All published articles of this journal are available on ScienceDirect.
Utilisation of Plastic Waste as Synthetic Fiber and Aggregate in Concrete – A Review
Abstract
Plastic waste materials are non-biodegradable and therefore require safe and economic disposal to have a green environment. The use of plastic waste in the construction industry holds a big potential to minimize the global environmental burden. For this purpose, a comprehensive review of published research works was done that disclosed the use of plastic waste materials, like polypropylene (PP), high-density polypropylene (HDPE), and polyethylene terephthalate (PET), in concrete as partial or full replacements for cement and aggregates. This paper has reviewed various properties, like workability, compressive strength, split tensile strength, flexural strength, temperature effect, elastic modulus, drying shrinkage, carbonation, and structural behavior of concrete with stated plastic waste materials. The review revealed that the strength, durability and structural characteristics of such concrete improved while the workability was reduced. The review gave information that the footpath panels with HDPE, PP and PET fibre can be used as a substitute for steel-reinforced panels. The review also indicated that further detailed investigations on various strength and durability properties are required on concrete made using plastic wastes like HDPE, PP, and PET with various aspect ratios.
1. INTRODUCTION
1.1. Plastic Wastes used as Aggregate Replacement
Plastic wastes are non-biodegradable, and due to this, several negative impacts are caused on the environment, like soil pollution, air pollution, carcinogenicity and animal death. Dalhat and Wahhab [1] investigated recycled high-density polyethylene and recycled polypropylene thermoplastic polymers bounded concretes and compared them to asphalt concretes and Portland cement concretes. The plastics were processed and crushed to achieve the desired sizes, starting from 2.38 mm. Recycled high-density polyethylene-bounded concrete with no fine aggregate possessed compressive load resistance of similar magnitude to that of asphalt concretes. Recycled polypropylene-bounded concrete exhibited compressive strength three times more than asphalt and comparable to Portland cement concretes. The strength of pure PP was higher than that of pure HDPE. Morgan et al. [2] reported that the global annual generation of plastic waste is more than 300 million metric tons as of 2014, and it is expected to keep rising. Some countries reuse a plastic waste maximum of 50%, and in most countries, 90% of plastic waste ends up in landfills. Rahmani et al. [3] analyzed the reinforced concrete with PET bottles waste fibers and found that adding a little amount of recycled fibers from PET bottle wastes can have a great influence on the post-cracking performance of simple concrete elements. Asokan et al. [4] reported that plastic fibers could effectively improve post-cracking performance and control the drying shrinkage of concrete. Glass Reinforced Plastic waste powder and fiber usage in concrete and cement composites improve quality. As per Cengiz et al., flexural ductility, ultimate load capacity, and toughness improved significantly [5], while plastic shrinkage improved [6] upon the use of high-performance polypropylene fiber. The various properties of concrete got improved with the use of PET [7, 8] and synthetic fiber [9-11]. A good number of experiments have been conducted to know the effect of the usage of various plastic fibers in concrete, like polyethylene terephthalate particles [12, 13], synthetic fiber [9, 10, 14], PP [15-17], nylon fiber [18], recycled granulated waste plastic [1], mac matrix fiber [19], and GRP waste powder [20]. Shi Yin et al. [21] reported that plastic waste fibers could control plastic shrinkage and drying shrinkage of concrete. The usage of plastic waste fibers in precast elements [22], concrete foot-paths [23], and shotcrete has also been reported.
The objective of this review was to critically focus on the results obtained by various researchers after introducing waste plastic in various forms to concrete. The review revealed the fact that the fibers slightly enhance the performance of the fresh and hardened concrete but reduce the workability. The surface treatments of the plastic with a cognizant material, like slag, silica fume, and metakaolin, improve the strength of the cement concrete due to the pozzolanic reaction. The various forms of plastics added to or replaced with different constituents of concrete and their field applications are presented in Table 1 [24, 25].
1.2. Preparation and usage of Fiber
Yap et al. [18] investigated the effect of adding i) fibrillated PP and ii) multi-filament PP with 3 volume fractions of 0.25, 0.50 and 0.75% in oil palm shell fiber-reinforced concrete with 0.65% superplasticizer by cement weight. Asokan et al. [4] investigated using GRP waste fiber 20 mm in length and powder 2 mm. Corinaldesi et al. [26] utilized glass fibre-reinforced plastic waste with limestone powder and wood waste. Yin et al. [27] utilized recycled PP fibres 6 kg/m3 in M-25 and M-49 grades of concretes. Ruiz-Herrero et al. [28] made PP fibres of diameter 0.8 to 0.9mm by melt spinning and hard drawing process. Yin et al. [21] extruded the fibre of length 47 mm by spinning at 210–250 LC, stretching at 140–170 LC, and stabilizing at 110–130 LC. He used roller die for diamond and line indents on fibres. Karahan and Atis [29] utilized 0, 15 and 30% fly ash on a mass basis and PP fiber 0, 0.05, 0.10 and 0.20% on volume basis. Rahmani et al. [30] and Donkor and Obonyo [19] used PET particles 5, 10 and 15% as sand replacement, while Zheng et al. [31] and Cengiz et al. [5] used PET fibers in mortar. Kim et al. [32] compared PET fiber with polypropylene of 0.5, 0.75, and 1.0%. Luiz et al. [33] utilized fibers cutting from bottles 0, 0.5, 1.0 and 1.5% in cement-lime mortar. Yin et al. [21] utilized fibers of 1–2 mm diameter PET granules extruded and hot drawn at a temperature of 70–150 LC. Fraternali et al. [34] used PET fibers embossed, straight and crimped and PP fibers of 40 mm, 47 mm, and 52 mm. Islam et al. [35] prepared PET coarse aggregate by melting the PET bottles in an oven at 280 LC and 320 LC and utilized 0-40% with coarse brick aggregate. Foti [36] worked with PET bottles 0.5 and 0.75%, while Liguori et al. [37] reported on the use of polyolefin and polyethylene terephthalate plastic aggregate at 10-20% replacing silica powder. Sadrmomtazi et al. [38] investigated using PET aggregates 5-15% and fly ash 10.0-30%. Kavas et al. [39]. worked on plastic fiber and 10% sepiolite (a natural clay mineral) fibers, while Zheng et al. [31] worked on steel fiber and PP fiber. Naik et al. [40] reported on HDPE treated with water, bleach, bleach with sodium hydroxide separately, 0-5% of concrete by weight, passing through a 3/8 inch sieve. Shwan and Razak [41] used 12 mm length polyethylene fibers of 1-2.5% volume fractions. Liu et al. [42] used polyester resin and quartz as binding and filling materials. Rao et al. [43] added recycled high-density polyethylene (rHDPE) plastic fibres at six mix variations like 0, 0.3, 0.4, 0.5, 0.6, and 0.7% in concrete and concluded that the application of rHDPE has no significant effect on the results of compressive strength, but it significantly improves the splitting tensile and flexure strength. Rao and Patro [44] investigated the behaviour of HDPE at high temperatures on the mechanical characteristics of HDPE fiber-reinforced concrete. The authors reported that the melting of the HDPE fibres during heating causes modest changes in the residual compressive strength, elastic modulus, and splitting tensile strength.
The mechanical shredder used for the cutting of fibres, as reported by Borg et al. [12], is shown in Fig. (1); the manufacturing process of PET fiber, as reported by Kim et al. [7], is presented in Fig. (2), and the cutting of R-PET fibre from bottles, as reported by Fraternali et al. [45], is presented in Fig. (3). Fig. (3a) shows the bottle, Fig. (3b) shows the cutting, and Fig. (3c) shows fibres. Different types of plastic fibres used in the past studies are presented in Fig. (4a) [46-51].
Authors’ Name/Refs | Mode of Plastic Waste Utilized | Size of Fiber | Utilized in Concrete as a Replacement of | Used in Concrete/Mortar as an Inclusion | |
---|---|---|---|---|---|
Cement | FA/CA | ||||
Asokan et al., 2009 [4] | GRP ground sample | 500 µm - 2 mm | GRP waste fiber | FA 5- 50% | - |
Cengiz and Turanli, 2004 [5] | High-performance PP fiber, steel | Length-30mm, Dia-0.6 mm and aspect ratio 50 | - | - | The fiber at 7 and 10 kg/m3 i.e, 0.78% and 1.1% of 1 m3 of shotcrete. |
Alberti et al., 2016 [24] | Polyolefin fibers | Length - 60mm and Dia-0.6 0.903mm | - | - | 3 - 10% kg/m3 of concrete. VCC and SCC |
Pelisser et al., 2010[25] | PP and PET | - | - | - | Inclusion of PP, PET, glass, and nylon fibres. Short PP fibers to the mortar mixture |
Kim et al., 2008 [7] | PET fibers | Length-50mm | - | - | CM 1:2, w/c 0.55, PET straight, crimped, embossed fibers 0.10, 0.25,0.5,0.75 and 1.0% |
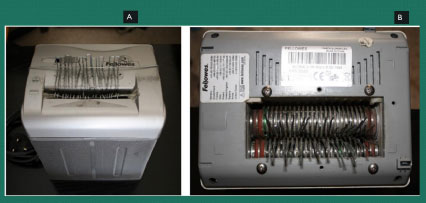
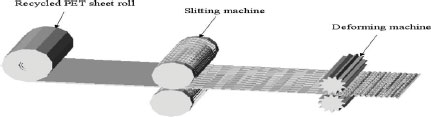
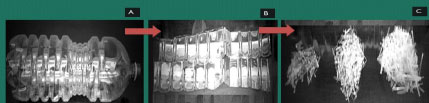
1.3. Effects of Replacement/Inclusion of Plastic Fiber
Saikia and Brito [22] described the inclusion of waste plastic aggregate in concrete to show many negative effects on workability and mechanical behavior. The authors reported a reduction in the modulus of elasticity and strength of concrete containing plastic aggregates in comparison to concrete made with natural aggregates. Less hydration of cement and poor bonding of cement paste with plastic aggregate are the reasons for the poor properties of concrete containing aggregate made with plastic. Remedies suggested by Saikia and Brito [22] are chemical treatments. Slag and sand powder coating improves the mechanical properties of concrete since it improves the cement paste interaction. Zheng et al. [31] reported hybrid fiber to show great resistance to elevated temperature. Pujadas et al. [11] reported that the tendency of the orientation of plastic fibers is parallel to the walls of the formwork, and in free surface flow, it is perpendicular to the direction of the flow. Saikia and Brito [52] reported that because of the sharp edges, angular shape and non-absorbent properties of plastic aggregate, the slump value increases in concrete containing plastic aggregates. Yin et al. [53] reported more spalling resistance in polypropylene fiber concrete [42], while Fraternali et al. [45] reported better alkali resistance in concrete using PET.
2. METHODOLOGY
The use of three types of plastic waste materials, namely polypropylene (PP), polyethylene terephthalate (PET), and high-density polyethylene (HDPE), in concrete and their performances were reviewed in this work. A total of 89 papers published in various international journals of repute was studied and summarized.
Tools for data collection were based on some characteristics of concrete, such as fresh properties, mechanical properties, durability and microstructural condition. The aspect ratio of plastic waste materials was another tool for data collection. Primary data were collected using the aforesaid tools separately for each type of plastic waste material of different aspect ratios. Data were collected on various physical properties, such as specific gravity, melting point, tensile strength ignition point, elongation, surface texture, etc., of PP, PET and HDPE. Data were also collected on the behavior of PP, PET and HDPE when used in various mix proportions of concrete.
Data analysis was carried out using the grounded theory method. Under this method, the collected data were coded first and the coding of data was done in three phases, such as open coding, axial coding, and selective coding. Under open coding, collected data were read several times and summarized using preliminary levels. Then axial coding was done by creating families from the summaries. Thereafter, selective coding was done by converting the families to a formal network with a variable. The variables of the study were workability, compressive strength, split tensile strength, flexural strength and modulus of elasticity, freezing and thawing, carbonation, permeability, drying shrinkage, temperature effect and scanning electron microscopy of concrete using PP, PET, and HDPE.
3. PHYSICAL PROPERTIES OF PLASTIC WASTES AS AGGREGATE
The various properties, like specific gravity, melting point, Young’s modulus, tensile strength, ignition point, elongation at break, surface texture, the temperature at vaporization, density and aspect ratio of PP, PET and HDPE as reported by authors of the past are presented in Table 2 [55]. Specific gravity is for PP and HDPE is less than one and just more than one for PET. As the specific gravity of plastic aggregate is very less than granite aggregate, the concrete will become lightweight by replacing the granite coarse aggregate with the plastic aggregate. As Young’s modulus reduces, the strength decreases but the ductility property of concrete increases. The aspect ratio from 33 to 108 has been used by various researchers. Ball formation of fiber in concrete occurs as the aspect ratio increases. Tensile strength of concrete increases by creating a good bond between concrete made of PP and PET in comparison to that of concrete made of HDPE. The density of nylon, as reported by Foti [54], has been found to be 1.14g/ cm3. Several researchers have studied the effect of waste plastic in different forms and different lengths, either by replacing with or adding to various ingredients of concrete and mortar. The strength of plastic fiber concrete increases with improvement in the bond between fiber and concrete.
4. MIX PROPORTION OF PLASTIC WASTE-BASED CONCRETE
Selected mix proportions of plastic-waste-based concrete are presented in Table 3. Researchers have used different target strengths from 20 MPa to 51.6 MPa by adopting different cement types, plastic-waste types, replacement levels of aggregates, and water-cement ratios. The authors [57] here followed various codes, such as ACI 211.1, AASHTO M 323-12KCI [57], BS 12:1996 [58], US State and local building codes [19], Design of Concrete Structures code in China [58], US State and local building codes [19], and IS 10262: 2009 [59] have been followed by different researchers [51, 56] for mix proportioning the plastic-waste concrete. Researchers [7] targeted the strength of M25, M30 and M35 by replacing 100% of cement with PP [1], with a maximum of 1% aggregate [3] in concrete. Asokan et al. [4] followed the British standard (BS 12:1996) for proportioning GRP-based concrete, replacing the GRP from 5-50% of fine aggregate with a w/c ratio of 0.5-0.71 with superplasticizer of 2% to maintain the workability. Zhang and Li [60] studied the durability properties, like carbonation, water permeability, freezing, and thawing, using Chinese standards and ASTM by using OPC (Class 42.5R) concrete 1:1.657:2.949 with water cement ratio of 0.4 with the inclusion of 0.06-0.12% PP fiber.
Properties | PP [55] | PET [34, 36] | HDPE [56] |
---|---|---|---|
Specific gravity | 0.90–0.92 | 1.11 | 0.93-0.96 |
Melting point(LC) | 150-179 | 62 | 129-140 |
Young’s modulus (GPa) | 1.2-10, | 3.1-10.2 | 5-1.1 |
Tensile strength (MPa) | 284.1-750 | 250-550 | 30-60 |
Ignition point (LC) | Over 450-460 | 252.8 | 480-500 |
Elongation at break (%) | 6.2-15 | 11-29 | 28-180 |
Surface texture | Continuously embossed | - | - |
Temperature at vaporization (oC) | 341 | - | 430-480 |
Density (g/cm3) | 0.85-0.930 | 0.464-1.38 | 0.93-0.96 |
Aspect ratio | 40-108 | 33-70 | 75-92 |
Article/Refs | Code | Grade of Concrete / Mix Proportion | Type of Binding Material Used | Plastic-waste used | SP* (%) | w/c Ratio | Aspect Ratio / Dimension | |
---|---|---|---|---|---|---|---|---|
Name of Plastic Waste | Replacement of Aggregate (%) / Inclusion | |||||||
Zhang & Li, 2013 [60] | Standards of China | 1:1.657:2.949 | OPC (Class 42.5R) | PP | 0.06%, 0.08%, 0.1% and 0.12% inclusion | 0.2% | 0.4 | Length= 10-20mm |
Medina et al., 2014 [6] | Spanish concrete code | 1:2.547:3.141 | Cement II/B-P 32.5R | PP | 0.03%, 0.06%, 0.09%, and 0.12% | - | 0.4,0.5, 0.6 |
Length= 19mm |
Cengiz, Turanli, 2004 [5] | - | M35/ 1:1.812:0.98 | PC 42.5, ASTM Type I | High performance PP | 0.45% and 0.64% of 1 m3 | 0.42% | 0.41 | 50 |
Dalhat, Wahhab, 2016 [1] | AASHTO M 323-12 | M30 | OPC AND ASPHALT | PP & HDPE | 100% by volume & by weight of cement | - | 0.36 | - |
Behfarnia, Behravan, 2014 [14] | ACI 211.1 | M30 | PC-II | HPP &steel | 0.8,0.6,0.4 | 0.17% | 0.59 | 52.34, 53.33 |
Zheng et al., 2012 [31] | Design of concrete structures in China | M20 | OPC-Grade 42.5 (Chinese ) | STEEL&PP | (2%, 0.1%), (2%, 0.2%) and (1%, 0.2%) | 0.058 | 0.29 | Length= 18-20mm |
Yap et al., 2013 [18] | ASTM C143/C143M-12 | 1:1.83:0.604 | OPC | PP and Nylon, oil palm shell | 0.25%, 0.5%, 0.75% inclusion | 10% Silica Fume | 0.3 | 47.5, 240, 63.3 |
Yew et al., 2015 [61] | ASTM | 1:1.846:0.635 | OPC | PP, PP Twisted Bundle | 0%,0.25%, 0.375%, 0.5% | 1% | 0.3 | 108, 60, 40 |
Song et al., 2005 [62] | - | 1:2.83:3.5 | Type I Portland cement | PP+Nylon | 0.6%+0.6% | - | 0.646 | 19mm length |
Asokan et al., 2009 [4] | BS 12:1996 | 1:1.744:2.907 | OPC | GRP | 5%, 15%, 30% and 50% (w/w). | 2 | 0.5 TO 0.71 | 10 |
Pesic et al., 2016 [56] | ASTM C1579-13 standard | 1:2.05:2.316 | CEM II/A-L 32.5 R | HDPE | 0.4%, 0.75%, 1.25% | - | 0.62 | 92, 75 |
Yin et al., 2015 [53] | ASTM C1550-12 | M40 / 1:3.359:3.711 |
OPC | HDPE | 0.45% | 3.36% of Cement | 0.41 | 52, 47mm length, 0.8-0.9 mm diameter |
Saikia, Brito, 2013 [52] | Euro code 2 | 1:2.29:2.8 | CEMIIA-L42.5 R type cement | PET | 0%,5%,10%and15% | - | 0.53 | Fine aggregate |
Kumar, 2014 [63] | IS: 10262- 2009 | M25 | PPC | polythene | 0.5%,0.75%,1% | 0.4% | 0.44 | - |
Yin et al., 2015 [53] | ASTM C1550-12 | M40 / 1:3.359:3.711 |
OPC | line and diamond indents PP | 0.45% | 3.36% of Cement | 0.41 | 52, 47mm length , 0.8-0.9mm diameter) |
Karahan, Atis, 2011 [29] | TS-EN 12350-2 | 1:4.742 | OPC | PP (15.0% and 30.0% fly ash ) | 0%,0.05%, 0.1%,0.2% | 1% of Cement | 0.35 | - |
5. FRESH PROPERTIES OF CONCRETE
5.1. Workability
The ease and homogeneity of freshly mixed concrete are called workability. Workability can be achieved by the inclusion of admixture in waste plastic concrete. The plastic fibre affects the quantity of free water, and consequently the workability.
Waste plastic reduces the workability of concrete. Saikia and Brito [64] and Mazaheripour et al. [55] suggested that workability can be increased by using fibers less than 1% and with the inclusion of a plasticizer. Yang et al. [46] utilized recycled modified polypropylene (PP) plastic particles at 10-30% of sand by volume and reported that the slump flow value improves with an increase in the sand quantity in self-compacting concrete. Karahan and Atis [29] reported that polypropylene fiber decreases the workability of concrete. An increase in aspect ratio decreases workability [65]. Fig. (4b) shows slump test values of plastic FRC. The test values show that the presence of plastic fibers decreases slump, and as a consequence of this, the workability of fresh concrete also decreases. The formation of network structure by the fibers in the concrete lowers the flow.
Yap et al. [18] have added i) fibrillated PP and ii) multi-filament PP with 3 volume fractions of 0.250%, 0.500%, and 0.750% in oil palm shell fiber-reinforced concrete with a poly-carboxylate based superplasticizer of 0.65%. Fibrillated PP showed higher workability when compared to multi-filament PP, and workability decreased with the increase of fiber from 0.25-0.75%. Zhang and Li [60] reported that there is a decrement in the slump of concrete by 7% in which 0.12% PP, 15% fly ash, and 6% silica fume were added.
Zhang and Li [60] added four different fiber volume fractions of PP fiber 0.06, 0.08, 0.1, and 0.12% with 15% fly ash, 6% silica fume, and 4.94 kg/m3 water reducer. The result showed a little reduction in workability with an increase in the percentage of fiber from 0.06 to 0.12. Rai et al. [66] investigated concrete of M-30 with w/c of 0.44, which partially replaced sand 0-15% by waste plastic flakes, and concluded that the workability increases by about 10-15% when superplasticizer is added. Yew et al. [61] opined that polypropylene fibers volume fractions of 0.25-0.5% are included in oil palm shell fiber-reinforced concrete with various aspect ratios and geometry. The slump value was reduced from 180-80 mm as the volume fraction of fiber increased from 0-0.5%. The twisted bundle showed a higher slump compared to straight fiber.
Karahan and Atis [29] studied using 0-0.2% along with fly ash 0%, 60 kg/m3, and 120 kg/m3. Workability has improved with the rise in the quantity of fly ash content from 0 kg/m3 to 120 kg/m3 and reduced with an increase of volume fraction of PP fiber. Overall observation workability improved with the inclusion of fly ash along with silica fume and low volume fraction of fiber.
6. HARDENED PROPERTIES OF CONCRETE
6.1. Compressive Strength
The strength of concrete is generally understood as its compressive strength. To know the effect of the inclusion of waste plastic in concrete, it is essential to know the compressive strength of the normal and modified concrete when waste plastic is used to replace the ingredients of concrete. The testing methods as suggested in ASTM C 109, ASTM C 109C and EN 12390-3 have been mainly used in previous studies for the determination of compressive strength.
6.1.1. Effect of Polypropylene
Arreola et al. [68] reported an interesting behavior that the greater the amount of polymer, the slower the hardening of cement and poor interaction in the cement matrix. They also reported that compared to controlled concrete, there is a huge reduction in compression strength. Singh et al. [69] and Sharma et al. [65] suggested mechanical indentations on the surface of PP fibers to avoid low bonds with the cementitious matrix. Kumar [62] reported that with the increase in polythene bag fibers, workability reduced and compressive strength increased up to 0.75%. Peyvandi et al. [70] reported higher compressive strength to be shown by steel fiber with polypropylene. Yap et al. [18] reported a decrement in compressive strength of hardened concrete by 31.31% and 55%, in which fibrillated PP and multi-filament PP were added, respectively, by 0.75%. Yew et al. [61] reported an increment in compressive strength of concrete by 14.8% and 14.1% in which 0.5% monofilament-PP twisted bundle and 0.5% monofilament-PP straight were added, respectively, into oil palm shell fiber reinforced concrete. Karahan and Atis [29] concluded a deterioration of 2.9%, 6.4%, and 2.2% in compressive strength when 0.2% PP was used with 15, 30 and 60% of fly ash as cement replacement. Afroughsabet and Ozbakkaloglu [16] studied the effect of the inclusion of 12-mm length PP fibers at 0.15%, 0.30%, and 0.45% with 10% silica fume as a cement replacement in high-strength concrete. The inclusion of 0.45% fiber showed an increase of compressive strength by 8%, 13%, and 14% at 7 days, 28 days and 91 days, respectively, as compared to controlled concrete.
Mazaheripour et al. [55] added 12 mm length PP fibers of 0%, 0.1%, 0.2%, and 0.3% and reported no increase in compressive strength and elastic modulus of lightweight self-compacting concrete. Altun and Dirikgil [71] studied the temperature effect at 24.5, 100, 200, 400, 600, and 800 LC at polypropylene volumetric ratios of 0.0%, 0.1%, 0.2%, 0.3%, 0.4%, and 0.5% in M40 grade concrete at 7, 28, and 90 days, respectively. They reported 0.4% fiber to be effective at lower 200 LC temperatures, and at higher values of 400 LC temperatures, they reported compressive strength to decrease with an increase in the fiber ratios beyond 0.4%. Ruiz-Herrero et al. [72] investigated mortars with polyethylene and PVC waste of electric cable at 0%, 2.5%, 5%, 10%, and 20% added to the mortar. Donkor and Obonyo [19] investigated compressed earth blocks using 0.20%, 0.40%, 0.60%, 0.80%, and 1.00% weight fractions of polypropylene fibers, and reported that at 0.4% fiber content, the compressive strength improved by 22.5%. The effect of PP on compressive strength is summarized in Fig. (5).
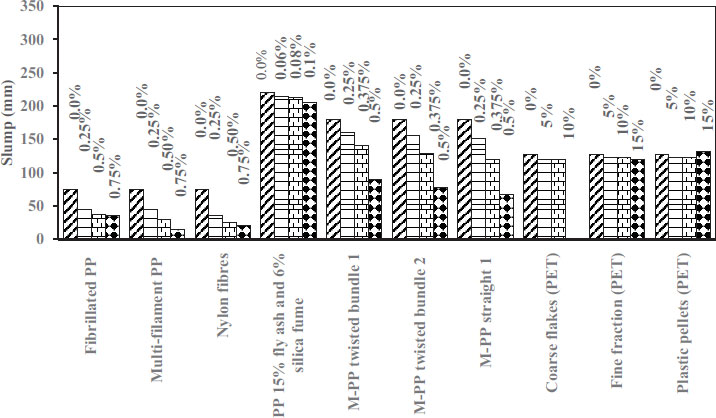
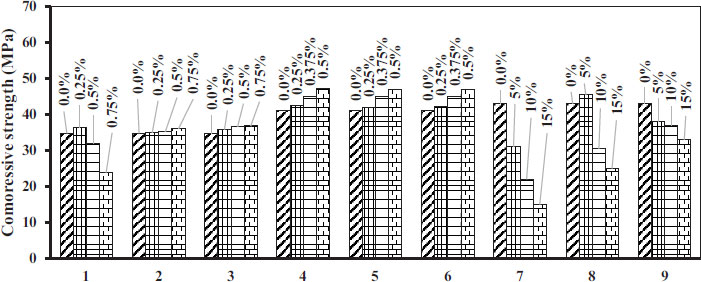
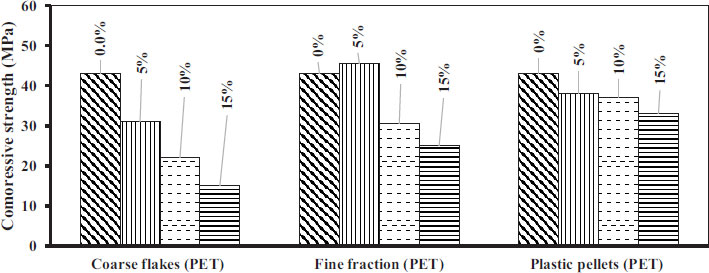
6.1.2. Effect of Polyethylene Terephthalate
Nikbin et al. reported lightweight concrete without PET to show better crushing strength than normal PET concrete [73] and recycled polystyrene [65]. 10-50% recycled plastic reduced compressive strength by 34% and 67% [74]. Asokan et al. [4] reported an increase in curing for 14–180 days; the compressive strength with 5% GRP increased to 45.75 N/mm2. They also reported that at 28 days, compressive strength increased by 45% with 5–15% GRP waste powder and 2% superplasticizer [20]. The effect of polyethylene terephthalate on compressive strength, as reported by the various authors, is summarized and presented in Fig. (6).
6.1.3. High-density Polyethylene
Figs. (7 and 8) show the compressive strength of HDPE fiber-reinforced concrete [39]. Naik et al. [39] used shredded and soaked HDPE small particles of an average 1 mm size as soft filler in the concrete of grade M35 at various dosages of 0.5, 1.5, and 2%. The authors soaked the fibres in water in a 5% bleach solution and 5% bleach + 4% NaOH solution. Alkaline bleach treatment (bleach +NaOH) showed good performance, and compressive strength decreased beyond the inclusion of 0.5% fiber. Rao and Ravula [75] investigated PET and HDPE fibre in concrete and concluded compressive strength and flexural strength to reduce and split tensile strength to increase, and PET pellets showed more reduction compared to HDPE fibre in concrete.
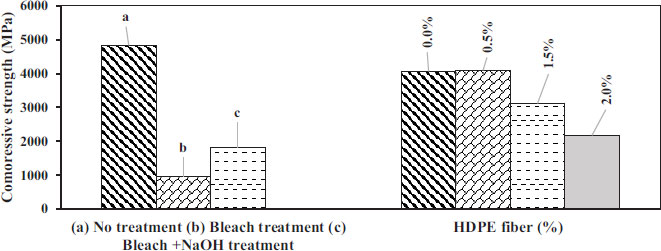
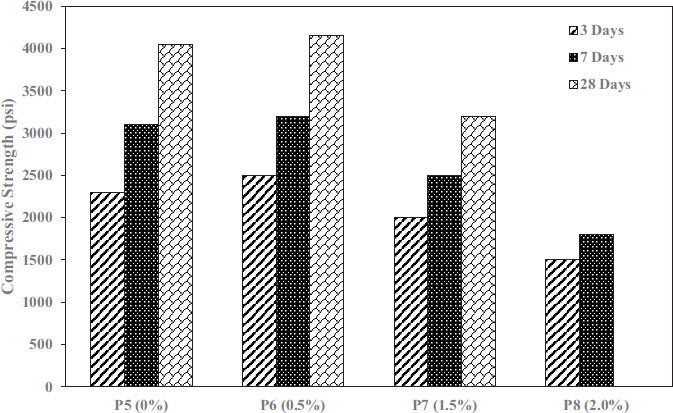
6.2. Split Tensile Property
To know the tensile property behavior, the indirect method, i.e.., split tensile test, is carried out as the direct measurement is difficult because truly axial load application is almost impossible in direct tension. The effect of plastic fiber in concrete on the tensile strength of concrete is described in the following sections. The testing methods, as suggested in EN 12390-3, have been mainly used in previous studies for the determination of splitting tensile strength.
6.2.1. Polypropylene
Afroughsabet and Ozbakkaloglu [16] concluded the inclusion of 0.45% fiber to show an increase of split tensile strength by 15%, 20%, and 16% at 7 days, 28 days, and 91 days, respectively. Rahmani et al. [3] reported PP fibers in concrete to increase flexural strength by 25% as compared to steel fibers. Yin et al. [65] reported virgin plastic to show higher tensile strength but lower flexural strength compared to recycled PP Fiber. Split tensile strength increased by 13%, 16%, and 20% for concrete containing PP fiber of 0.15%, 0.3%, and 0.45%, respectively, at 28 days [42]. Yew et al. [61] reported that the inclusion of PP Twisted Bundle1/0.25–0.5%, PP Twisted Bundle2/0.25–0.5%, and PP Straight1/0.250 –0.50% fibers increased the splitting tensile strength up to 8.0–33.0%, 10–27%, and 13–21%, respectively, compared to the normal one. Hesami et al. [17] added polypropylene fibers (0%, 0.1%, 0.12%, 0.15%), along with the partial sand replacement with Tire Rubber Crumb (TRC) (0%, 5%, 10%, and 15%) in self-compacting concrete. PP fiber of 0.15% with 0, 5, 10, and 15% TRC showed higher tensile strength by 27.96%, 26.14%, 27.42%, and 26.9%, respectively, compared to no fiber. Mazaheripour et al. [54] reported that the addition of 12 mm length PP fibers of 0%, 0.1%, 0.2%, and 0.3% increased the tensile strength by 14.4% of lightweight self-compacting concrete. Ghernouti et al. [49] reported that plastic bag waste fibers of 12 mm in length at 1, 5, and 7 kg/m3 increased split tensile strength value from 4% to 74% at 28 days when added to self-compacting concrete. The effect of PP on concrete is summarized and presented in Fig. (9).
6.2.2. Polyethylene Terephthalate (PET)
Rahmani et al. [3] investigated the effect of PET-processed particles (produced by grinding employing industrial machines) on 5%, 10% and 15% substitution of sand. When 15% of sand was replaced with PET particles, the w/c ratios of 0.42 and 0.54 showed 15.9% and 18.06% reduction in tensile strength, respectively.
6.3. Flexural Property
Flexural strength (FS) is the capacity to resist failure in the bending of a structural member. Three-point or four-point loading test is used to determine the FS of concrete. The effect of plastics in concrete on the FS of concrete is presented in the following lines. The testing methods, as suggested in EN 12390-5, have been mainly used in previous studies for the determination of flexural strength.
6.3.1. Polypropylene
Ruiz-Herrero et al. [28] described that the FS of concrete with 20% PP decreased three times at 28 days compared to control concrete. Ghernouti et al. [49] investigated the effect of plastic bag waste fibers of 12 mm in length and 1, 3, 5 and 7 kg/m3 in weight and reported that FS improved by 0-14% at 28 days. Yin et al. [65] investigated virgin and recycled PP fibers. Fibers with 0.8–0.9 mm diameter and line and diamond indents with indenting roller die were used to increase the fiber–concrete interaction.
Greater tensile strength but lower flexural strength was observed in the use of virgin PP fibers compared to recycled PP fiber. Mazaheripour et al. [55] added 12 mm length PP fibers at 0%, 0.1%, 0.2% and 0.3% and reported an increase in the flexural strength by 10.7%. Dalhat and Wahhab [1] reported that stiffness and flexural strength increased by 3 times of recycled PP-bounded concrete compared to Portland cement concretes. Banthia and Gupta [15] reported that PP fiber showed higher flexural strength and also good control over plastic shrinkage. Finer and longer fibers are more effective as compared to coarser and short fibers, but in SCC, the strength was not affected by the length of the fibers used [25]. Rai et al. [66] described the FS of waste plastic concrete to have lowered with the increase in the percentage of plastic waste. He also reported that the effect of plasticizers on the FS of concrete is irrelevant. Zhang et al. [76] reported that within 0.1% volume fraction, PP fiber had shown good resistance to crack propagation. Behfarnia and Behravan [14] and Medina et al. [6] described that the FS increased with PP fibre content up to 0.09% and decreased with an increase in fibre content. Rao [77] investigated an effect of micro silica on waste plastic concrete and found flexural strength to be increased on 10% addition of micro silica. The effect of PP on flexural strength, as reported by previous authors, is summarized and presented in Fig. (10).
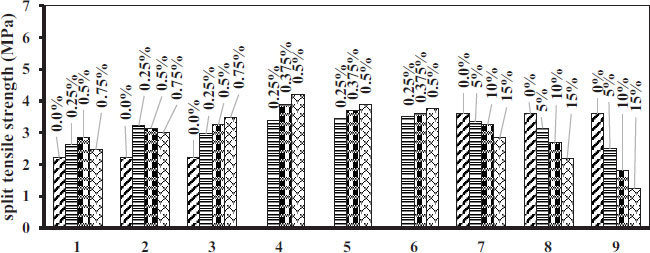
6.3.2. Polyethylene Terephthalate (PET)
Pelisser et al. [25] investigated recycled-bottle PET FRC fibers with lengths of 10, 15 and 20 mm and volume fractions of 0.05, 0.18 and 0.30% related to the volume of concrete. The energy at the first crack is increased for 20mm long fibre concrete compared to 10mm long fibre concrete. More first crack impact strength was shown by 0.18% fibre at 28 days of curing, and more failure impact strength was shown by 0.05% fibre concrete. They concluded that the higher toughness was shown by 20mm long fibre, and FS increased by 19.20% at 0.3% of recycled PET fiber concrete. Alberti et al. [78] investigated polyolefin fibre with lengths of 48 mm and 60mm. They found negligible differences in behaviour between them in concrete. Ghernouti et al. [49] described that the plastic bag waste fiber (PET) in the SCC has an ignorable effect on the FS. Rahmani et al. [3] reported that 5% sand volume replacement with PET particles with the same w/c ratios increased flexural strength by 6.71% and 8.02%, but there was a reduction at 15% substitution of PET particles in w/c ratio by 14.7% and 6.25%. Borg et al. [12] reported 1% PET fiber volume to show the highest flexural strength, and long and deformed fibers to show slightly better performance than short and straight fibers. The length of fiber had been reported to exhibit a higher effect than the type of fiber. Donkor and Obonyo [19] reported that 0.4% fiber content enhanced the 3-point flexure strength by 22.0%. Corinaldesi and Nardinocchi [67] reported that the hybrid systems had improved the flexural strength of either PP or PET fibers.
6.4. Modulus of Elasticity
Fig. (11) shows the modulus of elasticity of PP fibre concrete as reported by the authors in the past. The authors followed test methods as suggested in EN 13412 and ASTM c 215 for the determination of the modulus of elasticity. Karahan and Atis [29] reported that the modulus of elasticity increased up to 0.05% of PP fiber content and decreased with an increase in fibre content. Yew et al. [61] reported that the 0.4 mm size PP fiber at a content of 0.75% had shown 24.22% improvement in the modulus of elasticity. PP fiber of 0.4 mm size had shown higher modulus compared to 0.25 mm size PP Fig. (11).
7. DURABILITY
The durability of concrete structures has been largely studied to prevent steel corrosion of reinforcement in concrete. Medina [6] investigated the length of water permeability and carbonation, which are the two main processes responsible for durability. Foti [36] reported that the ductility of concrete increased by using PET bottle fibers in concrete. Saikia and Brito [64] concluded that several types of waste plastic aggregate decreased the permeability of concrete; hence, the durability of concrete also increased.
7.1. Freezing–thawing Behaviour
The uniform distribution of PP fiber forms a grid structure; hence, the bleeding and also segregation of the concrete mixture are decreased, and also micro-cracks are reduced [79]. Zhang and Li [60] concluded that the addition of PP fiber in concrete had shown good durability on freeze-thaw cycle exposure. The higher the relative dynamic elastic modulus, the better the freezing–thawing durability of PP-based concrete. Zhang and Li [76] concluded that the inclusion of PP fiber volume lower than 0.08% and 0.07% [80] improved durability. Zhang and Li [60] concluded that an increase in fiber volume lower than 0.120% decreased the length of water permeability, the carbonation depth, and the dry shrinkage strain of concrete with fly ash and silica fume, but it was found to be a little increased when compared to the controlled concrete; also, freezing–thawing resistance increased with the enhancement of fiber volume fraction below 0.08%, and decreased slightly beyond 0.08%. The authors in the past have used ASTM C666/C666M procedure for testing freezing–thawing behavior.
7.2. Carbonation
Fan et al. [80] concluded that when CO2 reacts with the CaOH and cement gel, it is called carbonation. It leads to the corrosion of steel reinforcement of the concrete due to a decrease in the pH of the material. Pesic et al. [56] concluded that durability increases by reducing cracks generation. Cracking correlates to durability, but cracking cannot be measured [60]. Song et al. [81] investigated the diffusion of acid-soluble M4 chloride in concretes versus various crack densities. Fan et al. studied the early cracking effect on durability and the area of the crack during setting and hardening [80]. Younsi et al. [82] simulated real-setting conditions with fast water and deficient hydration in the outside layer of concretes. The depth of carbonation related to various volume fractions of plastic fibre is presented in Fig. (12). Authors followed the procedure of GB/T 11974 for the determination of carbonation.
7.3. Permeability
Tam et al. [83] concluded that permeability affects concrete durability because permeability is a reason for many concrete degradation mechanisms, aggressive chemicals movement, and water movement during freeze–thawing cycle [84] . Zhang and Li studied durability by investigating water impermeability, carbonation resistance, dry shrinkage, and freeze–thawing of PP FRC having fly ash and silica fume, and also studied the effect of fiber volume fraction on impermeability [60] of pozzolan cement with PP fiber [6]. The relationship between the length of water permeability and PP fiber volume fraction concrete composite is shown in Fig. (13). The inclusion of PP fiber lowers the water permeability of FRC. PP fiber fraction from 0.0% to 0.120% decreased the length of water permeability from 8.7 mm to 7 mm. Fan et al. [80] concluded that permeability is inversely proportional to density and compactness, i.e.., the lower the compactness, the higher the permeability due to more porosity. The authors followed the procedure of J. E30-2005 for the determination of permeability.
7.4. Drying Shrinkage
Corinaldesi and Nardinocchi [67] reported shrinkage and permeability of concrete to be reduced by using an expansive agent with hybrid fibers. All the plastic fibers had shown extreme resistance to corrosion of concrete except for PET fibers. Toutanji et al. [85] concluded that the plastic’s early drying shrinkage can be reduced by polypropylene fibers by improving the tensile strength of concrete and arresting cracks. Huang [86] reported that the brittleness of the matrix is reduced by introducing polypropylene fiber. Toutanji et al. [85] also reported that polypropylene fiber resists the formation of cracks effectively caused by shrinkage. Tangchirapat and Jaturapitakkul [87] reported that the cracks are mainly due to dry shrinkage. Loss of water in concrete occurs during dry and hot environments, leading to cracks. Zhang and Li [60] used 100x100x400 mm3 prisms concrete composite to carry out the dry shrinkage testing following the Chinese Standards. After 2 days of curing at 100% humidity, the lengths of the specimens were measured and then shifted for further curing. The authors followed the procedure of J. E30-2005 for determination of drying shrinkage.
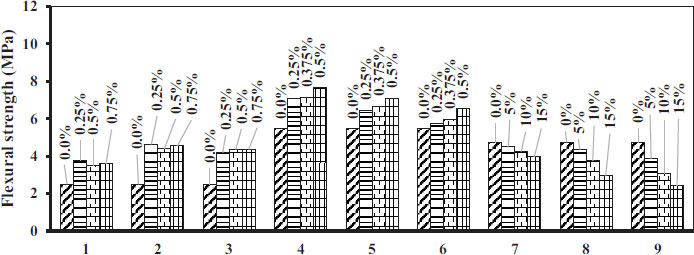
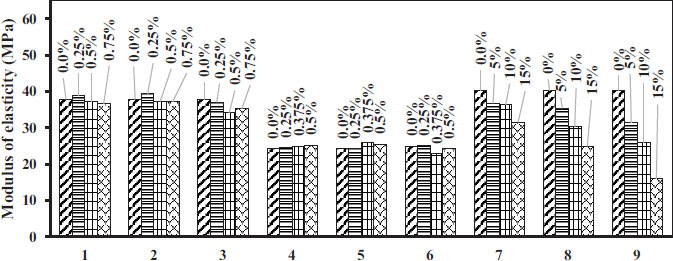
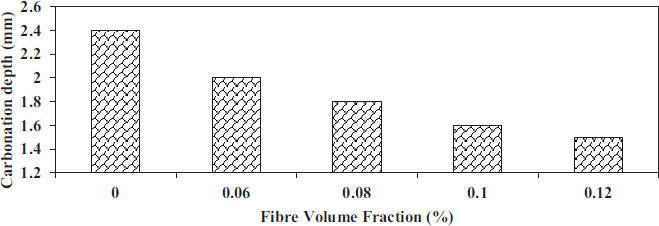
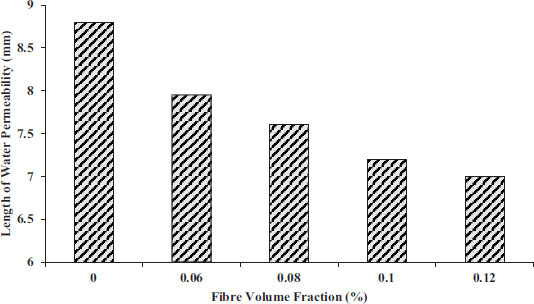
7.5. Effect of Elevated Temperature
Liu et al. [42] studied the evolution of chemical and physical properties of cement paste as well as the change in properties in samples of self-compacting cement paste (SCCP) containing various dosages of PP fibre at various elevated temperatures. After exposure to elevated temperature, the microstructure was examined using scanning electron microscopy (SEM) and mercury intrusion porosimetry (MIP). To ascertain the impact of microstructural changes on the permeability of SCCP samples, gas permeability tests were conducted. The micro and macro characteristics were compared using various PP fibre doses. The authors reported that up to the application of 100°C, the PP fibres did not melt, and their compatibility with the gel was also found to be good. On application of 200°C, the fibres melted and spread through the pores, which were reported to absorb more energy and elevate temperature. At 300°C, due to the melting of PP fibres, moisture diffusion is reported. The authors of a research work [20] reported inconsistency in mechanical and thermal properties of concrete containing PP fibres when subjected to high temperatures. Kalifa [88] reported that the inclusion of fibres resulted in a significant reduction in the pressure field that accumulated in the porous network during heating. Persson [89] proposed that a fibre content of 0.7 kg/m3 for indoor concrete and 1.4 kg/m3 for tunnel concrete is adequate to prevent explosive fire spalling in self-compacting concrete.
8. SCANNING ELECTRON MICROSCOPY
Zheng et al. [60] investigated the mass loss and appearance of hybrid RPC in the heating process by using about 5 mm small pieces from the compressive failure specimens (70.70 x 70.70 x 70.70 mm cubes, 40.0 x 40.0 x 160.0 mm prisms and 70.70 x 70.70 x 228 mm prisms); samples were also taken for scanning electron microscope (SEM) test. The SEM micrograph of PPF and PPF melt channel is shown in Fig. (14), the same of master fibre in Fig. (15), and RPC matrix in Fig. (16). At room temperature, RPC had shown higher strength because the internal structure of RPC is dense and the continuous block C-S-H gel exists, as shown in Fig. (16). At 400 LC, without a change in the density of RPC, begins to increase in the C-S-H gel. SEM micrographs reported by the authors of the past are presented in Figs. (17-25).
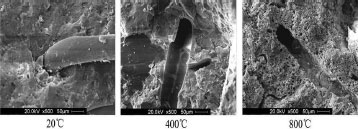
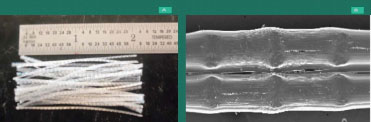
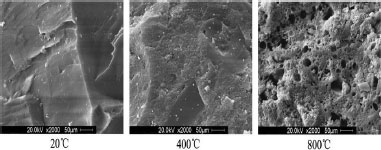
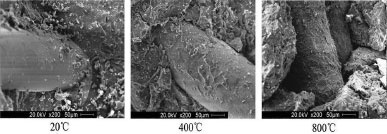
Liu [42] reported that the macro cracks could not be captured at a magnification lower than 35X. Figs. (21 and 25) show visible thermal cracks on the surface caused by temperature differences. At a magnification of 500X, the physical size of the image is of length 263 μm and 186 μm in width when used. For 0.152 μm per pixel, the image size is 1728 × 1027 pixels. A video microscope with 35X magnification and an image size of 640 × 414 pixels was used to take the pictures [42]. Fig. (17) shows the interface between matrix and steel fiber after exposure to 20 LC, 400 LC and 800 LC RPC matrix PPF and PPF melting channels. The reports of Liu et al. [42], as indicated in Figs. (22 and 23), explain that the PP fibre did not melt up to the temperature of 130°C. From this, it is evident that the PP fibres have good contact with the hydration products and that there is no clear interface between them and the matrix. Figs. (18 and 24) indicate that when the samples heated to 200 °C, the melting of PP fibre occurred. When the PP fibres melt, the liquid-stated melted fibres travel through the pores surrounding them. This change serves as the link between hydrated goods. The melted PP fibre absorbs more energy and evaporates at greater temperatures. As a result, the flow path and the fibre channel remnants are joined to one another, forming a more interconnected pore network. The picture of a sample of HPCP PPF1 heated to 300 °C is shown in Fig. (19). When the PP fibres melt, the residual PP fibres act as a conduit for moisture to diffuse.
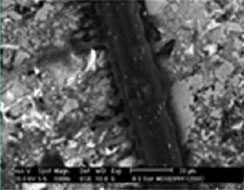
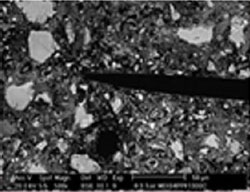
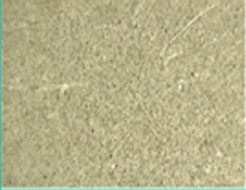
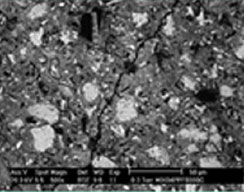
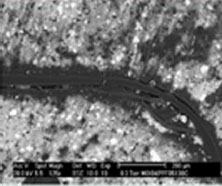
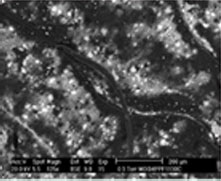
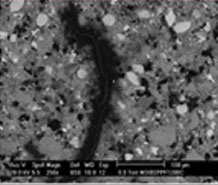
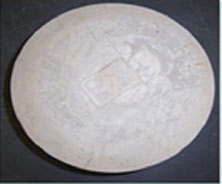
9. APPLICATIONS OF PLASTIC FIBER IN THE FIELD
Further research is required worldwide to use waste plastic fiber in concrete, even though plastic fiber-reinforced concrete has been used in various projects. Different environmental problems can be eliminated by using plastic in cement concrete. For lightweight semi-structural applications, like partitions, walls and panels for floor, GRP foamed concrete can be used. Recycled plastic fibers have been used in reinforcing concrete footpaths and precast panels [74]. Asokan et al. [4] developed 12 mm thick and 8 mm thick architectural cladding panels using GRP waste fiber with 5%, 15%, 30% and 50% partial substitutes for fine aggregates. Cengiz and Turanli [5] developed fiber-reinforced shotcrete panel with a fiber content of 0.78% and 1.1%, respectively. Shi Yin et al. [74] developed 0.45% and 0.67% PP fiber concrete footpaths in 25 MPa and precast panels in 40 MPa concretes.
Dalhat et al. [1] reported the use of lightweight and special pavement, race tracks, bridge decks, and pedestrian and bicycle lanes. Borg et al. [12] developed Kraai panels with 0.5, 1, and 1.5% inclusion of plastic fiber in concrete. Zhang et al. [60] reported that the construction of pavement is possible with the inclusion of polypropylene fibers. Saikia and Brito [88] reported the formation of lightweight concrete, paving slabs, and hydraulic structures by replacing FA and CA with PET aggregate. Pelisser et al. [25] developed small thin slabs with the inclusion of PP, glass, nylon, and PET fibers to the mortar mixture.
Due to the light weight of plastic aggregate, there is a decrease in density; hence, it can be used as lightweight concrete, and due to more resistance to permeability, it can be used in a water tank. Raju et al. [65] reported the same as Saikia but within the aspect ratio of 50 only due to its low workability [56].
10. FUTURE RECOMMENDATIONS
Based on the review made on plastic waste concrete, the following works are recommended on un-explored/little-explored areas for future study:
1. A little work has been reported on the effect of various types of plastic wastes, like PP, HDPE, and PET, on the strength properties of concrete when used as replacement materials for aggregates. Therefore, a detailed study on various strength properties of concrete containing PP, HDPE and PET individually is required in comparison to normal concrete.
2. Report on the effect of various methods of blending plastic waste fibers, such as PP, HDPE, and PET, in FRC is found scanty. As such, research on this area is felt essentially required.
3. Very limited works are available on the effect of the shape, aspect ratios, and the surface of plastic waste fibers in FRC. Hence, a detailed study is required on concrete containing each type of plastic waste.
4. It is observed from the review that little work is reported on the durability of concrete containing plastic wastes. Therefore, a complete study on various durability aspects of concrete containing each type of plastic waste is required compared to normal concrete.
5. It is seen that little is reported on the use of PP in self-compacting concrete. Behaviour of HDPE and PET in self-compacting concrete is yet to be ascertained.
6. Further, a large-scale study on the thermal property of concrete with plastic wastes as aggregate replacement is required to establish the quality of FRC.
7. Reports on life cycle assessment and life cycle cost analyses of plastic FRC are rarely visible, for which a detailed study is required.
8. Studies on pollution due to the leaching of toxic constituents from concrete with plastic waste materials have been found to be almost absent. So, research on this area is also essential.
CONCLUSION
After a review of the literature on plastic waste concrete following important conclusions are drawn:
1. The surface treatment of plastic wastes with reactive materials like metakaolin, iron cinders and silica fume increases the strength of waste plastic concrete due to pozzolanic reaction. The compressive strength increased on the inclusion of fibres up to 0.45% and it is recommended to use 0.4% to get good compressive strength.
2. The inclusion of waste plastic fibers in cement concrete increases tensile strength and flexural strength due to the good bond between concrete and plastic. Bond increases on the introduction of silica fume in such concrete. The bond between cement and plastic can be improved by making protrusions on the fibre. When 15% of sand is replaced with PET particles at water-cement ratios of 0.42 and 0.54 there is a reduction in tensile strength of 15.9% and 18 %, respectively.
3. There is an improvement in the ductility of plastic waste concrete due to the arrest of micro-cracks by the plastic fiber.
4. The young’s modulus of cement concrete declines with the increased amount of plastic fiber.
5. The inclusion of PP fiber enhanced the water impermeability of concrete.
6. Plastic waste aggregates meet the standards of lightweight aggregates. Thus the introduction of plastic waste as concrete aggregate lowers the density of concrete and fulfills the requirements of lightweight concrete. The workability of plastic waste concrete reduces with an increase in the amount of plastic waste. Twisted bundles showed higher workability than straight fiber.
7. Plastic waste aggregate has a lower coefficient of thermal conductivity in comparison to natural aggregate which is found beneficial in controlling loss or gain of temperature from a structure made with plastic waste concrete. Hybrid plastic fibre reinforced concrete has more tolerance to elevated temperatures in comparison to normal concrete.
8. PP fiber concrete shows more spalling resistance due to bridging action.
LIST OF ABBREVIATIONS
PP | = Polypropylene |
PET | = Polyethylene Terephthalate |
HDPE | = High-density Polyethylene |
MIP | = Mercury Intrusion Porosimetry |
SCCP | = Self-compacting Cement Paste |
SEM | = Scanning Electron Microscopy |
CONSENT FOR PUBLICATION
Not applicable.
FUNDING
The authors did not receive any funds from any source for the present work.
CONFLICT OF INTEREST
The authors declare no conflict of interest, financial or otherwise.
ACKNOWLEDGEMENTS
Declared none.