All published articles of this journal are available on ScienceDirect.
Mechanical Strength and Water Transport Properties of Concrete Containing Treated Recycled Aggregates
Abstract
Objective:
The objective is to determine the effect of treated RCA on the mechanical strength of hardened concrete, and determine the influence of treated RCA on water transport within the matrix of hardened concrete.
Aim:
The study aims to use pozzolanic concentration of cement and RHA slurry to pretreat coarse RCA for full replacement of NCA for sustainable concrete production.
Background:
One of the common modes of disposal of construction waste is strained landfills. This study proposes a constructive way of recovering the coarse aggregates of recycled aggregates from laboratory concrete waste taken through a focused treatment process with pozzolan. The study aims to replace the proportions of the cement slurry to treat and replace with rice husk ash (RHA) for the modification of recycled concrete aggregate (RCA) and replace fully natural coarse aggregate (NCA) for sustainable concrete production. One of the main challenges of recycled concrete aggregate (RCA) is the fractured surface, which often results in reduced strength and loss of concrete durability. The strength of concrete with RCA is principally influenced by the fractured hardened paste attached to the surface, predominantly characterized by voids and gaps resulting from its production using a mechanical method. High water penetration within and around the aggregate matrix due to the presence of micro- and macro-cracks results in strength and durability deterioration of concrete.
Methods:
This study addresses these problems by specifying aggregate treatment with a pozzolanic slurry of cement and RHA. This was conducted in two (2) phases; first, to determine the optimum proportion of cement slurry concentration (0, 20, 40, 60, 80, and 100%), and second, to increase the silicate formation in cement slurry by substituting the proportions of cement with RHA (0, 5, 10, and 15%). The performance of concrete was evaluated by mechanical strength (compressive and split tensile strength) at 7, 28, and 56 days and water transport within the concrete (surface suction and submergence) at 28 and 56 days of curing age.
Results:
The use of cement slurry treatment at various concentrations generally increased compressive strength at 28 days compared to untreated RCA. The findings show that at a 20% concentration of cement slurry, the increase in compressive strength is 38.4%. Upon replacement of cement in treatment slurry of RCA with 5% RHA, the increase in compressive strength was 61%, while the split tensile strength increased by 10.2%. The amount of water absorbed was observed after 30 minutes of full submergence in water, indicating that samples with 20% cement concentration at 28 days resulted in the lowest water absorption of 2.01%. However, with the replacement of 5% RHA, the water absorption slightly increased to 2.3%, but still less than the requirement of 3.5%. The corresponding test results for water suction by capillarity, initial and secondary sorptivity coefficients (Si and Ss) were found to be 0.0330mm/√sec. (1.98mm/√hr.) and 7.95×10−4mm/√sec. (0.04mm/√hr.) respectively, all less than 6mm/√hr requirement. This improved performance was attributed to the increased strength and structure of the interfacial transition zone (ITZ) around the RCA.
Conclusion:
Based on the results of mechanical strength and water transport, characteristics of the new concrete were improved when coarse RCAs were pretreated with 20% pozzolanic concentration containing cement and RHA. The use of a pozzolanic treatment slurry containing 15% cement and 5% RHA to treat coarse RCA can produce concrete with characteristics similar to those of natural concrete aggregates. This study presents a methodological utilization and improvement of RCA wastes for field application.
1. INTRODUCTION
The demand for concrete in the world has been on an increasing trend; annually, the world consumes approximately 48.3 billion tonnes [1]. Concrete is the most preferred construction material owing to its low chemical reactivity, strong compression resistance, and more durable and can be manufactured from local materials. In Kenya, the construction industry has been booming, consuming about 800 million tonnes per year [2]. Infrastructural development is measured by the physical facilities such as good roads and structural buildings, which consume a lot of concrete. This has prompted the development of alternatives for concrete replacement and elimination of resulting wastes, which are less costly and environmentally viable [3]. These facilities consume a lot of aggregate and cement to the tune of 1.6billion metric tonnes being the main binder of the aggregates [4]. Due to the ever-limited space in urban areas, the desire to further development has meant the demolition of existing or dilapidated facilities. This leads to the generation and production of construction waste in the form of aggregate rubbles.
Construction is also one of the major contributors to waste and environmental pollution associated with the depletion of resources from quarry sites; the only remedy is to utilize the generated waste constructively to minimize the side effects. There has been a general trend to utilize recycled concrete aggregates (RCA) produced in construction to minimize the burden on landfills [5]. The utilization of RCA to substitute NCA in concrete production decreases the environmental pollution associated with RCA disposal. To date, only a small portion of RCA is used for structural purposes owing to its low quality compared to NCA.
However, challenges with the direct application of RCA have generally been associated with its reduced structural performance. The RCA is regarded as a composite material consisting of natural aggregates and adhered surface mortar [6-10]. Adhered surface mortar is made of old hydrated cement paste that exhibits structural problems because it is physically characterized by numerous fractured macro and micro-cracks, probably due to the originally sustained load or crushing during the production process. Previous studies have shown that the old ITZ of RCA makes the new concrete microstructure more fragile because of higher porosity and cracks, which could have resulted during processing stage fractures or due to the poor quality parent concrete, thus acting as the weak link [1]. Given the challenges arising from the weak structure of RCA, the viable solution would be to develop a mechanism that will manipulate the surface structure before any attempt to recommend structural concrete.
Studies have shown that the adhered mortar on the surface defines the most important features of the resulting concrete, that is, reduced compressive strength [10], high water absorption [1, 10-13], high porosity [14], reduced work ability [10], high chloride attack [10], and highly porous structure likely to cause high sorptivity [15]. This being the case, research by Marinković, Radonjanin, Malešev, & Ignjatović [16] recommended partial substitution of RCA with NCA to a maximum 50%. However, other studies which have utilized 100% substitution of NCA with RCA, have also reported lower performance, hence recommending its use to be limited to non-structural developments [11, 17], or as road sub-base material [18-21].
Water penetration is a key component in the durability of concrete as it carries deleterious agents, such as chloride and sulphate, into the matrix of a cement-based material. Infact, the main cause of the difference in the rate of water movement between RCA and natural aggregate is the old mortar attached to recycled aggregate [22]. The study by Liu et al. [22] further demonstrated that the volatility and water penetration in concrete is a direct function of the proportion of RCA in concrete. Goracci, Monasterio, Jansson, & Cerveny [23] noted that the movement of water at different time scales in concrete depends on the pore size and networks. Similarly, a study by Olorunsogo & Padayachee [24] demonstrated that water sorptivity of concrete depends on the proportions of and curing age of concrete with recycled aggregate (RA). The study observed sorptivity reductions for the 50% and 100% replacement of recycled aggregate of concrete mixes were 42.7% and 44.0%, respectively. The 100% replacement of RCA in concrete mix attained the ‘poor’ category at the age of 28 days with a sorptivity value of 14.48mm/√hr [24].
Sustainable development all over the world should be carried out effectively without numerous time-to-maintenance activities. For this reason, structural concrete should not just be strong but should also adhere to durability requirements. In fact, water absorption characteristics are an indicator that is correlated with the mechanical and durability characteristics of concrete [1, 12]. Water absorption within the aggregate structure is essential because, with water in the pores, it will attract dangerous chemicals and solutions [25]. For this reason, water absorption has received a lot of attention because water-induced corrosion is a major problem that reduces concrete durability [26], and concrete strength deterioration [1, 27-31].
With the magnitude of development ever going on, recent studies have now focused on a positive adventure adding pozzolan to improve the performance of concrete [32] [33]. ITZ treatment method by ground granulated blast furnace slag (ggbs) pozzolan “W3T4” involving three parts of adding water and four stages of mixing procedures has been proposed by H. L. Wang et al. [32]. However, this has not been given full attention, especially given the cost of some pozzolans being high. Therefore, the challenge of concrete made with RCA persists.
RHA is one of the pozzolans that could be used with a targeted approach as a treatment agent for the adhered mortar to improve aggregate performance in concrete [34]. Rice husk is an agricultural product commonly found in the central and western parts of Kenya. Ash (from burnt rice husks) has been found to be a siliceous element [28, 35] in the proportion of about 75% and above chemical proportion [36]. As a pozzolanic material, its utilization has to be initiated by water and cement to be fully effective in forming hydrated calcium silicate [28]. The utilization of RHA as pozzolan in concrete enhances latent hydrations that produce a dense, insoluble calcium silicate hydrate (C–S–H) gel, having the potential of filling the voids from the reaction of siliceous oxide with calcium hydroxide or free CaO in the concrete pore water [32]. Hence, the compressive strength of the concrete mix increases.
However, cost remains a major issue in the attempt to improve the performance of RCA. One fact is that these aggregate (RCA) materials, which have reached their full life and contributed to an environmental deterioration in terms of used cement leftover quarries of aggregate, now the adoption should be subjected to a cheap and affordable mechanism that could reduce the consumption of cement better. The sustainability issues in its utilization cannot be wished away. This research adopts the proportionate use of pozzolanic cement and RHA to develop the optimum treatment without reducing the mechanical strength and water transport characteristics.
2. MATERIAL PROPERTIES AND METHODS
2.1. Cement
In this study, Ordinary Portland Cement of grade 42.5N Type CEM I, used for concrete mixing, was sourced from local hardware-based in Juja, Kenya. The results of the chemical analysis according to BS EN 196-2 [37] show that the proportions of calcium oxide, CaO, were 82.6%, which is dominant, followed by the proportion of silicon oxide, SiO2, at 7.1%, as shown in Table 1. This is an indication of high early strength development cement in concrete or mortar mix. In this study, cement type is not a variable hence was obtained from one source. Other preliminary results of the tests conforming to BS 12 [38] were conducted on cement, including standard consistency tests, setting time and soundness tests [39], and specific gravity [40] to ascertain its quality for use in this study. The specific gravity of cement was 2.87±0.06, standard consistency 36.25±0.79% and initial and final setting times found to be 87±5.10 and 323±6.02 minutes, respectively, meeting the requirements set out in KS-EAS18-1 [41].
Content | Quantities (%) |
---|---|
Silica, SiO2 | 7.10 ± 0.05 |
Calcium, CaO | 82.60 ± 0.11 |
Phosphorus, P2O5 | 1.43 ± 0.02 |
Iron, Fe2O3 | 3.14 ± 0.06 |
Aluminium, Al2O3 | 1.95 ± 0.03 |
Others | 3.78 ± 0.09 |
*LOI (%) | 3.80 ± 0.07 |
2.2. Fine Aggregates
River sand was purchased from sand suppliers from River Ewaso Nyiro, Urchers Post, Isiolo County, Kenya. Natural fine aggregates constitute those fractions from 150μm to 5mm for standard sieves. The following tests were carried out to ascertain the quality of the sand; sieve analysis for fine aggregate and fineness modulus [42], specific gravity and water absorption [43], moisture content [44], and silt content [45]. The results of the particle gradation are represented graphically in grading curves, as shown in Fig. (1). The natural fine aggregates were found to have a fairly fine grading conforming to the limiting requirements for fine grading stipulated in BS 882 [46]. The fineness modulus was found to be 2.73, which is within the range of 2.8–1.5 for medium fine sand [47]. The test results for other physical properties of the fine aggregates are shown in Table 2.
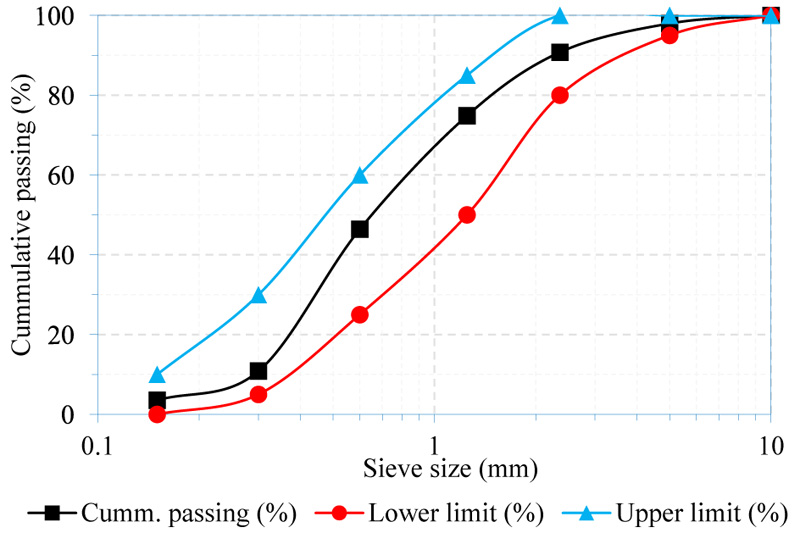
Properties | Value | Remark |
---|---|---|
Specific gravity (SSD condition) | 2.59 ± 0.04 | 2.5–3.0 |
Specific gravity (Oven dry condition) | 2.50 ± 0.08 | 2.5–3.0 |
Bulk density | 1.49 ± 0.04 | – |
Voids (%) | 40.3 ± 4.51 | – |
Water absorption (%) | 3.78 ± 0.11 | – |
Fineness modulus | 2.76 ± 0.15 | 2.3–3.1 |
Water content (%) | 0.40 ± 0.05 | – |
Silt content (%) | 6.50 ± 0.99 | < 8.0 |
Grading zone | Zone II | OK |
2.3. Coarse Aggregate Sourcing and Preparation
The size of natural coarse aggregate (NCA) used in this research ranged between 5–20mm. The natural coarse aggregates were sourced from a local supplier, Warren Concrete Limited (K), in Kiambu County, Kenya. One of the challenges with recycled concrete aggregates (RCA) is the determination of consistent quality from sources. Natural coarse aggregates were used to design class C30 concrete, then used to prepare cubes, cylinders, and beams, which were tested and again recrushed into the desired aggregates, maximum size 20mm, to maintain and ascertain the uniformity of the source of RCA. The mix details of the parent concrete are shown in Table 3. These aggregates were properly sieved to comply with the requirement of BS 882 [46] requirement before being used (Figs. 2 and 3). Physical properties such as particle size distribution, specific gravity, bulk density, and others were assessed, as shown in Table 4.
Specifications | Values |
---|---|
Water -to- cement ratio | 0.54 |
Cement (kg/m3) | 389 |
Water (kg/m3) | 210 |
Fine aggregates (kg/m3) | 645 |
Coarse aggregates (kg/m3) | 1052 |
Average compressive strength MPa | 34 ± 4.49 |
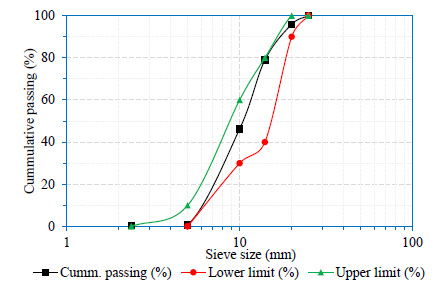
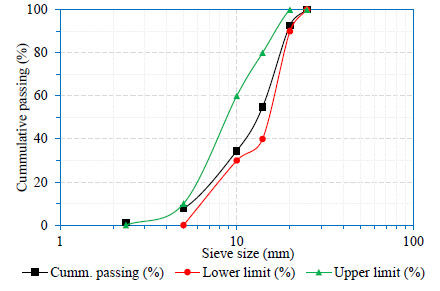
From Figs. (2 and 3), the coarse aggregates were well graded, which is within the grading envelope as provided in BS 882 [46]. This meant that the coarse aggregates used in concrete for this investigation met the necessary criteria and could thus be utilized to produce concrete for the research without the need for blending. The particle size distribution of RCA is similar to the sieve curve of natural coarse aggregate, with little variation.
The aggregates were composed of natural aggregate with attached surface mortar, as shown in Fig. (4). RCA had a larger absorptive capacity and lower bulk density compared to natural coarse aggregates. The presence of an adhering mortar on the surface of RCA is responsible for these outcomes. The natural coarse aggregate had the lowest water absorption and the highest bulk density since there was no adhering mortar, as in the case of RCA (see Fig. 4).
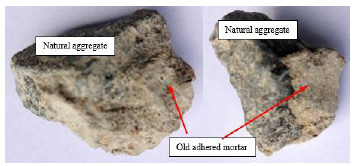
Properties | NCA | RCA |
---|---|---|
Specific gravity (SSD condition) | 2.54 ± 0.07 | 2.4 ± 0.06 |
Specific gravity (oven dry condition) | 2.45 ± 0.12 | 2.25 ± 0.08 |
Bulk density | 1.6 ± 0.08 | 1.42 ± 0.09 |
Voids (%) | 40.1 ± 3.12 | 44.2 ± 6.35 |
Water absorption (%) | 3.36 ± 0.17 | 6.44 ± 0.36 |
Fineness modulus | 2.78 ± 0.08 | 3.33 ± 0.18 |
Water content (%) | 2.82 ± 0.03 | 3.3 ± 0.10 |
Aggregate impact value (%) | 8 ± 1.20 | 19.2 ± 2.07 |
Aggregate crushing value (%) | 14.8 ± 1.37 | 24.4 ± 2.19 |
Strength of parent material (MPa) | – | 34 ± 4.49 |
Content | PC (%) | RHA (%) |
---|---|---|
Silica, SiO2 | 29.36 ± 0.01 | 88.18 ± 0.09 |
Potassium, K2O | 2.62 ± 0.01 | 3.85 ± 0.01 |
Calcium, CaO | 54.95 ± 0.03 | 2.94 ± 0.02 |
Aluminium, Al2O3 | 4.62 ± 0.01 | _ |
Iron, Fe2O3 | 4.74 ± 0.02 | 0.92 ± 0.01 |
Others | 3.71 ± 0.01 | 4.11 ± 0.01 |
*LOI (%) | 4.19 ± 0.02 | 4.59 ± 0.01 |
*LOI = Loss of ignition according to BS EN 196-2 [37] |
2.4. Properties of Pozzolanic Cement and Rice Husk Ash
In this research, pozzolanic cement (PC) and RHA were used to treat the surface of recycled concrete aggregate (RCA) in a slurrinated form. Pozzolans (PC and RHA) were procured from the country Kenya. Rice husk ash (RHA) was prepared by burning rice husks for 2hr. at 450oC. RHA powder was first sieved through a 0.30mm sieve size. The RHA and the pozzolanic cement were taken for chemical analysis to ascertain their key mineral compositions which are given in Table 5. shows that RHA has a high content of amorphous silicon, SiO2 (at 88.18%), while the pozzolanic cement (CEM II) has a high calcium oxide, CaO, (at 54.95%). These components are important in the hydration process during the surface treatment of RCA. The hydration process is enhanced because the surface of the RCA also contains calcium hydroxide in addition to those produced by the hydration of the pozzolanic cement, which would fill the gaps in the RCA [27]. RHA cannot be used alone but with pozzolanic cement (PC) that facilitates the binding effect in a proportion of cement. This RHA used in this research was classified as class N pozzolan because silica, SiO2, the proportion is greater than 70% [48].
2.5. Surface Treatment Method of RCA
To strengthen the surface of RCA, the adhered mortar, and the improved properties of RCA using cement slurry and RHA, the treatment process was achieved in two phases. First, cement slurry was used to treat in five (5) different treatment concentrations at an interval of 20% by weight of RCA (see Table 6). This was to determine the best concentration to effectively treat the aggregates (RCA). Second, proportions of RHA were used to replace content cement at an interval of 5%, as shown in Table 6. The slurry was prepared by first applying 20% of the treatment water to RCA, and then the remaining 80% of the treatment water for preparation of pozzolanic slurry. RCA was introduced into the slurry, stirred for 5 minutes, and then soaked for 15 minutes. The aggregates were then removed from the treatment bath in a moist state. The coated aggregates were further air-dried at room temperature of 20°C for 3 days. Finally, the hardened RCA was sieved to remove the fine particles before carrying out the material tests.
Treatment slurries | Pozzolan concentration | Binder (kg) | RCA (kg) | Water (kg) | Binder to water ratio | |
---|---|---|---|---|---|---|
PC | RHA | |||||
20% PC | 20% | 20 | - | 100 | 100 | 2:10 |
40% PC | 40% | 40 | - | 100 | 100 | 4:10 |
60% PC | 60% | 60 | - | 100 | 100 | 6:10 |
80% PC | 80% | 80 | - | 100 | 100 | 8:10 |
100% PC | 100% | 100 | - | 100 | 100 | 10:10 |
20%PC&0%RHA | 20% | 20 | 0 | 100 | 100 | 2:10 |
15%PC&5%RHA | 20% | 15 | 5 | 100 | 100 | 2:10 |
10%PC&10%RHA | 20% | 10 | 10 | 100 | 100 | 2:10 |
5%PC&15%RHA | 20% | 5 | 15 | 100 | 100 | 2:10 |
2.6. Mix design and proportions for concrete mix
In this study, concrete mix design was done using the Department of Environment (DOE) Method of concrete mix design. The chosen target slump for all fresh concrete was maintained at 30–60mm. The design concrete was class C30 using cement grade 42.5 (CEM I). The total aggregates content used were clean and clear aggregates, having a maximum size of 20mm and the percentage of fines passing the 600μm sieve was 39.5%. The summary of the mix proportions used is shown in Table 7.
Contents | NCA | RCA |
---|---|---|
Cement (kg/m3) | 389 | 389 |
Water (kg/m3) | 210 | 210 |
Fine aggregates (kg/m3) | 670 | 635 |
Coarse aggregates (kg/m3) | 1027 | 993 |
w/c ratio | 0.53 | 0.55 |
Proportion of mix | 1:0.53:1.73:2.64 | 1:0.55:1.66:2.60 |
2.7. Tests on Hardened Properties
The mechanical properties of concrete were determined using density, compression strength [49], and split-tensile strength [50] for cubes and cylinder samples, respectively, at 7, 28, and 56 days. The tests were conducted on a UTM machine named Servo Plus Evolution, which has a load capacity of 1500 kN and a loading rate of 0.5 kN/sec. The test setups were as shown in Fig. 5 (a) and (b), and the numerical values were computed using Equations (1) and (2), respectively.
Concrete water transport in the concrete mix was assessed by the rate of water absorption [51] and the determination of water sorptivity [52] for the concrete samples at 28 and 56 days. A water absorption test was done by full submergence of cube samples to determine the rate of water penetration into the concrete [51] conducted, as shown in Fig. 5 (c). The cumulative amount of water absorbed was calculated using Equation (3). The Sorptivity test measures the capillarity rise of water within the pores of the concrete. The concrete samples were oven-dried at 51.5ºC for 72 hours as specified by ASTM C1585/C1585M (2007). Initial (Si) and secondary (Ss) sorptivity suction for short and long-term exposure of the concrete core surface to water were investigated, as shown in Fig. 5 (d). Sorptivity was obtained from the slope of the linear regression analysis of the plot of I (mm3/mm) against the square root of time (√sec.). The sorptivity coefficient was calculated using Equation (4).
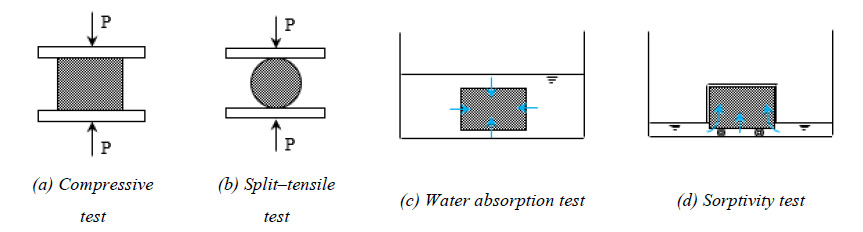
![]() |
(1) |
![]() |
(2) |
![]() |
(3) |
![]() |
(4) |
Where P – load, A – cross-section area, L and D –dimensions of the cylinder (length 200mm and 100mm diameter), Wo – original weight of the sample after oven drying, Wsub – sample weight after submergence in water within the period, I – cumulative absorption at time, t – elapsed time in seconds, Δw – change in weight = W2 – W1, d= density of water.
3. RESULTS AND DISCUSSIONS
3.1. Workability of Concrete Mix
The workability test for fresh concrete is the most crucial test due to the absorption of water by RCA. This test was conducted according to BS1881-102 [53], noting the difference in the initial and final concrete slump. Fig. 6 show a pictorial display of slump measures for concrete mixes with natural coarse aggregate and recycled concrete aggregate, respectively. Normal concrete generally shows a smooth and stable concrete slump, while the concrete mix with RCA shows a rough surface. There was a uniform mix in a concrete mix containing NCA, while for concrete with coarse RCA, it was an inconsistent mix, probably due to continued absorption of the mixing water.
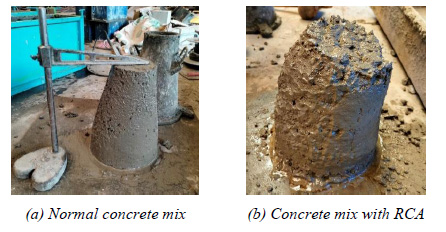
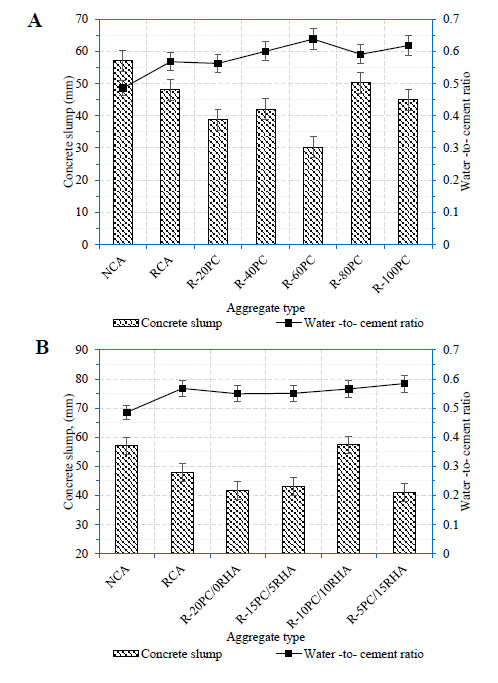
In this study, the slump was fixed by a mixed design range of 30–60mm for maximum aggregate size of 20mm. For concrete with natural coarse aggregate, the average slump was 57mm, however, for concrete with coarse RCA, the slump was reduced to 48mm and the water demand to achieve the target slump increased in varied proportions of pozzolanic treatments. Fig. (7a) illustrates the effect of cement slurry treatment for RCA on the workability of concrete mix. The sample with 20% cement slurry treatment (marked R–20PC) resulted in the least water demand at 15.8%, which was achieved by a slump of 38.1mm; this is still within the target slump of 30–60mm. Probably with 20% treatment, there was an optimal pozzolanic reaction on the surface of the aggregates that formed the C–S–H gels that filled the voids of the adhered cement paste, resulting in low water demand. However, samples with 60% pozzolanic treatment had the highest water demand of 31.3% in the concrete mix. Workability was reduced by 46.8% (30.3mm) compared to control concrete with natural coarse aggregate. Treatment of aggregate with cement slurry above 20% concentration, a lot of unreacted elements remain on the surface of the aggregate leading to increased water demand.
Again, Fig. (7b) represents the effect of treatment with RCA on the proportion of cement and RHA slurry at 20% concentration on the slump. At 20% pozzolanic concentration, samples marked R–20PC, and R–15PC/5RHA revealed no significant difference in water demand (as 13 and 13.4%) to achieve a workability slump of 30–60mm. This implies that by replacing RHA less than 5%, there was adequate C–S–H gel that fills the gaps on the surface of the RCA, resulting in fewer cracks and voids and, therefore, An adequate chemical reaction process could have been achieved in the treatment with C–H on the surface of RCA, cement, and RHA, leading to the formation of additional C–S–H to seal the gaps around the aggregate.
Both untreated and treatment of RCA with substitution of RHA beyond 5% resulted in increased water demand above 15%. The additional water demand could be due to the presence of more voids and micro-cracks within the surface of aggregates. The presence of microcracks could be aggravated by the presence of or more unreacted RHA elements known to have high fineness and a more porous surface structure [54], enabling it to attract more mixing water. This could also have the side effect of enabling an incomplete hydration process that leads to the formation of a filling C–S–H gel to seal voids in the aggregate structure.
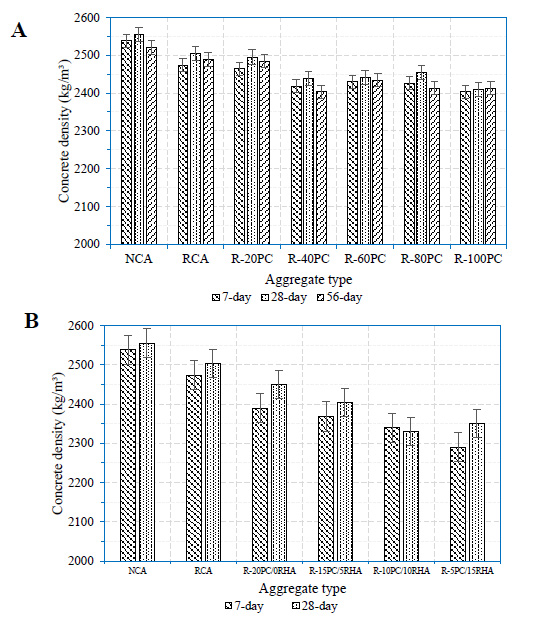
3.2. Concrete Density
The test on concrete density was done according to BS 812-Part 2 [55] of hardened concrete density properties. Fig. (8a) illustrates the dry density of concrete determined using 100mm cubes of concrete with different treatments at 28 and 56day. The control concrete samples done with NCA gave a density of 2555kg/m3, which was the highest compared to other categories of RCA (treated and untreated). The results of the average concrete density for all treated aggregates ranged from 2408 to 2504kg/m3 for dry concrete at 28day. From the standard error of 95% CoV, there was no significant difference in dry density development; however, the density appears to decrease as the concentration of cement slurry treatment increases. The sample marked R–100PC indicated the lowest density in the category of aggregates treated with cement slurry. The decreasing trend in the density could be explained by excess unreacted pozzolans, which occupy the voids of RCA, while for untreated RCA, the density could be due to empty pores and voids around the aggregate, which could be occupied with pore water.
Again, in Fig. (8b), for concrete samples made with coarse RCA, which were treated with cement and RHA slurry, the error bars at 95% CoV indicate an inconclusive variation in the dry density of concrete. Interestingly concrete done with untreated coarse RCA resulted in a density of 2504kg/m3, higher compared to concrete samples containing treated coarse RCA, as shown in Fig. (8). However, the sample marked R–15PC/5RHA (RCA treated with 15% PC and 5% RHA) resulted in the highest density compared to the concrete mix of proportionate aggregate treatments. The density increased slightly with the addition of pozzolan because the pozzolanic reaction could be initiated to form more gels that occupy the voids around the aggregate matrix, displacing the excess air voids. The test results are in agreement and consistent with findings by Junak and Sicakova [56] and Sicakova et al. [29] after modifying the surface of RCA with geopolymer slurry. Substitution of cement slurry beyond 5% formation of C–S–H could have been marginally hindered by an increase in concrete water demand resulting in reduced density.
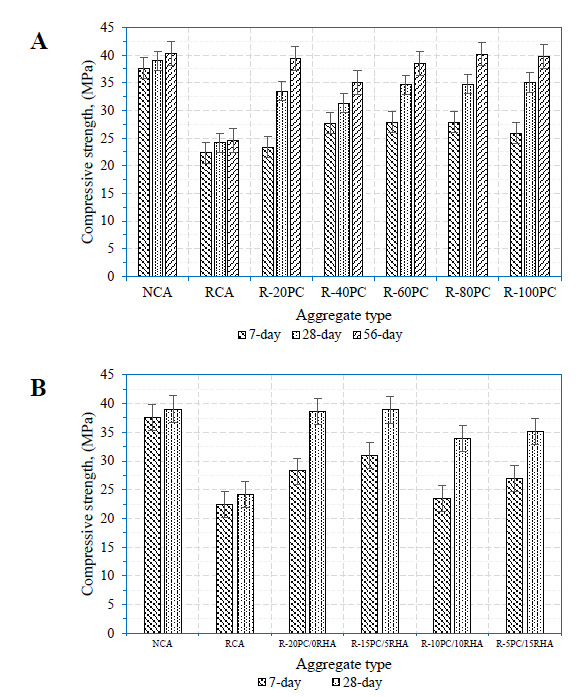
3.3. Compressive Strength of RCA Treated with Pozzolanic Slurry
Based on the 28day results shown in Fig. (9a), the use of cement slurry for the treatment of recycled concrete aggregates (RCA) resulted in improved strength compared to the untreated cases. Treatment of RCA with cement slurry, at a concentration ranging from 20 to 100%, resulted in strengths of 33.5MPa (R–20PC), 31.3MPa (R–40PC), 34.7MPa (R–60PC), 34.7MPa (R-80PC), and 35.1MPa (R–100PC). Although the results for samples with treated coarse RCA are lower than the performance of the control concrete mix (NCA) of 40.3MPa, they are better than concrete done with untreated RCA of 24.2MPa. Cement content as a treatment slurry takes an important role in RCA, contributing to the substantial improvement in the strength and quality of concrete mixtures. The cement content has an excellent effect on the strength because cement enhances the material’s strength, and the bonding force between the particles of adhered surface mortar and original natural aggregate was improved due to the increase in hydration products. This has the overall effect of forming more calcium silicate hydrates, improving the weakened bond and filling the pores within the adhered mortar on the RCA. The results of compressive strength were consistent with the findings of Shahbazpanahi, Tajara & Faraj [57], even though the concrete mix had nano-silica as an admixture, not a targeted treatment of coarse aggregates.
The previous section's results show that coating the aggregates with cement slurry leads to increased strength compared to untreated cases. However, cement production is energy-dependent and results in the emission of a large amount of carbon dioxide (CO2) in the atmosphere [58] [59]. Therefore, efforts to minimize the negative impacts of CO2 on cement (clinker) production by using partial supplementary cementitious materials (SCM) will be of positive gain [58] [60-62]. This research aims to utilize RHA at a 20% concentration of cement slurry to pretreat RCA. Fig. (9b) shows the 7 and 28 day strength development of the concrete mix with 20% concentration treatment with cement and RHA slurry. From Fig. (9b), attempts were made to replace portions of cement with rice husk ash (RHA) within the RCA treatment slurry to a considerate degree taking into account its economic and environmental sustainability. Therefore, starting from the lowest concentration of cement slurry, 20% (marked R–20PC), which gave the best strength, was replaced with a portion of RHA as 5%, 10%, and 15% to treat RCA. The samples marked R–15PC/5RHA indicated the highest strength for 7 and 28day, 30.9 and 38.92MPa, respectively, representing an increase of 25.1%. This strength was comparably similar to the 28day finding for control concrete mix (39.0MPa) shown in Fig. (9a) above, but 61% higher than untreated coarse RCA. Most of the concrete strength gain was realized at 7day and this could be due to the use of CEM I for concrete mixing resulting in high early strength gain (about 70%) of concrete. The strength development was attributed to the improvement in the structure of coarse RCA with 15% cement slurry plus 5% of RHA. The treatment resulted in the formation of more hydrated calcium silicate that seals off the cracks and voids in RCA, hence stronger aggregate within the concrete mix. This argument is supported by the findings by Krezel et al. [20] where they reported an increased strength where pozzolans react more calcium hydroxide (C–H) to produce hydrated calcium silicates (C–S–H).
3.4. Split Tensile Strength
Splitting tensile strength is experimentally investigated in the Universal Testing Machine (UTM), and the laboratory testing setup as shown in Fig. (10). In Fig. (10), it is observed that the failure crack was concentrated around the boundary of the recycled aggregate. In Fig. (11), the split tensile strength has been exposed with respect to various treatments of cement slurry concentration. Fig. (11 a, b) represent the contribution of cement slurry and cement plus RHA slurry, respectively, for the treatment of RCA.
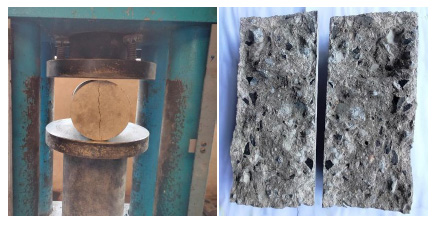
In Fig. (11a), the contribution of the cement slurry concentration was assessed to determine the change in the split resistance of the concrete. Control concrete gave the best split tensile strength at 28day. Among the concretes with coarse RCA, those treated with varying concentrations of cement slurry, sample marked R–20PC (20% concentration cement slurry) gave the highest tensile strength of 2.6MPa. Treatment led to the formation of C–S–H gels that strengthened the structure and surface of RCA. The sample with 80% pozzolan gave the lowest split strength of 2.3MPa. There was a general reduction in tensile strength with a further increase in concentration beyond 20%. The trend in the reduction in strength was similar to that of compressive strength.
Fig. (11b) illustrates the effect of RHA replacement in the proportions of cement in the RCA treatment slurry on the split tensile strength of concrete. With the introduction of RHA in the slurry concentration at 20% shown in Fig. (11b), the split resistance of concrete increases sharply with 44.5%, the highest percentage for the replacement of 5% RHA, then a slight increase in strength of 15.4% and 26.5% for the replacement of cement with RHA at 10% and 15%, respectively, in the RCA surface treatment. The strength depends on the chemical reaction of the pozzolans leading to the formation of C–S–H that strengthens the surface of RCA. For samples marked R–15PC/5RHA, there could be more C–S–H formation than untreated and other proportions of cement and RHA in the concrete mix. Fig. (11b) indicates that cement and RHA in treatment slurry for RCA result in split tensile strength values generally within 4–13% of the tested compressive strength. This was in general agreement with the study by Mindess, Young & Darwin [63], in which they found that the split tensile is between 6–13%.
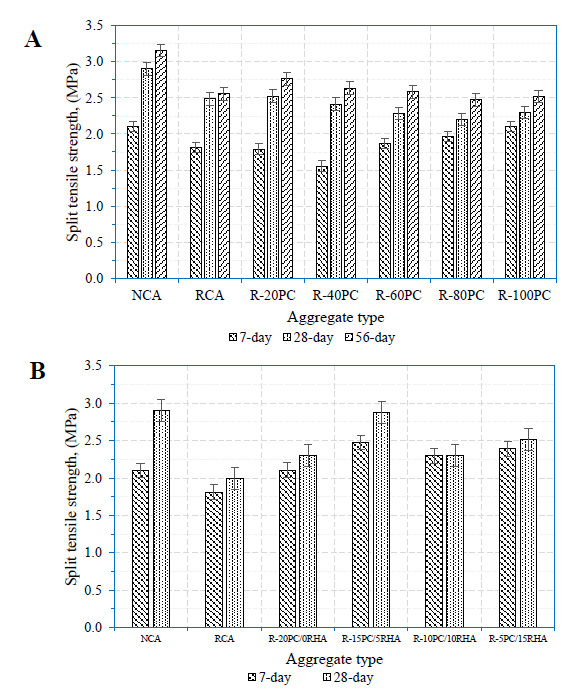
3.5. Water Absorption
Fig. (12 a and b) show the results of the rate of water absorption from all faces of concrete after 28 and 56day of curing. The results show the rate of water absorption after 30 minutes of full submergence in water was 1.95% (NCA), 3.08% (RCA), 2.01% (R–20PC), 2.10% (R–PC40), 2.15% (R–60PC), 2.62% (R–80PC), and 3.11% (R–100PC) tested after 28day; for 56day of testing the rate of water absorption was 1.41% (NCA), 2.06% (RCA), 2.19% (R–20PC), 2.12% (R–PC40), 2.11% (R–60PC), 2.03% (R–80PC), and 2.45% (R–100PC). For control, concrete samples with NCA resulted in water absorption of 1.95% and 1.41% at 28 and 56day, respectively. The surface treatment of coarse RCA with 0%, 20%, 40%, 60%, 80%, and 100% of cement slurry also slightly reduced water absorption at 28 and 56day.
Generally, the water absorptions of samples containing RCA were greater than those of the control. The test findings for concrete containing RCA, treated using cement slurry, were within the range of less than 3.5% requirement for water absorption of concrete samples by BS1881-122 [51]. The reason for the increase in water absorption for untreated RCA is mainly because of the attached cement paste and double ITZ that increases the overall capillary potential within concrete [22]. The reduction in concrete water absorption as the cement slurry concentration increases is attributed to the increased pozzolanic reaction and the hydration of C-H to produce more of C–S–H, which acts as a filler material to; (i) strengthen unhydrated pastes (ii) fill the pores and holes within RCA.
The surface treatments of coarse RCA with a 20% concentration of pozzolanic slurry (containing cement and RHA) at 28day were as shown in Fig. (13 a and b) after 30 minutes of the test. There was a general reduction in water absorption rate from 28 to 56day, a decrease of about 44.5% for the 20% pozzolanic concentration at 56day sample marked R–20PC/0RHA resulted in water absorption of 1.98%. These were immediately followed by a 5% proportion of RHA, where the sample marked R–15PC/5RHA revealed the next best water absorption rate of 2.3%. It was also observed that an increase in the proportion of RHA beyond 10% in the cement slurry increased the water absorption rate. Indeed, the sample marked R–5PC/15RHA resulted in the highest water absorption of 3.31%.
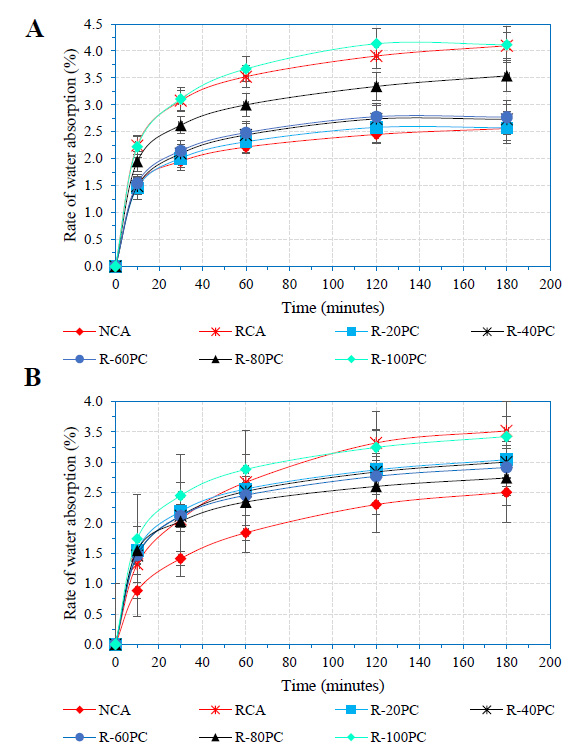
Fig. (13 a and b) show the increased hydration within the concrete matrix due to the pozzolanic treatment of RCA. The pozzolans resulted in the formations of C–S–H (binding gel) from the reaction of Si2+ (silicon ions) and CH2- (calcium hydroxide ions). Silicon ions are contributed by RHA pozzolan, while calcium hydroxide ions are contributed by unhydrated mortar, RCA, and cement slurry hydration. The binding gel improves the matrix of paste around the aggregate, reducing the fractured cracks, thereby reducing the pore spaces that are likely to accumulate water molecules and dangerous chemicals within concrete. Therefore, this explains the reduced water absorption rate, as the C–S–H (gel) fills the pore spaces around the recycled concrete aggregate in the concrete mix.
The pores and holes within the concrete and around the aggregate are the greatest contributors to high water absorption in concrete. As the proportion of RHA in aggregates treatment cement slurry increases, more unhydrated cement pastes are formed. RHA draws more water, limiting treatment water for the hydration process needed to form hydrated calcium silicate gels around RCA, hence the adhered mortar becomes more porous. The increased concentration of pozzolan also resulted in underutilization of reacting elements, which resulted in a dormant hydration process, thereby resulting in the efflorescence of the chemicals and hence the creation of paths that form weak joints within concrete.
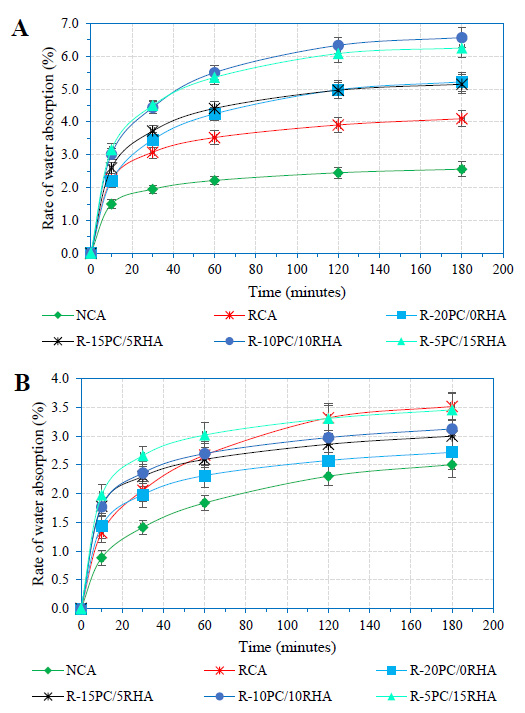
3.6. Water Sorptivity
As demonstrated in Section 2, water sorptivity measures the penetration rate of water within the concrete matrix from the surface of the sample according to ASTM C1585/C1585M [52]. Concrete with a lower sorptivity value has a higher resistance to the effects of water absorption and this function of pore structure of concrete matrix [26]. Figs. (14 and 15) represent the results of sorptivity for 28 and 56day of testing, respectively. At 28 day of testing (Fig. 14), initial sorptivity coefficients ranged from 0.0182 to 0.0349mm/√sec. The sample marked RCA showed the highest sorptivity, while NCA gave the lowest value. The secondary sorptivity coefficients were found to range between 7.44×10−4 to 40.88×10−4mm/√sec. The sample marked R–20PC resulted in the lowest initial sorptivity coefficient, and again RCA showed the highest coefficient at 28day of testing.
From Fig. (15a), initial sorptivity coefficients at 56day of testing were found to range from 0.0156–0.0422mm/√sec. The sample marked R–20PC resulted in the lowest initial sorptivity coefficient, and RCA showed the highest coefficient. However, the secondary sorptivity coefficients were found to range between 4.49×10−4 to 17.67×10−4mm/√sec., the NCA-labeled sample gave the lowest initial sorptivity coefficient, while R–20PC showed the highest coefficient at 56 day of testing (Fig. 15b).
From the results, it was concluded that concrete samples with coarse RCA pretreated with cement slurry at 20% concentration were regarded as the best in terms of cement used in treatment. A better sorptivity performance was achieved for a 20% concentration of cement slurry, possibly due to the effect of the presence of pozzolanic reaction during the treatment period; (i) the creation of a more sinuous and discontinuous pore network in the concrete matrix due to the filler effect, consequently reducing the rate of water absorption; and (ii) the consumption of calcium hydroxide and the production of more calcium silicate hydrate gel (C-S-H) due to the pozzolanic reaction, making the microstructure of concrete denser, hence having a significant impact on the transport of water in concrete.
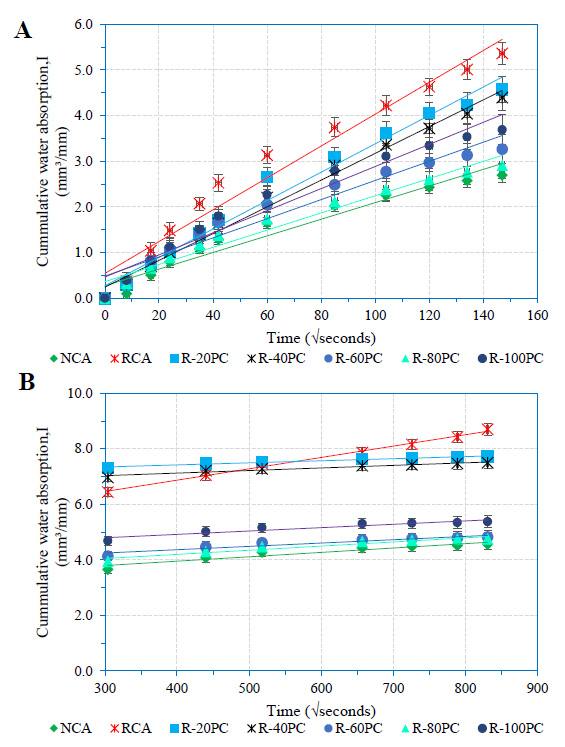
Furthermore, with the replacement proportions of cement with RHA in 20% concentration of pozzolanic treatment, for coarse RCA, the results of sorptivity tests are shown in Fig. (16). From Fig. (16a), it was observed that at 28day, the initial sorptivity coefficients were 0.0182mm/√sec. (NCA), 0.0349mm/√sec. (RCA), 0.0311mm/√sec. (R–20PC/0RHA), 0.0330mm/√sec. (R–15PC/5RHA), 0.0392mm/√sec. (R–10PC/10RHA) and 0.0348mm/√sec. (R–5PC/15RHA). Sample R–20PC/0RHA resulted in the lowest sorptivity after concrete with natural coarse aggregates (NCA), while R–10PC/10RHA gave the highest value of sorptivity. For long-term measurements of the rate of surface water absorption (secondary sorptivity coefficient), the findings were 15.84×10−4mm/√sec. (NCA), 40.88×10−4mm/√sec. (RCA), 7.44×10−4mm/√sec. (R–20PC/0RHA), 7.95×10−4mm/√sec. (R–15PC/5RHA), 7.69×10−4mm/√sec. (R–10PC/10RHA) and 7.83×10−4mm/√sec. (R–5PC/15RHA) (from Fig. 16b). There was an insignificant difference in change secondary sorptivity coefficient for samples with pretreated aggregates. The samples containing RCA pretreated with combined cement and rice husk ash slurry performed better than those composed of natural coarse aggregates (NCA) and untreated RCA.
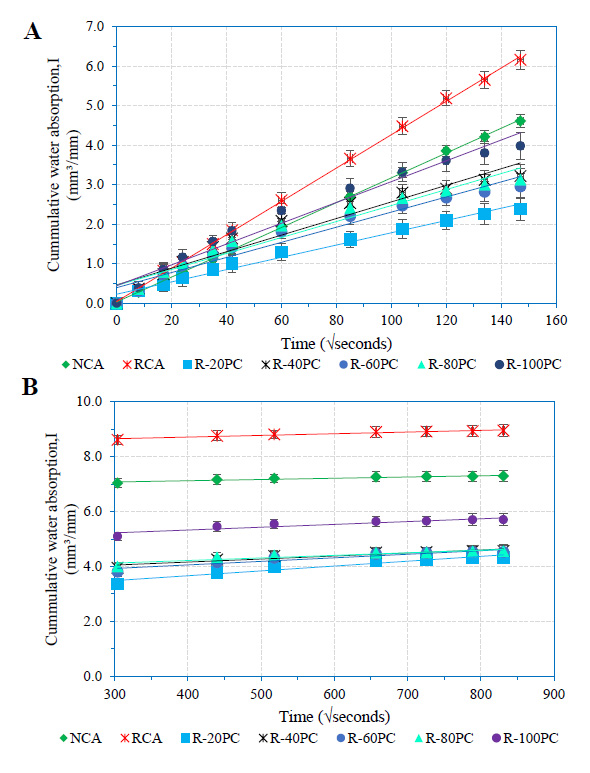
Based on the initial sorptivity coefficient, the results indicate that as the proportion of RHA increased beyond 5%, the treatment of RCA results in the formation of more unhydrated paste around aggregates. A high concentration of lime calcium hydroxide is an efflorescence material that escapes from the concrete surface leaving behind capillary voids and ducts. RHA is a hydrophilic material that absorbs more water for hydration around the aggregate, resulting in incomplete hydration and formation of C–H, which is again an efflorescence material that will escape to the concrete surface. It also facilitates the formation of soluble substances calcium carbonate by reaction with CO2 along the route. Reduced sorptivity index of sample R–15PC/5RHA of 15% replacement of cement with 5% RHA at 20% concentration of RCA surface treatment results in adequate consumption of crucial elements reducing the interconnection pore networks within the concrete resulting in dense concrete.
These findings were consistent with the study by Onikeku et al. [64], where they observed that pozzolanic treatment reduced sorptivity by about 50% when pozzolan was used in concrete. The reduction in sorptivity was attributed to an increase in Si2+ that reacted C–H ions to form a gel that occupies pores in concrete. In addition, there was a general reduction in the sorptivity coefficient at 56day compared to values of 28day. The reduction in sorptivity resulting from pozzolanic treatment and curing age was similar to the findings of Olorunsogo & Padayachee [24] and was also supported by the findings of Wu [15].
The study by Olorunsogo & Padayachee [24] on the effect of bamboo leaf ash (BLA) on sorptivity found that there was a linear reduction in sorptivity of 50.3% from 0.167 to 0.083mm/√hr. when the percentage replacement of the BLA mix increased from 0 to 20% replacement. Furthermore, treatment of RCA with RHA plus cement slurry generally resulted in concrete with less than 6mm/√hr. based on the studies, indicating durable concrete.
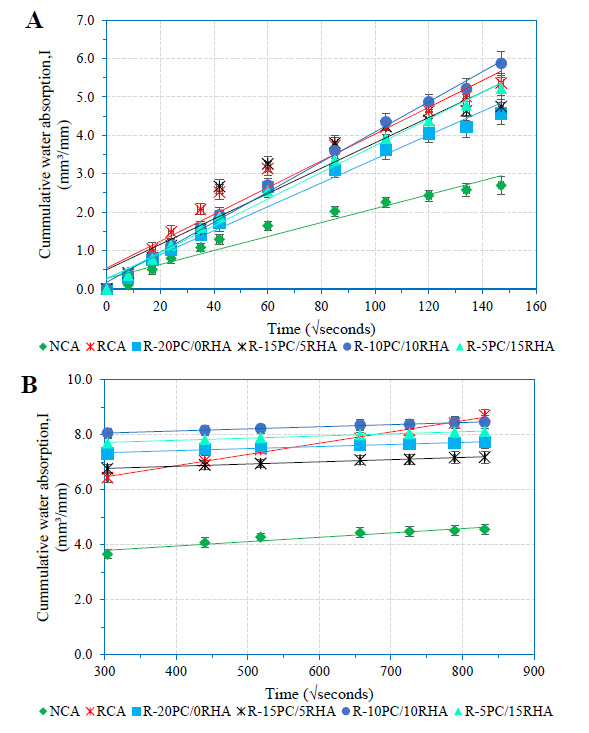
CONCLUSION
This study sought to determine the effect of treated RCA with PC and RHA pozzolanic slurry on the mechanical and water absorption of the resulting concrete. It is possible to make sustainable concrete with the target treatment of RCA with cement plus RHA pozzolanic slurry. The findings of this research demonstrate that RCA can be modified with pozzolanic materials. This research clearly illustrates that it is possible to improve the surface structure of RCA for use as structural concrete. The following conclusions are drawn based on the findings of this study;
- Based on the results and findings, it can be resolved that the application of pozzolanic treatments may have an influence on the workability of concrete. Samples marked R–20PC gave the least water demand with a slump value of 38.1mm, which is within the target slump of 30–60mm. While with the replacement of 5% RHA in cement slurry for RCA treatment, the water demand for the concrete mix was 13.4%, achieving a slump value of 43mm.
- Compressive strength test findings revealed that when cement slurry alone was used to treat coarse RCA surface at a 20% concentration, it resulted in a strength of 33.5MPa, which is 16.9% lower than that of natural coarse aggregates (NCA) and better than untreated RCA by 38%. For samples marked R-15PC/5RHA, the highest strength of 38.9MPa was observed, which is comparable to the control sample with NCA but higher than untreated coarse RCA with 61%.
- The use of cement slurry treatment of coarse RCA surface gave a 27% improvement in split tensile strength with a 20% concentration of treatment (the lowest concentration of cement in treatment slurry). However, surface treatment with 15% PC and 5% RHA resulted in the highest increase in split tensile strength by 44.5% compared to untreated coarse RCA.
- Water absorption was significantly reduced by treating the aggregate with pozzolans. On 28day of testing concrete samples where coarse RCA surfaces were treated with 20% concentration, cement slurry resulted in water absorption of 2.01%, slightly higher than the referenced concrete (NCA) of 1.95%. The sample marked R–15PC/5RHA resulted in water absorption of 2.3%, which is lower by 25.1% compared to the untreated coarse RCA
- Water sorptivity for concrete at 20% concentration of cement slurry treatment, resulting in an initial (Si) and secondary sorptivity coefficients (Ss) of 0.0311mm/√sec. and 7.44×10−4mm/√sec., respectively, at 28day and 0.0156mm/√sec. and 17.67×10−4mm/√sec. accordingly, at 56day of testing. With the introduction of rice husk ash for the sample marked R–15PC/5RHA, the initial and secondary sorptivity coefficient of 0.0330mm/√sec. and 7.95×10−4mm/√sec, respectively, at 28day of testing, which is comparatively lower than untreated coarse RCA (0.0349mm/√sec. and 40.88×10−4mm/√sec.).
Based on the conclusion above, practitioners in the construction industry should consider the utilization of these aggregates on a wide scale to produce better aggregates.
CONSENT FOR PUBLICATION
Not applicable.
AVAILABILITY OF DATA AND MATERIALS
The data supporting the findings for this paper are available within the paper.
FUNDING
None.
CONFLICT OF INTEREST
The authors declare no conflict of interest, financial or otherwise.
ACKNOWLEDGEMENTS
Declared none.