All published articles of this journal are available on ScienceDirect.
The Effect of Using Jute on the Compressive Strength of Concrete
Abstract
Background
Concrete comprises cement, fine aggregates, coarse aggregates, and water, making it the most widespread construction material globally. However, while producing cement as an important component of concrete, it generates significant CO2 emissions, worsening global warming and environmental challenges worldwide.
Objective
This study aims to investigate the impact of incorporating jute fiber into concrete mixes of varying proportions to enhance compressive strength.
Methods
Concrete mixes of three grades were prepared, with varying percentages of jute (0.5%, 1.0%, 1.5%, and 2%) by weight of cement. Compressive strength tests were conducted at 7 and 28 days of curing.
Results
It shows notable enhancements in strength, improvement of 15.07 % (for Nominal mix 1:1:2) and 20.29% (for Nominal mix 1:1.5:3 ) is at the addtion of 1% jute but 6.72% (for Nominal mix 1:2:4) is at addtion of 2% jute mix.
Conclusion
Findings suggest that adding jute fiber, particularly with higher cement content, significantly enhances concrete strength, emphasizing its potential as a reinforcing material for sustainable construction.
1. INTRODUCTION
Concrete is a vital construction material renowned for its strength and durability and the most common building material in the world [1]. It consists of mainly four main ingredients, namely cement, fine aggregates, coarse aggregates, and water [2]. When aggregate is combined with dry Portland cement and water, it creates a fluid mass that can be molded easily. Chemical reactions occur between the cement, water, and other ingredients, resulting in a hard matrix that binds the materials together, forming a durable, stone-like substance [3]. “Compressive strength, crucial in concrete, is influenced by various factors: raw material quality, water-cement ratio, aggregate proportions, concrete age, compaction, temperature, humidity, and curing methods.
These parameters collectively determine the durability and structural integrity of concrete structures” [4]. Cement significantly impacts the compressive strength of concrete due to its binding properties and chemical reactions [5]. The demand for cement is rising daily due to its crucial role in construction and infrastructure development [6]. During cement production, clinker is burned at around 1500°C, emitting substantial CO2. This contributes to the rise of global temperature, a significant factor in climate change [7]. Cement production contributes about 7% of global CO2 emissions, resulting in continuous increases in global warming [8].
Nepal presents a prime opportunity for implementing jute incorporation into concrete production due to its abundance, offering a viable and potentially successful strategy for enhancing construction materials [9]. On the other hand, the code described in the references [10] and [11] for concrete admixture specification does not explain the use of jute on concrete. Unfortunately, there is no such code or any legal document that defines the use of natural fiber, such as jute on concrete. Thus, it is essential to study the real effect of the jute fiber on the compressive strength of concrete experimentally.
1.1. Limitation on Previous Research
The previous research examining the impact of incorporating jute fibers into concrete to assess its effect on compressive strength faces several limitations. Firstly, there is a scarcity of comprehensive studies specifically dedicated to this aspect, with much of the existing literature focusing on other characteristics of jute-reinforced concrete. Additionally, the variability in experimental conditions, including differences in jute fiber types, concrete mix designs, curing methods, and testing protocols, presents challenges in drawing conclusive comparisons across studies.
To solve these problems, research in cement and concrete technology has concentrated on the use of artificial or natural fiber materials as partial replacements for cement. According to a study [12], natural fibers show promise over artificial polymer-based fibers for rein- forcement in Fiber-Reinforced Cement Concrete (FRCC), offering solutions to address inherent deficiencies in FRCC with polymer-based fibers. The primary drawbacks of artificial fibers in concrete are their high cost and associated health and environmental risks [13].
The benefit of using natural fibers is that they can help reduce building costs [14]. It can also help to preserve the environment by optimizing the usage of plant and agricultural waste [15]. In correspondence to that, many studies on natural fibers have taken place for more than twenty years. According to a study [16], “extensive research is underway to explore the utilization of reinforcing fibers such as jute, bamboo, sisal, awkward, coconut husk, and sugarcane bagasse in cement composites, particularly for construction materials. Previous research .” [17-19] studied different types of fibers and found that the total plastic shrinkage crack area was reduced as compared to normal concrete. Recent investigations [20, 21, 22] deal with the effect of jute as natural fiber reinforcement on the strength of concrete. They found that the strength of the concrete increased.
1.2. Research Significance
1.2.1. Environmental Sustainability
This study explores the integration of jute into concrete, presenting a potential eco-friendly solution to reduce the carbon footprint of construction. Investigating its impact on compressive strength aligns with global efforts towards sustainable building practices, offering insights into green alternatives to traditional rein- forcement materials.
1.2.2. Economic Implications
Understanding how jute affects concrete strength carries significant cost implications for the construction industry. If proven effective, jute could offer a cost-effective alternative to conventional materials like steel, particularly in regions where jute is abundant and affordable. This research has the potential to drive cost savings and enhance the economic viability of construction projects.
1.2.3. Performance Optimization
Evaluating the influence of jute on compressive strength contributes to the development of optimized concrete formulations. By identifying the ideal balance between strength requirements and sustainability goals, engineers can design more resilient structures while reducing environmental impact. This research facilitates the advancement of performance-driven construction practices.
1.2.4. Diversification of Materials
Research on jute-reinforced concrete diversifies the range of available construction materials, reducing dependence on finite resources. By promoting the adoption of sustainable alternatives, this study fosters innovation within the construction sector and enhances resilience against material shortages or price fluctuations.
1.2.5. Market Opportunities
The findings of this research could create new market opportunities for jute producers, manufacturers, and construction firms. Jute-reinforced concrete has the potential to introduce innovative products and technologies to the market, driving growth and competi- tiveness in the construction industry while addressing environmental concerns.
1.2.6. Global Impact
The significance of this research extends globally, addressing sustainability challenges in construction beyond local contexts. By offering a viable solution to enhance the environmental performance of infrastructure projects, this study contributes to broader international efforts towards sustainable development and mitigates the impact of construction activities on the planet.
2. MATERIALS AND METHODS
2.1. Jute
Nepal is one of the major jute-producing countries [23]. Jute is mainly produced in the Terai region of Nepal [9]. It was fined using the fining comb. Furthermore, the jute fiber was chopped in length about 5 mm to 1 cm and was submerged in water for 24 hrs before use. Table 1 shows the properties of the jute used in this study. A previous study [24] concluded that the enhancement of compressive strength on concrete is greater for 10- and 15-mm fiber cuts than for other lengths. So, for this study, the length of the jute was chosen to be 5 to 10mm. Tables 2 and 3 show the physical and chemical properties of jute, respectively. [25].
S.No. | Physical Properties | Test Result |
---|---|---|
1 | Maximum size (mm) | 0.2 to 0.5 |
2 | Chopped length (mm) | 5 to 10 |
3 | Slenderness ratio | 10 to 50 |
Density (g/cm3) | 1.3 |
---|---|
Young’s modulus (GPa) | 26.5 |
Tensile strength (MPa) | 393–773 |
Elongation at break (%) | 1.5–1.8 |
Constituents | % |
---|---|
Cellulose | 61–71 |
Hemi Cellulose | 14–20 |
Lignin | 12–13 |
Waxes | 0.5 |
2.2. Cement
Cement, typically utilized for bonding in concrete within the construction industry, commonly consists of ordinary Portland cement, serving as a fundamental component in various construction applications. Tables 4 and 5 show the physical and chemical properties of cement, respectively [26].
S.No. | Characteristics | OPC 53 |
---|---|---|
1 | Specific Surface (Blain method), m2/kg, Min | 225 |
2 | Soundness | - |
- | a) By Le Chatelier method, mm, Max | 10 |
- | b) By autoclave test method, percent, Max | 0.8 |
3 | Setting time in minutes | - |
- | Initial, minutes, min | 45 |
- | Final, minute, max | 600 |
4 | Compressive strength, MPa (by keeping 1 day in the air) | - |
- | 72 ± 1 h, Min | 27 |
- | 168 ± 2 h, Min | 37 |
- | 672 ± 4 h, Min | 53 |
2.3. Fine Aggregate
Fine aggregate for the concrete mix was sourced locally from river sand, undergoing washing and screening processes to remove undesirable materials and oversize particles. Specific gravity testing, as referenced in [27], was conducted on surface dry aggregate. Table 6 presents the properties of the fine aggregates utilized in this study, providing essential data for understanding their characteristics and suitability for concrete production. Fig. (1) illustrates the gradation curve of fine aggregates [28].
S.No. | Characteristics | OPC 53 |
---|---|---|
1 |
The ratio of the percentage of lime to percentages of silica, 0.66-1.02 alumina, and iron oxide, when calculated by the
formula: CaO – 0.7 SO2/ 2.8 SiO2+ 1.2Al 2 O 3 + 0.65 Fe2O 3 |
0.80-1.02 |
2 | The ratio of the percentage of alumina to that of iron oxide, Min | 0.66 |
3 | Insoluble residue, percent by mass, Max | 2.0 |
4 | Magnesia, percent by mass, Max | 5.0 |
5 | Total Sulphur content calculated as Sulphuric anhydride (SO3), percent by mass, Max; If | - |
- | Content of C3A < 5% | 2.5 |
- | Content of C3A ≥ 5% | 3.0 |
6 | Loss on ignition, percent by mass, Max | 4.0 |
S.No. | Physical Properties | Test Result |
---|---|---|
1 | Maximum size (mm) | 4.75 |
2 | Specific Gravity | 2.36 |
2.4. Coarse Aggregate
Coarse aggregates, sourced locally with a 20 mm size, underwent experimental specific gravity testing. They were ensured to be free from adherent coatings, harmful disintegrated pieces, alkali, vegetable matter, and other deleterious substances, ensuring their suitability for construction [28]. Special attention was given to ensure that the coarse aggregate did not contain excessive flaky, elongated shapes or organic impurities that could compromise concrete strength or durability. Table 7 shows the properties of Coarse aggregates.
S.No. | Physical Properties | Test Result |
---|---|---|
1 | Maximum size (mm) | 20 |
2 | Specific Gravity | 2.79 |
2.5. Water
To ensure concrete strength, clean water devoid of contaminants like oil, acid, alkali, salt, sugar, silt, and organic matter was used for mixing and curing in this study, promoting the integrity and durability of specimens
2.6. Concrete
Nominal mix concrete, comprising sand, cement, water, coarse, and fine aggregate, was utilized, with the water-cement ratio following American standards [29], to obtain high workability. Volume batching was used for the mixing process. Table 8 shows the properties of the concrete mix.
S.No. | Symbol | Cement | Fine Aggregates | Coarse Aggregate | Water |
---|---|---|---|---|---|
1 | M1 | 1 | 2 | 4 | 0.8 |
2 | M2 | 1 | 1.5 | 3 | 0.7 |
3 | M3 | 1 | 1 | 2 | 0.6 |
Table 8 presents sample details for plain cement concrete and concrete mixes with varying percentages of jute content (0.5%, 1%, 1.5%, and 2%). Cube specimens for compressive strength testing at 7 and 28 days were provided for each mix. The specimens were prepared in triplicates for consistency
3. EXPERIMENTAL
The experiment involved testing various fiber proportions to assess their impact on concrete performance and strength characteristics.
3.1. Mix Proportion
Three types of nominal mix (1:2:4, 1:1.5:3, 1:1:2) of concrete by volume batching were used. Jute was added in concrete on the base of the weight of the cement.
3.2. Preparation of the Specimen
Timber cube molds measuring 150x150x150 mm were employed for preparing concrete samples, adhering to Indian standard specifications. Before casting, all molds were meticulously cleaned, oiled, and securely fastened to ensure accurate dimensions and consistent results.
3.3. Batching, Mixing, and Casting of the Specimen
Weigh batching was executed using an electronic weighing balance for each mix proportion, followed by thorough hand mixing on a watertight platform. Here, jute fibers, previously submerged for 24 hours, were mixed with cement to enhance bonding. Subsequently, coarse and fine aggregates were added and mixed comprehen- sively, ensuring uniform distribution. Mixing continued for 2-3 minutes to achieve thorough integration before water was cautiously added to prevent loss. Cubes measuring 150x150x150 mm were utilized, cleaned, and oiled to prevent cavity formation. A needle vibrator was utilized to minimize the formation of honeycombs, and fresh concrete was deposited in molds in three layers, with vibrations halted upon the appearance of cement slurry. Entrapped air within the concrete was removed using a needle vibrator.
3.4. Demoulding and Curing
After 24 hours in timber molds at ambient conditions, the specimens were carefully removed to avoid breakage and placed in a curing tank at atmospheric temperature
3.5. Compressive Strength Test on Concrete Specimen
Compressive strength represents concrete's ability to withstand axial loading. Specimens measuring 150x150x150 mm were cast for each mix proportion, following guidelines outlined in [29]. These specimens, incorporate various jute fiber contents for testing at 7 and 28 days of curing. At least three specimens per age were prepared for testing. Specimen weight was measured using an analog weighing machine. Subsequently, specimens were placed in a compressive testing machine, ensuring axial load application without shock, gradually increasing until specimen failure. The maximum load endured was recorded, from which compressive strength was derived. Compressive strength (fc) is calculated using the formula [30]:
fc=P/A |
Where fc is the compressive strength (N/mm2), P is the maximum load endured by the specimen, and A is the cross-sectional area of the specimen (150x150 mm). This systematic testing process adheres to standardized procedures, ensuring accurate determination of concrete compressive strength under varying jute fiber contents and curing periods. The average of three values is considered representative if the individual variation does not exceed 15% of the average.
4. RESULTS & DISCUSSION
4.1. Compressive Strength at the Age of 7 Days
Table 9 illustrates the compressive strength of specimens at 7 days. A notable increase in compressive strength is observed with higher jute content, particularly evident in mixes 1:1:2 and 1:1.5:3. However, for these mixes, compressive strength peaks at 1.5% jute content, thereafter declining. Similarly, in mix 1:2:4, compressive strength increases with rising jute content. This trend suggests an optimal jute content for enhancing compressive strength in concrete mixes, beyond which excessive jute content may adversely affect strength characteristics.
S.No. | Jute (%) | Compressive Strength 7 Days (Mpa) |
---|---|---|
Nominal mix 1:1:2 | ||
1 | 0 | 16.96 |
2 | 0.5 | 21.04 |
3 | 1 | 22.67 |
4 | 1.5 | 24.44 |
5 | 2 | 23.19 |
Nominal mix 1:1.5:3 | ||
1 | 0 | 16.96 |
2 | 0.5 | 21.04 |
3 | 1 | 22.67 |
- | 1.5 | 24.44 |
- | 2 | 23.19 |
Nominal mix 1:2:4 | ||
1 | 0 | 10.00 |
2 | 0.5 | 10.22 |
3 | 1 | 10.37 |
4 | 1.5 | 10.44 |
5 | 2 | 10.81 |
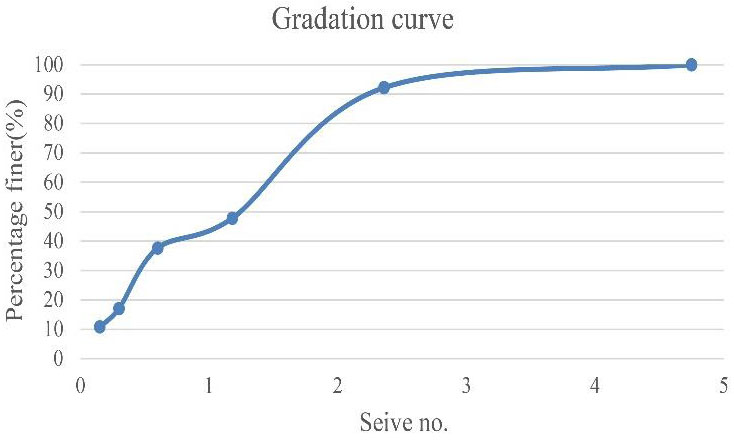
Fig. (2) depicts the percentage deviation in compressive strength of Jute Fiber Reinforced Concrete Composites compared to plain concrete across varying jute fiber weight dosages and mix ratios (1:1:2, 1:1.5:3, and 1:2:4) at 7 days. The maximum strength increment occurs at 1.5% jute content for the 1:1:2 and 1:1.5:3 mixes and 2% for the 1:2:4 mix. In mix 1:1:2, compressive strength rises by 24.02%, 33.62%, 44.10%, and 36.68% at jute contents of 0.5%, 1%, 1.5%, and 2%, respectively. Similarly, for mix 1:1.5:3, strength increases by 28.72%, 35.11%, 52.13%, and 1.06% at the same jute contents. Conversely, in mix 1:2:4, strength increments are lower, at 2.22%, 3.70%, 4.4%, and 8.15% for the respective jute contents. These findings highlight the varying effects of jute content on compressive strength across different mix ratios, emphasizing the potential for optimizing jute fiber usage to enhance concrete performance.
4.2. Compressive Strength at the Age of 28 Days
Table 10 presents the compressive strength of specimens at 28 days, indicating a significant impact of jute content on concrete strength. In nominal mixes M20 and M25, strength increases with up to 1% jute content, after which it declines. At 2% jute content, strength is lower than plain concrete. Conversely, in nominal mix M15, strength increases with jute content, albeit with lesser increments, suggesting jute's limited effect on lower-grade concrete. These findings emphasize the complex relationship between jute content and concrete strength, varying across different mix compositions and highlighting the need for careful optimization to achieve desired performance enhancements.
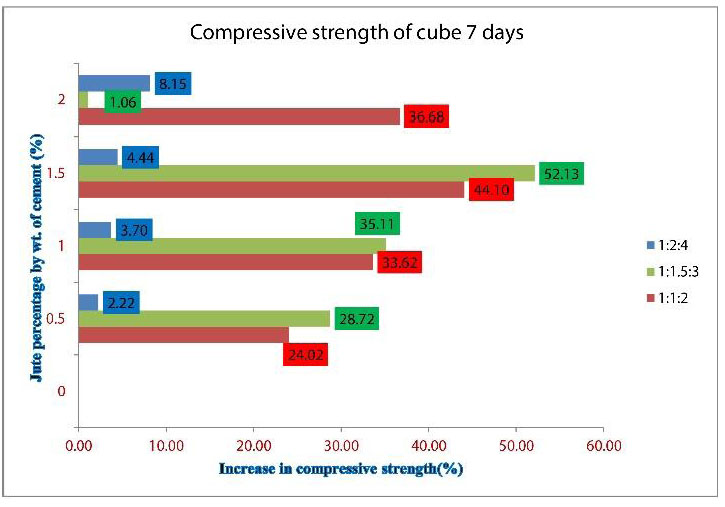
S.No. | Jute (%) | Compressive Strength 28 Days (Mpa) |
---|---|---|
Nominal mix 1:1:2 | ||
1 | 0 | 25.56 |
2 | 0.5 | 28.74 |
3 | 1 | 29.41 |
4 | 1.5 | 27.19 |
5 | 2 | 23.63 |
Nominal mix 1:1.5:3 | ||
1 | 0 | 20.44 |
2 | 0.5 | 23.70 |
3 | 1 | 24.59 |
- | 1.5 | 21.56 |
- | 2 | 19.04 |
Nominal mix 1:2:4 | ||
1 | 0 | 17.63 |
2 | 0.5 | 17.70 |
3 | 1 | 17.93 |
4 | 1.5 | 18.00 |
5 | 2 | 18.81 |
Fig. (3) displays the percentage deviation in compressive strength of Jute Fiber Reinforced Concrete Composites compared to plain concrete across different jute fiber weight dosages and mix ratios at the age of 28 days. In mix 1:1:2, compressive strength increases by 12.46%, 15.07%, and 6.38% at 0.5%, 1%, and 1.5% jute content, respectively. However, strength decreases by 7.54% at 2% jute content. Similarly, in mix 1:1.5:3, strength increases by 15.54%, 20.29%, and 5.43% at the same jute content, with a 6.38% decrease at 2% jute content. Conversely, in mix 1:2:4, strength increments are lower, at 0.42%, 1.86%, 2.10%, and 6.72% for the respective jute contents. Notably, the optimal strength increase of 20.29% is achieved at 1% jute content in mix 1:1.5:3, highlighting the importance of carefully selecting jute content to maximize concrete performance.
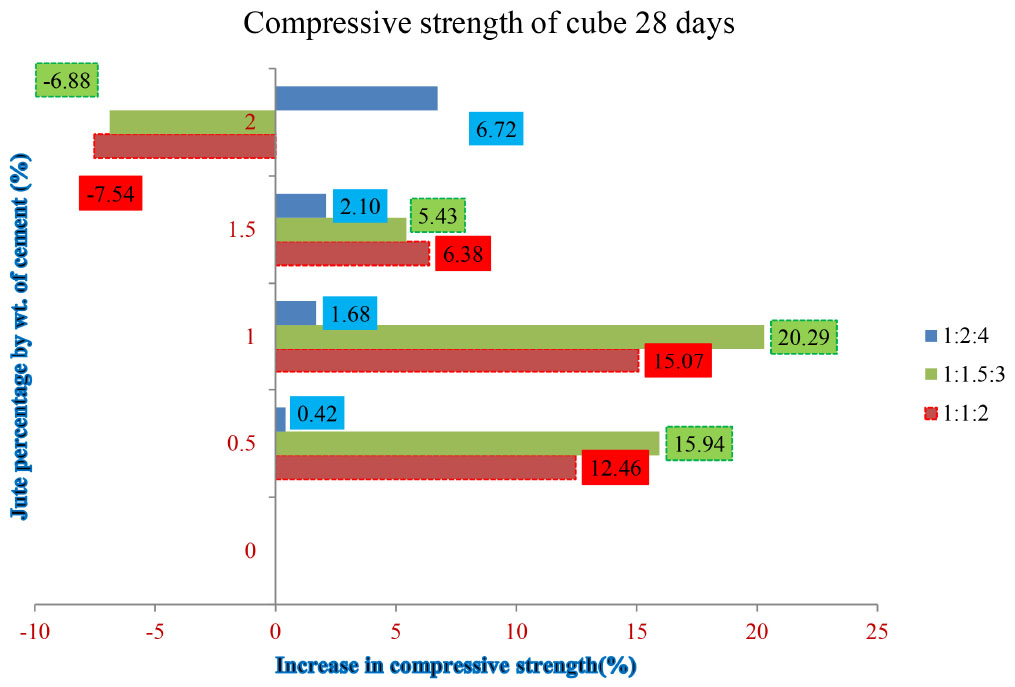
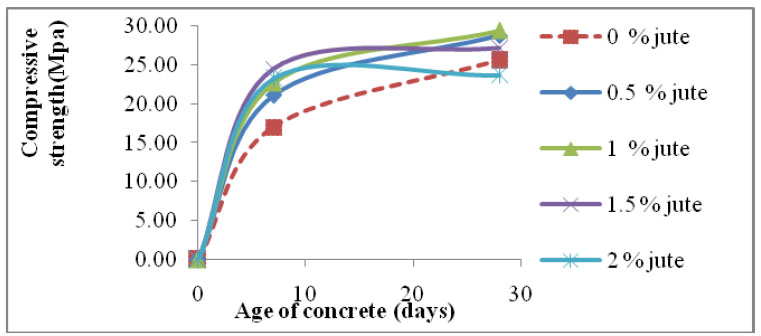
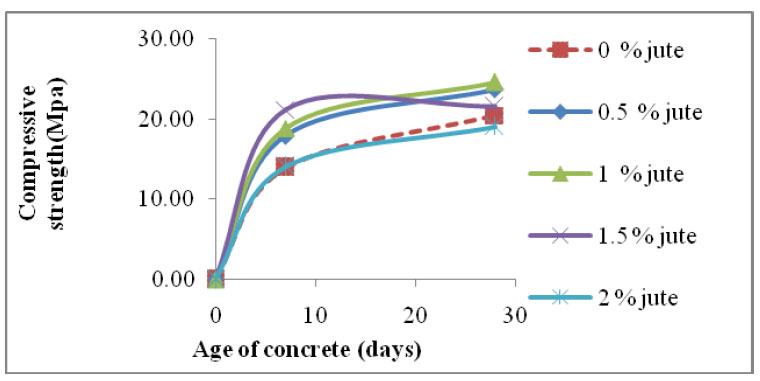
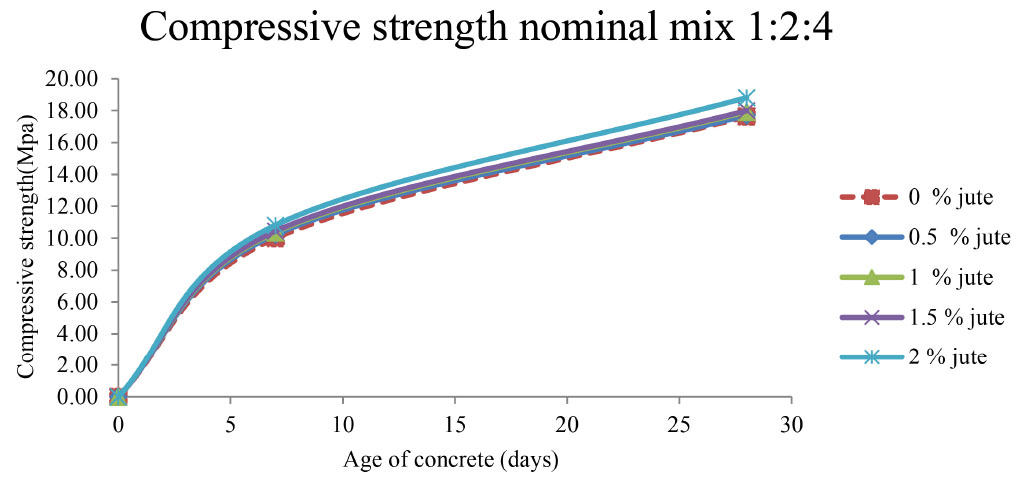
4.3. Strength Curve based on Concrete Grade
Figs. (4 and 5) show the strength curve for nominal mix 1:1:2 and 1:1.5:3, respectively. In the case of nominal mix 1:1:2 and 1:1.5:3, an increase in early age strength is found more than 28 days. It is also observed that the amount of jute has a significant effect on the compressive strength of this concrete.
Fig. (6) gives us the strength curve for nominal mix 1:2:4. Strength curves for different jute are almost coinciding, which means the effect of jute contains on compressive strength for low-grade concrete is less. Jute fiber shows better bonding with cement and aggregates.
5. DISCUSSION
Compressive strength (for both 7 days and 28 days) increases with an increase in the jute mix amount. The result is similar to the previous studies [31, 17].Maximum increment in compressive strength is 20 to29% in this research, whereas the result shown in [31] is 12.4%. However, the result of the research contradicts [32], where compressive strength decreases with the addition of jute fiber. Also, the higher content of jute causes an inhomogeneous mix. Unfortunately, the higher content of jute shows a negative effect on the strength of the concrete, which may be due to the formation of balling. A similar trend has also been observed in previous studies [24, 32].
CONCLUSION
Jute fiber demonstrates enhanced bonding with cement and aggregates, leading to increased compressive strength at both 7 and 28 days with higher jute mix amounts. However, excessive jute content can result in an inhomogeneous mix and potential negative effects on concrete strength, possibly due to balling formation. Consequently, it is concluded that optimizing jute content is crucial to maximize strength improvements while avoiding detrimental effects. This research underscores the importance of balancing jute content in concrete mixes to harness its reinforcing benefits effectively while maintaining overall structural integrity. The following conclusions have been drawn from this research work. Top of Form
1. Jute fiber improves compressive strength compared to plain cement concrete, indicating its potential as a reinforcing material.
2. Jute's impact on compressive strength is more pronounced at an early age (7 days), with greater strength increment compared to 28 days.
3. The highest strength increment occurs at 1.5% jute content for 1:1:2 and 1:1.5:3 concrete mixes and at 2% for 1:2:4 mix at 7 days of age.
4. The greatest enhancements in compressive strength were observed at 15.07% (1% jute) for 1:1:2, 20.29% (1% jute) for 1:1.5:3, and 6.72% (2% jute) for 1:2:4 after 28 days of curing.
5. Jute content has a minimal effect on low-grade concrete strength.
6. At 2% jute content, compressive strength decreased compared to plain cement concrete.
Findings of this research can be useful for sidewalks and roadways, basement foundations, bridges, shotcrete, drainage pipe and septic tanks, and mass concreting work.
LIMITATIONS OF THE STUDY
1. All the experiments were carried out at an atmospheric temperature and room temperature has not been maintained standard.
2. The properties of the cement were not determined experimentally.
3. Durability was not taken into consideration.
4. Workability was not taken into account.
RECOMMENDATIONS FOR FURTHER STUDY
1. As the present study had been conducted by co-relating the effect of the jute content on the compressive strength only, the study can be further extended using other parameters like durability, tensile strength, shear strength, etc
2. The study can be further extended increasing the curing days and types of curing methods.
3. This study could be extended to other types of natural fibers.
4. Develop research using fiber treatment with chemicals and refinement of methods of treatment.
5. Develop an investigation on the effect of fiber on the thermal response and cyclic load to composite materials.
6. Further investigation of the post-failure analysis.
LIST OF ABBREVIATIONS
IS | = Indian Standard |
FRCC | = Fiber Reinforced Cement Concrete |
Wt | = Weight |
MPa | = Mega Pascal |
GPa | = Giga Pascal |
Kg | = Kilogram |
gm | = Gram |
RCC | = Reinforced Cement Concrete |
PCC | = Plain Cement Concrete |
cm | = Centimeter |
mm | = millimeter |