All published articles of this journal are available on ScienceDirect.
The Effect of Hybrid Fibers Reinforcement on the Mechanical and Physical Properties of Concrete
Abstract
Background:
Hybrid fiber reinforced concrete is the use of two or more than two fiber textures in a single concrete matrix to improve the overall properties of concrete.
Materials and Methods:
In this study, the ductility of medium strength concrete was observed to improve by incorporating steel and polypropylene in a ratio of 50:50 as a hybrid fiber. Four proportions of Volume fractions (Vf) were used (0.25, 0.5, 0.75, 1%). The changes in the mechanical properties and density occurred due to the addition of these hybrid fibers.
Results:
The features examined include bulk density, compressive strength, and flexural strength by using thirteen concrete mixtures with various volume fractions of steel and polypropylene fibers.
Discussion:
The results showed a significant increase in compressive and flexural strength due to the addition of steel fibers. On the other hand, polypropylene fibers exhibited minor changes in the mechanical properties of hardened concrete exclusively in the mixtures made with both steel and polypropylene fibers in which the strength increased in comparison to plain concrete by 4.4% and to steel fiber group having the optimal strength and other properties.
Conclusion:
These remarks provide a clear view of the importance of using different fiber reinforcing systems to improve the mechanical performance of concrete, which is considered quasi-brittle.
1. INTRODUCTION
Fibers Reinforced Concrete (FRC) is generally defined as composites with two main components, the fiber and the matrix, as the cementitious matrix may itself be considered a composite with several parts. The fiber exemplifies the 2nd main component. The fiber texture assumed to be discontinuous and stated with random positioned and dispersed in the bulk of the concrete composites. Together the fiber texture and the matrix inferred to work by bonding and provide the synergism needed to make a useful composite. The matrix form, whether it is a paste, mortar, or concrete, is assumed to contain all the aggregates and additives specified. Air voids entrapped in the matrix during mixing are supposed to be part of the matrix form [1]. Hybrid fiber reinforced concrete is the use of two or more than two fiber textures in a single concrete matrix to improve the overall properties of concrete. In well-designed hybrid composites, there is a positive collaboration between fiber textures and the hybrid performance, exceeding the sum of individual fiber performances. Hybrid Fiber Reinforced Concrete (HFRC) is a mixture of different fiber types that vary in material characteristics, continue bonded as one when inserted in concrete, and retain their identities and properties. The process of fibers hybridization provides improved specific or synergistic features not obtainable by any of the original fiber texture acting alone. Until today mainly, three types of hybrid composites have been used by the researchers using the combinations of polypropylene-carbon, carbon-steel, and steel- polypropylene fibers [2].
2. LITERATURE SURVEY
Nikbakht et. al. investigated the shear and flexural performance of HPSCC beams with no coarse aggregate and compressive strength over 100 MPa. The effect of different forms of steel fiber on the mechanical characteristics and failure forms of reinforced HPSCC beams has been studied. The results showed that the influence of the type of steel fiber is more significant than the influence of the longitudinal strengthening ratio. Furthermore, the ultimate load and deformation amount of HPSCC beams increased noticeably for the beam samples with steel fiber [3]. Khed et al. studied the optimization by exploiting response surface methodology (RSM) for the pull-out strength employing partial substitute of crumb rubber with the sand along with the integration of hybrid fibers for example PVA (Polyvinyl alcohol) and tire wire in Engineered Cementitious Composites (ECC). The crumb rubber in ECC formed the lower pullout strength but ensured the homogeneous distribution of fibers. As a result, the hybrid fiber mixture did not influence the pull-out strength both positively or negatively. RSM assisted in improving the constituents in the ECC to attain better performance of the ECC material. RSM optimized results using ANOVA (Analysis of variance) were experimentally proved and less than 5% of the variance in the results was observed with the desirability of 1 [4].
Teng et al. investigated the flexural performance and durability characteristics of high-performance hybrid fiber reinforced concrete. In the Fiber Reinforced Concrete (FRC) mixtures, Silica Fume (SF) is present. Furthermore, Ground Granulated Blast Furnace Slag (GGBS) was used as a mineral additive in proportions (10% and 30%) of cement weight. Double Hooked end steel and single Hooked End (HE) steel fibers, and Polyvinyl Alcohol (PVA) fibers mixed in various proportions in concrete were used to prepare hybrid FRC. The total volume fractions of fibers combined were 0%, 0.6%, and 1.2%. Many tests to obtain compressive strengths, flexural behavior, rapid chloride migration coefficients, and electrical resistivity tests were conducted. The results indicated that mineral additives and especially silica fume have a significant effect on concrete durability properties. A highly durable concrete was obtained by the continuous addition of SF and GGBS to concrete. Results also showed that the incorporation of fiber improved the mechanical strength of the concrete notably. The post cracking flexural resistance and toughness of FRC can be increased effectively by the insertion of 1.2% (DHE) steel fibers, indicating that the DHE steel fibers substitution by HE steel or PVA fibers resulted in flexural performance reduction of hybrid (FRC). Also, a higher diffusivity of chloride in FRC was observed, while there was a lower electrical resistivity of FRC rather than mixtures without fibers. J. Novák et al. investigated the concrete behavior under ambient temperature and elevated temperature up to 400 15°C and 600 °C. The test of the split tension and compression was carried out on 150 mm cubes. According to the results, residual and peak strengths of the material were specified for a variety of degrees of temperature. The results have contributed to the enhancement of knowledge in the area of the two concrete structures, which can be exposed to high degrees of heat and fiber reinforced concrete’s structural behaviors. The structural design case of the concrete structures with high fire loading risks was also used [5]. M. Ali et al. studied the behavior of new hybrid fiber-reinforced concrete composites, which incorporated short arbitrarily dispersed shape memory alloy (HECC-SMAF) and PVA fibers investigated with the use of the impact test of the drop weight. The results indicated that the SMA fibers considerably improved tensile and impact performances of Engineered Cement Concrete. The addition of fibers over a specific dose resulted in the clustering of the fibers, which is why no additional gain in tensile and impact performance was detected. The HECC-SMAF specimens’ impact resistance was additionally enhanced when exposed to heat treatment. This study presented new composites of the cement having superior tensile characteristics and impact resistances for protecting the critical infrastructures in case of explosions or impact loads [6]. Alberti et al. studied the self-compacting polyolefin fiber reinforced concrete’s fracture behavior. The post-cracking practices provide high residual strength values, particularly for the large deformation types. For the small deformations, the residual flexural strength can be improved by small amounts of the steel-hooked fibers, obtaining HFRC, which is suitable for the structural uses. The study has shown two synergies (with two fiber types that work together in the processes of fracture) and enhancement of fibers distribution and orientation on the surface of the fracture [7]. Mohankar et al. studied the mechanical efficiency of the Hybrid Fiber Reinforced Concrete (HFRC) by using steel and polypropylene fibers in different proportions (0.25%, 0.5%, 0.75%, and 1%). Adding small, evenly dispersed, and narrowly spaced fibers to the concrete would play the role of the crack resistor and would considerably enhance its characteristics [8]. W. Song et al. investigated the compressive strength and the impact toughness of the steel fiber reinforced concrete (SFRC), HFRC, and CFRC at a volume fraction of the carbon fiber 0.10%, 0.20%, 0.30% and steel fiber of 0.50%, 1.0%, 1.50%. Results have shown the fact that adding carbon and steel fibers might increase compressive strength. CF, SF and hybridizing between them might considerably enhance compressive strength. Impact test results have shown the fact that by increasing the fiber volume, the impact number of the 1st visible crack and ultimate failure also increase [9].
3. MATERIALS AND METHODS
3.1. Materials
3.1.1. Portland Cement
(Tasluja) cement type (I), according to I.Q.S No. 5/1984 [10] standards, has been functional in all concrete content mixes. The physical and chemical properties of cement are given in Tables 1 and 2.
No. | Compound Composition | Chemical Composition | Percentage by Weight | Limit of Iraqi Specifications No.5,1984) |
---|---|---|---|---|
1 | Lime | CaO | 63.11 | - |
2 | Silica | SiO2 | 20.37 | - |
3 | Alumina | Al2O3 | 5.15 | - |
4 | Iron oxide | Fe2O3 | 4.39 | - |
5 | Sulfite | SO3 | 2.57 | 2.8 (max) |
6 | Magnesia | MgO | 1.68 | 5 (max) |
7 | Loss on ignition | - | 2.72 | 4 (max) |
Total | - | - | 99.99 | |
8 | Insoluble residue | - | 0.69 | 1.5 (max) |
9 | Lime saturation factor |
- | 0.92 | 0.66‒1.02 |
10 | Tricalcium silicate | C3S | 49.23 | - |
11 | Dicalcium silicate | C2S | 21.5 | - |
12 | Tricalcium aluminate | C3A | 6.22 | - |
13 | Tetra calcium alumina ferrite |
C4AF | 13.34 | - |
Physical Properties | Test Results |
Limit of Iraqi Specifications No.5,1984 |
---|---|---|
Specific surface area (Blaine method) m2/kg |
442.6 | 2300 (min) |
Setting time (vicats method) Initial setting, hrs: min Final setting, hrs: min |
1:30 (hr:min) 5:00 (hr:min) |
45 (min) 10 (max) |
Compressive strength of mortar, (MPa) 3-day 7-day |
24 32 |
15 (min) 23 (min) |
3.1.2. Fine Aggregate
Usual sand of zone 3 applied as fine aggregate in the presented study that fulfills the I.Q.S No.45/1984 [12] standards (Fig. 1). Examined physical properties are given in Table 3.
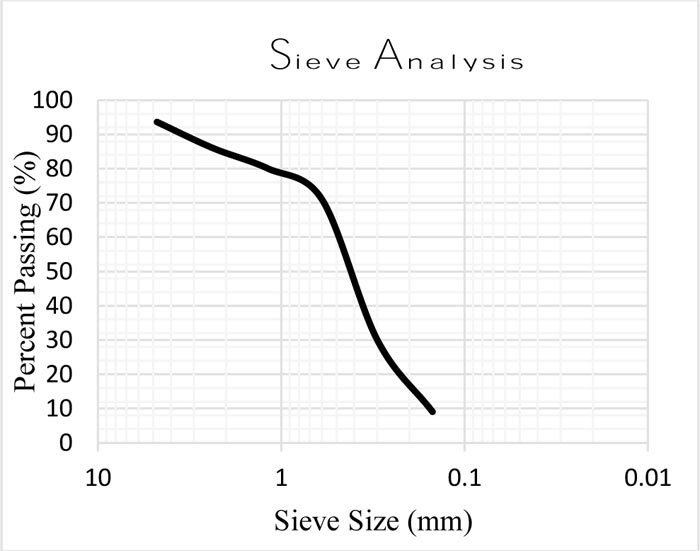
Physical Properties |
Test Result | Limits of Iraqi Specification No.45,1984 |
---|---|---|
Specific gravity | 2.53 | - |
Apparent density | 2.7 | - |
Sulfate content | 3.56 | specification requirements ≤ 0.5% (max) |
Absorption | 2.25 | - |
Physical Properties | Test Results | Limits of Iraqi Specification No.45,1984 |
---|---|---|
Specific gravity | 2.3 | - |
Absorption | 6.2 | - |
SO3 Content | 0.09 | specification requirements ≤ 0.1% (max) |
3.1.3. Coarse Aggregate
A crushed river grit of a maximum size range (5-12mm) was operated as coarse aggregate. The coarse aggregate was listed according to Iraqi requirement No.45/1984 [12] standards. Examined features are provided in Table 4.
3.1.4. Water
In this study, ordinary tap water was used in all concrete mixes and the specimen’s curing.
3.1.5. Superplasticizer
Superplasticizer, commercially called Master Glenium 51 superplasticizer, was used. It reduces the ratio of water to cement to increase the mechanical properties and workability of concrete; also, it fulfills the ASTM C 494 type F. The features of the admixture as specified through the manufacturer (BASF Company) are provided in Table 5.
3.1.6. Steel Fibers
Hooked end fibers were used, employing volume fractions of 0.125, 0.25, 0.375, 0.5%, obtained from “Sika Company” (Iraq). Table 6 represents the SF technical characteristics instructed by the instruction of the producer company. Fig. (2) displays the Hooked steel fiber.
Structure of the Material | Polycarboxylic Ether-based |
---|---|
Color | Amber |
Density | 1.082 - 1.142 (kg/liter) |
Chlorine Content% (EN 480-10) | < 0.1 |
Alkaline Content% (EN 480-12) | < 3 |
Description | Hooked end |
---|---|
Density | 7860 (kg/m3) |
Ultimate strength | 1180 (MPa) |
Length | 50 (mm) |
Diameter | 0.75 (mm) |
Aspect ratio | 60 |
Modules of elasticity | 2×105 (MPa) |
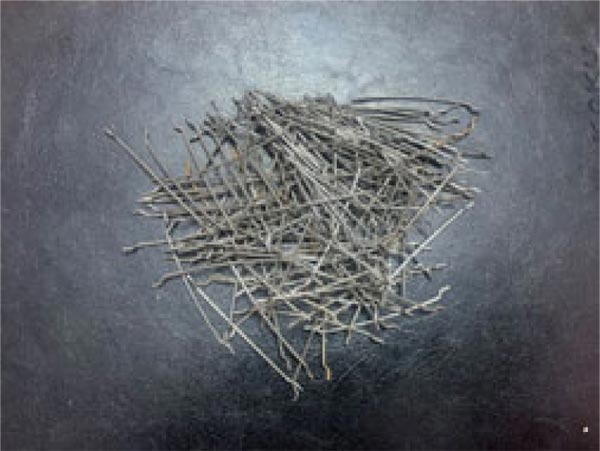
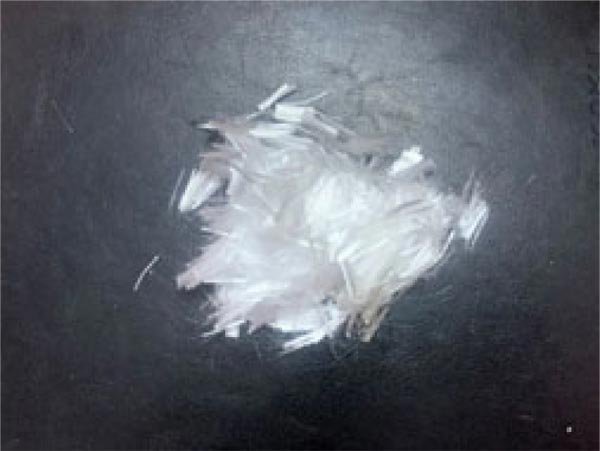
Property | Specification |
---|---|
Chemical Base | % 100 Polypropylene |
Reaction with water | Hydrophobic |
Water Absorption | Nil |
Tensile Strength | 300 – 400 (N/mm2) |
Density | 0,91 (g/cm3) |
Length | 12 (mm) |
Diameter | 18 (microns) |
Aspect ratio | 80 |
Modules of elasticity | 4000 mm2) |
3.1.7. Polypropylene
Sika fibers, as a monofilament, were applied in this study with volume fraction (0.125%, 0.25%, 0.375%, 0.5%). Polypropylene was exploited for lessening and controlling plastic shrinkage cracks through raising the fresh concrete strain capacity. Table 7 indicates the technical belongings of the polypropylene fiber based on the manufacturing company. Fig. (3) shows the polypropylene fiber.
3.2. Mix Design Proportions
All trials conducted between April 2019 - Oct 2019, at room temperature, are presented in Tables 8 and 9.
No. | Item | Kg/M3 |
---|---|---|
1 | Cement | 565 |
2 | Fine Aggregate | 777 |
3 | Coarse aggregates | 1225 |
4 | Water | 158 |
5 | Super Plasticizer | 7.9 |
No. | Mix | Steel Fiber % | Polypropylene fiber % |
---|---|---|---|
1 | P.C. | - | - |
2 | SF | 0.25 | - |
3 | 0.5 | - | |
4 | 0.75 | - | |
5 | 1 | - | |
6 | PP | - | 0.25 |
7 | - | 0.5 | |
8 | - | 0.75 | |
9 | - | 1 | |
10 | H. SF. PP | 0.125 | 0.125 |
11 | 0.25 | 0.25 | |
12 | 0.375 | 0.375 | |
13 | 0.5 | 0.5 |
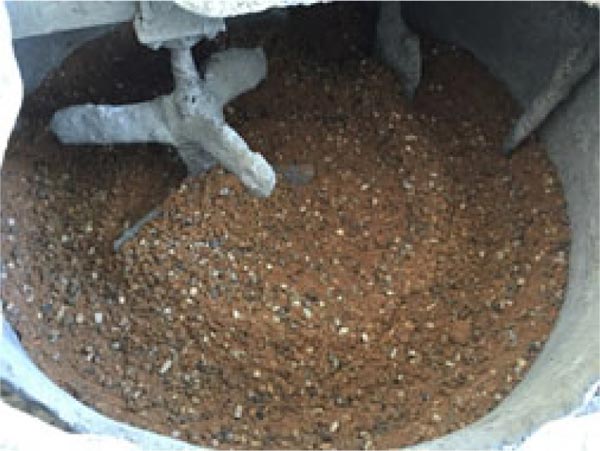
Concrete mixes were created based on the technique of British Standards B.S1881: part 125 1986 [17]. All the mixes established were treated for 28 days. After many tryouts, a reference mix proportion was employed in the study. Firstly, dry elements (aggregate, sand, and cement) were mixed for 1min to 3mins in a pan mixer of the capacity 0.1m3, as shown in Fig. (4). The mixer's inner surface was cleaned and soaked before the insertion of materials; after that, the amounts of the water/admixture were supplemented and the whole mix of ingredients was exposed to mixing for more than a minute. Then, it was blended with different volume fractions of polypropylene or steel fiber was gradually inserted to run the pan mixer for (1) minute merely; over mixing was evaded to avoid balling complications, which can lead to fiber damage and loss of strength.
3.3. Casting and Curing
The blends were transferred into 3 cube molds of dimension 150x150x150 mm and 9 prism molds of dimension 10x10x50 mm in 2 or 3 layers for each mix; each one of these layers was shaken through a vibrating table for 10 to 15 seconds until there were no air bubbles in concrete’s surface. All molds were extensively lubricated before forming to gain fair face for the cast and to effortlessly demolding the samples. The sample's face was flattened via hand trawling and marked after that. The samples were cured under laboratory condition temperature (25˚C) in a large water tank for testing.
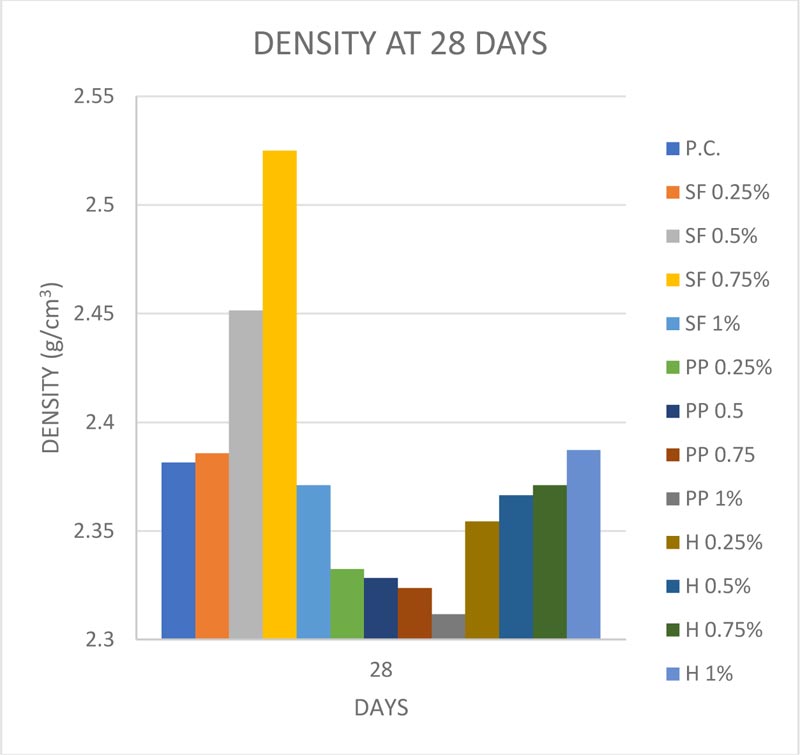
4. RESULTS AND DISCUSSION
4.1. Bulk Density Measurement
According to the British Standards B.S. 1881 (1983), the density of the cebes was measured. Figs. (5) and (6) indicate the results of the density measurement of each concrete mix of the three groups at 28 days curing time as follows:
Fig. (5) shows an increase in the density of the SFRC from 0.1% at 0.25% Vf to 6% increase at 0.75% Vf in steel fiber reinforced concrete (SFRC) group due to the excellent bonding of steel fibers with the concrete matrix. The density reduced at 1% Vf due to the accumulation of the steel fibers as the workability declines with the increase of volume fraction, which drops the compaction of the cubes, and that initiates voids of entrapped air. Note that the excessive compaction of the cubes can make the steel fiber to settle at the bottom of the cube. For the PFRC group, results show a 3% reduction less than regular concrete as volume fraction Vf increases because of the less bonding between fibers and concrete. Also, the low weight of polypropylene fibers causes loss in concrete’s density [18].
Concerning HFRC (50:50) %, the measurement shows higher density values than the polypropylene fibers group by 1% to 2% as volume fraction increases but still remains less than the steel fiber group.
4.2. Compressive Strength Test
A compressive strength test has been specified based on B.S. 1881: part 116(1989) with the use of the digital compressive machine. The test has been carried out at ages (7, 14 as well as 28 days); average regarding three cubes have been adopted. The results show a compressive strength increment for the SFRC group which increases from 113.2% at 0.25% Vf to 125.84% 0.75% Vf. A higher bond of fibers and concrete enhances the concrete density. Also, the w/c ratio reduction improves compressive strength. Figs. (7) and (8) show compressive strength. For 1% Vf of steel fiber, concrete endured failure as the density reduction caused by the higher steel fiber Vf tends to cause air cavities that decrease the density as mentioned before. The cavities tend to weaken the cube since it works as a crack starter and the stress concentrates in these voids.
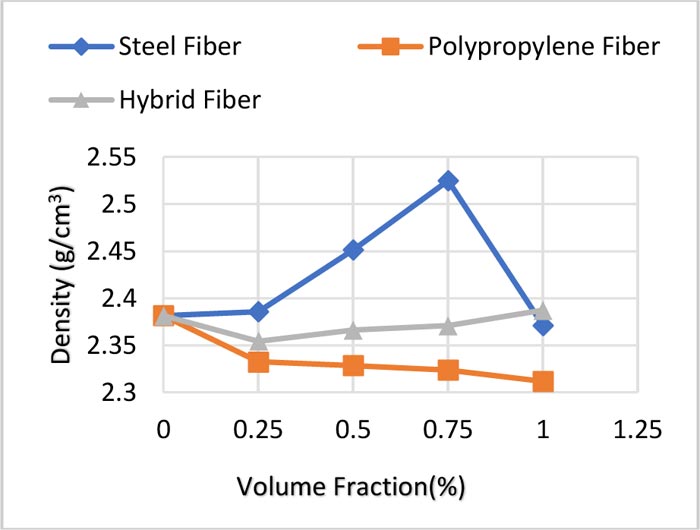
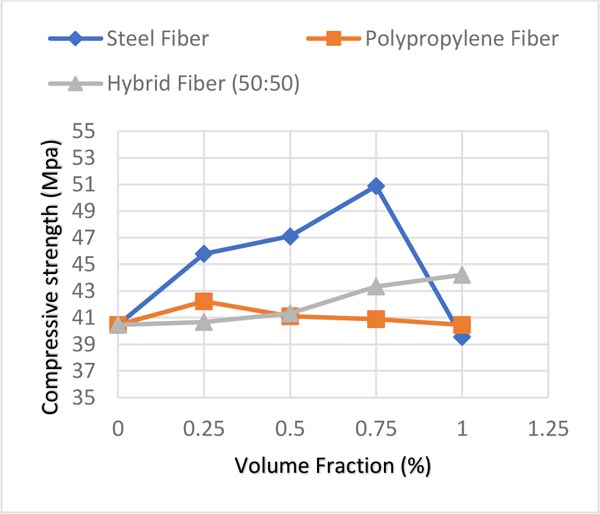
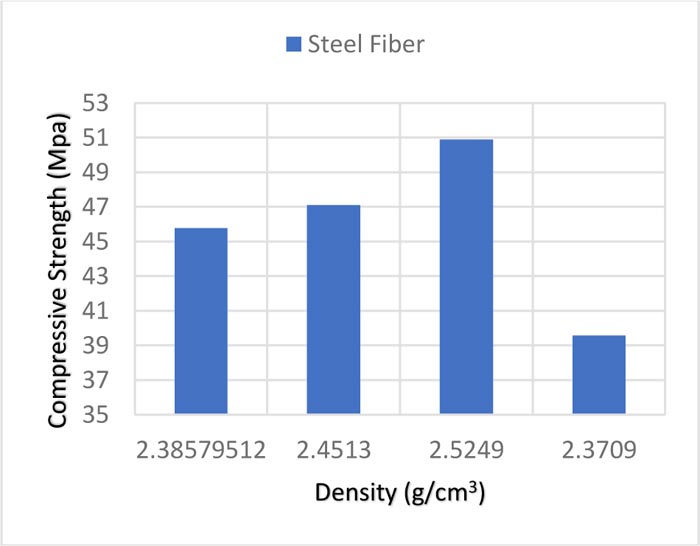
For the Polypropylene Fibers Reinforced Concrete (PFRC) group, as shown in Figs. (7) and (9), the strength increased in comparison to plain concrete by 4.4%. However, as fiber’s volume fraction increased, PFRC suffered a decrease in strength as the Vf increased equally as the strength of plain concrete and reduction was due to the less bonding of the polypropylene because its elastic modulus was much lower than the matrix itself.
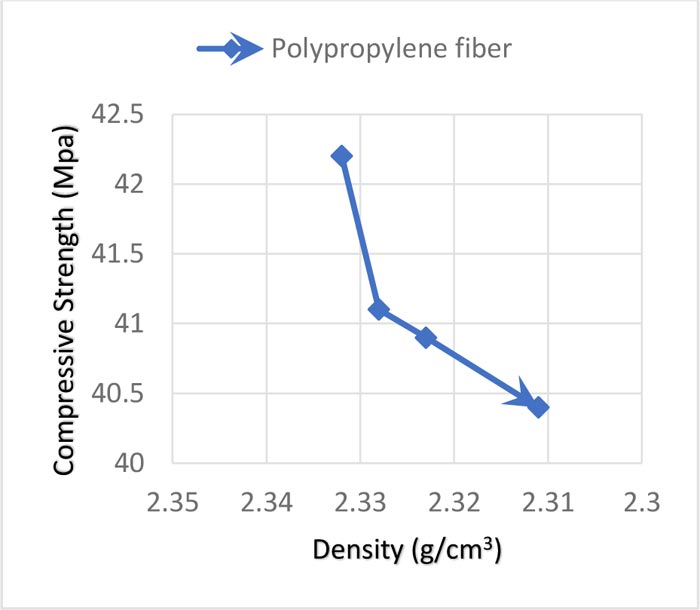
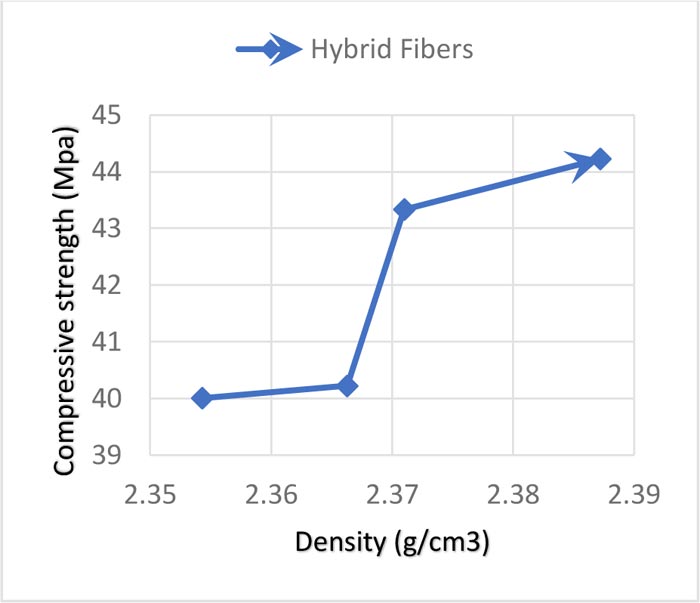
The hybrid fiber reinforced concrete (HFRC) group with 50:50% is presented in Figs. (7) and (10). The strength at 0.25% Vf was less than the two groups mentioned before due to the presence of polypropylene fiber of low modulus of elasticity causing the reduction of the strength. As the volume fraction increases, the strength increases almost linearly. Figs. (11-13) show the failing pattern of cubes in the compression test.
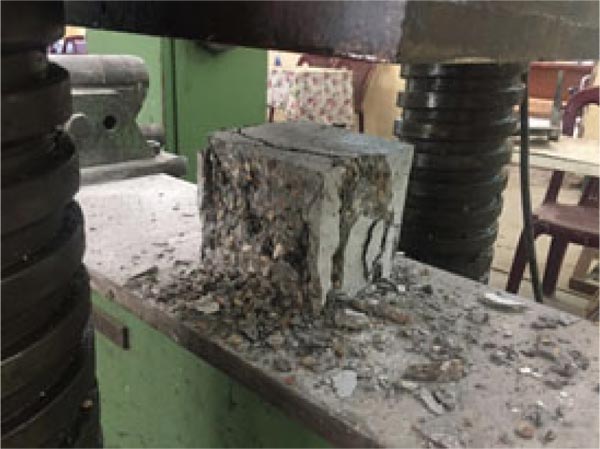
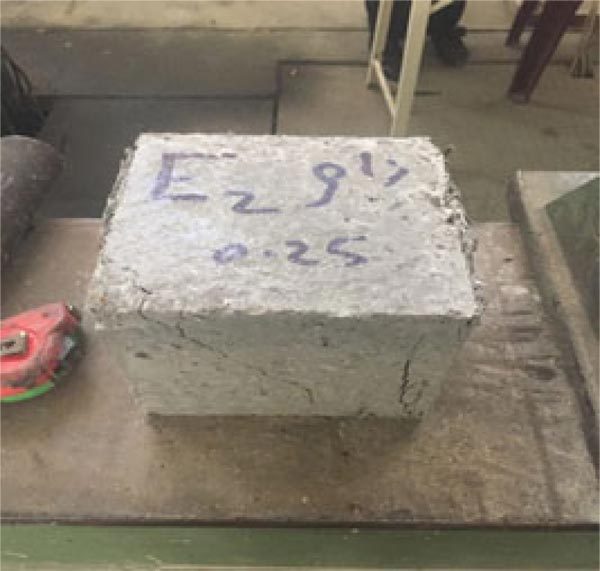
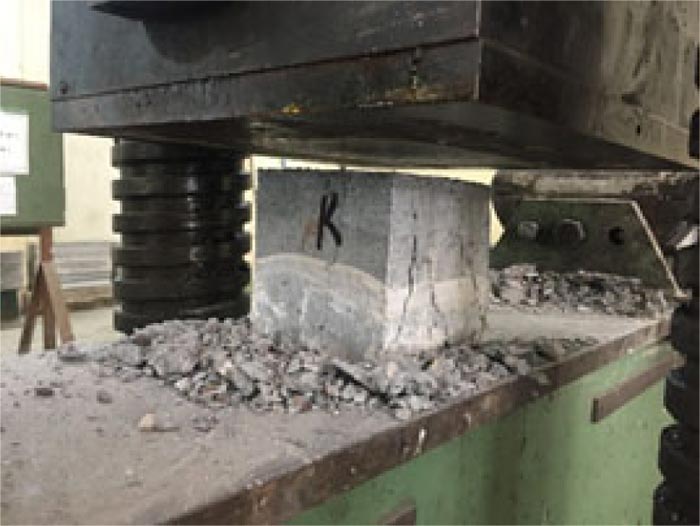
4.3. Flexural Test
According to the ASTM C78 Standards, flexural strength has been specified. From Fig. (14), for the SFRC, it might be shown that there has been an increase in the flexural strength with increased Vf of steel fibers (0.25% to 1%), from (13.95% to 34.88%), since steel fibers have been suitably strong, suitably bonded to the material. Also, it is a bridge across cracks that offer particular post cracking “ductility.”
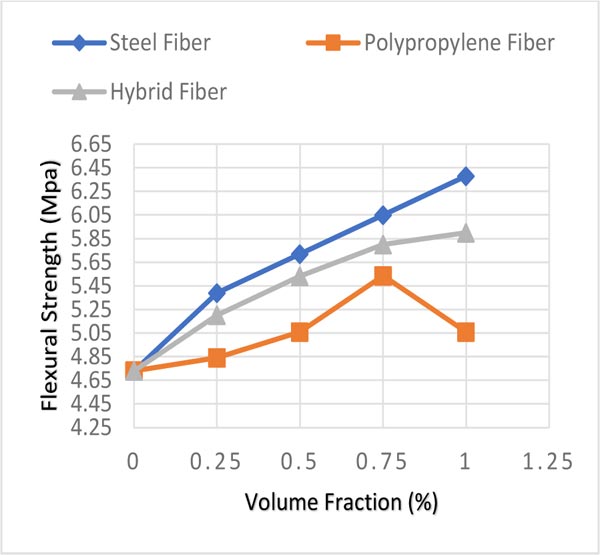
Concerning the PFRC group, the additions of polypropylene fibers increase the flexural strength from 2.3% to 17%, respectively. There will be an increment in the flexural strength when the percentage regarding fibers increases by up to 1% due to the ductile behavior of polypropylene fiber that makes it bridging across the macro cracks. The decrease in flexural strength was observed when the percentage of fibers increased to 1% due to the lack of bonding between the polypropylene fibers and the concrete as the volume fraction increased. The addition of both steel and polypropylene fibers 50:50% in the HFRC group increased the flexural strength of concrete from 13.95% to 25.1%. Respective pseudoplastic zones were found to be much narrower in comparison to that of fibers with a higher aspect ratio. In general, fibers enhance the ductility of plain concrete. Figs 15-17 show the failure pattern of the flexural strength test.
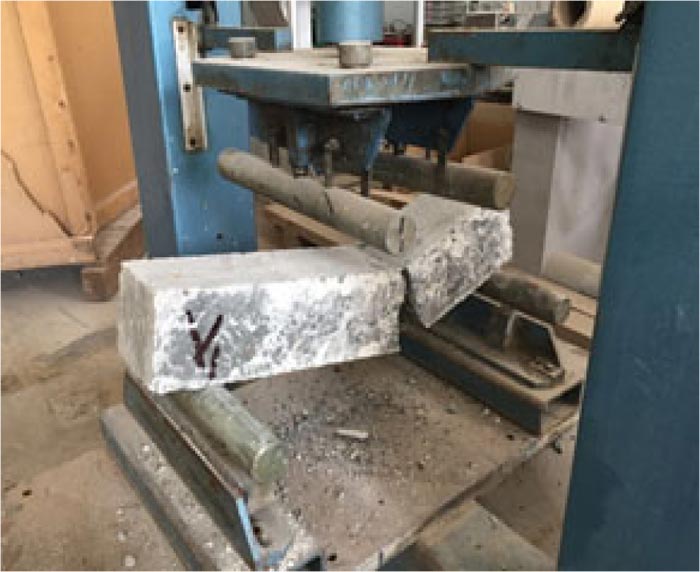
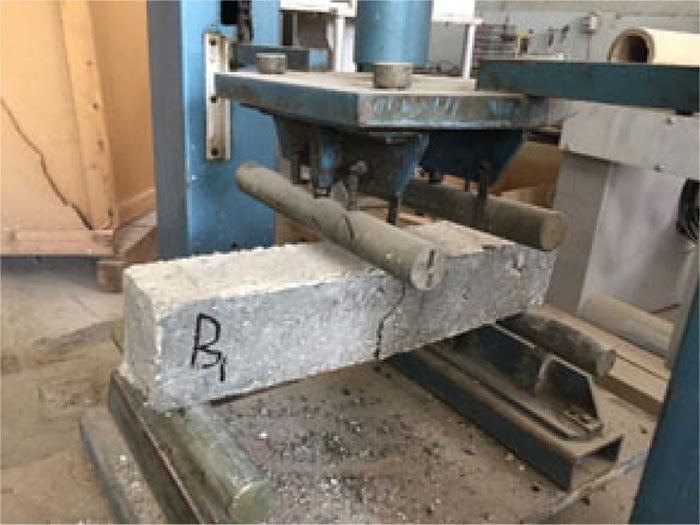
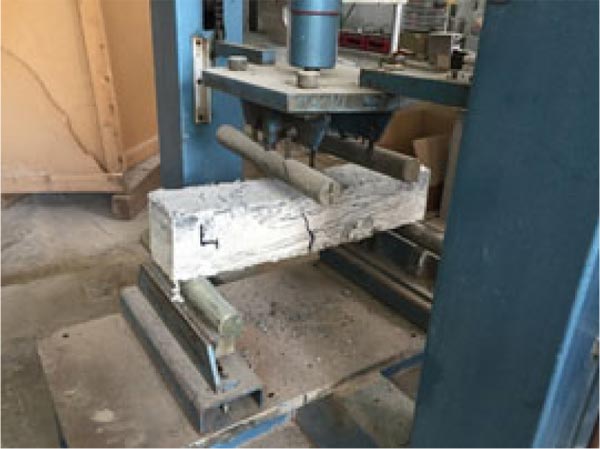
CONCLUSION
In summary, the following conclusions can be drawn from this study:
1. The addition of steel fiber increased the density of concrete by 6% at 0.75%, while polypropylene showed a reduction effect of 3%; a reduction less than regular concrete.
2. The higher volume fraction of steel fiber increased the voids entrapped that required more superplasticizer.
3. Compressive strength improved by the increase of volume fraction of steel fiber, while decreased with the rise in polypropylene fiber volume fractions
4. Hybrid fiber concrete showed intermediate strength behavior in terms of compression and flexural strength.
5. In the flexural strength test, both fibers acted as a crack propagation resistant material that caused the delay in the concrete failure and made it slightly ductile.
6. The fibers affected the workability of the concrete as the volume fraction was increased.
CONSENT FOR PUBLICATION
Not applicable.
AVAILABILITY OF DATA AND MATERIALS
The authors confirm that the data supporting the findings of this study are available within the article.
FUNDING
None.
CONFLICT OF INTEREST
The authors declare no conflicts of interest, financial or otherwise.
ACKNOWLEDGEMENTS
Declared none.