All published articles of this journal are available on ScienceDirect.
A Sustainable Revolution in Sisal Fiber with Enhanced Mechanical Properties of Concrete
Abstract
Introduction
This study provides a comprehensive comparative analysis of conventional concrete (CC) and Sisal Fiber Concrete (SFC) and incorporates sisal fiber into a concrete blend for the M25 grade concrete mix.
Methods
In order to evaluate the efficacy of both variations of concrete, mechanical and durability parameters were examined. As compared to CC, the results indicated that SFC had a substantially greater compressive strength. The average compressive strength of SFC at the 28-day was 29.47 N/mm2, which signified a significant incremental percentage growth of 9.58% in comparison to CC. In the same way, SFC exhibited an exceptional flexural strength, as evidenced by its mean value of 7.81 N/mm2, which represented a significant 34.42% improvement in comparison to CC. The Bayesian factor independent sample test yielded a t-test value of 12.495 for compressive strength, accompanied by a p-value below 0.001. These results suggest that the observed difference was statistically significant. Conversely, a t-test value of 19.380 and a p-value below 0.001 were produced by the Bayesian factor independent sample test for flexural strength, both of which further supported the existence of a significant difference. The mean disparity in compressive strength between CC and SFC was 5.1522 N/mm2, with a 95% confidence interval encompassing values between 4.2856 and 6.0188 N/mm2. In a similar manner, the mean discrepancy in flexural strength was 2.0000 N/mm2, accompanied by a 95% confidence interval that varied between 1.7831 and 2.2169 N/mm2.
Results
The obtained results provide further evidence that SFC is stronger than CC in both compressive and flexural strength, which is consistent with the results obtained from the frequentist statistical analysis.
Conclusion
With its eco-friendly properties, sisal fiber concrete could indeed play a significant role in the future of sustainable construction.
1. INTRODUCTION
Concrete has been the primary building material for centuries, and recent advancements have led to modifications aimed at improving its performance, strength, and sustainability. One such improvement is the integration of natural fibers like sisal fiber into the concrete mix, resulting in sisal fiber concrete [1]. This innovative material deals with several benefits, including enhanced mechanical properties, reduced environmental impact, and better sustainability. Conventional concrete is still widely used today due to its affordability and ease of use. It finds extensive use in the construction of residential, commercial, and infrastructure projects, including the structural foundation of bridges, dams, highways, and the development of modern architectural designs. Its strength, durability, and versatility make it an indispensable material in the construction industry [2]. In comparison to conventional concrete, sisal fiber concrete has unique constituent materials and production processes. It also boasts different physical properties and mechanical strength [3]. Applications of sisal fiber concrete range from structural to non-structural use cases. While it offers many advantages over traditional concrete, such as increased durability and decreased carbon footprint, there are also some disadvantages, such as higher production costs. As the construction industry becomes increasingly eco-conscious, sustainable construction materials like sisal fiber concrete are gaining popularity. It is worth exploring the future prospects of this material in the industry as it holds immense potential in terms of reducing greenhouse gas emissions and promoting sustainable practices [4].
The sisal fiber research showed around 816 topics in Google Scholar during the examination of the past five years. Hence, this research will be helpful in giving guidance to construction engineers as newer or advanced materials that reduce the cracks in concrete. Sisal fiber, derived from the Agave sisalana plant, has been utilized for centuries for ropes and twine production [5, 6]. Such applications are deemed suitable due to the fiber's strength, durability, and resistance to deterioration. Specifically, the 3% polypropylene fiber concrete mix exhibited the highest average compressive strength at both 28 and 90 days, while the 2% polypropylene fiber mix showed the highest split-tensile strength. Flexural strength results followed a similar trend. Results show that 3% HHF addition leads to notable improvements in concrete strength properties, albeit not as significant as with polypropylene fibers [7]. Over time, sisal fiber has been utilized in various other industries, including the manufacturing of carpets, geotextiles, paper, and even automotive components. More recently, sisal fiber has been incorporated into the construction industry as reinforcement for building materials. This shift towards sisal fiber reinforcement is attributed to the eco-friendly and biodegradable properties of the fiber, rendering it an attractive alternative to conventional reinforcement materials, such as steel [8]. Sisal, a renewable resource, can be grown quickly and sustainably. The use of sisal fibers in concrete reduces the reliance on non-renewable materials, such as steel or synthetic fibers, rendering it an eco-friendly option for construction projects. Many advantages are offered by sisal fiber concrete over traditional concrete and other building materials. The fiber mechanism of concrete is shown in Fig. (1). Its exceptional durability, strength, and resistance to environmental factors make it an ideal choice for a wide range of construction applications [9].
Modern construction material, sisal fiber concrete, also known as fiber-reinforced concrete, is composed of sisal and other natural fibers that are incorporated into the mixture design [10]. Conventional concrete, which is the prevailing variant utilized in the construction sector, primarily consists of coarse aggregate, fine aggregate, Portland cement, and water. Sisal fiber, renowned for its remarkable attributes, including resilience and springiness, has been implemented across diverse sectors for millennia. It is derived from the foliage of the agave plant and is distributed across multiple nations globally [11, 12]. Since its introduction in the 1960s, sisal fiber concrete has grown in popularity due to its numerous advantages. An important benefit of sisal fiber concrete in comparison to conventional concrete is its improved tensile strength and resistance to impacts. It also exhibits enhanced resistance to cracks and prolonged durability [13]. It is an ideal material for construction projects requiring high levels of strength and stability due to these characteristics. Sisal fiber concrete presents a multitude of benefits in comparison to conventional concrete on account of its distinctive characteristics, which augment its overall efficacy. Sisal fiber concrete is reinforced with natural fibers, including sisal fiber, which enhances the material's tensile strength and fracture resistance [14]. Recycled aggregate may be incorporated into sisal fiber concrete in certain instances, thereby further reducing the environmental impact of the material and enhancing its sustainability [15]. The compressive strength of sisal fiber concrete is significantly influenced by the cement proportion, whereas the incorporation of sisal fiber into concrete yields enhanced mechanical characteristics [16].

2. METHODS
The production of 2% of sisal fiber concrete involves proportioning materials (cement, fine aggregate, water, and sisal fiber) based on the mix design, followed by thorough mixing for proper fiber dispersion. The mix is then cast, compacted using manual or mechanical methods, and undergoes an initial curing period. Subsequently, mechanical performance tests assess compressive, tensile, and flexural strengths to ensure material quality. The mix proportions may need adjustment to accommodate the presence of fibers, and trial mixes should be conducted to ensure the desired properties are achieved. The M25 grade concrete mix is used to find the experimental test, and this ratio can be expressed as 1:1:2 for cement, sand, and aggregate. Additionally, the water-cement ratio is taken as 0.45. Moreover, conventional concrete follows a similar process, determining mix design, blending materials, casting into molds, and undergoing curing. Sisal fiber concrete is a durable material that is well-suited for use in harsh conditions.
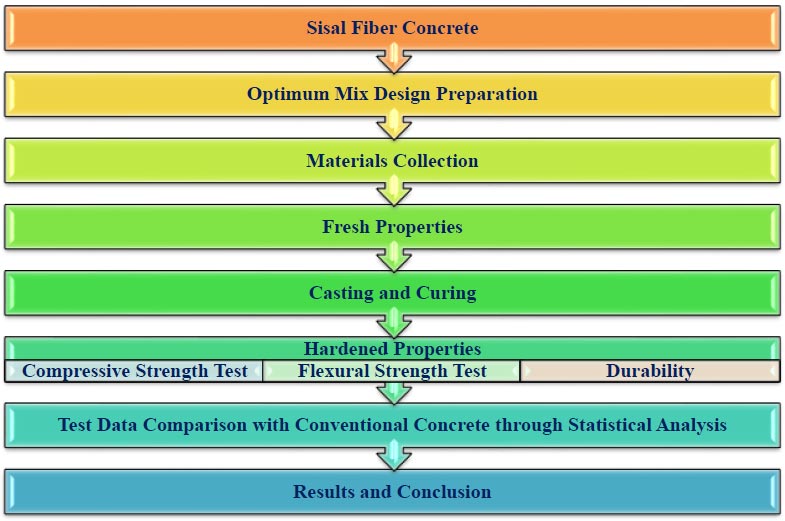
S.No. | Fibre Type | Result |
---|---|---|
1 | Fiber length (mm) | 25 |
2 | Fiber diameter (mm) | 0.25 |
3 | Aspect ratio | 100 |
4 | Elongation (%) | 268 |
5 | Tensile strength (MPa) | 14.8 |
6 | Modulus of elasticity (GPa) | 42.5 |
7 | Density (g/cm3) | 1.70 |
The reinforcement provided in the form of fibers enhances the strength of the concrete, resulting in a material with comparable properties to conventional concrete. Table 1 shows the properties of Sisal Fiber. This contributes to its overall mechanical performance, making it an ideal choice for projects that require high levels of strength and durability. Moreover, 2% of sisal fiber concrete has been found to have excellent resistance to environmental factors, such as moisture, heat, and chemicals. This makes it a popular choice for applications in marine environments or areas prone to extreme weather conditions.
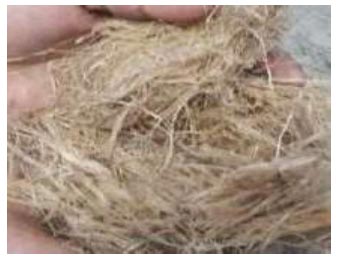
The alkaline treatment involves soaking the fibers in an alkaline solution, typically sodium hydroxide (NaOH) or potassium hydroxide (KOH) [17]. Here is a general guideline for the chemical treatment: Materials needed for the alkaline treatment of sisal fibers include sisal fibers, 10% NaOH solution for 24 hours - an alkaline solution (sodium hydroxide or potassium hydroxide), and protective equipment (gloves, goggles, etc.). Dissolve sodium hydroxide or potassium hydroxide in water to create an alkaline solution. The concentration and temperature of the solution can vary based on the desired treatment level. Immerse the sisal fibers in the alkaline solution for a specific duration. Fig. (2) shows the sisal fiber, and Fig. (3) shows the pre-treating of sisal fiber with alkaline solution for 24 hours. The soaking time can range from a few minutes to several hours, depending on factors, such as fiber type and desired properties. After soaking, thoroughly rinse the fibers with water to eliminate any residual alkali [18]. Fig. (4) shows the slump test of concrete, and Fig. (5) shows the mixing of concrete. Neutralize the fibers with an acid solution (e.g., acetic acid) to ensure complete removal of alkaline residues. Allow the treated fibers to air dry. Fig. (6) shows the casting of a concrete cube, and Fig. (7) shows the casting of a flexural beam.
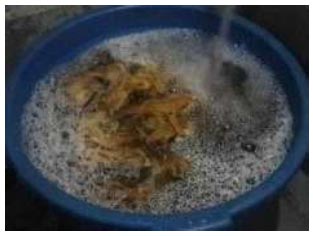
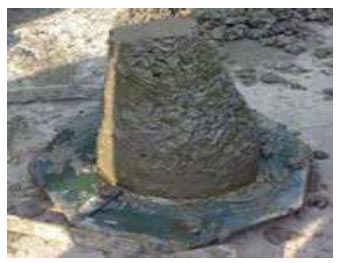
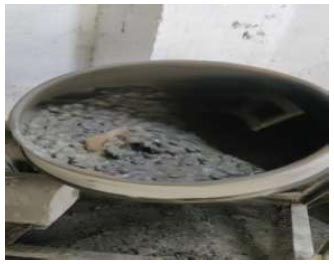
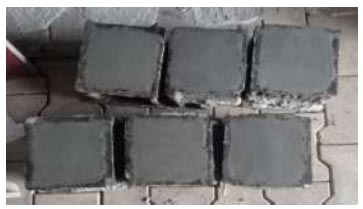
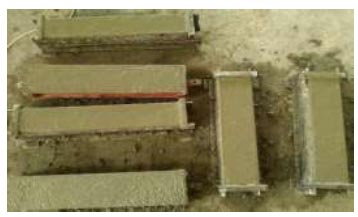
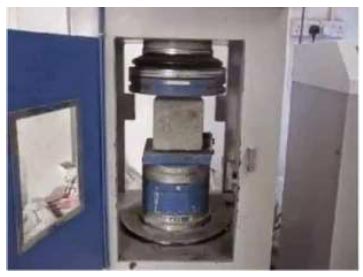
In this study, two groups of concrete were investigated: Group 1 consisted of conventional concrete, while Group 2 involved sisal fiber-reinforced concrete. The evaluation of the concrete in both groups focused on several key parameters, including compressive strength of cubes, flexural beam tests, and a durability test. A total of 18 samples were prepared for compressive and flexural strength tests and 8 cubes for the durability test for conventional and modified concrete after 28 days of curing. Figs. (8 and 9) show the compressive strength and flexural strength testing arrangements. This involved preparing standard cube specimens from each concrete mix, subjecting them to the prescribed curing conditions, and subsequently testing their compressive strength using a hydraulic press. The compressive strength, denoted by fc′, was calculated using the formula in Eq. (1):
![]() |
(1) |
where P is the maximum applied load, and A is the cross-sectional area of the cube.
The flexural strength of the concrete in both groups was assessed through a flexural beam test. Standard beam specimens were prepared, cured, and tested using a three-point bending setup. The flexural strength (flex) was determined using the formula in Eq. (2):
![]() |
(2) |
where P is the maximum load, L is the span length, b is the width, and d is the depth of the beam.
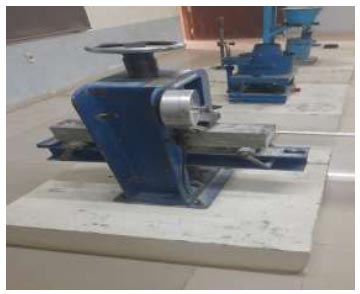
Durability was evaluated through a specific test designed to assess the resistance of the concrete to harsh environmental conditions. Sodium Hydroxide (NaOH) is often chosen because it is aggressive and can cause degradation in concrete, making it a suitable choice for evaluating the durability of concrete structures in acidic environments [19, 20]. For this study, a 28-days cured cube from each group was immersed in an acid solution within the range of 5 to 10%. The mass loss and visual inspection after exposure to acid provided insights into the durability performance of both types of concrete. The curing period for all specimens was standardized at 28 days, allowing the concrete to attain its optimum strength and durability characteristics. Fig. (10) shows the concrete cube after the durability test is done.
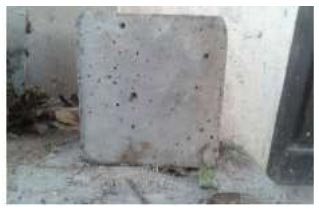
3. RESULTS
Adding sisal fiber to concrete can indeed improve its tensile strength and help prevent cracking when subjected to loads. Sisal fibers are natural fibers derived from the agave plant, and they are known for their strength and durability. When these fibers are mixed into concrete, they act as reinforcement, providing additional support and reducing the likelihood of cracks forming under stress. The average compressive strength for the 18 cubes of conventional concrete was 21.17 N/mm2, and sisal fiber concrete was 30.82 N/mm2. The average flexural strength for the 18 cubes of conventional concrete was 5.81 N/mm2, and sisal fiber concrete was 7.81 N/mm2. The average durability of concrete by compression test for the 18 cubes of conventional concrete was 19.23 N/mm2, and sisal fiber concrete was 25.21 N/mm2. Table 1 shows the compressive strength of M25 Grade for 28 Days: Comparison of both conventional concrete and sisal fiber. Table 2 shows the flexural strength of M25 Grade for 28 Days: Comparison of both conventional concrete and sisal fiber. Table 3 depicts the durability test of M25 Grade for 28 Days: Comparison of both conventional concrete and sisal fiber. The mean durability for sisal fiber concrete after acid immersion is approximately 8.723 g, and for conventional concrete, it is approximately 8.134 g. Tables 4 and 5 show the maximum change in percentage and compressive strength of mixes after H2SO4. Table 5 shows the mean strength of durability test results. Table 6 shows the Bayesian independent sample test for compressive strength: Group Statistics Report – Total number of sample: 18, Mean (27.17, 30.82), Standard Deviation (1.017, 1.422), and Standard Error Mean (0.239, 0.335). Table 7 shows the Bayesian factor independent sample test (Method = Rouder)a: The observations were as follows: The t-test value: 12.495, Degree of Freedom (df): 34, sig. (2-tailed) value less than 0.05, i.e., p<0.05; hence, there was no significant difference statistically. Table 8 shows the posterior distribution characterization for independent sample meana. Table 9 shows the Bayesian independent sample test for flexural strength: Group Statistics Report – Total number of sample: 18, Mean (5.81, 7.81), Standard Deviation (0.239, 0.366), and Standard Error Mean (0.056, 0.086). Table 10 shows the Bayesian factor independent sample test (Method = Rouder)a: The observations were as follows: The t-test value: 19.380, Degree of Freedom (df): 34, sig. (2-tailed) value less than 0.05, i.e., p<0.05; hence, there was no significant difference statistically.
Compressive Strength (N/mm2) For M25 Grade | |||
---|---|---|---|
S.No. | Conventional Concrete (CC) | Sisal Fiber | |
7 Days Strength | 28 Days Strength | ||
1. | 24.69 | 27.82 | 28.78 |
2. | 23.73 | 26.89 | 29.47 |
3. | 23.87 | 26.43 | 29.20 |
4. | 23.96 | 27.42 | 29.57 |
5. | 24.98 | 26.44 | 30.78 |
6. | 24.09 | 25.25 | 31.99 |
7. | 22.98 | 26.67 | 30.20 |
8. | 21.87 | 28.73 | 29.41 |
9. | 22.67 | 31.54 | 30.62 |
10. | 24.44 | 24.90 | 28.43 |
11. | 22.84 | 28.70 | 31.04 |
12. | 22.09 | 28.97 | 31.25 |
13. | 25.47 | 30.45 | 32.64 |
14. | 22.22 | 30.00 | 32.67 |
15. | 23.96 | 28.35 | 31.88 |
16. | 24.18 | 29.89 | 32.09 |
17. | 24.27 | 28.94 | 32.30 |
18. | 23.78 | 26.04 | 32.51 |
Flexural Strength (N/mm2) For M25 Grade | ||
---|---|---|
Sl.No. | Conventional Concrete (CC) | Sisal Fiber Concrete (SFC) |
1. | 5.67 | 7.35 |
2. | 5.68 | 7.84 |
3. | 4.84 | 8.24 |
4. | 5.68 | 7.31 |
5. | 5.45 | 8.00 |
6. | 5.50 | 7.44 |
7. | 4.98 | 8.09 |
8. | 5.70 | 7.76 |
9. | 4.20 | 7.78 |
10. | 5.78 | 7.81 |
11. | 5.53 | 7.84 |
12. | 5.86 | 7.59 |
13. | 5.59 | 8.74 |
14. | 5.79 | 7.16 |
15. | 5.87 | 7.87 |
16. | 4.14 | 7.90 |
17. | 4.10 | 7.92 |
18. | 4.23 | 7.95 |
Durability of Concrete Cube | |||
---|---|---|---|
Sample Name | Weight Before Exposure (Kg) | Weight After Exposure (Kg) | % Change |
CC1 | 8.45 | 8.26 | 2.25 |
CC2 | 8.42 | 8.25 | 2.02 |
CC3 | 8.50 | 8.32 | 2.12 |
CC4 | 8.48 | 8.29 | 2.31 |
CC5 | 8.43 | 8.22 | 2.49 |
CC6 | 8.47 | 8.28 | 2.24 |
CC7 | 8.41 | 8.20 | 2.50 |
CC8 | 8.44 | 8.25 | 2.17 |
SFC1 | 8.75 | 8.72 | 0.54 |
SFC2 | 8.69 | 8.65 | 0.46 |
SFC3 | 8.78 | 8.70 | 0.91 |
SFC4 | 8.80 | 8.68 | 1.36 |
SFC5 | 8.72 | 8.66 | 0.69 |
SFC6 | 8.71 | 8.64 | 0.80 |
SFC7 | 8.73 | 8.67 | 0.68 |
SFC8 | 8.77 | 8.70 | 0.80 |
S.No | Mix Name | Max Value for Before and After Exposure (Kg) | Max. % Change | Mean Strength After Exposure (N/mm2) | % Change | |
---|---|---|---|---|---|---|
1 | CC | 8.41 | 8.20 | 2.50 | 19.23 | 6.95 |
2 | Sisal fiber | 8.80 | 8.68 | 1.36 | 25.21 | 5.31 |
Table 11 shows the posterior distribution characterization for independent sample meana. Table 12 shows the Bayesian independent sample test for durability test: Group Statistics Report – Total Number of Sample: 18, Mean (19.23, 25.21), Standard Deviation (1.776, 1.543) and Standard Error Mean (0.418, 0.363). Table 13 shows the Bayesian factor independent sample test (Method = Rouder)a: The observations were as follows: The t-test value: 10.784, Degree of Freedom (df): 34, sig. (2-tailed) value less than 0.05, i.e., p<0.05; hence, there was no significant difference statistically. Table 14 shows the posterior distribution characterization for independent sample meana. Figs. (11a,b,c) show the simple bar chart mean of compressive strength, flexure strength, and durability test. Figs. (13-15) illustrate the Bayesian statistics of the log-likelihood function, prior distribution, and posterior distribution: Mean of compressive strength in N/mm2, flexural strength in N/mm2, and durability test.
Group Statistics | |||||
---|---|---|---|---|---|
Variables | Groups | N | Mean | Std. Deviation | Std. Error Mean |
Compressive Strength, N/mm2 | Conventional Concrete | 18 | 27.1717 | 1.01789 | 0.23992 |
Sisal fiber Concrete | 18 | 30.8239 | 1.42286 | 0.33537 |
Variables | Mean Difference | Pooled Std. Error Difference | Bayes Factorb | t | df | Sig.(2-tailed) |
---|---|---|---|---|---|---|
Compressive Strength, N/mm2 | 5.1522 | 0.41235 | .000 | 12.495 | 34 | <.001 |
Compressive Strength, N/mm2 | Posterior | 95% Credible Interval | |||
---|---|---|---|---|---|
Mode | Mean | Variance | Lower Bound | Upper Bound | |
- | 5.1522 | 5.1522 | 0.193 | 4.2856 | 6.0188 |
Group Statistics | |||||
---|---|---|---|---|---|
Variables | Groups | N | Mean | Std. Deviation | Std. Error Mean |
Flexural Strength, N/mm2 | Conventional Concrete | 18 | 5.8106 | 0.23969 | 0.05650 |
Sisal fiber Concrete | 18 | 7.8106 | 0.36640 | 0.08636 |
Variables | Mean Difference | Pooled Std. Error Difference | Bayes Factorb | t | df | Sig.(2-tailed) |
---|---|---|---|---|---|---|
Flexural Strength, N/mm2 | 2.0000 | 0.10320 | 0.000 | 19.380 | 34 | <0.001 |
Variables | Posterior | 95% Credible Interval | |||
---|---|---|---|---|---|
Mode | Mean | Variance | Lower Bound | Upper Bound | |
Flexural Strength, N/mm2 | 2.0000 | 2.0000 | 0.012 | 1.7831 | 2.2169 |
Group Statistics | |||||
---|---|---|---|---|---|
Variables | Groups | N | Mean | Std. Deviation | Std. Error Mean |
Durability Test | Conventional Concrete | 18 | 19.2300 | 1.77652 | 0.41873 |
Sisal fiber Concrete | 18 | 25.2117 | 1.54342 | 0.36379 |
Bayes Factor Independent Sample Test (Method = Rouder)a | ||||||
---|---|---|---|---|---|---|
Variables | Mean Difference | Pooled Std. Error Difference | Bayes Factorb | t | df | Sig.(2-tailed) |
Durability Test | 5.9817 | 0.55469 | 0.000 | 10.784 | 34 | <.001 |
a. Assumes unequal variance between groups.
b. Bayes factor: Null versus alternative hypothesis.
Variables | Posterior | 95% Credible Interval | |||
---|---|---|---|---|---|
Mode | Mean | Variance | Lower Bound | Upper Bound | |
Durability Test | 5.9817 | 5.9817 | .349 | 4.8165 | 7.1469 |
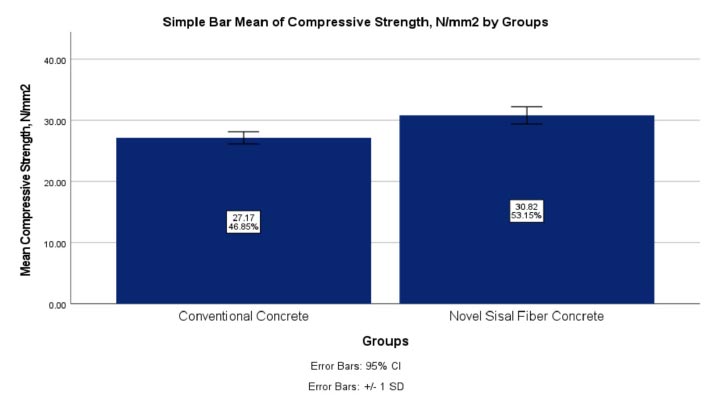
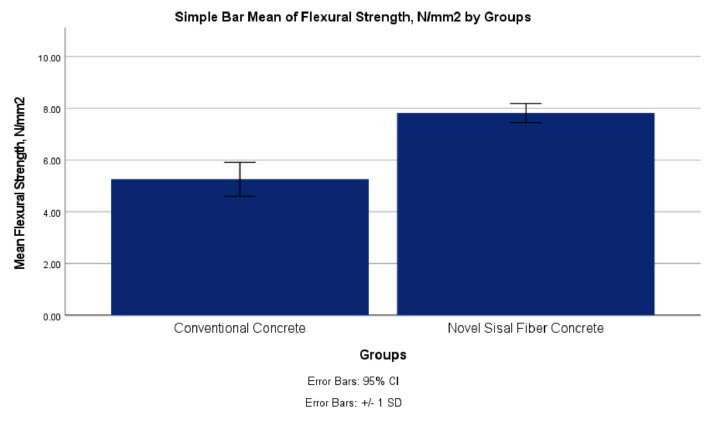
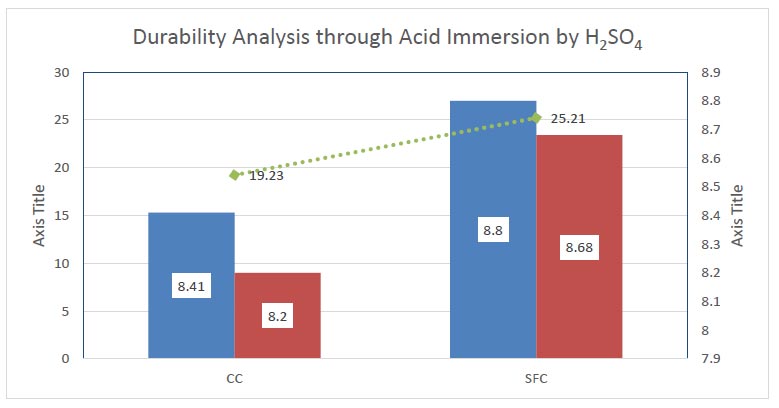
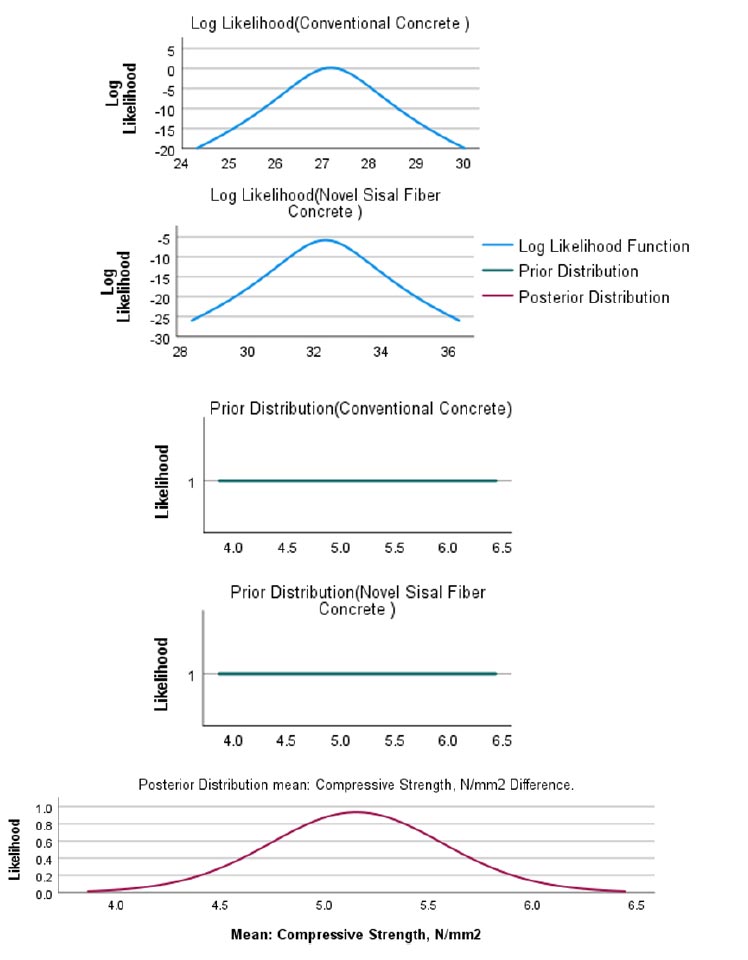
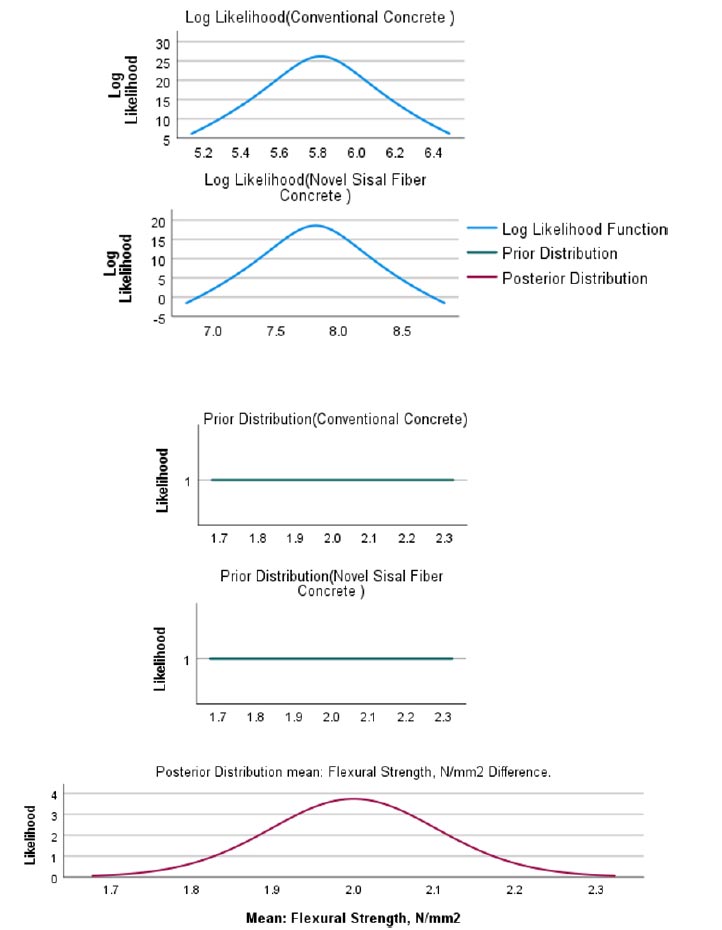
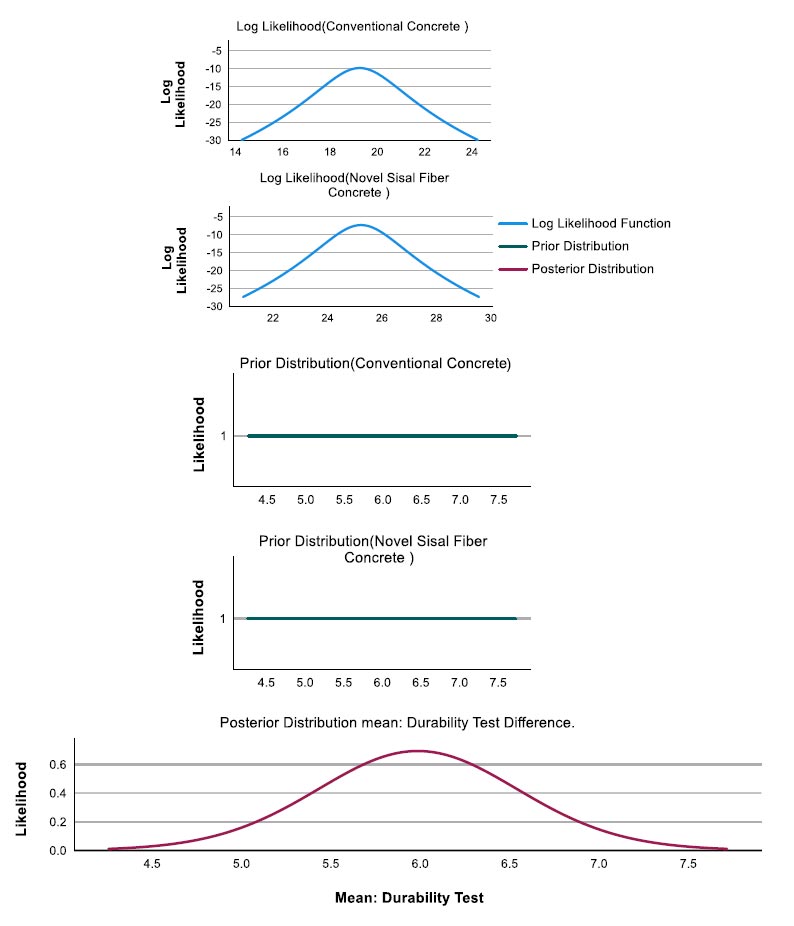
4. DISCUSSION
The results of this study regarding the benefits of sisal fiber concrete in sustainable building practices are consistent with previous research by Ferraz et al. [21], which also emphasized the eco-friendly properties of sisal fiber concrete. This consistency reinforces the growing body of evidence supporting the environmental advantages of using natural fiber-reinforced concrete compared to conventional concrete. The findings of reduced environmental impact and enhanced sustainability associated with sisal fiber concrete align with the increasing emphasis on environmentally conscious building materials, as noted by de Lima et al. [22]. This alignment underscores the relevance of sisal fiber concrete in addressing sustainability challenges in the construction industry and supports the broader trend towards eco-friendly construction practices.
Further, the results highlighting the mechanical properties of sisal fiber concrete, such as strength and durability, reinforce previous research by Gu et al. [23]. This consistency underscores the long-term structural benefits offered by sisal fiber concrete and establishes a recurring pattern of its superior mechanical performance compared to conventional concrete. The identification of drawbacks associated with sisal fiber concrete, such as reduced tensile strength and limitations in flexural strength, contributes to a nuanced understanding of the performance characteristics of the material. This recognition of potential limitations adds depth to existing literature and provides valuable insights for practitioners considering the adoption of sisal fiber concrete in construction projects [24, 25].
Additionally, the discussion on the cost-effectiveness of sisal fiber concrete in supporting sustainable building practices echoes the findings of Joseph et al. [2] and Palanisamy et al. [26], who also highlighted the economic advantages of the material. This consistency suggests a robust pattern of sisal fiber concrete offering cost-effective solutions for sustainable construction, further supporting its viability as a mainstream building material. The authors' exploration of potential improvements in sisal fiber concrete production, such as optimizing mix designs and enhancing manufacturing processes, aligns with ongoing research efforts documented by Natarajan et al. [27]. This emphasis on innovation underscores the dynamic nature of the field and signals a collective effort towards advancing the performance and sustainability of sisal fiber concrete.
CONCLUSION
In conclusion, comparing sisal fiber concrete to conventional concrete reveals that sisal fiber concrete offers several advantages in terms of sustainability and environmental impact. With its natural fibers, sisal fiber concrete provides better durability and strength, making it a suitable choice for sustainable construction. The sisal fiber concrete exhibits superior mechanical properties, including higher compressive and flexural strengths compared to conventional concrete, as well as enhanced durability, as evidenced by the Bayesian analysis results.
- In conclusion, the study compared the properties of conventional concrete and concrete reinforced with 2% sisal fibers.
- The average compressive strength of sisal fiber concrete increased by 45.5% to 30.82 N/mm2, significantly surpassing the 21.17 N/mm2 of conventional concrete.
- Similarly, the flexural strength of sisal fiber concrete increased by 34.4% to 7.81 N/mm2, outperforming the 5.81 N/mm2 of conventional concrete.
- The durability test results also showed a significant improvement, with sisal fiber concrete achieving a compressive strength of 25.21 N/mm2, a 31.1% increase compared to the 19.23 N/mm2 of conventional concrete.
- Statistical analyses, including ANOVA and Bayesian independent sample tests, were performed, and the results indicated no significant statistical differences between the two types of concrete in terms of compressive strength, flexural strength, and durability.
- The graphical representations, including Simple Bar Charts and Bayesian Statistics, further support the findings.
AUTHORS’ CONTRIBUTION
Vijayan Selvam contributed to the data collection, data analysis, and manuscript writing. Tholkapiyan Muniyandi and Ramadhansyah Putra Jaya contributed to the conceptualization, data validation, and critical review of the manuscript.
LIST OF ABBREVIATIONS
CC | = Conventional Concrete |
SFC | = Sisal Fiber Concrete |
df | = Degree of Freedom |
AVAILABILITY OF DATA AND MATERIALS
The data and supportive information are available within the article.