All published articles of this journal are available on ScienceDirect.
Effect of Gravel-sand Ratio on Physico-mechanical, Thermal and Macrostructural Properties of Micro Epoxy Polymer Concrete based on a Mixture of Alluvial-dune Sand
Abstract
Introduction:
In the Polymer Concrete (PC) composites, aggregates are the most important constituent, which considerably affect their performance. The purpose of this experimental study is to examine the effect of Gravel-to-Sand (G/S) ratio on the physico-mechanical, thermal and microstructural properties of epoxy micro-polymer concrete made up of local aggregates.
Materials & Methods:
The Micro Epoxy Polymer Concrete (MEPC) studied consists of epoxy resin as a binder and a mixture of two types of sands (alluvial (0/0.63 mm) and dune (0/4 mm) sands), as well as crushed limestone gravel (3/8 mm). Six compositions were prepared with two epoxy resin contents (10% and 14% of the total weight of mixture) and three G/S ratios (0.25, 0.50 and 0.75). The studied properties are density, water absorption, compressive and flexural strengths, thermal conductivity, thermal diffusivity, specific heat and macrostructure.
Results & Discussion:
The obtained results show that the G/S ratio, as well as the epoxy resin content, has a significant influence on the properties of MEPC. In addition, 14% epoxy resin and the G/S ratio of 0.75 can be considered as optimal values, which lead to very interesting physico-mechanical performances (denser and less porous material, more resistant with almost similar thermal conductivity). Moreover, the density, the water absorption and the optical microscopic observation confirm that mixes containing 14% epoxy are more impermeable, compact and homogeneous than those containing 10% epoxy.
Conclusion:
Finally, it should be noted that the incorporation of aggregates being relatively coarse decreases the grains’ specific surface and reduces the porosity of the granular mix, which enable the epoxy product to completely cover the surface of mineral grains. A perfect covering of aggregate grains with a bender improves the adhesion between the aggregates and the polymer matrix.
1. INTRODUCTION
The use of Polymer Concrete (PC) is one of the strategies followed to limit the use of ordinary cement concrete in applications requiring high tensile strength or excellent resistance to certain extreme conditions [1]. The Polymer Concrete (PC) is a composite consisting of a polymer resin binder and a mixture of aggregates [2]. Despite its relatively high cost, epoxy is one among the most preferred and used resin binders in the production of PC, due to its excellent properties [3, 4]. The achievement of better mechanical characteristics, stronger adhesion, lower shrinkage as well as easer in situ application, has extended the use of Epoxy Polymer Concrete (EPC) in the construction sector [5, 6].
Until now, a great effort in terms of experimental research has been devoted to the characterization of the physical, mechanical, thermal and durability properties of EPC [5, 7-9]. Moreover, the performances of EPC heavily depend on the amount of polymer binder, the type of aggregates and their size distribution, the reinforcement (fillers and fibers), the quality of the adhesion between components, etc [8, 10-12]. Aggregates and fillers typically occupy more than 40-80% of the volume of PC [10, 13], and they also play a key role in the mechanical and other properties [14]. These aggregates are generally of natural or industrial origin, or waste materials [15]. According to the literature, several researchers have favored the use of locally available aggregates, such as river sand and crushed stone, in order to reduce the cost of PC products [1, 3, 14, 16].
Various research works [12, 17] have been carried out to study the influence of natural aggregates on the behavior of PC in the fresh state and hardened state and in chemically aggressive environments. An optimized aggregate mix proportion with a minimum void content results in a considerable decrease in the binder content, without compromising the properties of PC, making the system more cost-effective [12, 17]. Shigang et al. [18], found that the aggregate geometrical shape has a significant impact on the failure behaviors of PC. When the aggregates have a small number of edges, they will have more sharp angles inducing a higher stress concentration during the loading and the micro-cracks will, therefore, be more easily generated in these locations, which reduce the resistance of PC. The optimal percentage of a resin polymer in the PC system depends on the nature of aggregates used. Let us note that, when using fine aggregates, it is recommended to increase the resin dosage, because of their large surface area [19, 20]. Ferdous et al. [1], noted that the distribution of aggregates in the EPC strongly depends on the resin / charge ratio of the mixture. When the resin content is more than 60%, the aggregates are uniformly distributed throughout the entire depth of the PC, due to the increased fluidity of the epoxy matrix. On the basis of the experimental and simulation results of the packing density, an optimization study of gravel percentage in PC was carried out. The optimal packing density was obtained with gravel contents of 35-55%. However, the value of 35% of gravel and 65% of sand (G/S=0.54) was retained in order to improve the workability of EPC [3]. On the other hand, Haidar et al. [8], developed a Micro-Polymer Concrete (MPC) based on a mixture of coarse and fine aggregates of granular sizes of 2-4 mm and 0-1.25 mm respectively. They reported that the MPC which was designed with a G/S ratio of 0.25 and an epoxy content of 9% has higher physicomechanical characteristics. Furthermore, Shokrieh et al. [21], reported that the effect of the epoxy resin content on the compressive / flexural strengths and the interfacial shear strength between PC and steel, is more significant than the effects of aggregate size and percentage of chopped glass fibers.
Moreover, Nogueira et al. [22], studied the effect of water absorption on the mechanical properties of an epoxy resin system and found that the increase in absorbed water led to a gradual decrease in the tensile properties.
In another context, it should be noted that the fine and coarse alluvial aggregates are becoming depleted and therefore, their cost is considerably increased. In addition, the extraction of these aggregates poses a real ecological problem, so that government regulations in many countries prohibit the overuse of these aggregates [23]. In contrast, crushed limestone sands, as well as dune sands, are widely available in the Laghouat region and remain largely unexploited [24, 25]. In fact, the use of these local materials provides an opportunity to mitigate the high cost of the EPC and decreases the environmental impact of these composites.
The main objective of this study is to optimize the composition of a Micro Epoxy Polymer Concrete (MEPC) using local aggregates (alluvial - dune sand and crushed limestone gravel). The purpose is to seek the optimal values of the epoxy resin content and the G/S ratio. The optimization of these factors may have interesting implications in terms of performance and cost. Let us note that, in previous research, different aggregates were used in the preparation of PC, but the use of dune sand in this concrete type has not been studied previously. The use of this new material in MEPC is part of the valorization of local materials and highlights; indeed, the originality of this study [26, 27].
The optimization of MEPC was carried out on the evaluation of its mechanical (compressive and flexural) strengths and thermal properties, density, water absorption capacity and the macrostructure. In addition, the combination of these tested parameters will allow us to develop more cost-effective and durable MEPC as small-scale building materials such as roof and floor tiles and for repairing damaged concrete surfaces at shallow depth.
2. MATERIALS AND EXPERIMENTAL INVESTIGATION
2.1. Materials and Sample Preparation
The studied Micro Epoxy Polymer Concrete (MEPC) was prepared using a mixture of local natural aggregates with a maximum size of 6 mm and epoxy resin. These different components are characterized below.
2.1.1. Aggregates
A mixture of two different types of local natural sand was used as fine aggregate. The first is alluvial sand (AS) (Fig.1a) obtained from the M’zi river running through the city of Laghouat (South of Algeria). The second is dune sand (DS) (Fig.1b) also from the same region. The granular classes of AS and DS are (0/0.63 mm) and (0/4 mm), respectively.
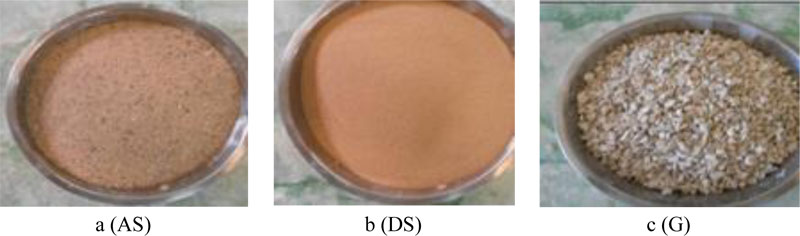
The dune sand was used to correct the fine part of the alluvial sand [28]. The natural fines of DS are very useful to improve the compactness of the MEPC composite. For this reason, the mixture of alluvial - dune sand obtained, denoted as ADS, is well-graded, and its grading curve is continuous and fits into in the desired ranges (Fig. 2). Let us note that it was used for a predetermined AS/DS mass ratio equal to 1.7 after its verification [23]. The main physical properties of the used sands (AS, DS and ADS) are summarized in Table 1. The sand equivalent values show that the three types of sand are clean and perfectly suitable to obtain a concrete composition with high performance. The fineness modulus of ADS, equal to 2.28, confirms its better finesse compared to other sands. The results of the XRD analysis confirm the essentially siliceous nature of the used sands (Fig. 3); however, the AS contains some traces of calcite.

Physical Characteristic | AS | DS | ADS |
Apparent density (kg/m3) | 1482 | 1428 | 1511 |
Specific density (kg/m3) | 2576 | 2596 | 2583 |
Fineness modulus | 2.45 | 1.18 | 2.28 |
Porosity (%) | 43 | 45 | 42 |
Visual Sand Equivalent (%) | 87 | 91 | 92 |
Piston Sand Equivalent (%) | 84 | 82 | 81 |
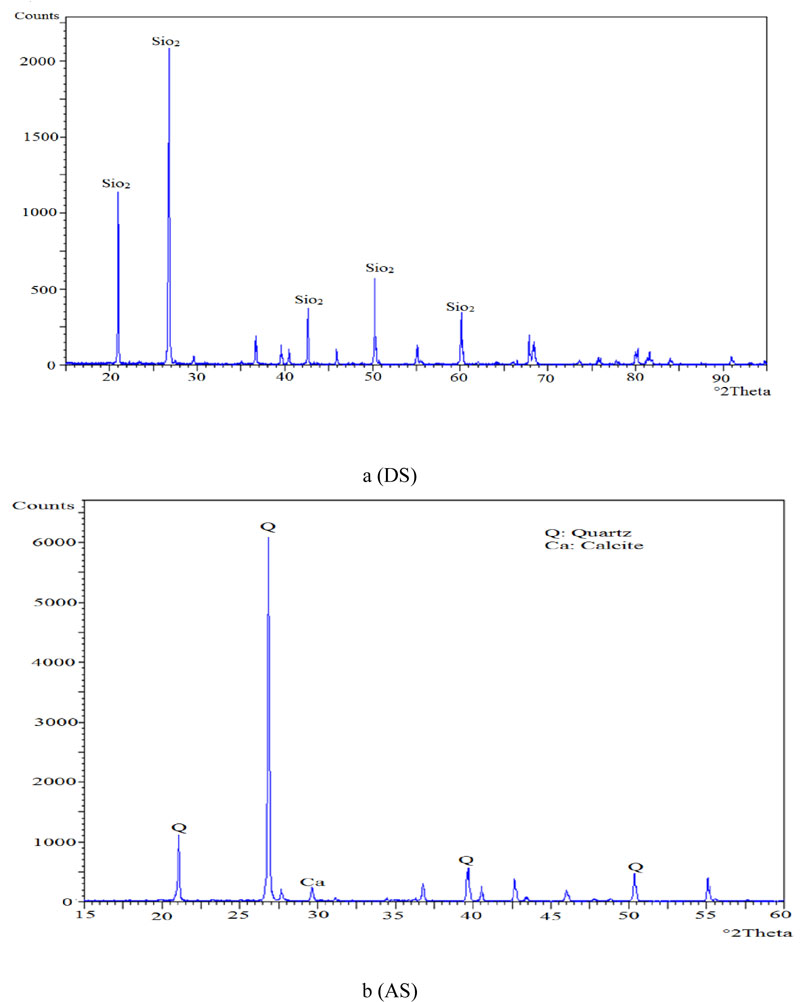
Characteristic | Value |
Density | 1.1±0.05 g/cm3 |
Viscosity at 25°C | 11000 MPa.s |
Curing time at 20°C and 65% HR | 16h |
Usual practice time (NFP18 810) | 1h 15min |
Compressive strength | > 70 MPa |
Flexural strength | >25 MPa |
Adhesion on concrete | >3 MPa |
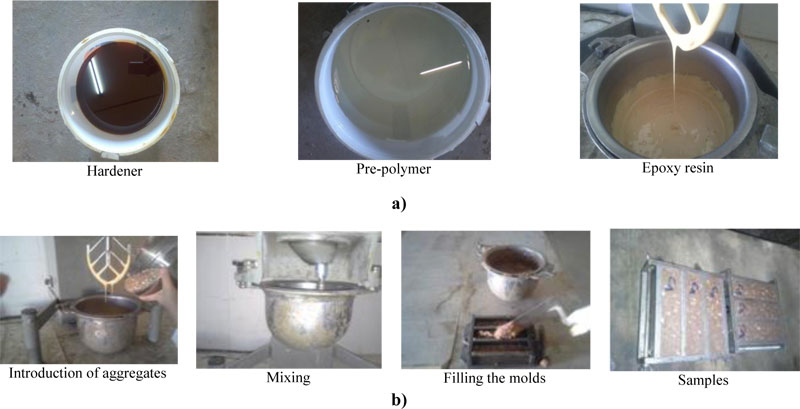
A crushed limestone gravel (G) of size range 3/8 mm (Fig.1c), extracted from a crushing plant in Laghouat, was used as a coarse aggregate. Its bulk and absolute densities are 1.42 and 2.66, respectively, its Los Angeles coefficient (LA) is 21% and its absorption rate is 1.07%. The grading curve of this gravel is presented in Fig. (2). In order to obtain good adhesion between the PC components, all the used aggregates have been dried at 100± 5°C for 24 h, before being mixed with epoxy resin [29]. The combined angularity and surface texture properties of this gravel created a strong bond with the epoxy matrix and therefore improved the mechanical properties of the concrete [30].
2.1.2. Polymer
In this study, the polymer used is an epoxy resin whose trade name is “MEDAPOXY STR” from the Algerian Granitex company. This epoxy mixture is obtained by an epoxy resin prepolymer (part A) / hardener (part B) weight ratio of 3/2, according to the manufacturer’s recommendations. The characteristics of the epoxy used, according to the supplier's technical sheet, are noted in Table 2.
2.1.3. Sample Preparation
The mixing process of the studied MEPC was performed using a mortar mixer with 5 liters capacity. It should be noted that the preparation mode of MEPC is similar to that of concrete based on ordinary cement, but the curing mode is different [7].
First, the prepolymer (part A) and the hardener (part B) were sufficiently mixed for 3 minutes to achieve a perfectly homogeneous mixture (Fig. 4a) [30, 31]. Then, the aggregates, previously dry-mixed, were gradually added to the epoxy binder for 3 minutes at low speed to ensure that all the aggregates were completely covered with epoxy resin. Immediately after mixing, 4×4×16 cm3 molds were filled in three equal layers and carefully compacted [31-34]. The latter were placed in the laboratory ambient conditions (23±2°C and 50±10% RH). Finally, the demolding was carried out after 24h and the MEPC specimens were cured in the same conditions (23±2°C and 50±10% RH) until the corresponding test time.
The two epoxy resin contents (10% and 14%) were selected for this study. This choice was based on a study of tensile and compressive strengths at 7 days of mortars samples, without gravel 3/8 mm, produced with different epoxy contents, by taking into account all the other parameters approved in the preparation of studied MEPC composites such as the AD/DS ratio =1.7. The results obtained revealed that the optimum epoxy content that leads to the best mechanical strengths ranges between 10% and 14%. The tensile and compressive strengths at 7 days ranged from 16.6 to 19.5 MPa and from 45.1 to 55.5 MPa, respectively. It should be noted that, at 7 days, epoxy polymer systems commonly achieved about 90% of their 28-day strength [35]. Table 3 shows the mixture design for the selected MEPC composites.
2.2. Experimental Investigation
2.2.1. Physical Tests
The density of PC composites is an essential property, especially in the case of repair and reinforcement applications [30]. In this work, the variation of the density of MEPC samples as a function of G/S ratio and epoxy content was followed during the first 28 days by the weight measurement of the studied samples, using a digital precision balance, with 0.1g resolution. Each measurement was repeated at least three times.
In order to study the water absorption ratios of MEPC composites, 4×4×16 cm3 prismatic specimens, at 28 days of age, were dried in an oven at a temperature of 105±5°C until obtaining a constant weight (initial weight). Then, they were entirely immersed in water for 24h, then removed and weighed (final weight) after wiping the surface water of each sample with a dry cloth. The water absorption capacity (in mass) is reported as a percentage of the absorbed water in the dry samples. This value is taken as the average of the three measurements for each composition.
2.2.2. Mechanical Tests
Flexural and compressive strength tests of MEPC composites were carried out in accordance with standard NF EN 196-1 [36], at various ages: 1, 7, 28, 90 and 180 days. The flexural strength was examined by the three-point bending test on three prismatic specimens (4×4×16 cm3) for each mixture. The six half-test pieces resulting from the flexural test were then used to measure the compressive strength. A universal testing machine with a capacity equal to 100kN was used to perform these mechanical tests. The applied loads have constant speeds of 50N/s and 2500N/s for flexural and compression tests, respectively.
2.2.3. Thermal Tests
The thermal characteristics studied of MEPC are thermal conductivity, thermal diffusivity and specific heat. These tests are carried out on pairs of prismatic specimens of 4×4×8 cm3 at 28 days of age. The method used to determine these thermal properties is based on the principle of the Transient Plane Source (TPS) technique using the “Hot Disk TPS 500” device. The used software includes tools for automatic measurement and control of the temperature of external devices as well as tools for exporting the results to the microcomputer (Fig. 5a). The test was carried out using a small probe placed between two samples of the same composition (Fig.5b). Each measurement is relative to three similar tests.
2.2.4. Structure Analysis
Finally, the structure analysis of the studied composites was conducted on the macroscopic observation of the distribution of aggregates in the epoxy matrix and the aggregate-matrix contact zone. This analysis was made on the fractured faces of MEPCs using a Zeiss optical microscope (Stemi 2000-C, Germany) at 16×, 32× and 50× magnification.
3. RESULTS AND DISCUSSION
3.1. Density
First of all, the daily monitoring of the dry density variation of MEPC samples studied during the first 28 days showed a very slight change in the density over time. This may be due to the increased cross-linking density of the epoxy binder [3]. Fig. (6) shows the average dry densities of MEPC samples obtained at 28 days.
From Fig. (6), it was found that the density of MEPCs increased by increasing the G/S ratio. However, this increase in density differs according to the amount of epoxy resin: the rate of increase reaches about 6%, for MEPCs containing 10% of epoxy, when the G/S ratio varies from 0.25 to 0.75. This is likely due to the use of coarse aggregates, which reduce the large pores by producing a high-density MEPC [37]. On the other hand, the effect of G/S ratio on the density of MEPCs, which contain 14% of epoxy is limited; the rate of density increase does not exceed 0.7% when the G/S ratio changes from 0, 25 to 0.75.
Moreover, the approximate density values of MEPCs made with 14% of epoxy showed that this epoxy content is the optimal content, which is necessary to almost completely fill the voids between aggregates. This remark is in accordance with the results of Haidar et al. [8], where they found, for a fixed G/S ratio equal to 0.25, a slight increase in the density of MPC with the increase in epoxy content. Elalaoui et al. [3], noted, for a constant G/S ratio equal to 0.54, a significant decrease in the density of PC as the epoxy content increased. The mixtures of 14% epoxy show density-growth rates of 7%, 4% and 1% compared to those containing 10% epoxy for G/S ratios of 0.25, 0.5 and 0.75, respectively. Maherzi et al. [38], found that the optimal amount of epoxy (14%) results in a maximum density of polymer mortars. It should also be noted that increasing the quantity of coarse aggregate limits the effect of epoxy percentage on the density of MEPC. Finally, the densest MEPC is obtained at a polymer content of 14% and a G/S ratio = 0.75.
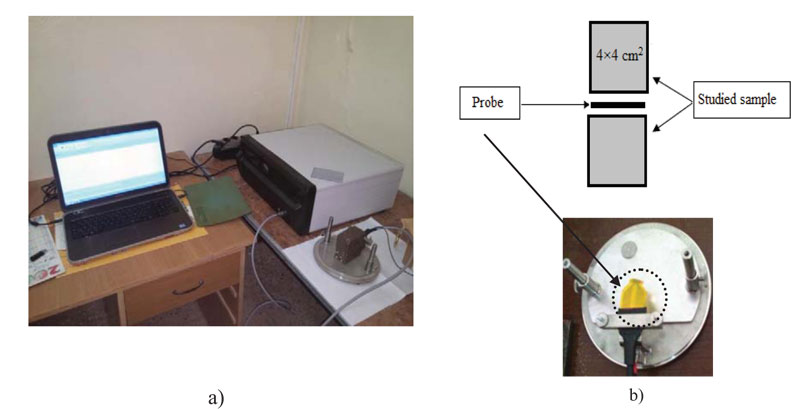
Designation | Coarse Aggregates (%) | Fine Aggregates (%) | G/S | Epoxy (%) | |
AS (%) | DS (%) | ||||
MEPC10/0.25 | 18 | 45.33 | 26.67 | 0.25 | 10 |
MEPC10/0.5 | 30 | 37.78 | 22.22 | 0.5 | 10 |
MEPC10/0.75 | 38.57 | 32.38 | 19.05 | 0.75 | 10 |
MEPC14/0.25 | 17.2 | 43.32 | 25.48 | 0.25 | 14 |
MEPC14/0.5 | 28.67 | 36.10 | 21.23 | 0.5 | 14 |
MEPC14/0.75 | 36.86 | 30.94 | 18.2 | 0.75 | 14 |
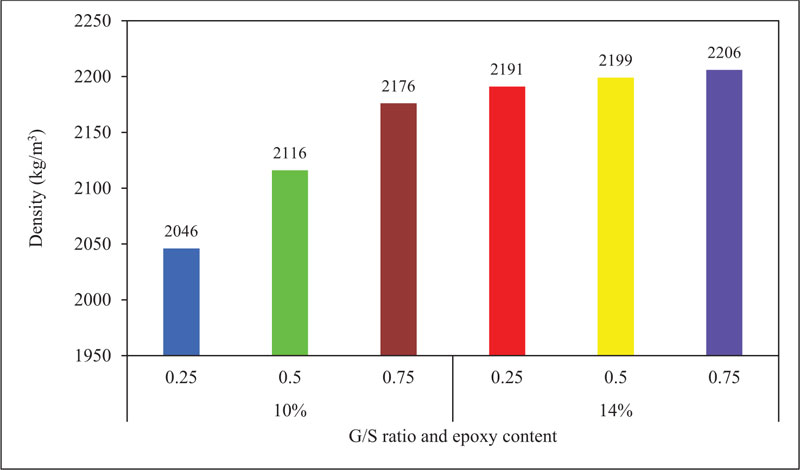
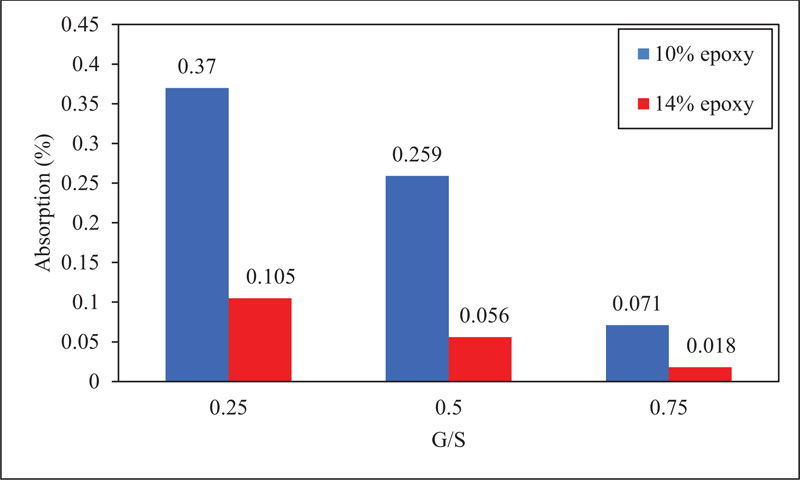
3.2. Water Absorption
Fig. (7) shows the water absorption of the studied MEPC. The first point to be made is that all water absorption rates of MEPCs are very low and below 0.4%, because of their high water-tightness [4, 39, 40], and hydrophobic properties of hardened epoxy resins [4]. This desirable property indicates that MEPCs have better durability against adverse weather conditions as they can prevent the intrusion of water and salts [1, 41]. In addition, the water absorption capacity of MEPCs decreases with the increase in G/S ratio for the two epoxy contents (10% and 14%), which confirms the decrease in the open porosity with increasing the G/S ratio. However, when the gravel ratio changes from 0.25 to 0.75, the rate of decrease in water absorption of MEPCs for the two epoxy contents (10% and 14%) is almost identical and reaches 80%.
Furthermore, the MEPCs produced with 14% epoxy have very low water absorption rates, compared to those based on 10% of epoxy, regardless of the G/S ratio. This is due to the fact that all MEPCs with 14% of epoxy have fewer voids, due to the strong matrix-aggregate bond which prevents water penetration. Haidar et al. [8], discovered that the water absorption of MPC is at low levels for an epoxy content ≥ 9%. The mixture MEPC10/0.25 shows a very high water absorption capacity than that of other mixtures. This is mainly due to the absence of coarse aggregates, which can make the mixture enough compact and the quantity of epoxy resin insufficient to wrap all aggregates and fill in all voids. However, the presence of coarse aggregates, in combination with the alluvial and dune sands, and an epoxy content of 14%, show a synergy in the resistance to water absorption where the water absorption rate of mixture MEPC14/0.75 is practically too low (0.018%).
The optical microscope images (at a magnification of 32×) of the fracture surfaces of MEPCs, illustrated in Fig. (8), confirm the previous results (density and water absorption).
It can also be seen that the voids between aggregates and matrix are clearly reduced by increasing the amount of epoxy polymer. The pore diameters become smaller and the porosity is evenly distributed.
3.3. Flexural strength
The variation in the flexural strength of the studied MEPCs as a function of time is illustrated in Fig. (9). It is clear that the changes in epoxy resin content, G/S ratio and curing time cause a variation in the tensile strength of MEPCs. The flexural strength of the MEPCs obviously increases with the curing time: A rate of increase of 30% is reached between the first day and the seventh day, while a slight increase is recorded between the seventh day and the 180th day. These increases are due to the cross-linking of the polymeric binder. In addition, it should be noted that all MEPCs have very significant flexural strength at the age of 1 day.
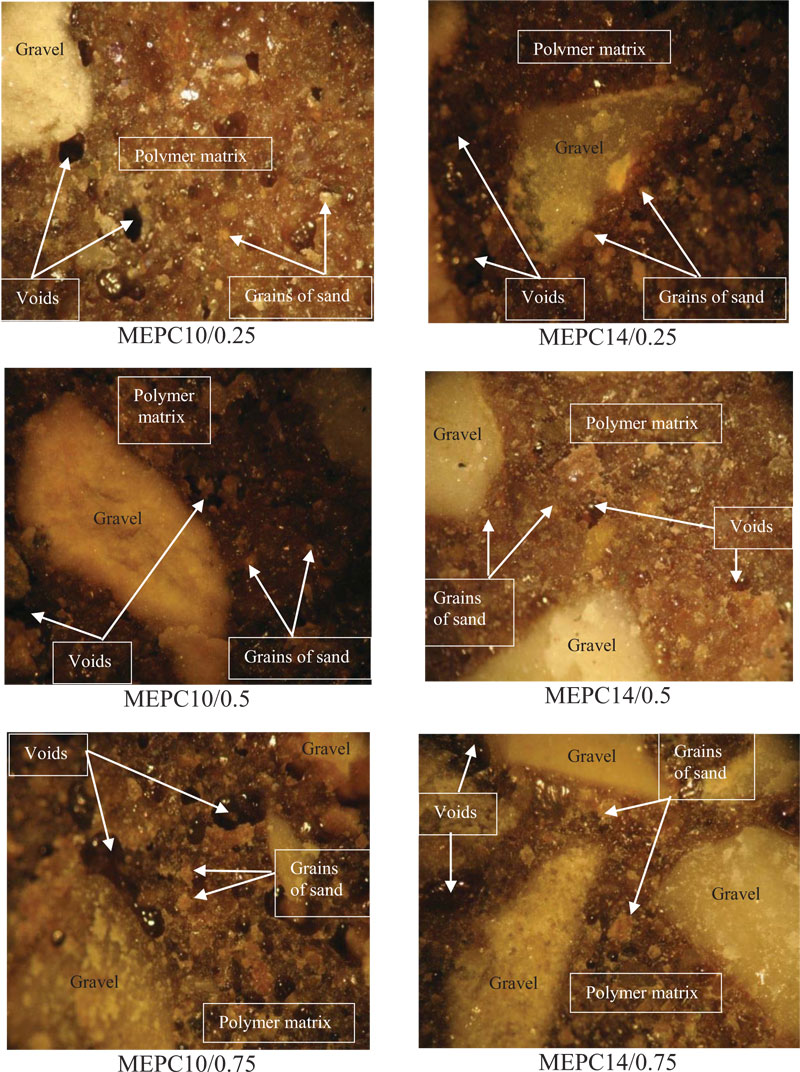
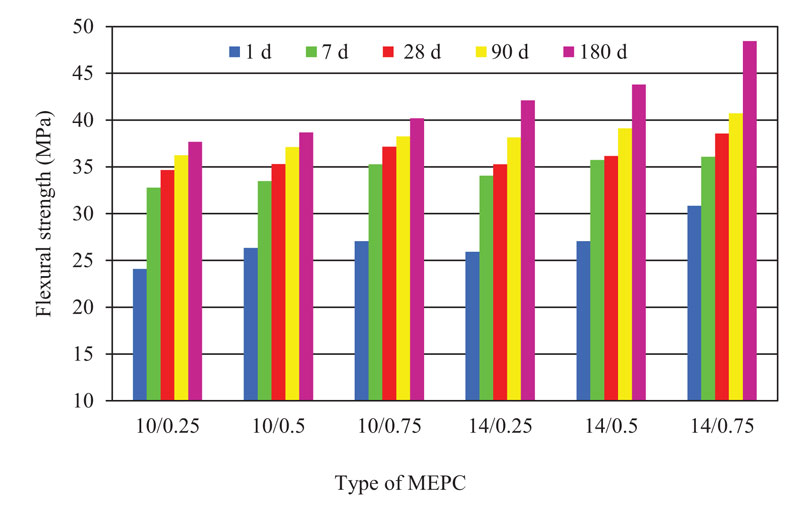
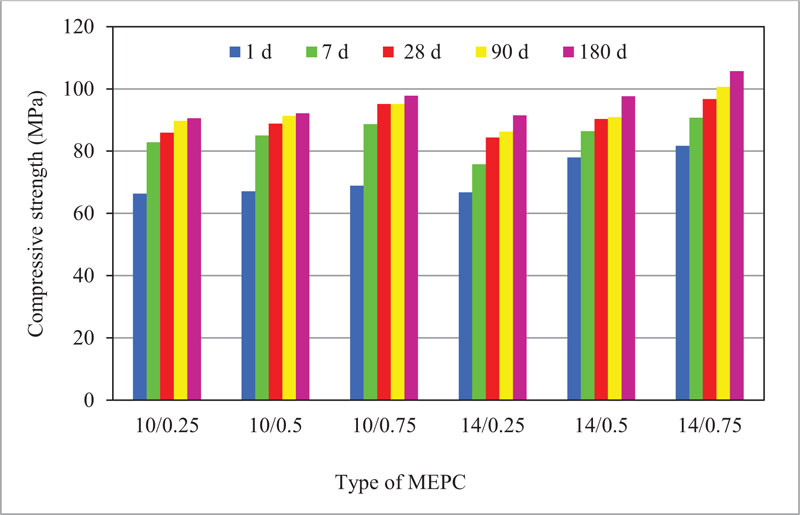
Regarding the effect of epoxy content on the flexural strength of MEPCs, the comparison between the two epoxy contents studied (10% and 14%) for a constant G/S ratio shows that this effect remains limited, especially when the mixture contains fine aggregates (low G/S ratio) [5]. This can be attributed to the insufficient amount of epoxy resin to cover the sand particles [42]. Otherwise, the best flexural strengths were obtained for the MEPC with 14% of epoxy resin. This highlights the favorable effect of epoxy resin on the flexural strength of MEPC samples [5, 43]. On the other hand, when the G/S ratio is increased, the flexural strength is improved. Therefore, the maximum value of the flexural strength is obtained for the MEPC14/0.75 mixture and is equal to 48.44MPa at 180 days. This result can be explained by the larger size of aggregates that decreases voids in the composite (makes it denser) and therefore, increases its flexural strength [42, 44]. Preliminary experiments also confirm that the flexural strength of MEPCs is very high than that of polymer mortar for equal epoxy content. The addition of 3/8 mm gravel has a major effect on the flexural strength.
3.4. Compressive Strength
The results of the compression strength test of MEPCs are presented in Fig. (10). These results show a trend almost similar to that observed in the evolution of the flexural strength of MEPCs.
From Fig. (10), it is observed that the compressive strength evolved overtime for all MEPC mixtures. At 7 days, the compressive strength can reach more than 90% of the 180day compressive strength. This makes it easy to meet the application requirements for faster repair
[15, 35]. In addition, it should be noted that the values of compression and flexural strengths obtained show that the MEPC composites are high-performance materials.
Furthermore, we can see that the compressive strengths slightly increased with the increase of the mass of epoxy resin, but the epoxy resin has a little effect on the compressive strength for G/S= 0.25. The same remark has been observed for the influence of the G/S ratio in the case of epoxy content equal to 10%, where this effect was limited. Contrary to that, the increase in the percentage of coarse aggregates, for example, G/S=14%, contributes to obtaining a very high compressive strength. Consequently, the mixture MEPC0.75/14 has the best compressive strength at all ages and the maximum value of this resistance reaches 105 MPa at 180 days. These values are higher than those obtained by Novoa et al. [45], who found a maximum compressive strength at 7 days equal to 68 MPa for a percentage of 20% of epoxy resin and by Haidar et al. [8], who found compressive strengths between 23 and 70 MPa for percentages of epoxy binder ranging from 5% to 13%. These results are justified by the fact that the G/S ratio of 0.75 increases the adhesion between the epoxy and the aggregates, which gives the MEPC of better quality. In addition, the amount of epoxy resin of 14% is sufficient to bind the grains and fill the intergranular voids.
3.5. Thermal Properties
The obtained results of the thermal tests, carried out on the different studied compositions are grouped in Table 4.
To quantify the influence of the G/S ratio and the epoxy content on the heat transfer potential, the thermal conductivity coefficient is calculated for each mixture. The thermal conductivity values of various MEPC composites are very low [3, 4, 46]; they are affected by the G/S ratio and the polymer content. The increase in the epoxy content decreases the total porosity and the average pore size by filling the voids of granular skeletons and by enveloping the aggregates. The heat transfer through the MEPC will, therefore, be attenuated and thus, a slight decrease in thermal conductivity will be recorded [3]. When the G/S ratio was increased, this decrease was significant: when the polymer content increased from 10% to 14%, the rate decrease in thermal conductivity of 6%, 20% and 23% was recorded for the G/S ratios of 0.25, 0.5 and 0.75 respectively. However, it should be noted that the thermal conductivity of MEPCs increases with increasing G/S ratio. It was concluded that the addition of mineral aggregates increased the conductivity of MEPCs [4]. But, this increase in conductivity, caused by coarse aggregates, differs depending on the epoxy content used. The effect of the G/S ratio on the conductivity of MEPC mixtures with 10% of epoxy is clear, since the percentage increase reaches 26%, while this percentage does not exceed 3% in the case of MEPC mixtures with 14% of epoxy.
As indicated in Table 4, the thermal diffusivity values increase when the G/S ratio increases; a similar evolution has been observed for both MEPC with 10% and MEPC with 14% of epoxy. In addition, the values of thermal diffusivity range from 1.14 to 1.29 (10-6×mm2/s) in the case of 10% of epoxy and 0.89 and 1.19 in the case of 14% of epoxy, which show that the thermal diffusivity decreases with increasing epoxy content.
Epoxy Content (%) | G/S | Thermal Conductivity λ (W/mK) |
Thermal Diffusivity (m2/s)×10-6 |
Specific heat (J/kg K) |
10 | 0.25 | 1.597 | 1.14 | 640 |
0.5 | 1.903 | 1.22 | 690 | |
0.75 | 2.026 | 1.29 | 810 | |
14 | 0.25 | 1.495 | 0.89 | 570 |
0.5 | 1.516 | 1.01 | 700 | |
0.75 | 1.551 | 1.19 | 760 |
Regarding the specific heat, the obtained values were between 570 and 760 (J/kg K) for MEPCs based on 14% of epoxy and between 640 and 810 (J/kg K) for MEPCs of 10% of epoxy. These values indicate that the specific heat of MEPCs is increased when the coarser aggregates are added. In addition, increasing the epoxy content from 10% to 14% decreases the specific heat of MEPC. The same arguments used to justify the decrease in thermal conductivity are still valid for the thermal diffusivity and the specific heat.
3.6. Macrostructure
The optical microscope examination of the structure of the studied material was concentrated mainly on the general appearance of the composite, the morphology of the polymer paste, the matrix-aggregate adhesion and the distribution of aggregates in the matrix. The optical microscope images obtained are presented in Figs. (11 and 12).
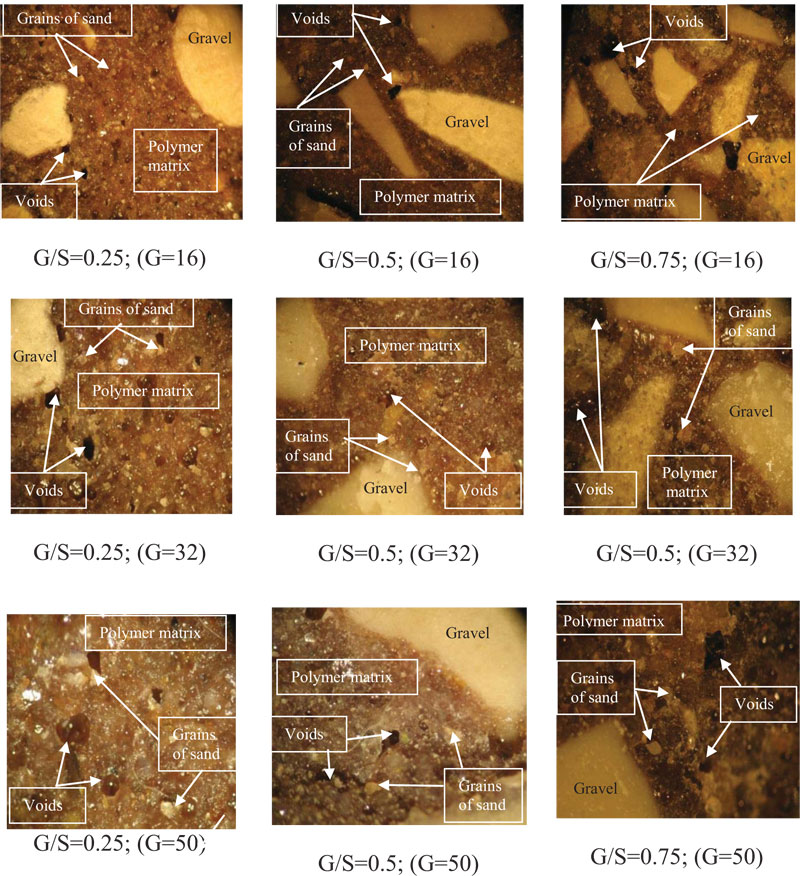
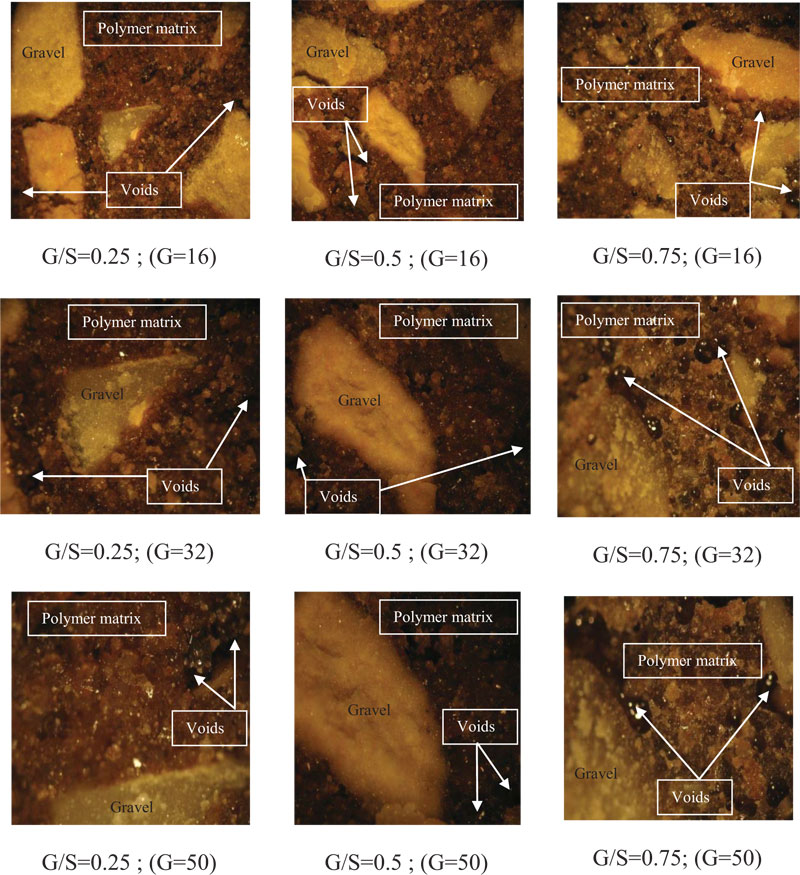
The analysis by optical microscope of all the studied MEPC mixtures confirms that they have a continuous macrostructure with the absence of cracks and failures between aggregates and matrix. This shows that MEPCs can be considered as durable and more resistant building materials. In addition, the obtained images show the random distribution of coarse aggregates and porosity in the matrix. The pore distribution is different from one sample to another. It can be noted that the quantity and the size of the voids observed decrease with the increase in G/S ratio. This finding confirms the increase in the density of MEPCs with the increase of G/S ratio. Compared to other mixtures, MEPC10-0.75 presents good aggregate-matrix adhesion, the sand grains are well coated by the paste and the aggregates are well distributed in the matrix.
From Figs. (11 and 12), it can be noted that the structure of MEPCs with 10% of epoxy seems to be less compact and less homogeneous than that of MEPCs with 14% of epoxy, which leads to more air bubbles due to their low polymer percentage. The general appearance of the matrix shows an increase in the porosity of the matrix when the percentage of the polymer decreases. This finding confirms the decrease in the density of MEPC with the decrease in polymer content, seen previously.
Finally, it should be noted that the density, the water absorption and the optical microscopic observation also confirms that mixes containing 14% epoxy are more impermeable than those containing 10% epoxy.
CONCLUSION
The study of the physico-mechanical, thermal and microstructural properties of MEPCs, prepared from local materials according to different G/S ratios and epoxy contents, led to the following conclusions:
- The density of MEPCs increased with the increase of coarse aggregate content and epoxy content; consequently, the densest MEPC is obtained with a polymer content of 14% and a G/S ratio of 0.75.
- The water absorption coefficients of all MEPC mixtures indicate their high resistance to water absorption. In addition, the use of coarse aggregates in combination with alluvial and dune sands, in the case of an epoxy content of 14%, leads practically to lower water absorption rate, which can reach 0.018%.
- The best mechanical strengths obtained at an early age show that the studied MEPCs are high-performance building materials that can easily meet the application requirements for faster repair.
- The addition of coarse aggregates and the increase in the epoxy content increase the flexural and compressive strengths of the studied MEPCs. However, this improvement is reduced at low G / S ratios.
- The reduced thermal conductivity of MEPCs, prepared with 14% of epoxy and containing coarse aggregates, can make it possible to obtain better thermal insulation performance.
- Optical microscopy images have shown that MEPCs present a dense and homogeneous macrostructure, especially when they contain coarse aggregates.
- Finally, the density, the water absorption and the optical microscopic observation also confirm that mixes containing 14% epoxy are more impermeable than those containing 10% epoxy.
CONSENT FOR PUBLICATION
Not applicable.
AVAILABILITY OF DATA AND MATERIALS
Not applicable.
FUNDING
None.
CONFLICT OF INTEREST
The authors declare no conflict of interest, financial or otherwise.
ACKNOWLEDGEMENTS
We would like to thank the General Directorate of Scientific Research and Technological Development of Algeria (DGRSDT) for their support.