All published articles of this journal are available on ScienceDirect.
Impact of Wood Ash on the Properties of Micro Basalt Fiber Cement Mortar
Abstract
Background
The continuous use of cement has been on the rise. This increase has a significant detrimental effect on the ecosystem. Many studies are being carried out in an effort to find materials that can replace cement in mortar, either fully or partially. These investigations should have solutions that will be able to produce a higher strength and durable mortar than conventional mortar.
Aim
This study aims to present a sustainable structural cement-based material with lower cement content that provides better mechanical and physical properties.
Objective
The goals of this study were to determine the cement-wood ash replacement percentage that resulted in the best compressive and flexural strength on cubes and rectangular beams, respectively, as well as to examine and evaluate the physicomechanical characteristics of the cement-wood ash mortar with and without scattered basalt fiber reinforcement.
Methods
A variety of mortar mixtures were created, each with a different amount (20%, 40%, 60%, 80%, and 100%) of wood ash replacing cement in part or entirely by volume. The effects of scattered chopped basalt fiber and wood ash/cement substitution were tested for strength after 7 and 28 days of cure. On the mortar, tests for density, slump, and water absorption rate were performed.
Results
The result of this research revealed that mortar reinforced with chopped basalt fiber had an improved compressive and flexural strength at defined mixes at 28 days of curing with a maximum compressive strength of 12.58 N/mm2. The experimental results suggest 20-40% replacement as the optimum range for cement-wood ash partial replacement. An average increase in density with an increase in sample age as well as the addition of basalt reinforcement was observed with a sample B1 containing 20 percent partial replacement of cement with ash and in the presence of basalt fiber reinforcement, exhibiting the highest density of 2272kg/m3 at 28 days of age contrasting with sample A5, containing 80 percent partial replacement of cement with wood ash. Moreover, sample A5 showed a density of 1824 kg/ m3, the lowest value at 28 days of age.
Conclusion
The study showed improvement in the flexural and compressive strength of the mortar when reinforced with micro basalt fiber. The partial replacement of cement with wood ash in mortar showed an impact on the water absorption rate and strength of the mortar. Hence, this cement-wood ash mortar reinforced with micro basalt fiber can be used in plastering walls or for flooring to improve the properties of the concrete structural members. Additionally, it can also be used in concrete repairs.
1. INTRODUCTION
The fields of building and material science have shown a great deal of interest in several adaptable and sustainable materials because of their unique qualities and commitment to the environment. For example, mortar, basalt fiber, and wood ash may be used. Mortar, a mixture of cement, sand, and water, is crucial to the construction industry. Buildings, bridges, and walls benefit from their binding properties, which give them strength and durability [1]. In between bricks, stones, or other building materials, mortar is renowned for its ability to fill gaps and create a strong connection. Due to its superior compressive strength (fc), outstanding workability, and weather resistance, it is a crucial component in building projects all over the world.
The correct design of mortar is one of the most important issues because the connection between two structural elements plays an important role in the construction of a building. Proper design means selecting appropriate components and their relative proportions to economically improve the required workability, strength, and durability [2].
The rapid development of the construction industry has increased the demand for cement. However, cement production causes depletion of natural resources and greenhouse gas emissions. Finding new, environmentally friendly cement varieties is important, and using substitute products as supplemental cementitious materials is a possibility [3]. Ash is one example of these materials [4]. There is also industrial waste and agricultural and industrial waste. According to this understanding, partially replacing ordinary Portland cement (OPC) with fly ash has two advantages. (i) reintroduce waste into the production chain and (ii) the amount of cement that has to be produced is reduced [5].
A large amount of waste and by-products are generated during manufacturing processes, service industries, and general waste. As a result, solid waste management has become one of the world's major environmental issues [6]. As environmental awareness increases, landfill space becomes limited, and costs continue to rise, the use of waste and by-products in mortar manufacturing and construction has become an attractive alternative to landfills [7], partially addressing environmental concerns. We will provide you with a solution. The use of wastes and by-products in mortar not only facilitates their use in reducing the quantity of cement used in mortar and concrete production but also helps in producing a sustainable construction material for a sustainable environment, which has many indirect benefits, such as reduced landfill costs, savings in energy, and potential environmental protection. The use of by-products and waste in mortar production reduces the amount of carbon dioxide emitted during the production of cement. Also, the cost efficiency in the use of by- and waste products is better compared to the use of 100% cement in mortar. In addition, its use can improve the microstructural properties of mortars and concrete, which are difficult to achieve with ordinary Portland cement alone.
Studies have shown that most of these materials used as concrete aggregates are absorbed by the construction industry [8]. Fly ash [9], silica fume [10], pulverized fuel ash [11], volcanic ash [12], rice husk ash [13], and corn husk ash [14] have been investigated for use as additional cement materials. Wood waste, produced as a by-product of combustion in wood-burning power plants, paper mills, and other wood-burning facilities, is of interest as a sustainable material for a variety of applications. Calcium, magnesium, potassium, and phosphorus are just a few of the many chemical elements included in this product.
The use of wood ash has been considered to produce sustainable building materials that can reduce the amount of cement in cement-based building materials. Wood ash has long been used as a soil additive for its ability to increase soil fertility and provide nutrients for plant growth [15]. According to a study [16], the possibility of wood ash as a partial replacement of cement in concrete production was investigated because it has pozzolanic properties that improve the strength and service life of concrete mixtures.
Whether cementitious matrices can be used in structural cementitious material is dependent on the mechanical properties of the material. These characteristics typically suffer when OPC is substituted with wood bottom ash (WBA) [17]. Yet additional applications are being considered [18]. Research on the environmental impact of this binder [5, 19], as well as the sustainability of WBA products, needs to be expanded [20]. These conditions must be met for the use of these materials to be truly sustainable [21].
Research has been conducted on the impact of using wood ash instead of cement on the performance of concrete [22]. The performance of concrete has been studied when wood ash has been substituted for cement at percentages of 5%, 10%, 15%, and 20%. The results confirmed that adding wood ash instead of cement improves the overall functionality of concrete.
Aprevious study [23] investigated the use of wood ash from biomass as a partial replacement for cement in wood-cement particle boards. The thermal, flexural, and stiffness properties of wood cement ash panels (WCAP) were examined. Wood ash was used in place of some of the cement in 10%, 20%, 30%, 40%, and 50% of the particleboards. According to their findings, the mechanical qualities progressively deteriorated until the ash content reached 30% of replacement, while the water demand rose as the ash level increased. The best outcomes were reported when cement was replaced to a weight percentage of about 30%.
Work carried out using cement mortar in which a portion of the cement was replaced with wood ash is reviewed from various aspects, such as physical, chemical, strength, and durability of the mortar. Water absorption and compression tests were conducted in an environment simulating cement mortar [24]. The results showed that when 40 mm cubes were substituted with 0% wood waste ash, their fc was 24.07 N/mm2 after 7 days of curing and 28.13 N/mm2 after 28 days of curing; when 10% of wood waste ash was substituted, fc was 17.28 N/mm2 after 7 days of curing and 20.67 after 28 days of curing. The results showed that the water-absorbing capacity of the mortar dropped as the percentage of wood ash increased and that the fc of the mortar reduced by 26.52% at a replacement of 10% compared to the control mortar.
The behavior of concrete containing wood ash at different replacement percentages (0%, 5%, 10%, 15%, 20%, 25%, and 30%) was observed in the study [25]. Experiments have shown that adding wood waste ash to concrete as a replacement material reduces the workability of the concrete. This is because wood ash particles have a more specialized surface area than cement particles. After all, they are smaller. As a result, these particles take up more water, which eventually makes them less workable.
Another study [26] evaluated the fc of cement mortar mixtures that included fly ash made from wood waste that was collected from a power plant that burned wood biomass. Fly ash from wood waste was substituted for cement at 10, 20, and 30% replacement weight of the total weight of the binder. In comparison to identical pure OPC mortar, mortar mixtures containing 10% wood waste fly ash showed higher 28-day fc but reduced flexural strength (ff). Relative to a comparable clean OPC mortar mix, it was found that the use of wood waste fly ash as a partial cement replacement material reduced 28-day compressive strength at higher replacement levels of 20 and 30% of total binder weight.
The usage of wood ash in the creation of High-Performance Mortar (HPM) was covered in a research [27]. The various weight percentages of wood ash that were used to partially replace cement were 6%, 8%, 10%, 12%, 14%, and 16%. Density, fc, and ff were among the experimental tests conducted. The findings showed that the wood ash reduced the density of HPM. Furthermore, adding 10% wood ash to the mix in place of some of the cement resulted in the highest fc and ff for HPM.
The problem of cement mortars being generally brittle exists. Using cement mortar for construction has been extremely difficult due to its brittleness. The use of dispersed reinforcement has been contemplated to increase mortar strength and provide remedies for the tendency of the cement mortar to fracture easily. Fiber-reinforced cement-based composites are widespread worldwide. A study [2] has shown that mortars designed with appropriate fiber reinforcement significantly improve freshness, mechanical properties, and dynamics. Given the importance of chopped basalt fiber (BF) for mortar reinforcement, this study further explores the use of chopped BF for mortar design. The production, technical characteristics, and application-related advantages of chopped BF are described in detail in the study [2].
Basalt fiber is a relatively new material but is steadily growing in many industrial applications. It is made of basalt, a volcanic rock formed by the hardening of lava. The promising mechanical properties of basalt fibers (BF) include high tensile strength, excellent chemical stability, and thermal stability [28]. For composite structures, such as concrete, the strength and durability of basalt fibers make them ideal reinforcements.
Using a scanning electron microscope (SEM), a study [29] examined the fiber distribution and microscopic morphology of basalt fiber-reinforced polymer concrete (BFRPC), and the microstructure was used to further assess the BF reinforcing process. There was no discernible interfacial transition zone in the microstructure, indicating that the BF was firmly attached to the substrate. BF was tightly attached to the substrate and shared the stress with it when BFRPC was subjected to an external load. The reasearchers accomplished the goal of toughening and obstructing the crack in concrete so that the microstructure of the material could be enhanced and eventually pulled out or fractured by using their strength and good interfacial adhesion to absorb the energy of crack development. The cross-section of the fractured fiber is shown in Fig. (1b), whereas Fig. (1a) depicts the smooth hole that remains after the fiber is removed from the matrix. According to the study conducted by Zhang [30], if the BF content is low, the majority of the BF distributed along the crack is broken or pulled out; conversely, if the BF content is high enough, the fiber can withstand the majority of the transverse tensile force, which effectively slows down the concentration of stress and prevents the crack from expanding and developing. The degree of bonding between the cementitious base and the interfacial transition zone is affected by the uneven distribution of BF, as illustrated in Fig. (1a), which causes the fiber to agglomerate and overlap. As a result, the contribution of BF to the improvement of mechanical properties is reduced. Sha [31] also noted in his research that BF would agglomerate and lose fc if its volume proportion is too high.
In another study [32], the compression test failure mode for cubes was shown as illustrated in Fig. (2). The development of significant fissures over their whole length caused a cube specimen made of plain concrete to collapse. In contrast, adding BFs to the concrete failed because of the formation of small, thin fissures on their surfaces. This demonstrates how well the BFs and concrete matrix adhere to one another. Similar results have been reported by another study [33]. The amount of chopped BF and fiber dispersion affected the fc of BF concrete. Due to the periodic hoop effect, the standard concrete cube sample fractured with a loud noise as its weight increased. Fig. (2) shows the failure mode of normal concrete. Another study showed that cracks in simple concrete samples started forming at sloped locations and continued to grow until they eventually cracked.
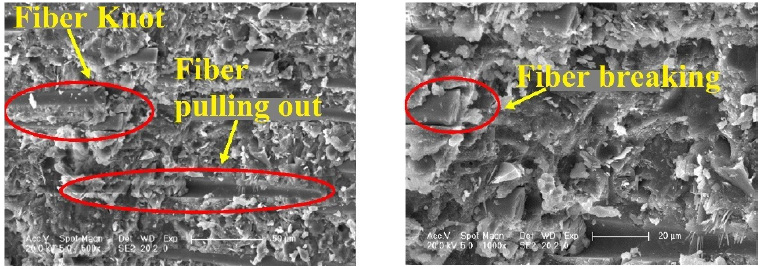
Available online under the Creative Commons Attribution (CC BY) license (https://creativecommons.org/licenses/by/4.0/) [29].
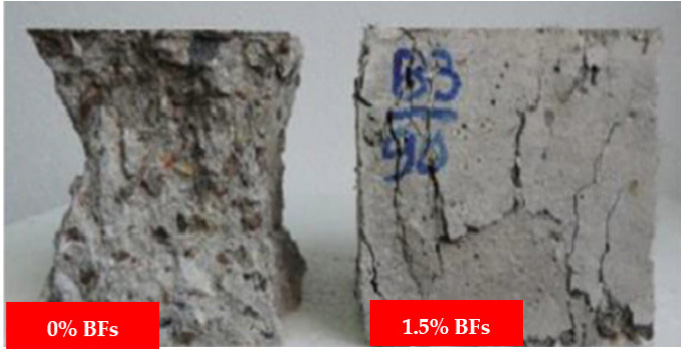
Available online under the Creative Commons Attribution (CC BY) license (https://creativecommons.org/licenses/by/4.0/) [32, 34].
Fiber-reinforced mortar (FRM) and fiber-reinforced concrete (FRC) have been two of the most frequently used materials for repairing aging concrete structures over the past three decades [35, 36]. The characteristics of FRM and FRC have been the subject of numerous studies. The addition of fibers improves the mechanical strength of mortar or concrete, especially in terms of splitting tensile strength and flexural strength, according to several earlier studies [37, 38]. Additionally, one of the most crucial conditions for a successful repair is the bond strength between the old substrate and the repair materials, which can be significantly improved using fibers in mortar or concrete [35, 39]. The toughness and flexural post-cracking behavior of the mixture are also significantly improved by adding fibers to mortar or concrete [40, 41]. Furthermore, the bridging effect of fibers reduces the number and width of cracks in mortar and concrete [42, 43]. More importantly, the addition of fibers increases the abrasion and freezing resistance of mortar or concrete [44, 45], two properties important for durability.
The performance of cementitious composites before cracking and especially after cracking is influenced by the number of fibers, the ratio of the elastic moduli of the fibers to the matrix, the ratio of the strength of the fibers to the matrix, the size of the fiber, and many other factors [46].
Basalt fiber is one of the most important environmentally friendly materials used these days to improve the performance of mortar and concrete. Basalt fibers come in two different sizes: macro basalt fibers and micro basalt fibers. However, macro basalt fibers are regarded as a novel material, and little is known about how they interact with cement mortars and other types of concrete [47, 48]. A composite material called chopped basalt fiber reinforced cement mortar is created by combining cement, water, and basalt fibers. The physicomechanical properties of the chopped basalt fiber-reinforced cement mortar are crucial in determining its suitability for different applications. These qualities must be properly balanced to make a material durable, long-lasting, workable, lightweight, and affordable.
Basalt fiber is an inorganic fiber with good corrosion resistance, high tensile strength, and low cost is basalt fiber. It is a brand-new type of reinforcing material that is used in cement mortar and has a consistent distribution, ratio, and percentage of fibers in various volume fractions.
There has been a great deal of experimental research on the behavior of fiber-reinforced mortar composites under static loads. These studies generally supported the effectiveness of fibers in terms of toughness and ductility at failure, as well as some tensile strength. A study [49] examined the flexural behavior of fiber-reinforced cementitious composites (FRCC) that contained two volume fraction contents and four different types of fibers, all of which were contained within an otherwise identical mortar matrix.
Recently, there has been a greater emphasis placed on experimental research into the behavior of composites made of fiber-reinforced mortar under dynamic loads, particularly impact loads. In terms of improved ductility and toughness compared to plain mortars, numerous researchers have confirmed the effectiveness of fiber-reinforced mortar composites.
A study [27] showed using an optimal proportion of wood ash (10%) with different volume content of coconut fibers (0.3%, 0.6%, 0.9%, 1.2%) in HPM. Experimental testing includes density, fc, ff, and impact strength according to ASTM C1018 and ASTM C1609. The results showed that the density of HPM decreased when using coconut fiber. Using 0.6% coconut fiber and 10% wood ash increases the fc and ff by approximately 15% and 30%, respectively. Additionally, the use of 0.9% palm fiber significantly increased the bending strength of HPM.
The addition of basalt fibers to cement-based materials significantly improves the performance of the raw material in engineering applications. Therefore, fiber-reinforced cement-based materials offer better engineering performance [49]. Basalt can increase the hardness of cement mortar, with short basalt fibers having the greatest effect [50]. Adding an appropriate amount of basalt fibers can greatly increase the structural strength of cement-based materials, and the improved tensile properties and strength of basalt fibers can greatly increase the tensile strength of concrete [51]. In addition, it is claimed that the addition of basalt fibers to cement mortar or cement concrete in a certain ratio can significantly increase the compressive and flexural strength of the materials [52, 53].
Basalt fibers and cement-based materials are widely used in artwork. In this context, the resistance of simple silicate solutions reinforced with basalt fibers to the unilateral salt freezing effect was systematically studied [54]. The mechanical strength, chloride ion diffusion properties, and microporous properties of cement mortars containing basalt fibers between 0 kg/m3 - 1.5 kg/m3 were tested under the influence of 0 to 40 freeze-thaw. The correlation of internal pore structure changes with mass loss, mechanical damage, and physical properties of materials due to salt freezing cycles was also analyzed. The results showed that a small amount of basalt fibers could significantly improve the mechanical properties and salt frost erosion resistance of cement mortar during unilateral salt freezing.
In a study [55], the mechanical and strength properties of polypropylene fiber-reinforced fresh mortar (PPFRM) and basalt fiber-reinforced mortar (BFRM) with different fiber contents were tested. Test results showed that the presence of polypropylene fibers (PP) and basalt fibers (BF) in solution reduced the initial sediment flux and increased the sediment flow rate. However, the adhesive strength and ff of fiber-reinforced mortar (FRM) were improved, and no obvious improvement in compressive strength was observed. Compared to the control solution, the bond strength of FRM and BFRM PP reinforced with fiber density 0.6 kg/m3, 1.6 kg/m3, and 2.6 kg/m3 increased by 16.60% to 28.80%, and 10.60% to 21.40%, respectively.
A research study [56] presented initial work with the application of BF in the field of reinforced cement composites. The effect of BF on mortar drying shrinkage, mechanical prosperities, and bond performance was studied. The results showed that adding BF reduced markedly dry shrinkage of mortar especially at early ages. BF mortar had a greater compressive and flexural strength during the early hydration period but had a little less strength at the age of 28 days than mortar without fiber. Four-point bending tests showed that the addition of BF effectively increased the toughness of mortar specimens at 28 days at the same loading but did not have a remarkable effect on fracture strength.
The exceptional rate of population growth and urbanization drive has greatly increased the demand for cement in the past few decades. The progress of scientific accomplishments in the last few decades, with such a rapid change in technologies and innovations, has initiated a global emphasis on cleaner and environment-friendly techniques in all fields. The significant increase in the production of cement results in an alarming level of release of CO2 into the atmosphere. One way of addressing this issue is to reduce the CO2 emission from the cement manufacturing process by replacing cement with locally available by-products [57] and using an environment-friendly reinforcement material. From the review conducted earlier, it was identified that most researchers conducted 0-50% wood-ash replacement of cement in mortar. However, this study needed to understand the properties of the mortar when partial or full replacement of cement with wood ash was above 50%; since the replacement was from 0%-100% and reinforcement of the mortar with basalt fiber was employed, it was necessary for the higher percentage replacement.
The growing need for the discovery and utilization of more sustainable, lightweight alternatives to conventional reinforcement materials, such as steel rebar and the lack of extensive research volume on basalt fiber as a new reinforcement material are important problems. In this case, in the quest for a sustainable material that can be used for the reinforcement of cement mortar, basalt fiber was introduced so that the production processes are not harmful to the environment. It was observed from the previous studies that there is very limited study on the use of micro basalt fiber in cement mortar reinforcement and no documented paper on cement-wood ash mortar reinforced with basalt fiber. This led to the necessity to examine the physicomechanical properties associated with cement mortar reinforced with micro basalt fibers in the form of chopped basalt fibers as well as the application of partial volume replacement of cement with wood ash to understand the best and appropriate application of such material in the construction industry.
2. METHODS
2.1. Experimental Materials
The objectives of this study were achieved by utilizing a series of materials needed for the cement mortar mixes. These materials are discussed below.
2.1.1. Cement
The type of cement used in this study as a binder was Dangote 3X, 42.5N Portland Cement at 1440 Kg/m3. The 3X stands for extra strong, extra life, and extra yield. This Portland cement used was bought from a Dangote dealer outlet in Ado-Ekiti, Nigeria. The chemical composition of the Dangote 3X Portland cement and the compared chemical composition of cement according to BS EN 197-1:2000 [58] are shown in Table 1.
2.1.2. Chopped Basalt Fiber
The chopped basalt fiber used in this study as the mortar reinforcement was bought from a seller known as EccoTexx company, Lipetsk, Russia, and is shown in Fig. (3).
The characteristics and properties of this basalt microfiber are shown in Table 2. The chemical composition of basalts depends on the deposit location and varies in wide ranges. The source of this basalt is Russia. It is not always possible to obtain fibers or products from stone with specific consumer characteristics [59].
CC | CaO | SiO2 | Fe2O3 | Al2O3 | MgO | K2O | SO3 | Na2O |
---|---|---|---|---|---|---|---|---|
% | Current study | |||||||
- | 61.20 | 18.12 | 2.73 | 4.91 | 1.93 | 0.14 | 1.39 | 0.41 |
BS EN 197-1:2000 [58] | ||||||||
58.67-63.90 | 17.46-21.59 | 1.21-3.76 | 3.29-6.14 | 0.61-3.30 | - | - | - |
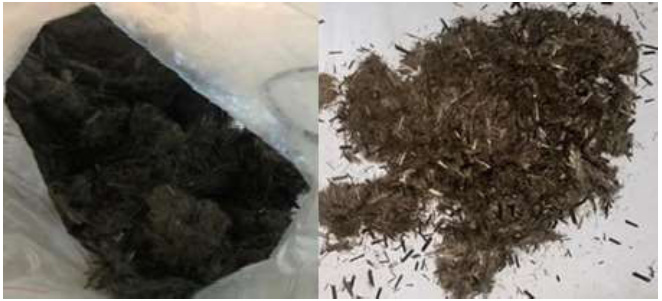
Length | 12 mm |
---|---|
Diameter | 24 micrometers |
Tensile strength | 3500 MPa |
Alkali resistance | High |
Modulus of elasticity | Not less than 70 GPa |
Elongation factor | 3.2% |
Melting temperature | 1450◦C |
Chemical composition | |
Constituents | Wt,% |
SiO2 | 43 - 58 |
Al2O3 | 11 - 20 |
CaO | 7 - 14 |
MgO | 4 - 14 |
FeO + Fe2O3 | 8 - 16 |
Na2O | 1 - 5 |
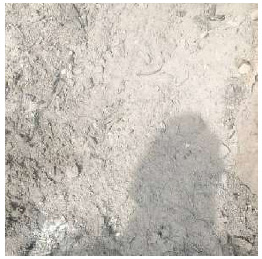
Constituent | Composition, % |
---|---|
SiO2 | 32.7 |
Al2O3 | 27.2 |
Fe2O3 | 2.85 |
MgO | 10.37 |
CaO | 12.11 |
NaO | 7.33 |
K2O | 12.03 |
LIO | 29 |
2.1.3. Wood Ash
Wood Ash (Fig. 4) is a term used to describe the waste product created when wood and wood products (chips, sawdust, bark, etc.) are burnt. It is the residue made up of both organic and inorganic components that remains after burning wood or unbleached wood fiber.
Ash is often produced in greater quantities by hardwoods than by softwoods, particularly by the bark and leaves of the tree as opposed to its interior woody portions. The typical quantity of ashes produced by burning wood is between 6 and 10%. The composition of wood ash can vary greatly depending on the environment and industrial activities [62]. The chemical composition of the wood ash used in this study is illustrated in Table 3. The wood ash used in this research was sourced from Afe Babalola University, Ado-Ekiti, Nigeria.
2.1.4. River Sand
The river sand with a 0.4-0.6 mm fraction was used in this research study as the fine aggregate at 1602 Kg/m3. The sand employed was sourced from Ado-Ekiti.
2.1.5. Superplasticizer
Superplasticizer was used as the water-reducing agent at 14.40 Kg/m3. The superplasticizer used was Sika visco-create 2000. It was obtained from Sika Manufacturing Nigeria. Sika ViscoFlow®-2000 (GB) is a liquid admixture for concrete based on unique polycarboxylate polymer technologies. Sika ViscoFlow®-2000 (GB) is designed as a high-range water reducer or superplasticizer. It is particularly suited for use in concretes that require low water/cement ratios and/or high-water reductions with excellent workability retention properties of up to 3 hours. Sika ViscoFlow®-2000 (GB) meets the requirements of BS EN 934-2 table [63].
2.2. Experimental Procedures
Mortar cubes and beam specimens were cast in metallic molds of dimensions 50 x 50 x 50 mm and 40 x40 x 160 mm respectively The specimens were cast with varying replacement percentages of cement (C) with wood ash (WA): 100%C + 0%WA, 80%C + 20%WA, 60%C + 40%WA, 40%C + 60%WA, 20%C + 80%WA, 0%C + 100%WA without basalt fiber reinforcement as control specimens. The same cement with wood ash percentage variations was prepared with chopped basalt fiber of 2.5% of the total cement-wood ash volume. Since the objective of this study was not to select or determine the optimal proportion of basalt fibers that would provide the highest strength, this proportion of 2.5% basalt fibers was selected in this study. This is because it falls within the optimum range for basalt fibers according to certain conditions. According to research, the optimal proportion of basalt fibers varies from 1% to 3% [64]. According to a study [65], fiber content varies but is generally approximately 3% to 7% of the cementitious material weight or 1% to 3% of total concrete or mortar weight. The length of the chopped basalt fiber was confirmed using a metal ruler. An electronic weighing scale was used to weigh the constituents of the mortar. A total of 12 (twelve) mix series were prepared (Table 4) in a concrete mix. The thoroughly prepared mortar mix was poured into the respective molds and compacted in two layers using a tamping rod to remove air bubbles and spaces that may adversely affect results. This was carried out in an orderly and coherent fashion to ensure even distribution, with the tamping rod pressure also being sufficient to achieve even distribution. About 32 strokes (4 rounds) of stamping per layer following (ASTM C109C 109M-08) [66] was done. After casting the mortar in their molds, the hardened samples were molded after 48 hours and cured in a curing tank for 7 and 28 days based on individual testing days. The mortar was prepared and cured at room temperature 22 ± 5°C. At 7- and 28-days age from casting, water absorption, flexural tests, and compressive tests of the specimens were conducted. This study employs the use of analytical and experimental procedures to arrive at results. A total of 144 cement-wood ash mortar cubes (72 cubes for water absorption and 72 for compressive strength test) and 72 cement-wood ash mortar rectangular prisms for flexural strength test were prepared. The compressive and flexural strength tests were conducted on the Matest Universal Testing Machine.
2.3. Experimental Tests
2.3.1. Water Absorption
Water absorption tests are usually used to ascertain the amount of water that has been absorbed by experimental samples under specific conditions. This water absorption test was conducted following BS 1881-122: 1983 [67]. Mortar cubes of 50 x 50 x 50 mm were employed, and the test was carried out at 28 days. The water absorption rate value was calculated using Eq. (1).
![]() |
(1) |
Where Ar is the absorption rate in % of the mortar; M1 is the dry weight of the mortar in kg; M2 wet weight of the mortar in kg.
2.3.2. Mechanical Properties
The compressive and flexural strength of the mortar specimens were tested on days 7 and 28 of curing. This experiment was conducted following BS EN 196-1:1995 [68].
3. RESULTS AND DISCUSSION
3.1. Water Absorption Test Results
The water absorption results of all the samples, with their average results taken at each experimental run, are illustrated in Table 5 and Fig. (5).
Mortar Mix Variation Identify | Mortar Mix Variation |
---|---|
A1 | 100%C + 0%WA |
A2 | 80%C + 20%WA |
A3 | 60%C + 40%WA |
A4 | 40%C + 60%WA |
A5 | 20%C + 80%WA |
A6 | 0%C + 100%WA |
B1 | 100%C + 0%WA+ BF |
B2 | 80%C + 20%WA + BF |
B3 | 60%C + 40%WA + BF |
B4 | 40%C + 60%WA + BF |
B5 | 20%C + 80%WA + BF |
B6 | 0%C +100%WA + BF |
Mortar Mix Variation Identities | Sample 1 | Sample 2 | Sample 3 | Average |
---|---|---|---|---|
A1 | 9.67 | 9.32 | 8.08 | 9.02 |
A2 | 4.84 | 5.44 | 5.25 | 5.14 |
A3 | 2.02 | 2.82 | 3.02 | 2.62 |
A4 | 4.22 | 5.42 | 5.42 | 5.02 |
A5 | 4.17 | 4.17 | 4.17 | 4.17 |
B1 | 8.71 | 8.51 | 8.31 | 8.51 |
B2 | 6.35 | 4.7 | 5 | 5.35 |
B3 | 4.34 | 6.04 | 5.64 | 5.34 |
B4 | 11.68 | 9.29 | 11.07 | 10.68 |
B5 | 6.76 | 6.56 | 6.36 | 6.56 |
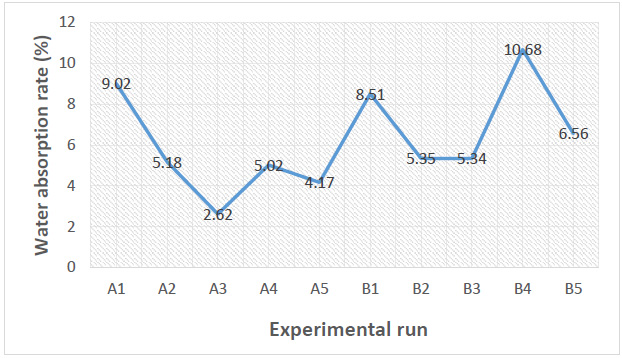
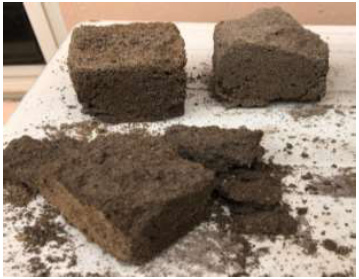
Mortar Mix Variation Identities | Sample 1 | Sample 2 | Sample 3 | Average |
---|---|---|---|---|
A1 | 10.09 | 11.06 | 10.58 | 10.58 |
A2 | 17.08 | 17.38 | 17.38 | 17.28 |
A3 | 17.06 | 17.42 | 17.54 | 17.34 |
A4 | 6.1 | 6.4 | 6.1 | 6.2 |
A5 | 1.1 | 1.8 | 1.9 | 1.6 |
B1 | 15.9 | 16.9 | 16.4 | 16.4 |
B2 | 15.69 | 15.69 | 15.69 | 15.69 |
B3 | 7.27 | 7.01 | 8.29 | 7.52 |
B4 | 4.02 | 4.54 | 3.5 | 4.02 |
B5 | 2.54 | 2.65 | 2.43 | 2.54 |
On average, the total water absorption of the mortar is between 4.17% to 10.68%. The basalt fiber reinforced mortar specimen with a 60% volume replacement of wood ash (B4) shows the highest water absorption rate. The possibility for higher absorption may be a result of the increased hydration demand due to the presence of wood ash. An increase in the amount of wood ash in mortar results in a decrease in its water absorption ability. This is because, when cured, cement particles serve as filler, while ash from wood waste is much smaller than cement particles. Due to their smaller size than cement particles, these particles occupy the empty area created by cement and sand particles [24, 25]. The amount of water that hardened mortar can absorb decreases as the percentage of wood ash increases because the matrix becomes more compacted. The incorporation of chopped basalt fiber increases the pores in the mortar. The pores are reduced by the wood ash, which is finer than the cement. Samples A6 and B6 failed at the demolding stage (Fig. 6) and, as a result, could not be tested.
3.2. Compressive Strength Test Results
The results of the compressive strength (fc) test carried out at different percentages of replacement of cement with wood ash at different ages of 7 and 28 days as well as reinforced with chopped basalt fiber are presented in Tables 6 and 7, while the average of the samples at each mix results are illustrated in Fig. (7). An average of three mortar cubes was taken to obtain the average weight of the cubes for the compressive test per experimental run.
After 7 days, it was observed that experimental run A3, containing 40% volume replacement of wood and no basalt fiber reinforcement exhibited the highest fc at 16.40N/mm2, while A5, containing 80% volume replacement of cement with wood ash, exhibited the least fc. In comparison with the control sample A1 (at 7 days), it can be seen that partial replacement of cement with wood ash (in the range of 20% to 40%) in the absence of any chopped basalt reinforcement increased the fc of mortar steadily, after which increased percentages of partial replacement of cement with wood ash led to very sharp drops in the fc of mortar.
In respect to samples B1 to B5 containing basalt reinforcement, after 7 days, when compared to the unreinforced samples A1 to A5 containing identical percentage replacement of cement with wood ash, increases in fc were only noticed in B1 and B5. Basalt fiber reinforcement was seen to cause a significant drop in fc for A3 and a slight decline in compressive strength for A2 and A4.
Mortar Mix Variation Identities | Sample 1 | Sample 2 | Sample 3 | Average |
---|---|---|---|---|
A1 | 10.09 | 10.66 | 10.72 | 10.49 |
A2 | 9.34 | 9.94 | 9.64 | 9.64 |
A3 | 19.05 | 19.2 | 19.35 | 19.2 |
A4 | 6.44 | 7.02 | 7.52 | 6.99 |
A5 | 2.06 | 3.06 | 1.06 | 2.06 |
B1 | 20.88 | 21.78 | 22.08 | 21.58 |
B2 | 7.28 | 8.87 | 11.69 | 9.28 |
B3 | 13.8 | 13.92 | 14.04 | 13.92 |
B4 | 3.99 | 5.23 | 6.47 | 5.23 |
B5 | 2.87 | 4.42 | 3.3 | 3.53 |
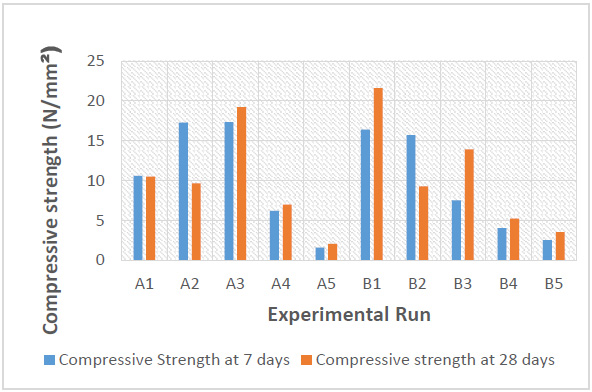
After 28 days, however, samples A1 and A2, containing 0% and 20% replacement of cement with wood ash, experienced a drop in fc, which is in line with a previous study [24], which may be attributed to an increase in moisture absorption. A3, A4, and A5 contrarily experienced slight increases in fc. Compared to the same samples (A1 to A5) after 7 days of curing, A3 (60% cement and 40% wood ash) still exhibited the highest fc.
Although basalt fiber reinforcement led to a decrease in fcfor A3 and A4, as seen in B3 and B4 after 28 days, the overall sample with the highest obtained fc was B1 (chopped basalt fiber reinforced mortar containing 0 percent replacement of cement with wood ash), while slight increases in fc were observed in B2 and B5 with basalt reinforcement. After 28 days, all basalt-reinforced samples (B samples) exhibited an increase in fc in comparison to 7 days except B2, which exhibited a very slight decrease. The fc results of all mortar cubes without basalt fiber were in correspondence with a previous study [26].
3.3. Flexural Strength Test Results
The flexural strength (ff) results of the samples are presented in Tables 8 and 9 for curing days of 28 and 7, respectively.
From the ff results of the mortar shown in Fig. (8), it is seen that at the age of 7 days and 28 days, it is observed that the experimental run B1 (chopped basalt fiber reinforced mortar beams containing 0% volume replacement of cement with wood ash) exhibited the highest ff of 6.54 N/mm2 and 6.77 N/mm2 respectively. An increase in the percentages of wood ash as a partial replacement of cement in mortar caused an increase in the ff of the mortar at days 7 and 28 for the mix variation A2, which is confirmed in the study [27]. This indicates that the percentage increase of wood ash must not exceed a certain amount to avoid depletion of the ff of the mortar.
Mortar Mix Variation Identities | Sample 1 | Sample 2 | Sample 3 | Average |
---|---|---|---|---|
A1 | 0.99 | 1.3 | 1.22 | 1.17 |
A2 | 1.99 | 3.2 | 3.54 | 2.91 |
A3 | 1.54 | 0.99 | 1.82 | 1.45 |
A4 | 0.81 | 1.13 | 1.15 | 1.03 |
A5 | 0.55 | 0.55 | 0.55 | 0.55 |
B1 | 7.33 | 5.87 | 7.11 | 6.77 |
B2 | 3.6 | 4.2 | 3.9 | 3.9 |
B3 | 2.75 | 2.95 | 2.82 | 2.84 |
B4 | 1.29 | 1.29 | 1.29 | 1.29 |
B5 | 0.7 | 0.15 | 0.32 | 0.39 |
Mortar Mix Variation Identities | Sample 1 | Sample 2 | Sample 3 | Average |
---|---|---|---|---|
A1 | 0.83 | 1.34 | 1.25 | 1.14 |
A2 | 2.34 | 2.29 | 2.32 | 2.32 |
A3 | 0.69 | 0.74 | 0.64 | 0.69 |
A4 | 0.54 | 1.38 | 1.02 | 0.98 |
A5 | 0.18 | 0.24 | 0.18 | 0.2 |
B1 | 6.33 | 6.81 | 6.48 | 6.54 |
B2 | 1.89 | 1.89 | 1.89 | 1.89 |
B3 | 2.88 | 2.83 | 0.92 | 2.21 |
B4 | 1.02 | 1.13 | 0.91 | 1.02 |
B5 | 0.22 | 0.28 | 0.28 | 0.26 |
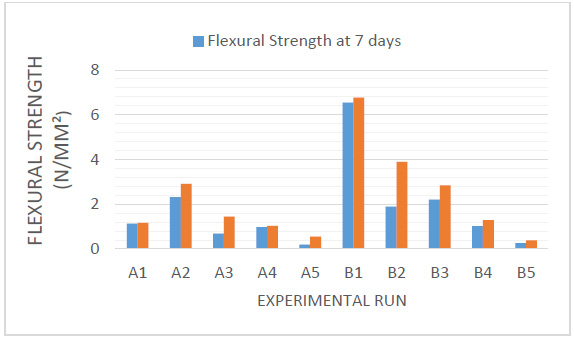
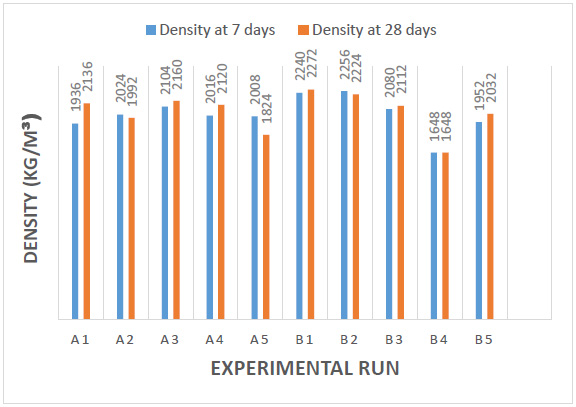
These results show that basalt fiber reinforcement improved the ff of the mortar at 28 days for B1-B4, whereas the ff from experimental runs, A1-A4 improved when chopped basalt fiber reinforcement was added. This supports the findings of previous studies [37, 38].
It is important to note that among the experimental runs (A1-A5) that are void of basalt fiber reinforcement, A2 produced the highest ff at both 7 and 28 days of age and can be considered the optimum percentage replacement ratio for flexural properties. Whereas B1 produced the highest ff among the mix variations bearing chopped basalt fiber. From the results in Fig. (8), it is seen that the ff decreased at B5 on day 28 with the addition of chopped BF whereas on day 7, the ff >of all chopped basalt fiber-reinforced samples, flexural strength A2 and B2 decreased.
Failure of the beams containing basalt fiber was seen to be gradual, and the specimen did not completely break apart at failure loads, attesting to the particle binding properties of basalt fiber. For the unreinforced samples, however, the failure was quick, and the mortar beam samples rapidly snapped into two pieces.
3.4. Density Test Result
From the set of values obtained from the weighed mortar specimens, the results are illustrated in Fig. (9). It can be seen that the experimental run B1, containing 20 percent partial replacement of cement with ash and in the presence of basalt fiber reinforcement, exhibited the highest density of 2272kg/m3 at 28 days of age. The lowest density, on the other hand, was exhibited by sample A5 at 28 days of age, containing 80 percent partial replacement of cement with wood ash. Sample A5 showed a density of 1824 kg/ m3, and this confirmed the findings of another study [27].
On average, it can be observed that both basalt reinforcement and age contributed to an average increase in the density of the samples. Higher percentages of partial replacement with wood ash understandably contribute to a reduction in density as wood ash is a lighter material than cement.
CONCLUSION
From the steps taken and the data derived, the following conclusions are drawn:
a. The average water absorption rate increased with chopped basalt fiber reinforcement due to an apparent increase in porosity with the highest percentage being 10.64% for experimental run B4 containing 60% replacement of cement with wood ash and the presence of basalt reinforcement.
b. The average compressive strength (fc) of all mixes apart from A2 and B2 increased with the age of the sample, with run B1 at age 28 days producing the highest fc of 21.58 N/mm2, indicating that chopped basalt fiber increases the fc of mortar and the lowest fc was run A5, exhibiting a strength of 2.06 N/mm2.
c. At 7 days of age, the fc of the unreinforced A2 and A3 containing 20% and 40% replacement of cement with ash showed higher fc than A1 containing no replacement, although the strengths of these mixes (A2 and A3) showed negative responses with reinforcement and exposure to water, indicating that the optimum range for partial replacement of cement with ash is 20%-40% under minimal water exposure and known granular interaction with reinforcement material.
d. For runs A6 and B6 containing total replacement of cement with wood ash, samples failed at demoulding, indicating that wood ash is not a suitable direct substitute for cement in construction.
e. The flexural strength (ff) of the beam samples also increased with age. Experimental run B1, containing no replacement of cement and containing 2.5% basalt reinforcement, showed the highest ff of 6.77N/mm2 at 28 days of age and is, therefore, the optimum mix. This also indicates that chopped basalt fiber reinforcement improves the flexural properties of mortar.
f. A2 and A3, however, showed ff higher than A1 at 7 days, indicating that 20-40% replacement of cement with ash is optimum. A3, however, showed a negative response with the addition of basalt fiber and with longer exposure to water.
g. The addition of basalt fiber to mortar increased its compressive and flexural capacities.
h. The density of the mortar was affected by the partial replacement of cement with wood ash and the incorporation of micro basalt fiber in the mortar.
Thus, this type of mortar is recommended to be used in plastering walls or for flooring to improve the properties of the concrete structural members. Furthermore, this can also be used in concrete repairs.
LIST OF ABBREVIATIONS
OPC | = Ordinary Portland Cement |
BF | = Basalt Fiber |
SEM | = Scanning Electron Microscope |
FRM | = Fiber-reinforced Mortar |
FRC | = Fiber-reinforced Concrete |
AVAILABILITY OF DATA AND MATERIALS
The data and supportive information are available within the article.
ACKNOWLEDGEMENTS
Declared none.