All published articles of this journal are available on ScienceDirect.
Performance of Bamboo Fibre on Modifying Mechanical Properties of Concrete
Abstract
Introduction
Towards Go-green’s concept, the use of natural fibres in the construction industry has received substantial attention from many engineering fields. Literature shows that the waste has been used as a replacement or addition material in the concrete mixture for producing lightweight concrete and improving the mechanical properties of the concrete. This innovation is one of the alternative solutions in converting waste into valuable, sustainable materials and consequently reducing the abundance of the waste that may permit environmental pollution.
Aims
This study aims to investigate the mechanical properties of concrete with the addition of bamboo fibre (BF) from species type Bambusa Vulgaris, specifically focusing on the compressive and tensile strength of concrete. The chosen bamboo fibre is adopted because it is largely found in Peninsular Malaysia and has a high tensile strength, as suggested by previous researchers.
Methods
To achieve this, three percentages of the BF, i.e., 0.5%, 1%, and 1.25%, were added to concrete grade M20. The plain concrete i.e., 0% BF, was prepared as a control sample. The performance of BF on modifying the mechanical properties of concrete for both fresh (i.e., slump test) and hardened (i.e., compression and split tensile tests) states were examined after 7 to 28 days of the curing process.
Results
The findings indicate the effectiveness of BF in improving the mechanical properties of the concrete grade M20. It is noted that the concrete samples with the addition of 0.5% BF is considered as the optimum percentage because it able to increase the compressive and tensile strength of concrete grade M20.
Conclusion
This study provides significant information on the ability of BF as a concrete strength enhancer which subsequently converts the abundance of unwanted agriculture by converting the waste to new green and sustainable concrete material.
1. INTRODUCTION
Concrete is widely used as a main construction material as it provides high compressive strength, good fire resistance, and low construction cost. Concrete is a composite material made from fine and coarse aggregate bonded along with a liquid cement paste that cures the concrete to harden completely. However, concrete has moderately low tensile strength, limited ductility, and low resistance to cracking. Usually, the microcrack of structural components, especially in plain reinforced concrete, will develop even before loading, particularly due to drying, shrinkage or other volume changes [1].
Most commonly, steel reinforcement is used to provide a high tensile strength in concrete structural components, e.g., beams, columns, slabs and foundations. This composite structure is widely known as a reinforced concrete structure. The reinforcement is installed as a strengthening material and aids in improving the elasticity of concrete, which subsequently limits the cracking of the concrete or the risk of structural failure. However, there are some disadvantages of steel material whereby this material is vulnerable to corrosion risk, non-renewable and relatively expensive, which causes an increment in the total construction cost.
Recently, many studies investigated the use of natural fibres in enhancing the strength of the concrete either as a replacement or addition material in a concrete mixture [2-5]. Natural fibres are a sustainable materials that can be found easily, renewable and relatively cheaper than synthetic fibre e.g., steel, carbon, and glass fibres. In most studies, fibre is added to a cement matrix in an orderly or randomly distributed manner. Concrete strength with the replacement or addition of natural fibre can be improved depending upon the efficiency of the concrete mixture and fibres in transferring the induced stresses. This largely depends on the type, percentage of replacement or additional, geometry, content, and distribution of the fibres in concrete. Besides, the mixing and compaction techniques of concrete, size, and shape of the aggregate also play an important role in improving the mechanical properties of the concrete [1-3].
Numerous studies showed that natural fibres such as pineapple leaf, coconut, kenaf, and bamboo fibre have successfully improved the tensile strength and energy absorption of concrete [2, 6-9]. For instance, studies conducted by Ali et al. [9], Fuqua et al. [10], Ahmad et al. [11] and Aziz et al. [12] reported that the natural fibres not only enhanced the tensile strength of concrete but have successfully bridging the crack of the concrete. In addition, numerous researchers proved that bamboo as an alternative to steel as a reinforcement in providing high tensile strength and bond strength [6, 13-22]. Meanwhile, bamboo Fibres (BF) have recorded remarkable achievements as reinforcing materials in various applications, such as concrete [23-28], mortars [29-30], asphalt [31, 32], and recycled plastic composites [33-35]. Most of the studies reported similar agreement that the addition of BF has significantly improved the mechanical properties (i.e., tensile, compressive, and flexural strength) and cracking resistance of the hybrid composites. The literature concludes that the maximum strength of bamboo-reinforced composites can be achieved after 28 days of curing with varying optimum addition percentages of BF, which range from 0.5% to 1.5% by weight of cement [23-28,30-35].
Surprisingly, Marcus Maier et al. [ 29 ] observed an insignificant adverse effect on the addition of BF when utilized in a mortar mixture. They highlighted that the reinforced mortar specimens experienced slight losses of compressive strength. However, they stressed that the addition of BF was able to improve crack-bridging effects and control crack propagation.
The advantages of the use of BF are extended in the research conducted by Tonmoy Kumar Brahmachary and Md. Rokonuzzaman [36] and Siswanto, et al. [37], whereby the BF is added in weak soil, improve the mechanical properties of the concrete. They concluded that the soil mechanical properties increase proportionally to the increment in length and diameter of BF. It was also found that increasing the percentage of BF increases the CBR value of reinforced soil, and this increment is significant at fibre dosage of 1.2%.
To highlight the inherent benefit of natural fibres, in this present study, the mechanical properties of concrete with the addition of BF were investigated. Three percentages of the BF, i.e., 0.5%, 1%, and 1.25% [25-27] were added in concrete grade M20. The results are reported for both fresh (i.e., slump test) and hardened (i.e., compression and split tensile load tests) states of concrete. The mechanical properties of the concrete with and without the addition of BF were tested after 7 to 28 days of the curing process. The outcome of this study may provide essential information on the utilization of BF as a new sustainable construction material in the industry. Consequently, the finding also offers an alternative solution to convert the abundance of bamboo to wealth.
2. MATERIALS AND METHOD
The material and experimental setup in this study is divided into subheadings i.e., preparation of bamboo fibre, preparation of concrete mix design for M20, preparation of compression load test, and preparation for the tensile load test. Each subheading provides a detailed and concise description of the types of materials used and experimental works conducted in this study.
2.1. Preparation of Bamboo Fibre
Bamboo waste used in this study is from the species of Bambusa Vulgaris because it is largely found in Peninsular Malaysia and has a high tensile strength, as suggested by previous researchers [5, 13, 21-23]. The fibres (coarse and short) were extracted from the untreated (i.e., no preservation treatment during post-harvest) bamboo culms waste using the manual handling method, i.e., using a hammer (Fig. 1). The fiber was left dried under sunlight for 24 hours to remove any substances before cut into ± 10 mm length (l) with diameter (d) in range of 0.25 mm and aspect ratio (l/d) of 40 [18,19,21-27] the untreated BF, i.e., 0.5%, 1%, and 1.25% was added in concrete mixture grade M20 based on weight calculation method as recommended by Kavitha S. and T. Felix Kala [25-27].
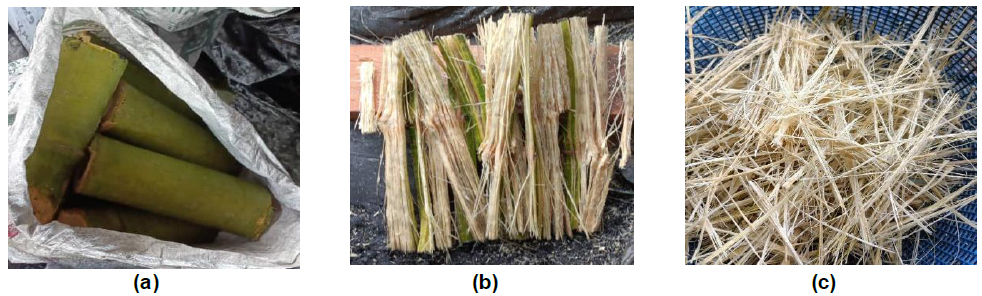
2.2. Preparation of Samples for Concrete Mixture M20
A concrete grade M20 was designed in accordance with standard BS 5328: Part 2: 1997 [38]. Table 1 shows the standard mix ST5 chosen in this study for the calculation of the concrete design mix of cube and cylinder samples. In the standard, the concrete mix design is presented as the total weight of cement, fine and coarse aggregate for 1 m3 volume of sample. The cube sample with the dimension of 0.15×0.15×0.15 m3 was prepared for the compression test, meanwhile, the cylinder sample with a dimension of π×0.075×0.3 m3 was used for the tensile split test. The Ordinary Portland Cement (OPC), with the maximum size of fine and coarse aggregate limited to 5 mm and 20 mm, respectively, was used in compliance with the Malaysian Standard (MS) MS 522: Part 1:2003 [39].
Table 2 shows the concrete mix percentage for the cube and cylinder samples used in the laboratory test, which contains the weights of water, BF, coarse aggregate, and fine aggregate. The concrete samples were made using three BF addition percentages, i.e., 0.5%, 1.0%, and 1.25%, in accordance with other studies conducted by [3, 6-9]. For validation reasons, samples with 0% BFW were generated as a reference or control sample.
A total of 36 samples (Fig. 2) were tested in two concrete states, i.e., fresh and hardened concrete. The slump test was measured in the fresh concrete state to determine the workability of the mixture. Further, in the hardened concrete state, the compression and tensile split tests were conducted to determine the mechanical properties of the concrete. The results of each laboratory test were recorded based on the average of three samples prepared with the addition of BF, as summarised in Table 3.
2.3. Preparation of Laboratory Testing
The effect of BF on concrete was investigated by performing the mechanical properties of the concrete in fresh and hardened states. The slump test was conducted according to BS EN 12390 Part 2 [40] to determine the workability of the concrete mixture of fresh concrete samples. In contrast, following the BS EN 12390 Part 3 [41] and Part 6 [42], two laboratory tests were conducted, i.e., compressive test and split tensile test for the hardened state of concrete. Fig. (3) shows the compression machine used to conduct testing on the samples of hardened concrete (Table 3).
Standard Mix | Characteristic Compressive Strength at 28 Days (N/mm2) |
Constituents (Cement and Total Aggregate) (kg) |
Maximum Size of Aggregate | |||
---|---|---|---|---|---|---|
40 mm | 20 mm | |||||
Workability | ||||||
Medium | High | Medium | High | |||
ST1 | 7.5 | Cement | 180 | 200 | 210 | 230 |
Aggregate | 2010 | 1950 | 1940 | 1880 | ||
ST2 | 10 | Cement | 210 | 230 | 240 | 260 |
Aggregate | 1980 | 1920 | 1920 | 1860 | ||
ST3 | 15 | Cement | 240 | 260 | 270 | 300 |
Aggregate | 1950 | 1900 | 1890 | 1820 | ||
ST4 | 20 | Cement | 280 | 300 | 300 | 330 |
Aggregate | 1920 | 1860 | 1860 | 1800 | ||
ST5 | 25 | Cement | 320 | 340 | 340 | 370 |
Aggregate | 1890 | 1830 | 1830 | 1770 | ||
Workability – Slump (mm) | 50 - 100 | 80 - 170 | 25 - 75 | 65 - 135 |
Component | ST5 | Cube | Cylinder |
---|---|---|---|
1m3 | 0.15×0.15×0.15 m3 | π×0.075×0.3 m3 | |
Cement (kg) | 383 | 1.302 | 2.03 |
Coarse Aggregate (kg) | 1256 | 4.270 | 6.657 |
Fine Aggregate (kg) | 560 | 1.904 | 2.97 |
Water (kg) | 192 | 0.653 | 1.018 |
Bamboo Fibre (BF) | |||
0.5% | - | 0.0374 kg | 0.0583 kg |
1% | - | 0.0748 kg | 0.1166 kg |
1.25% | - | 0.0935 kg | 0.1457 kg |
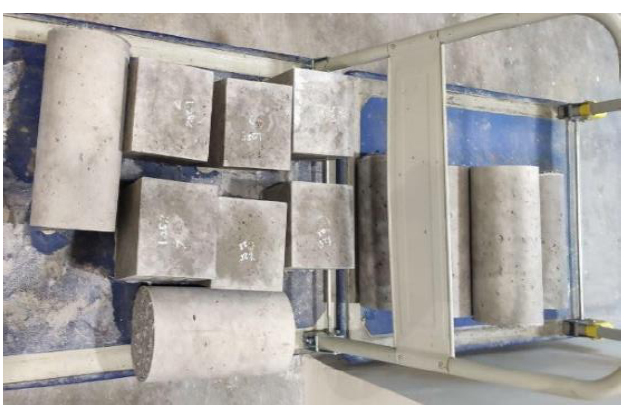
Sample |
Compression Test Cube: 0.15×0.15×0.15 m3 |
Split-Tensile Test Cylinder: π×0.075 ×0.3 m3 |
||
---|---|---|---|---|
Curing Days | ||||
7 | 28 | 28 | ||
% of Bamboo Fibre (BF) | 0% (Control) | 3 | 3 | 3 |
0.5% | 3 | 3 | 3 | |
1.0% | 3 | 3 | 3 | |
1.25% | 3 | 3 | 3 | |
Total | 12 | 12 | 12 |
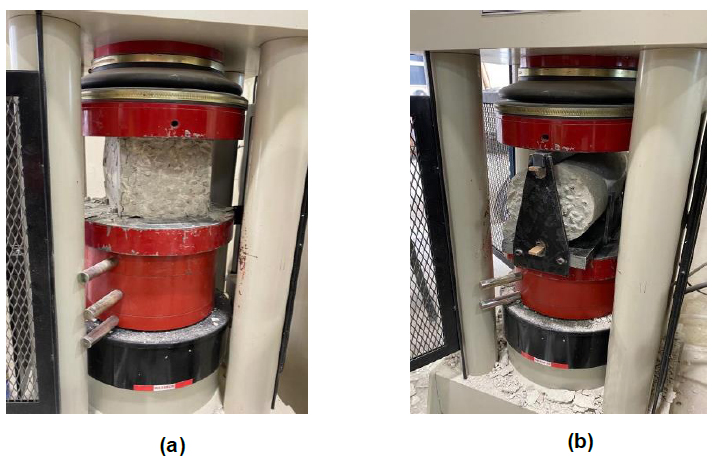
For the compression test, according to S. Mali et al. [43], Y. Xiao et al. [44], and P. Rossi et al. [45], the 7 to 28 days of curing samples were tested for a maximum load rate of 15 NM/m2/min (i.e., 150 kg/cm2/min) until the samples fail or break using compression machine depicted in Fig. (3). The test was performed to estimate the ultimate compressive strength of samples under the applied compression load. The compressive strength (fc) is determined according to BS EN 12390-3:2002 [41] as shown in Eq. (1). Two parameters are required for the calculation of fc, i.e., the maximum load after the sample break, F (N), and the surface area of the contacted sample, Ac (mm2).
![]() |
(1) |
Conversely, the tensile split strength (fct) was determined based on the shear failure of the samples at the age of 28 days of curing. According to the BS EN 12390-6:2000 [42], the fct is calculated using the Eq. (2);
![]() |
(2) |
where
F = maximum applied load on the sample, N
L = length of the contact line on the sample, mm
d = diameter of the sample, mm
3. RESULTS AND DISCUSSION
This section summarizes the results and discussion of the overall experimental works, which are divided into two subheadings, i.e., fresh state concrete test and hardened state concrete test. The results obtained from slump, compression and slip tensile tests for a total of 36 samples are presented herein.
3.1. Fresh State Concrete
3.1.1. Slump Test
Based on the observation, the slump test results reduced from 60 mm to 30 mm due to an increment in the percentage of BFW in the mixtures of concrete (Fig. 4). It is noted that 1.25% addition of fibres provides the smallest slump of 30 mm due to the low capability of the fibres to mix well with other materials in the concrete. The slump test result showed a good agreement with BS 5328 - Part 2:1997 [40], as described in Table 1 above. The standard recommends that for standard concrete mix type ST5 with maximum coarse aggregates of 20 mm, the fresh concrete mixture may experience two types of slump workability, i.e., medium and high workability for the slump. The medium workability results when the slump drops in the range of 25 mm to 75 mm, while when the slump is between 65 mm to 135 mm, the concrete mix is considered to have high workability. Thus, the result denoted that the concrete mixture is classified under true slump type with medium workability.
3.2. Hardened State Concrete
3.2.1. Compressive Strength (fc)
The compressive strength of the concrete samples with the addition of different percentages of BFW was obtained by performing the compression test. Fig. (5) shows the average compressive strength (fc) of concrete samples with four different percentages of BFW tested after 7- and 28-days of the curing process. As can be seen, the fc after 7 days of curing is slightly lower than the result obtained after 28 days [2-4, 6, 7, 9]. The difference in percentage of the fc is between 5% to 10%. The highest of the fc (i.e., 10% increment) was recorded for the concrete samples with the addition of 0.5% BF in the mixture. However, the trend started to decrease with more addition of BF for both 7- and 28-day concrete samples.
However, the fc of the 28 day samples increased slightly to it designed concrete grade M20 of each concrete sample. The lowest strength was recorded for concrete with 1.25% BF, i.e., 14.02 N/mm2, while the highest strength of 25 N/mm2 was obtained when 0.5% BF was added to concrete samples. It is found that the optimum addition percentage of BF is 0.5%, whereby the increment of strength between the samples with and without the addition of BF is approximately 7.33% and 8.33% for 7- and 28-day concrete samples, respectively.
It is interesting to remark that the addition of BF in concrete was able to increase the fc within 28 days of the curing process. As reported by previously mentioned researchers [2-4, 6, 7, 9, 18], the increment of strength might be due to the ability of the fibres to improve the bonding in the mixture and absorb the energy release from the applied load while subsequently retarding or reducing the risk of cracking.
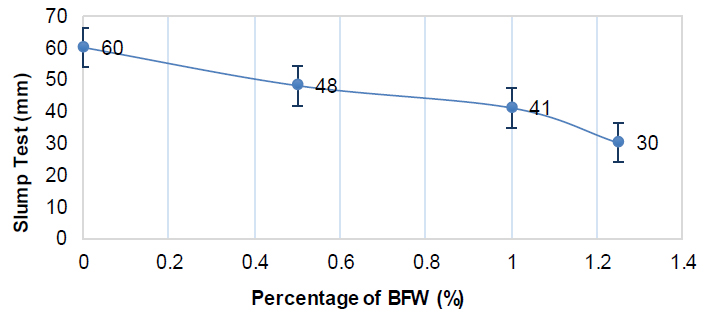
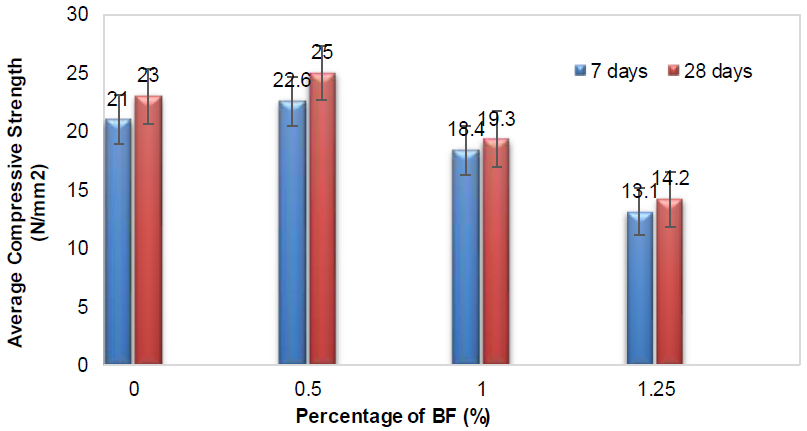
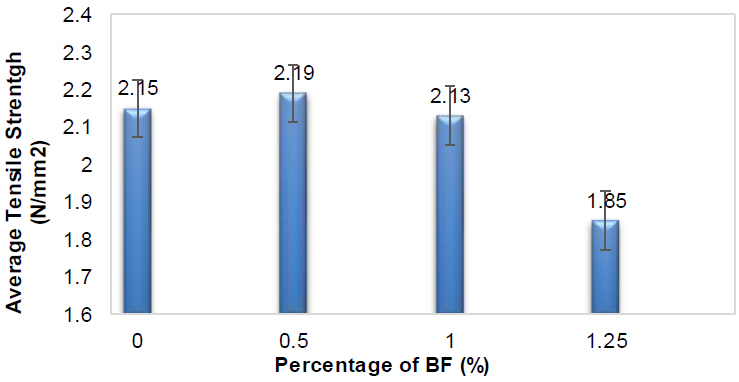
Strength |
BF
Content % |
Present Study, 2024
Concrete M20 |
S. Kavitha and T. Felix Kala [
25
]
Concrete M30 |
---|---|---|---|
Average Maximum Compressive strength (N/mm2) |
0 | 23 | 32.8 |
0.5 | 25 | 33.7 | |
1 | 19.3 | 41 | |
1.25 | 14.2 | 38.9 | |
Average Maximum Split tensile strength (N/mm2) |
0 | 2.15 | 2.68 |
0.5 | 2.19 | 3.1 | |
1 | 2.13 | 4.8 | |
1.25 | 1.85 | 4.3 |
3.2.2. Split Tensile Strength (fct)
The split tensile test after 28 days of the curing process was carried out to determine the capability of samples to resist the applied tensile load. Fig. (6) demonstrates the result of the average tensile split strength (fct) of the specimens. The tensile strength of the sample without the addition of BF is 2.15 N/mm2 was used as the reference value. It is noted that there is a slight increment of fct when the concrete is added with 0.5% BF i.e., 2.19 N/mm2. A similar trend of strength decrement was experienced when more BF was added in concrete [24-37]. The lowest was 1.85 N/mm2 for samples with the addition of 1.25% BF. It is noted that the fct in the present study produced relatively lower strength compared to previous literature [2-4, 6, 7, 9].
Furthermore, validation with previous literature is conducted by comparing the mechanical properties of concrete with various percentages of bamboo fibre addition, as demonstrated in Table 4. According to the table, it is found that both studies observed a significant increment in compressive and tensile strengths of the concrete with the addition of BF. However, the optimum addition percentage observed from both studies differs, i.e., the present study reports a strength increase of 0.5% BF, whereas the previous literature observed the optimum increment of strength after 1% BF is added in concrete. This variance may be due to the different concrete grades used by both researchers. Conversely, it may be hypothesised that the fibre functions as a bridge material, impeding the propagation of cracks in the hardened mixture and thereby enhancing its strength.
CONCLUSION
In this study, the performance of BF in modifying the compressive and tensile properties of concrete was investigated. Three percentages of the BF, i.e., 0.5%, 1%, and 1.25% were added in concrete grade M20. The results were examined under two hardened states of concrete, i.e., compression and tensile split tests. The results denoted that the addition of BF in concrete has slightly improved the mechanical properties of the concrete. The optimum addition percentage of BF is recorded at the addition of 0.5% BF at 28 days of curing.
According to the results, theaddition of BF has successfully increased the compressive strength of the samples by approximately 7.33% and 8.33% for 7- and 28-days of M20 concrete samples, respectively. An insignificant increment of tensile strength of concrete was recorded for tensile strength of the concrete. Nevertheless, a similar trend of strength decrement was experienced when 0.5 - 1% of BF is added in concrete [2-4,6,7,9,25-27]. The research found that similar agreement with previous literature [24-37] is observed when the strength of concrete drops at 1.25% fiber content due to poor bonding between the cement matrix and aggregate. This study presents significant information on the ability of BF as a concrete strength enhancer which subsequently converts the abundance of natural waste by converting the waste to application of production of noble green and sustainable concrete material.
HIGHLIGHTS
• Bamboo Fibre (BF) increased the compressive strength of the concrete grade M20.
• Bamboo Fibre (BF) increased the tensile strength of the concrete grade M20.
• Bamboo Fibre (BF) provides the ability to be used as a strength enhancer in concrete mixtures.