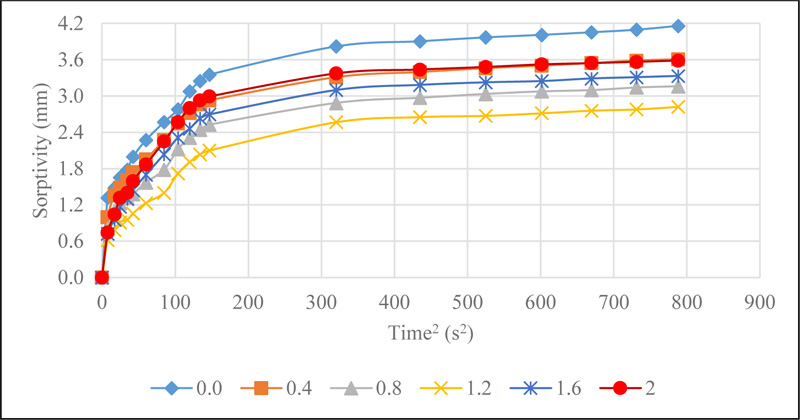
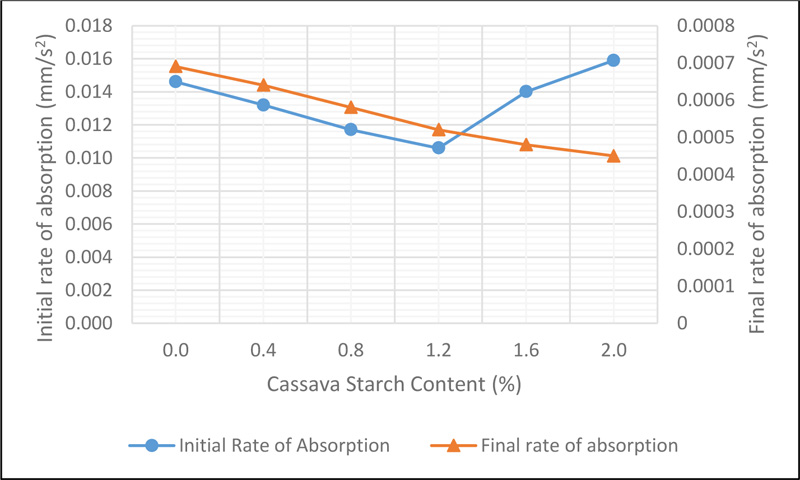
3.4. Sorptivity of CSMC
The results of the sorptivity of CSMC illustrated in Fig. (9).
Sorptivity of CSMC is a measure of the rate of absorption of water due to capillary action. This is influenced by the interconnectedness of the micro-pore spaces, which allows the capillary rise of water in concrete. The initial and final rate of absorption, which was determined by the slope of the best fit line plot of the sorptivity values against the square root of time is presented in Fig. (10).
Observations showed that the initial rate of water absorption decreased from 0.0146 mm/s 2 representing the control mix to 0.0107 mm/s 2 at 1.2% addition of CS before increasing for CS 1.6 and CS 2.0 . The decline can be linked to the muddy-like nature of activated CS which blocks the pore spaces, thereby reducing the rate at which water can freely move within concrete. However, the increase noted at 1.6% and 2.0% addition of CS can be said to be due to the less dense concrete achieved for each mix. This is because the viscous nature of the CS and an increase in its dosage led to a low workable concrete mix, hence, causing an increase in the number of pore spaces in the concrete until initial saturation occurs. However, once saturation occurs within the first 6 hours, the rate at which water rise due to capillary action will reduce as results show in the final rate of water absorption.
The final rate of water absorption which was measured between the interval of 6 hours and 9 days of the test, showed a decrease from 0.00066mm/s2 for the control mix to 0.00045mm/s2 for 2.0% addition of CS. The higher sorptivity rates as observed denote the existence of highly connected pore structure within the concrete and vice versa. A lower sorptivity value of concrete will reduce the rate at which aggressive chemicals such as chloride and sulphate ions diffuse into the concrete which will help its resistance to deterioration.
It was seen that the initial rate of water absorption was lower than the final rate of water absorption for all mixes. This is can be ascribed to the fact that the rate of water absorption reduced after the first six hours of the test due to concrete being saturated. The reduction in sorptivity values of concrete due to CS addition as observed reduces the rate at which water and moisture move within the concrete, thereby improving its durability characteristics.
3.5. Chloride Penetration of CSMC
The chloride penetration of CSMC is shown in Fig. (11).
The result showed a decrease in the penetration of chloride ions in concrete from 11.41 mm representing the control to 8.58 mm representing CS 2.0 at 45 days of ponding in sodium chloride solution, while the 60 days ponding also showed a decline from 12.10 mm for the control to 9.44 mm. The decrease in the extent of chloride penetration in concrete as the percentage of CS increased showed that the permeability of concrete is reduced with the addition of starch. The decrease in permeability of concrete can be ascribed to the jelly and muddy-like nature of activated CS which fills the pore spaces in the structure of the cement paste thereby leading to a reduction in the ease at which water moves in concrete. This decline in depth of penetration of chloride ions in concrete reduces the risk of exposing reinforcement to corrosion in reinforced concrete structures. This result compares well with the findings of Sindhu et al. [31] who reported that concrete containing starch is less permeable to chloride diffusion. The result of the chloride penetration coefficients which further supports the ability of CS to reduce the diffusion of chloride ions into the concrete is presented in Table 7.
The result showed that at 45 days, the chloride diffusion coefficient reduced from 0.1809 cm2/s for CS 0.0 to 0.1021 cm2/s for CS 2.0. The same trend was noticed at 60 days of exposure where the value reduced from 0.1525 cm2/s to 0.0928 cm2/s. Also, the diffusion coefficient of each mix designation at 60 days was lower than the value determined at 45 days, which suggests that the penetration of chloride ions in the concrete reduces with exposure days. This observation affirms that the rate at which water is absorbed in concrete reduced as discussed in section 3.4.
The depth of penetration of chloride ions in concrete after 45 and 60 days of ponding was determined by measuring the depth of the formation of white precipitates of Silver Chloride on the concrete surface when 3% Silver nitrate solution was sprayed on it. The dark brown region shows the part where the ions could not penetrate, as seen in Fig. (11). The results of the depth of penetration of chloride ion in concrete are illustrated in Fig. (12).
Mix No. | Chloride Penetration, x - 45 days (mm) | Chloride Penetration Coefficient, D – 45 days, (cm2/s) | Chloride Penetration, x - 60 days (mm) | Chloride Penetration Coefficient, D – 60 days, (cm2/s) |
---|---|---|---|---|
CS 0.0 | 11.41 | 0.1809 | 12.10 | 0.1525 |
CS 0.4 | 10.61 | 0.1564 | 11.18 | 0.1301 |
CS 0.8 | 9.91 | 0.1365 | 10.59 | 0.1168 |
CS 1.2 | 9.21 | 0.1179 | 10.14 | 0.1071 |
CS 1.6 | 8.74 | 0.1060 | 9.76 | 0.0993 |
CS 2.0 | 8.58 | 0.1021 | 9.44 | 0.0928 |
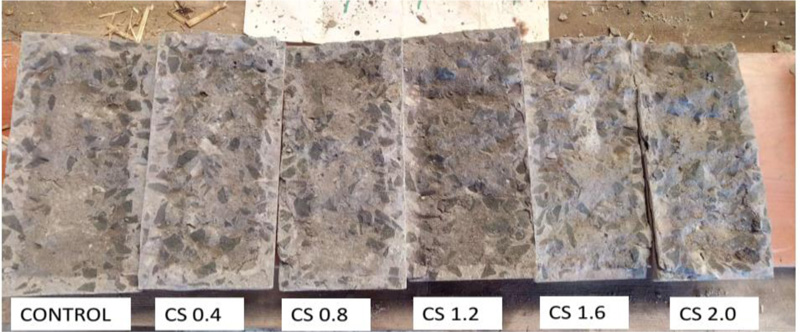
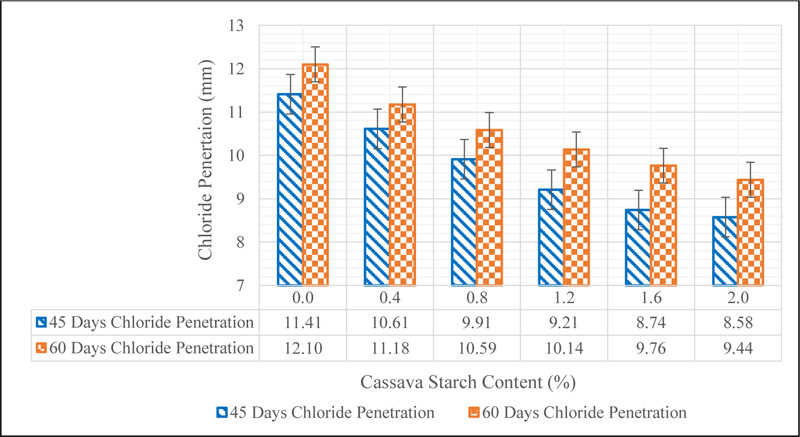
3.6. Sulphate Attack on CSMC
The gradual deterioration of concrete after ponding in a sulphuric acid solution is shown in Fig. (13).
This attack is characterized by the formation of white sludge on the concrete surface after exposure to sulphate ions. This causes an onward dissolution of the calcium silicate hydrates for as long as the concrete remains in the sulphate environment thereby causing a mass loss. The rate of dissolution of the cement hydrates is reduced as the CS dosage increases. This suggests that CS reduces the reactivity of calcium silicate hydrates with sulphate ions due to the ability of the starch granules to be adsorbed to the surface of the cement grains. The results agree with the findings of Akindahunsi and Uzoegbo [32]. The results of the weight loss in comparison with the 28-day mean weight are shown in Fig. (14).
The effect of sulphate on concrete was measured by the percentage loss in weight and strength after ponding in a sulphuric acid solution of pH 3 for a period of 45 and 60 days. At 45 days of ponding in sulphuric acid solution, a 14.16% loss in weight was observed for the control concrete while a 3.39% loss in weight was observed for 2.0% addition of CS. At 60 days of ponding, the control lost 14.47% of its weight while CS 2.0 lost 4.44%. The loss in weight was caused by the gradual deterioration of concrete surfaces due to the sulphate ion attack. The result of the compressive strength of CSMC after ponding for 45 and 60 days in comparison with the 28-day strength is shown in Fig. (15).
From the data shown above, it was observed that the sulphuric acid solution had a damaging effect on the strength properties of concrete. This can be linked to the loss of hydration products in concrete which is unstable in the presence of sulphate ions. Also, it can be seen that the rate of strength loss was reduced with an increase in CS content in concrete. This suggests that CS can help reduce the rate at which concrete is attacked in sulphate environments. A measure of the loss in strength as a percentage of the 28-day compressive strength is presented in Fig. (16).
A 27.37% loss in strength was observed for the control (CS 0.0) while 7.75% loss in strength was observed for CS 2.0. Similarly, 32.25% loss in strength was observed for the control at 60 days ponding and 10.17% loss was observed for CS 2.0. The improvement in the resistance of concrete admixed with CS can be linked to the decrease in the formation of unstable mono-sulphate aluminate hydrate, which is a second-order hydration product in cement hydration. This is so because CS reduces the formation of the first-order hydrate, ettringite by the adherence of the starch granules to C3A and C3S as discussed in section 3.1, thereby, reducing the susceptibility of concrete to sulphate attack. This result is in agreement with the findings of Akindahunsi and Uzoegbo [32] who concluded that “Starch concretes gave better resistance to the ingress of sulphate ions”.
3.7. Effect of Sodium Hydroxide on CSMC
The result of the effect of sodium hydroxide solution on concrete after ponding is shown in Fig. (17).
It can be seen from Fig. (17) that there is no deterioration of the concrete after ponding in sodium hydroxide solution of pH 12. This suggests that sodium hydroxide ion does not have any adverse effect on concrete in contrast to what was noticed when concrete was ponded in sulphate environment. The results of the change in strength when CSMC was ponded in sodium hydroxide solution is shown in Fig. (18).
There was a general increase in the strength of concrete as observed in Fig. (18) in comparison to the 28-day mean strength for all mixes. The 45-day strength for all concrete mixes (CS 0.0, CS 0.4, CS 0.8, CS 1.2, CS 1.6 and CS 2.0) are 49.67, 50.52, 50.94, 50.67, 49.35 and 48.87 MPa, while the 60-day strengths are 50.15, 50.83, 50.88, 50.55, 49.17 and 48.65 MPa respectively. These results show that sodium hydroxide does not adversely affect the strength properties of concrete asserting the fact that concrete is an alkaline material. However, a drop in strength was noticed between 45 and 60 days of ponding for CS 0.8, CS 1.2, CS 1.6 and CS 2.0. This may be linked to the hydroxyl group of CS which increases the concentration of hydroxides within the matrix of the cement hydration products which otherwise may have a negative effect in concrete Shetty [26].
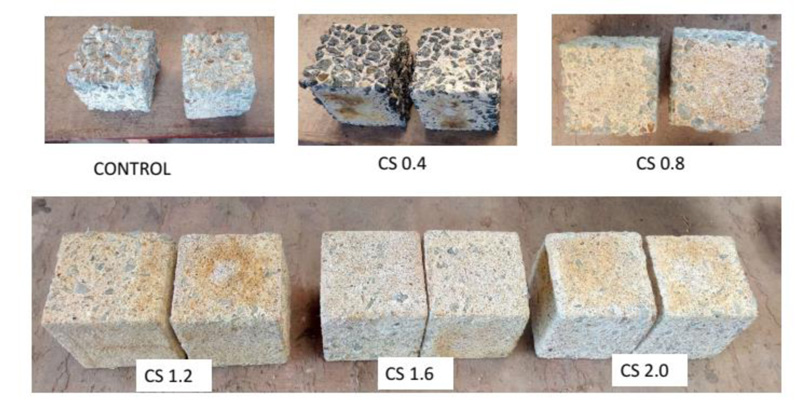
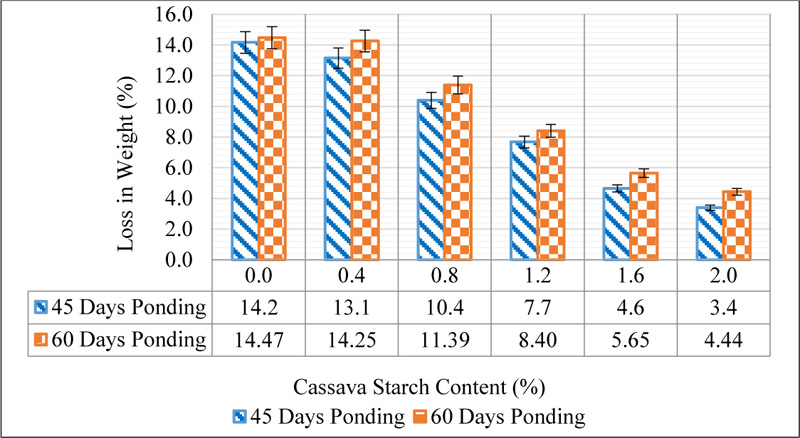
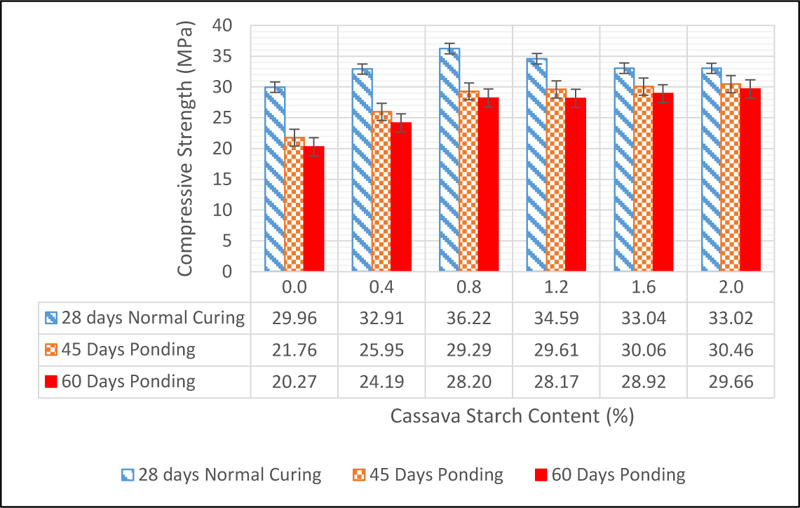
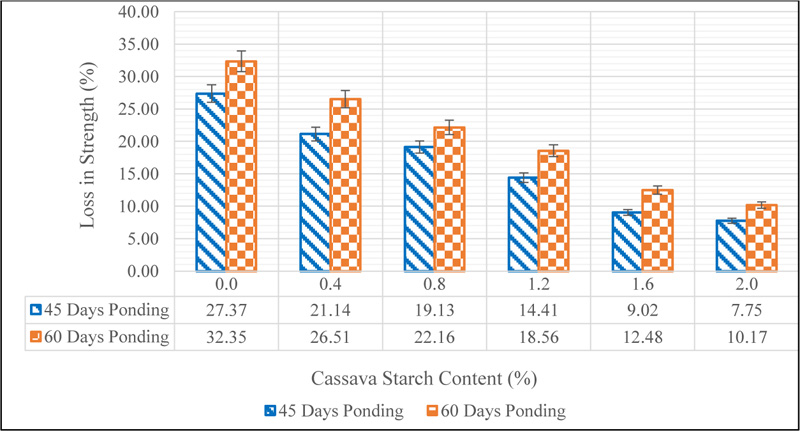
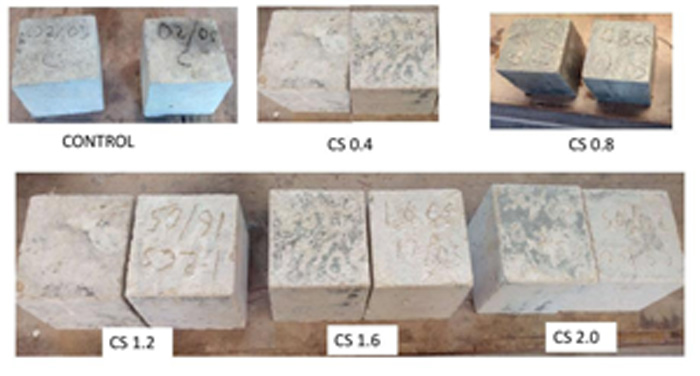
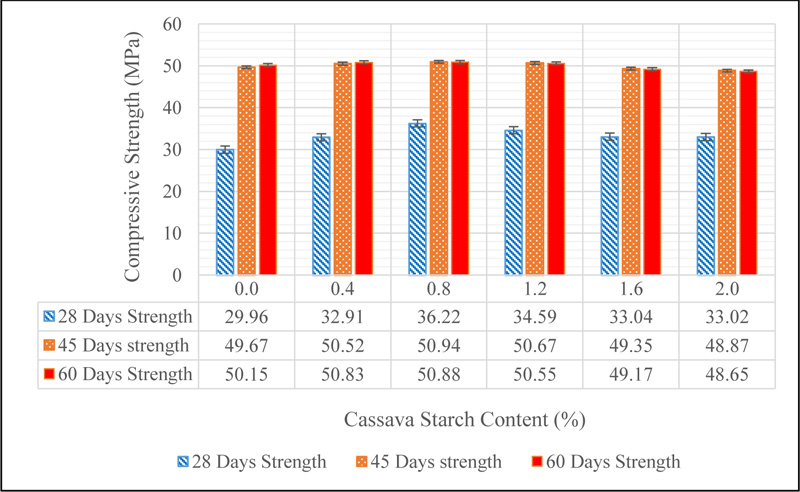
CONCLUSION
The conclusions based on the investigation of the effect of cassava starch on the durability characteristics of concrete is as follows;
The addition of CS to concrete by weight of cement reduces concrete workability. Cassava starch helped reduce the rate of water movement within the pore structure of concrete, hence, improves its resistance to chloride penetration. The retarding ability of cassava starch helped reduce the formation of mono-sulphate aluminates, hence, makes concrete less susceptible to sulphate attack. It was observed that concrete was less susceptible to attack from sodium hydroxide solution when compared to sulphuric acid solution. The comparative analysis of the concrete mixes showed that CS 2.0 gave a better resistance to chloride penetration and sulphate attack.
AUTHOR CONTRIBUTIONS
D.O.O. and J.M. designed the research; D.O.O. carried out the research; D.O.O., J.M. and C.K. analyzed the results; D.O.O. wrote the Paper; J.M. and C.K. reviewed and edited the final paper.
CONSENT FOR PUBLICATION
Not applicable.
AVAILABILITY OF DATA AND MATERIALS
The data that support the findings of this study are available from the corresponding author, [D.O., J.M., C.K.], upon request.
FUNDING
None.
CONFLICT OF INTEREST
There is no obligation or financial liability to any other third party. Therefore, the authors declare no conflict of interest.
ACKNOWLEDGEMENTS
The authors express their appreciation to the Pan African University, Institute for Basic Science, Technology and Innovation (PAUISTI), as well as Jomo Kenyatta University of Agriculture and Technology, for providing the laboratory where this research was performed.