All published articles of this journal are available on ScienceDirect.
Experimental Tests on Cement Mortars Manufactured with Hemp Flour
Abstract
Aim:
Currently, research and market needs are aimed at the production of more and more specific mortars and concrete with the best properties and mix design directed towards increasingly specific uses.
Background:
This research starts with a discussion on cement and aggregate assortments, which are the basic properties of mortars.
Objective:
The choice of suitable additives able to correct the rheological, workability and resistance properties of the mixture is focused.
Methods:
In this framework, the current research activity involves some experimental laboratory tests on cement mortars manufactured with hemp flour, intended as a “natural” additive. The aim is the search for any improvements given by the hemp flour to the physical and/or mechanical performances of the tested mortars.
Results:
Hemp flour, due to bonding properties, increases the compactness, and therefore, the resistance to environmental factors by the examined cement mortars. The rheological features of mixtures with different percentages of hemp flour, whose maximum water percentage absorbed was resulted to be 125%, were investigated. It was found that standardised sand reduces shrinkage phenomena of tested specimens. Moreover, the compression and bending moment behaviour of manufactured specimens was analysed with the aim of finding the optimal weight percentage of hemp flour to improve their mechanical performances.
Conclusion:
The experimentation performed leads to several conclusions and interesting future developments. It was found that 3% is the best-weighted percentage of hemp flour to increase the mechanical properties of examined mortars made of standardised sand. As further developments, there is a need to identify the limit percentage of hemp flour to be added to the mixture, so as to avoid the decay of the mechanical properties. In addition, further experiments must be carried out on concretes, where the presence of gravel leads to improve the stability and mechanical resistance of the cement matrix.
1. INTRODUCTION
According to studies conducted by the European Community, the construction industry accounts for 24% of the total raw materials used on a global scale. In addition, the processes related to constructions, such as extraction, processing, transportation and installation of materials, consume a large amount of energy and water. A useful tool for choosing the most suitable materials for sustainable building design is the Life Cycle Assessment (LCA) method. It compares the environmental impact of different materials commonly used in constructions and suggests low energy consuming alternatives. The method, defined by ISO 14040 (2006) [1] and ISO 14044 (2006) [2] standards, is rather complex, but some simplifications can be adopted by designers for the decision-making process to recruit the most adaptive sustainable materials.
In the project and erection phases, designers have a decisive role in reducing the impact of constructions on the environment, so that they can be easily dismantled, rather than demolished, at the end of their life cycle. In this context, reconsidering the design would facilitate the separation of materials for subsequent reusing and recycling, also saving energy in preventing demolishing operations with expensive and energy-consuming tools and machinery.
For these reasons, a frontier of new constructions is created with the aim of resolving the fundamental issue of “environmental sustainability”. A new way of designing and erecting buildings minimizing their impact on the ecosystem, leading to the so-called Green Buildings, is therefore introduced. Sustainable architecture and environmental issues have rightfully entered the agenda of business of local and international communities and people can no longer do without it. The word “sustainability” and the label “sustainable architecture” spread among architects, engineers and designers basically for functional and formal reasons. Objects that are considered sustainable must reveal ecological factors through their image. Sustainable architecture designs are conceived to limit the environmental impacts, considering project targets energy efficiency, health improvement and comfort of inhabitants. In this way, it is possible to have structures and appropriate technologies as well integrated into the buildings. Making sustainable architecture means knowing how to build and manage a construction that best meets the needs and requirements of clients, taking into account the natural resources already in the embryonic phases of the project. Therefore, without causing discomfort to people, sustainable architecture tries to fit harmoniously into the environment, also considering the reuse of materials.
The use of sustainable type materials, giving rise to a better healthiness of the built-up, has an improvement of the well-being and economy of the whole community. In this way, it has, therefore, become possible to live in a green house, due to the use of both sustainable construction materials and architectural and technological devices aimed at high energy saving. A house made with ecological materials, in fact, is a structure that does not harm those who live there and which greatly reduces the values of internal and external pollutions. Ecological materials are not much diffused in the construction market, but, given their positive impact on the environment aiming at reducing the air pollution, the building sector has started to change, evolve and to go towards these materials, whose use is becoming a very pressing need for political classes, designers and populations in less time. One of the main objectives of those persons engaged in the field of sustainable architecture is to recycle all or almost the architecture products. Building constructions that can be broken down into elements and materials easily to be recovered, reused and disposed of without causing further pollution through full or global recycling is the key issue of sustainable development. Modern elements composed of different layers of chemical materials glued together pose the serious problem of separation before recycling. The demolition of reinforced concrete itself requires an immense expenditure of energy. Unfortunately, designing buildings that can be dismantled and adapted to new uses becomes a prerogative exploited only by few political classes of World Countries.
Currently, the world of green buildings is constantly looking for discovering new economic and environmentally sustainable materials. In this framework, the hemp has been identified as a very interesting material to meet certain needs. Hemp products are the result of a highly sustainable production sequence. Hemp cultivation is rapid, requires little water and is subjected to very rare parasitic attacks. Green building plantations provide zero-kilometre materials, reducing production costs and polluting emissions from the building process. From hemp stem and flowers, completely natural plasters and varnishes are produced to make healthier the building interiors. The hemp, in fact, is able to synthesize carbon, reducing CO2 emissions and, therefore, improving environmental conditions. Wood panels or hemp-lime blocks give thermal-acoustic insulation and breathability to buildings. Considering green buildings, it is important to notice that, while traditional constructions are responsible for 30/40% of total CO2 emissions, the whole production process of lime and hemp is carbon negative, i.e., remove more CO2 from the environment than that would be entered by the production process. For the sake of example, it is estimated that one tonne of dry hemp can sequester 325 Kg of CO2. Moreover, it is calculated that, without considering transport and processing emissions, a square metre of hemp-lime masonry detains 35 Kg of CO2.
In this framework, the use of hemp flour (Fig. 1) is herein conceived as an additive of mortars, which plays a very important role in the behaviour of masonry structures [3, 4]. Hemp flour is used to both reduce the amount of cement, whose production gives rise to about 7% of CO2 released into the atmosphere each year, and avoid the use of other synthetic additives. Hemp flour is obtained from milled cannabis (Cannabis sativa) seeds after the pressing process used to obtain oils. In the past, the obtained flour, mixed with wastes from the hemp decortication process, was used as food for animals. Conversely, today, the flour is highly appreciated and intended for human consumption, due to its nutritional properties.
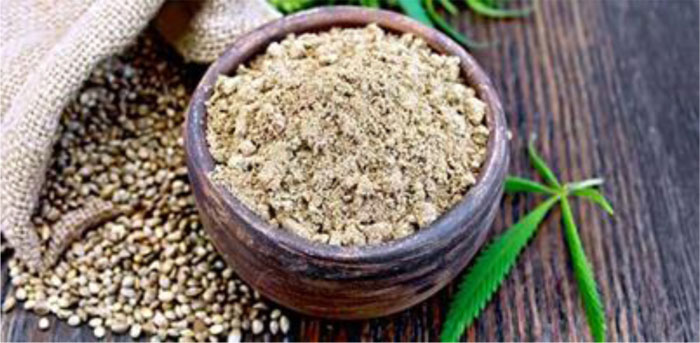
The experimental activity herein presented and discussed aims at showing the mechanical and physical benefits provided by hemp flour in manufacturing cement mortars. Through the results of compression and bending moment laboratory tests, the best percentage of hemp flour to imrpove the mechanical performances of tested mortars was found. In this way, housing solutions based on highly efficient and innovative materials with a low environmental impact are provided.
2. MATERIALS AND METHODS
2.1. Premise
When choosing the components of mortars, being unknown the nature of aggregates within the mixture, a series of initial questions should arise. Which sand type should be used? How much are considerable shrinkage phenomena depending on the type of sand used? In the current experimentation, two series of specimens, one manufactured with commercial (equal dimensions grains) sand and the other made of standardised (assorted dimensions grains) sand, have been packaged in order to evaluate their different behaviour in terms of shrinkage phenomena. Without modifying the percentages of other mixture components, it has also been possible to compare each to other the mechanical resistances of cement mortars manufactured with these two sand types.
In the packaging process, it is essential to comprehend two key aspects: the space occupied in the mixture by the individual constitutive elements and the hygroscopic behaviour of hemp flour. In fact, considering that the mixture consists of sand, cement and water, the addition of hemp flour as a fourth component should be carefully evaluated. In particular, hemp flour, considered as an additive, is added in terms of weight or volume percentage with respect to the cement amount in the mixture. It is also assumed that the ratio between the hemp flour weight and its volume is 1:1. This implies that reasoning in terms of hemp volume or hemp weight is the same.
Once the volume occupied by the constituents is established, it is essential to understand what is the water amount absorbed by hemp flour. The hemp structure is a cellulose polymeric matrix, that is a natural polymer where cellulose reacts with water and tends to dissolve. In general, the different properties of building materials depend on their chemical and/or mineralogical composition, micro- and macro-structures and porosity.
In order to have a correct water/cement ratio, it is vital to know the water percentage absorbed by aggregates aiming at rightly packaging the mortar mixture. Unsaturated aggregates remove water from the mixture, whereas aggregates in wet conditions give water to the mortar. The lack of knowledge related to the aggregate porosity can result in the reduction of the binder quantity, decrease in the hydration heat, there by counteracting the cement paste shrinkage.
2.2. Materials and Test Methods
Manufacturing of sustainable mortars investigated in the current work has required the use of water, two types (commercial and normalised) of sand and Portland cement type 425, composed by clinker plus gypsum (95,5%) and other substances (4.5%), which were verified and certified according to the EN 197-1 standard [5].
Normalised sand has particles from 0.063 to 4 mm in the percentage greater than 95%, while commercial sand is made almost entirely of particles between 0.5 and 4 mm, but with a high percentage of very fine aggregates.
Hemp flour is a material never used in the Building Engineering field. It was employed especially in the food sector instead of the wheat flour; it is characterised by moisture of 12% and is composed of particles having a diameter of 100 μm.
The procedure used for manufacturing the specimens is done following the “rule of art” defined in the UNI EN 197-1 standard [5], which establishes the preparation modalities of samples. In fact, with a suitable mixture, the correct performance and quality degree required in the design phase can be guaranteed. Subsequently, in order to understand the real properties of the mixture, it should be defined: 1) quality and quantity of the binder in the mixture, especially with reference to the hydration kinetics and 2) the water absorption capacity of vegetable particles, which influences the total water amount of the compound. The selection of the right proportions of ingredients for the mixture preparation has the aim to obtain a material with good workability, satisfactory strength and acceptable durability, so to have the least possible expenditure of economic and environmental resources. Other than the basic mixture (samples denominated “as are”), the use of the added flour aims at improving the rheological behaviour of the mixture.
In the current experimentation, the mortar mixture is therefore packaged with the following weights of components: 1) 1,350 kg of sand, 2) 0,225 Kg of water and 3) 0,450 Kg of cement, leading to a water/cement ratio = 0,5 (Fig. 2).
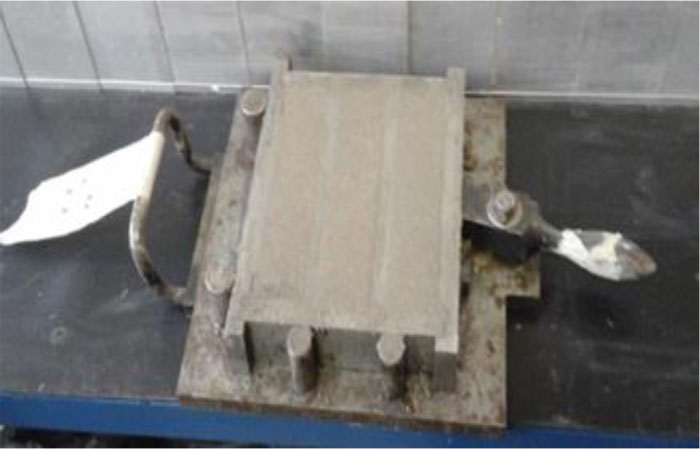
The samples manufactured with commercial sand are the reference specimens, which are tested to verify the influence of both a different sand type (standardised) and the hemp flour (as an additive) on the mechanical and physical behaviour of examined mortars.
The tests carried out in the laboratory provide the various basic parameters of each specimen necessary to have products conformed to the European Community qualification process (CE marked). The consistency of cement mortars is established through flow tests on a shaking table, which are ruled by the UNI 1015-3 standard [6]. These tests measure the slump flow of cement mortar specimens. After the flow table is wetted, a cone placed in the centre is filled with fresh cement mortar in two equal layers. Each layer is tamped 10 times with a tamping rod. A waiting time of 30 seconds is occurred before lifting the cone. The flow table is before lifted up to 40 mm and then dropped 15 times, causing the cement mortar to flow. After this phase, the diameter of the mortar flow is measured. The slump flow defines the workability and, therefore, also the fluidity level of the mortar sample. This dynamic test tries to evaluate the features under qualitative and quantitative ways, influencing the mortar workability. Once performed on the “as are” specimens, the procedure is applied to the additive mixture in order to understand the influence conferred by the hemp flour to the mixture in terms of workability (Fig. 3).
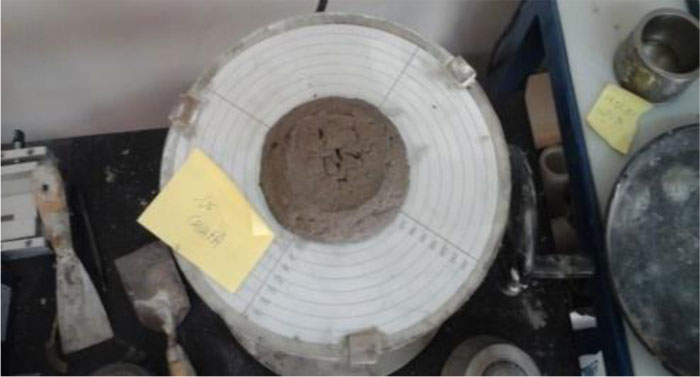
The first set of specimens is manufactured with commercial sand. For the packaging process, the correct balance of components is of fundamental importance in order to avoid any risk due to the physical alteration of samples. The addition of hemp flour is made in percentage terms compared to the cement weight. In particular, hemp flour percentages equal to 1%, 2%, 5% and 10% are considered for the packaging of specimens (Fig. 4).
After preparation of doughs and the consequent workability tests, the presence of an abnormal shrinkage is observed with the presence of micro-cracks. Perhaps, this is due to either the nature or the excessive percentage of the aggregate employed. After mortar hardening, specimens are discarded, showing surface moisture as a consequence of the excessive filler percentage used, which is responsible for their degradation in some parts, as shown in (Fig. 4) Thus, to eliminate this problem by leaving the sand weight unaltered, it is appropriate to make the inert sieving in order to check the used percentage quantity to be compared with the mixed assortment of the normalised sand. Therefore, a new granulometric mixture, having the same normalised sand percentage, is considered. This is useful to understand the right porosity amount to have the mechanical engagement of the mixture with the used hemp flour.
Once the physical problems of specimens made of commercial sand are solved, the granulometric range of the standardised sand is defined. These physical difficulties lead towards the careful observations of two main issues, namely the presence of the filler and lack of cohesion in the presence of high percentage aggregates. In order to eliminate the arisen problems, the hemp flour percentages are reduced, so to consider the moulding acceptable between aggregates and cement paste. This objective is pursued through a controlled particle size range of the standardised sand, whose use is permitted by the current standards for the production of cement mortars. As a consequence, a granulometric melt of this sand is selected and used to manufacture other specimens, also by taking into account the relative data on the size of the sieved commercial sand. In the manufacturing process, a very high percentage (85%) of aggregates with d = 1mm is used. Once the assortment with the normalised sand is defined, the same packaging process is also done with commercial sand aiming at having a granulometric comparison to know the filler percentage in the mixture.
Ultimately, from the granulometric curves, a significant presence of very fine inert in the commercial sand is enshrined. Of course, the sand dimensions, or the aggregate ones, largely influence the physical properties of the newly prepared specimens.
The procedure always follows the same process previously done. The only differences are the minor percentages of hemp flour used to avoid shrinkage and other physical nature phenomena. Thus, percentages of 0.5%, 1%, 3% and 5% are used for preparing new specimens (Fig. 5).
The comparison among specimens indicates how the excessive presence of the filler inside the commercial sand is responsible for several physical problems, including the pulverising of samples. In order to solve the detected troubles, the normalized sand is sifted to obtain a new granulometric assortment. Through this process, a new mix design with aggregates having diameters larger than those previously used is setup. This increases the mixture compactness, improving the mechanical strength of manufactured samples.
Conclusively, physical problems arising in the specimens manufactured with commercial sand are:
- Increased shrinkage;
- Pulverising of faces;
- Edge cracks;
- Poor compactness.
The use of commercial sand instead of the normalised one causes considerable differences among specimens, as shown in (Fig. 6). In this picture, it is clear that a different sand type provides specimens with clearly different features in terms of colour, delayed hardening, greater moisture in the mixture and smooth surface (no pulverisation).
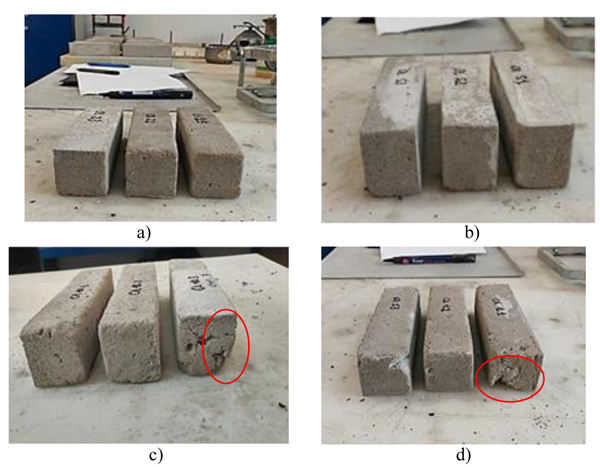
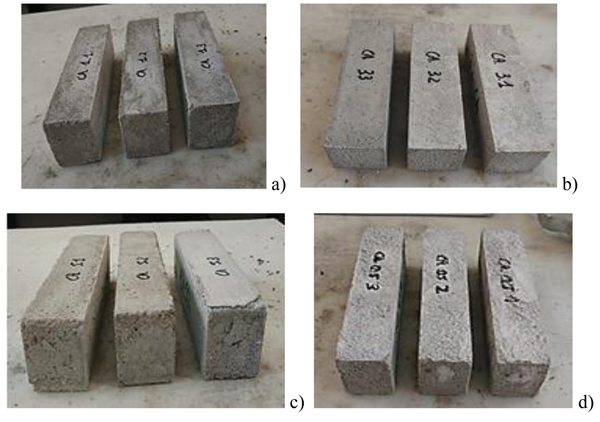
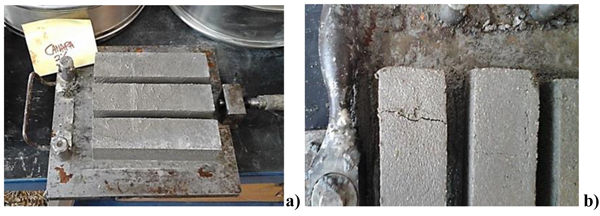
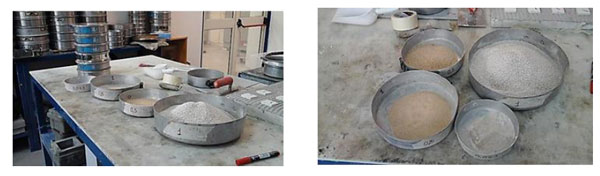
Subsequently, another set of specimens, without additives but with increased water able to saturate the hemp flour in the additive samples, is prepared. Based on the laboratory test results considering the hemp flour saturation, the maximum water percentage absorbed by hemp flour is equal to 125%. The new specimens are manufactured to individuate the limit value of added flour to be used, as well as to understand if the added flour concretely improves the mechanical performances of inspected cement mortars. In this case, the procedure follows the controlled melt of the normalised sand granulometric assortment. The components used for manufacturing the above described specimens are depicted in (Fig. 7).
The series of these new specimens contain an extra quantity of water, which would serve for the saturation of aggregates. Obviously, the addition of water inside the mixture causes, as a negative consequence, the reduction of the mortar mechanical properties. After packaging, the specimens are kept for 28 curing days before the discarding phase.
Subsequently, mechanical tests are performed on the three different series of the specimens above presented, namely samples with normalized sand, samples with commercial sand and samples with normalised sand and increased water replacing hemp flour as an additive component. In particular, for each percentage of added hemp flour, three samples are packaged. Bending tests are carried out on prismatic cement mortar specimens loaded in the middle with a concentrated force. Later on, the two halves of specimens broken under bending moment are subjected to compression tests.
The specimens manufactured for tests are shown in (Table 1), where the different experimental specimens are indicated by an acronym starting with a letter (N and C for normalised sand and commercial one, respectively) and followed by a number indicating the percentage of used hemp flour. For the last series of specimens, after the indication of the sand type, a further letter (W) is followed by a number specifying the additional water weight percentage put in the mixture to replace the hemp flour amount used in the other tests.
The achieved results, illustrated in the next section, are compared to each other in order to determine either the real improvement or the definitive deterioration of mechanical resistances due to the presence of the flour additive.
3. RESULTS AND DISCUSSION
The bending failure of additive specimens is of brittle type (Fig. 8) because, differently from lime or cement bio-composites manufactured with hemp fibres [7-13], the hemp flour, as an additive, has not a sewing function of cracks caused by the applied moment. The two halves of the prism obtained from the bending test are then subjected to compression tests with pressure applied on the lateral faces having a cross-section of about 40 mm x 40 mm (Fig. 9).
Once the tests are carried out, the bending failure stresses of specimens are computed, as shown in Figs. (10-12), where the mechanical performances of the three different groups of specimens are depicted. In these pictures, depending on the value achieved from tests, the stresses are labelled with maximum, intermediate and minimum terms.
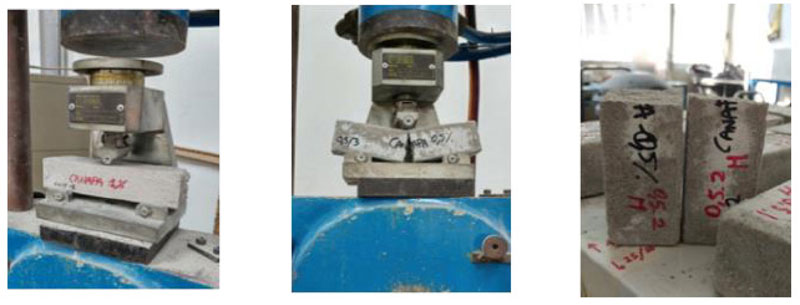
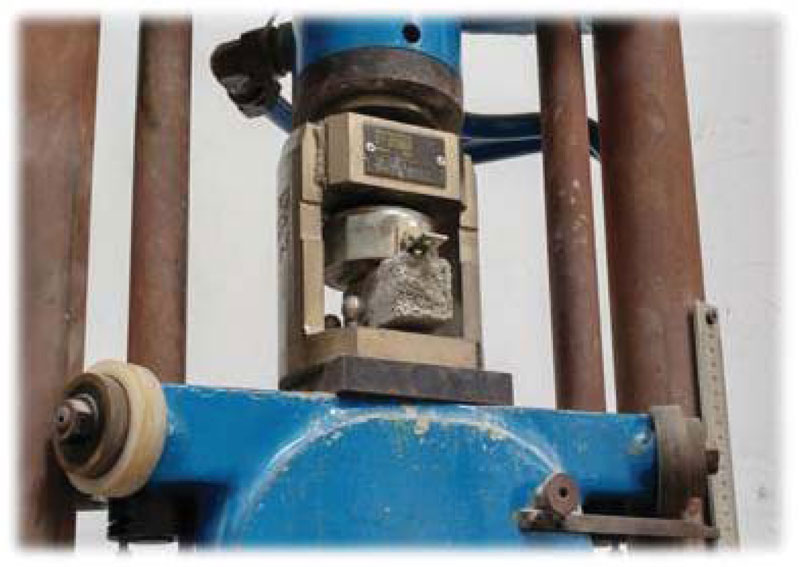
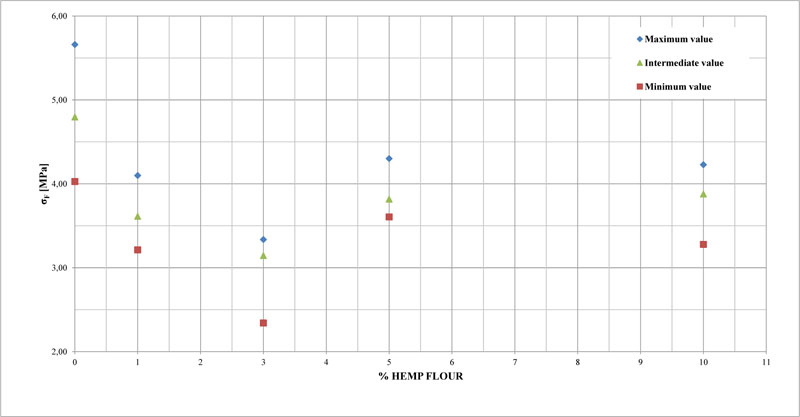
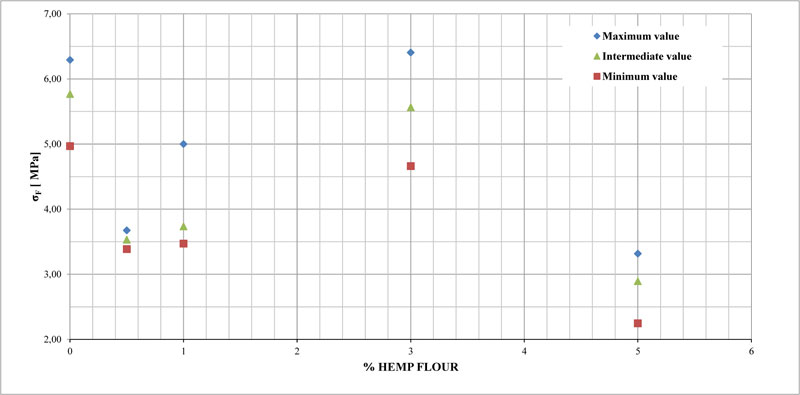
On the other hand, in Figs. (13-15), the compression failure stresses achieved from performed tests are respectively shown for samples with normalized sand, samples with commercial sand and samples with normalised sand and increased water replacing additives.
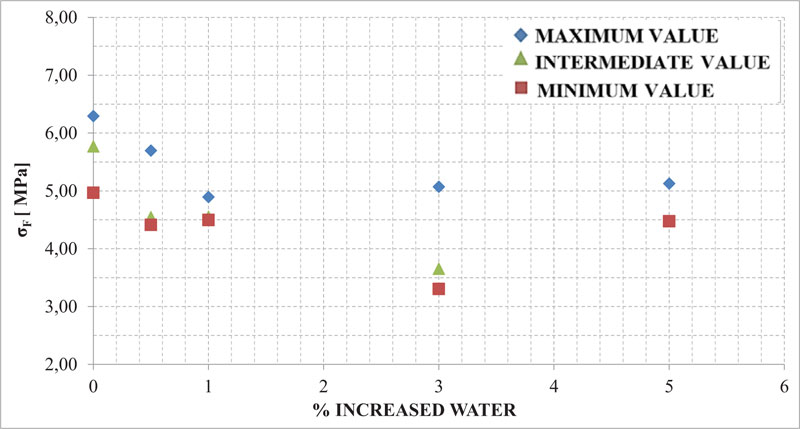
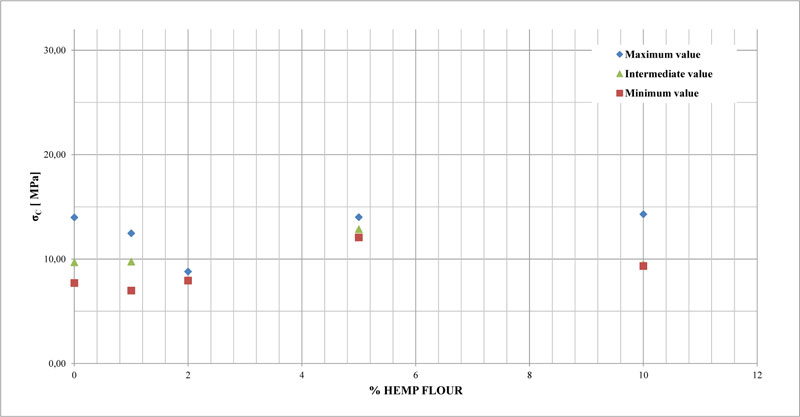
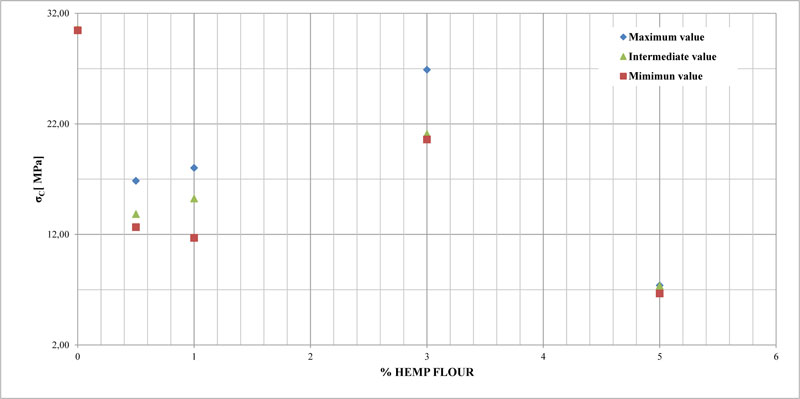
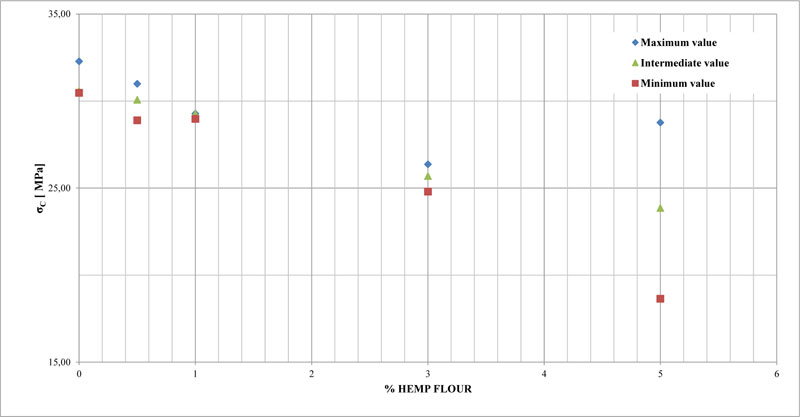
From the analysis carried out on the single groups of samples, an improved strength of mixtures made of normalised sand and 3% of hemp flour, compared to that of original samples, is noticed. Nevertheless, exceeded the limit value of 3% of additives, a sudden decline of the mechanical performances of additive cement mortars in terms of bending and compression stresses is observed. On the other hand, samples packaged with normalised sand and increased percentages of water, if compared to the corresponding original samples manufactured with hemp flour, show lesser mechanical performances. A better comparison of results is shown in (Table 1).
Specimen | Type of Sand | Hemp Flour (%) | Average Stress (MPa) | |
Bending Moment | Compression | |||
N0 | Normalized | / | 5.68 | 31.11 |
N0.5 | Normalized | 0.5 | 3.53 | 14.45 |
N1 | Normalized | 1 | 4.07 | 14.99 |
N3 | Normalized | 3 | 5.54 | 22.86 |
N5 | Normalized | 5 | 2.82 | 7.14 |
C0 | Commercial | / | 4.83 | 10.46 |
C1 | Commercial | 1 | 3.64 | 9.73 |
C3 | Commercial | 3 | 2.94 | 8.24 |
C5 | Commercial | 5 | 3.91 | 12.98 |
C10 | Commercial | 10 | 3.80 | 11.05 |
N0 | Normalized | / | 5.68 | 31.11 |
NW0.5 | Normalized | / | 4.89 | 29.99 |
NW1 | Normalized | / | 4.65 | 29.16 |
NW3 | Normalized | / | 4.01 | 25.62 |
NW5 | Normalized | / | 4.79 | 23.75 |
By analysing separately the average results obtained from tests, it appears that:
- For the same percentage of added hemp flour, by comparing specimens made of normalised sand and 3% of flour with those manufactured with commercial sand, the former has flexural mechanical stresses about 40% greater than the latter. Differently, by increasing the percentage of hemp flour, both specimen types have exhibited a sudden strength decrease.
- The comparison in terms of compression tests has shown that the mechanical stresses of normalised sand specimens are greater than those of commercial sand specimens. This occurs up to 3% of hemp flour added in the mixture.
- When bending tests are of concern, for both group of specimens, a reduction of flexural stress in comparison to that of the “as are” samples has been noticed. Nevertheless, the minimum stress decrease has been attained with 3% of hemp flour, with a strength reduction of about 2% and 19% when normalised sand specimens and commercial sand ones have been considered, respectively.
- If the comparison is made for each single set of specimens subjected to compression tests, for normalised sand specimens, a decrease of mechanical stresses as the hemp flour percentage increases has been detected. These specimens exhibit the lowest stress reduction (about 26%) in comparison to the “as are” samples one, when they are packaged with 3% of hemp flour. Contrary, for commercial sand specimens, up to 3% of hemp flour, a reduction of the compression stress of about 20% with respect to the original sample one has been observed. Instead, when the percentage of hemp flour is greater than 3%, the compression stress is larger than that of the “as are” specimens. In particular, the maximum stress growing (about 24%) has been attained with a sample manufactured with 5% of hemp flour.
- In order to evaluate the influence of hemp flour in the mixture, the results of tests on normalised sand specimens have been compared to those performed on specimens without sand, but with additional quantities of water absorbed by flours in the other doughs. From this comparison, only by using 3% of hemp flour, a significant increment (about 40%) of the bending moment stress and a slight reduction of the compression stresses (about 10%) have been occurred.
Finally, hemp flour in the measure of 3% of the cement weight has entailed a gradual improvement of the mortar flexural properties due to the binder property of the starch. Nevertheless, considering that the water/binder ratio is increased to take into account the water absorption of the hemp flour, a reduction of the compression stresses has been noticed. This occurs since hemp flour, after the starch binder power is exploited, behaves like inert material, thus reducing the compactness and resistance of the solid matrix. However, it has been noted that this reduction is less marked when 3% of hemp flour is used. Therefore, as a general conclusion of the performed experimental campaign, it can be said that 3% is the best percentage of hemp flour to be added to the cement mortar mixture in order to improve its bending failure stress without reducing seriously its compression resistance.
Further developments of the research will evaluate the possible benefits deriving from the use of hemp flour on the compression stress of sustainable cement conglomerates [14, 15], where the presence of gravel can assure mechanical performances higher than those of cement mortars.
CONCLUSION
In the paper, an experimental activity on cement mortar specimens manufactured with hemp flour as an additive component has been presented and discussed. Three different series of specimens, namely samples with normalized sand, samples with commercial sand and samples with normalised sand and increased water replacing the presence of flour, have been packed and tested. The first two groups of specimens have been manufactured with a variable percentage of hemp flour from 0.5% to 10%, whereas in the last series of samples, an added water percentage has been taken as a variable from 0.5% to 5%.
Firstly, the physical properties of the manufactured mortars have been investigated. In particular, considering that hemp flour remains trapped in the matrix in a latent way, it has been interesting to evaluate the rheological effects of doughs to establish if the flour remains active within the dough or behaves as an inert component. Compared to the use of hemp fibres, which the water initially absorbed must necessarily move away later for, causing the presence of a more porous matrix, the use of hemp flour, which is reagent with water, minimizing this effect. High percentages of hemp flour, in combination with fine sand, give rise to large decays of bending and compression failure stresses. This presupposes a clear change in the properties of the basic matrix. If, on the one hand, reduced hemp flour percentages do not provide an effective improvement of the mortar specimen strength, an excessive amount of hemp flour becomes an inert component, to reduce the compactness and resistance of the additive mortar matrix.
Later on, mechanical compression and bending tests have been carried out on the investigated specimens to evaluate the possible benefits deriving from the binder effect of the hemp flour due to the presence of starch in its microstructure. The aim of this experimental campaign was to understand what is the hemp flour percentage to be used to improve the mechanical performances of tested mortar samples. From experimental tests, it has been noticed that specimens made of normalised sand and 3% of hemp flour have flexural mechanical stresses about 40% greater than those manufactured with commercial sand. In particular, in bending moment tests, the performance of additive specimens has been worse than that of “as are” specimens. Nevertheless, the minimum stress decrease is attained with 3% of hemp flour, when a strength reduction of about 2% and 19% with normalised sand specimens and commercial sand ones, respectively, has been detected. On the other hand, also in compression tests, the same outcomes achieved from flexural tests have been detected. More in detail, a decrease in mechanical stresses has been noticed as the hemp flour percentage is increased. Specimens made of different percentages of hemp flour and packaged with either standardised sand or commercial sand have exhibited similar stress reductions compared to those of “as are” specimens. Contrary, when 5% of hemp flour has been used within doughs, the maximum stress growing of 24% with respect to the strength of “as are” specimens has been attained. In conclusion, the best mix design is that given by standardised sand and 3% of hemp flour. In fact, for specimens made of these constituents, a significant increment (about 40%) of the bending moment stress and a slight reduction (about 10%) of the compression stresses have been detected from laboratory tests.
The experimentation performed will lead towards numerous and interesting future developments. First of all, there is a need to identify the limit percentage of hemp flour to be added to the mixture, so as to avoid the decay of the mixture mechanical properties. Given the satisfactory results, further experiments must be carried out on cement conglomerates, where the presence of gravel can surely improve the stability and mechanical resistance of the cement matrix.
CONSENT FOR PUBLICATION
Not applicable.
AVAILABILITY OF DATA AND MATERIALS
The authors confirm that the data supporting the findings of this study are available within the article.
FUNDING
None.
CONFLICT OF INTEREST
The authors declare no conflict of interest, financial or otherwise.
ACKNOWLEDGEMENTS
None.