All published articles of this journal are available on ScienceDirect.
Experimental Mechanical Characterization of Silica Fume-based No-fines Concrete Reinforced by Steel or Nylon Fibers
Abstract
Aims:
In this study, the mechanical characterization of no-fines concrete solutions is addressed experimentally, with the purpose of possibly increasing their strength by using silica fume and embedded fibers (steel and nylon fibers) as possible efficient reinforcement.
Background:
Due to competition between developed and advanced countries, the contemporary construction sector is currently experiencing a shortage of fundamental building materials. In this regard, no-fines concrete is becoming increasingly popular, and it has been proven in the literature that it can offer some advantages as an economic and lightweight solution compared to conventional concrete. However, experiments and investigations are still needed to investigate the potential mechanical advantages for its efficient use in buildings, given that the major limitation compared to normal concrete is represented by limited strength.
Objective:
The primary objective of the present study is to assess the mechanical strength of no-fines concrete samples in which steel fibers, nylon fibers, and partial cement replacement with silica fume are used. For this purpose, no-fines concrete specimens are produced with fixed mix proportions of 1:6 cement-aggregate (c-a) ratio, various coarse aggregate gradations ((20-10) mm and (10-5) mm), and fixed w/c ratio (0.42).
Methods:
The experiments are carried out on cubes, cylinders and prisms of concrete samples with various aggregate solutions. The nominal length of both types of fibers is fixed at 20 mm. Steel fibers with 1 mm in diameter and nylon fibers with 0.3 mm, 0.4 mm, 0.5 mm, or 0.6 mm diameters, respectively, are taken into account to explore their effects on compressive strength, split tensile strength, and flexural strength.
Results:
The presented experimental results showed various mechanical advantages, such as increased compressive, splitting tensile and flexural strength parameters, for most of the examined samples. Nylon fibers, in particular, proved to significantly increase compressive, splitting tensile, and flexural strength values, compared to normal concrete, with additional benefits compared to steel fibers (for the examined arrangements and configurations).
Conclusion:
Overall, the examined compositions and mixtures of silica fume-based no-fines concrete samples encourage further investigations for the optimization of these solutions. In this regard, in addition to mechanical capacities, further key parameters (such as weight, cost, impact on concrete microstructure, etc.) will be taken into account.
1. INTRODUCTION
Currently, the production of special types of concrete solutions is increasing at a large scale and construction industries are mostly motivated by material economy demand. The result of this continuous innovation is that many types of concrete are presently used in construction for several reasons and applications, such as ferro-cement concrete, fiber-reinforced concrete, and other lightweight concrete types, such as aerated concrete, foam concrete, and even no-fines concrete [1-3]. Especially for no-fines concrete solutions, typical advantages are represented, among others, by economical input materials, lightweight properties, and thermal advantages. No-fines concrete represents a concrete type that is produced without fine aggregates (sand) [3, 4] (Fig. 1) but contains only coarse aggregates and cement mixed with water [5-9].
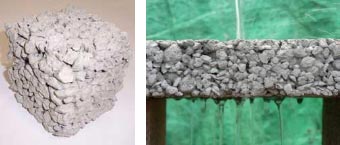
The coarse aggregate particles are typically coated with a thin cement paste having about ≈1.2-1.3 mm thickness [2]. Usually, the size of coarse aggregates ranges from 10 mm to 20 mm, and 10% undersize or 5% oversize components can be used [7, 8]. Uniform-size coarse aggregates can also be taken into account for casting [10, 11]. For this type of concrete, the cement-aggregate (c-a) ratio is usually set in the range from 1:3 to 1:7 [6, 10], while water to cement (w/c) ratio ranges from 0.38 to 0.52. As a major issue, the aggregates should satisfy the saturated surface dry (SSD) condition before mixing to avoid surface absorption and thus, the possible risk of improper cement coating.
While cement is a necessary component for possible concrete solutions, the overall cost of the material represents the first major challenge for producers. In this regard, the use of optimal amounts of cementitious components, such as silica fume, has been confirmed by literature studies to have important benefits on the performance of the final product since it allows to limit concrete cost and also significantly improves its durability [12]. In this regard, the available research evidence suggests that further studies are needed to effectively replace cement with silica fume, and the present investigation aims at contributing in this direction.
Another well-known issue of concrete, and especially no-fines concrete solutions, in mechanical terms, is represented by its typical brittle behaviour in tension and limited strength. The reinforcement of concrete by embedment of additional fibers, in this regard, can increase its strength and even ductility by reducing the propagation of micro-cracks [13]. Embedded fiber reinforcements can make concrete more homogenous, with major benefits in terms of mechanical performance and even shrinkage. It was found [14] that adding fibers to concrete mixes can effectively enhance the tensile strength of final products. In a study, the efficient improvement of concrete with Waste Plastic Fibers (WPFs) was explored [13] to enhance its strength properties and save natural resources, with economic advantages and enhanced durability. Besides, experimental studies in support of the optimization of fiber-reinforced no-fines concrete solutions are still limited and require further efforts. In this regard, the present investigation focuses on the assessment of mechanical effects due to the replacement of cement with silica fume and the reinforcement by embedded fibers in order to enhance the overall strength capacity of no-fines concrete.
2. RESEARCH METHODS AND LIMITATIONS
2.1. Scope
According to ACI 522R-10 document [15], no-fines concrete solutions can be used for bridge constructions, floor plates in greenhouses, permeable pavements and walkways for parking lots, rigid permeable pavements for supermarkets, structural walls with lightweight or thermal insulation properties, walls and slabs with good sound absorption capacity, and many other applications. For these applications, a critical parameter for design is represented by mechanical capacities under ordinary or accidental design loads. Hence, the mechanical characterization of basic strength values represents the first (but not sufficient) step for product optimization.
In this regard, the primary objective of the present investigation is to assess the physical strength qualities of no-fines concrete samples characterized by partial cement replacement with silica fume, most importantly, by using embedded reinforcement consisting of steel or nylon fibers. To this aim, major outcomes from an experimental investigation carried out on concrete samples characterized by various arrangements, i.e., fixed mix proportion (1:6 c-a ratio), various coarse aggregate gradations ((20-10) mm and (10-5) mm), and fixed w/c ratio (0.42), are presented. Both steel and nylon fiber dosages varied from a minimum of 0.25% up to 2% by weight of cement, with a progressive increment of 0.25%. Experimental details are discussed in Sections 3 and 4.
2.2. Embedded Fibers and their Impact on Concrete Microstructure
While mechanical properties are primarily addressed in this paper, it is important to know that several other aspects could contribute to final product assessment and optimization. Among others, the weight of final mixtures represents an important parameter to account for design and decision-making. In this regard, the presently reported experimental results will be further elaborated and extended by considerations in this direction. Moreover, the impact of embedded fibers on concrete microstructure represents the key to experimental observations. To this aim, it has been largely proven by literature studies that using SEM and XRD for self-compacting concrete (SSC) solutions can show major microstructure effects due to fibers [16]. The microstructure analysis of SCC mixes [17] revealed that the capacity of fibers to fill gaps or micro-cracks, and hence increase the material strength, is mostly attributable to their even distribution. However, fibers with twisted orientation are useless for the bridging process. Research on the microstructure of fiber-reinforced SCC samples exposed to elevated temperatures showed that the cementitious matrix, which has a fairly coherent structure, developed voids and micro-cracks both before and after thermal stress exposure. According to SEM comparisons for mixtures based on synthetic fibers towards steel or mineral fibers [18], the latter displayed an extra-dense fiber interfacial zone. On the other side, in the microstructure analysis, high-strength concrete samples containing polypropylene fibers, when subjected to temperatures up to 200°C [19], regulated water ejection from concrete, both at low and high temperatures.
3. MATERIALS SELECTION FOR THE EXPERIMENTAL INVESTIGATION
3.1. Cement
Cement is a binding material with adhesive and cohesive properties in concrete. It has the property of setting in the pre- sence of water by a chemical reaction known as the hydration process, which produces Calcium-Silicate-Hydrate (C-S-H) gel. According to ASTM C150/C150M – 19 standard, Ordinary Portland Cement (OPC) was taken into account [20]. The calculated chemical properties of OPC are listed in Table 1.
3.2. Silica Fume
Often called “condensed silica fume” or “micro-silica”, “silica fume” is the generally used name for this byproduct. It is obtained from ferrosilicon alloys and silicon during quartz and coal’s purity process in a submerged arc electric furnace. The silica fume is obtained by condensing of escaping gaseous SiO in the form of very fine spherical particles resulting in amorphous silica (SiO). Silica in the form of amorphous is highly reactive, and its particles speed up the reaction with Calcium-Hydro-Oxide by the hydration of OPC. The small particles of silica fume merge in between the cement particles, thus filling voids and improving the aggregate packing, hence increasing concrete strength. Silica fumes with the composition according to ASTM C1240 – 15 [21] were used for the present investigation (Table 1 and Fig. 2a).
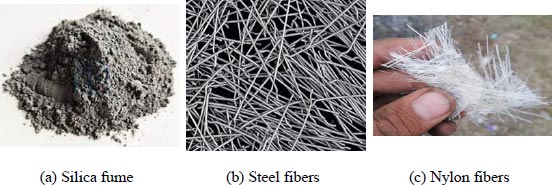
Major Component |
Cement (%) |
Silica Fume (%) |
---|---|---|
Calcium oxide (Cao) | 60 | 0.13 |
Aluminium oxide (Al2O3) | 3.75 | 0.07 |
Iron oxide (Fe2O3) | 3.12 | 0.03 |
Magnesium oxide (MgO) | 2 | 0.12 |
Silicon dioxide (SiO2) | 19.22 | 85.23 |
Sulphur trioxide (SO3) | 2.45 | 0.15 |
Carbon | 0.03 | 0.23 |
Loss on ignition (LOI) | 2.25 | 3.45 |
Tricalcium silicate (C3S) | 43.45 | 0 |
Dicalcium silicate (C2S) | 30.34 | 0 |
Tricalcium aluminates (C3A) | 8.56 | 0 |
Tetracalcium aluminates ferrite (C4AF) | 8.55 | 0 |
Table 2.
Diameter (mm) |
Effective Length (mm) |
Elongation (%) |
Load (N) |
Ultimate Tensile Strength (MPa) |
---|---|---|---|---|
Steel fibers | ||||
1 | 15 | 13 | 302.7 | 388 |
Nylon fibers | ||||
0.3 | 22 | 20 | 341 | 23.9 |
0.4 | 21 | 18.2 | 317 | 38.1 |
0.5 | 20 | 17.3 | 245 | 46.5 |
0.6 | 19 | 16.3 | 183 | 51.4 |
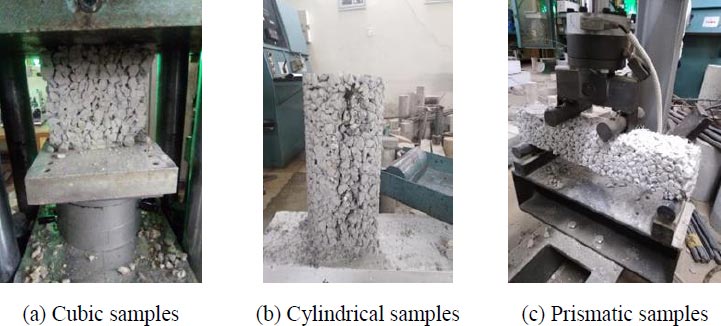
3.3. Fibers
Two types of fibers (steel and nylon fibers), according to ASTM C1765 – 19 [22], were taken into account as embedded reinforcement for no-fines concrete specimens. Steel fibers, as shown in Fig. (2b), were obtained by cutting steel binding wires of approximately 1 mm diameter in the specified nominal length (Table 2). In parallel, nylon fibers, as shown in Fig. (2c), were obtained from a straight cold-drawn thread of 0.30 mm, 0.40 mm, 0.50 mm, and 0.60 mm diameter, respectively, which were purchased from a local producer and cut in the desired length. The mechanical properties of steel and nylon fibers are summarized in Table 2.
3.4. Coarse Aggregates
Coarse aggregate is considered an inert material, but it also possesses thermal, physical and chemical properties, which influence the global performance of concrete. For the present investigation, crushed coarse aggregates were used for casting no-fines concrete samples, according to ASTM C33 / C33M - 18 [23] and ASTM C136 / C136M - 14 [24] specifications. The aggregates were preliminary sieved, washed and dried in the open air to satisfy the SSD condition.
3.5. Water
The ASTM C1602/C1602M - 18 document [25] specifies that water used for producing concrete should be acceptable for drinking. However, some types of water may contain chlorides, which can cause efflorescence and corrosion of embedded steel. Potable water was used for the presently discussed experimental investigation.
4. EXPERIMENTAL PROGRAM
For mechanical assessment purposes, conventional testing protocols from technical standards were taken into account, with primary attention on typical strength capacities (such as compressive strength, splitting tensile strength, and flexural strength) [26-28]. Standard-size parameters for cubic, cylindrical, and prismatic specimens were considered for a total of 375 samples. Moreover, to further address the experimental outcomes in terms of fiber reinforcement efficiency, a number of experiments were also carried out on normal no-fines concrete samples.
Typical setup configurations are proposed in Fig. (3), while a summary of examined configurations is reported in Table 3.
Series | Fiber Diameter (mm) | Specimen Shape | Fibers (%) | No. of Specimens |
---|---|---|---|---|
1 | 0.3 (NF) 0.4 (NF) 0.5 (NF) 0.6 (NF) 1 (SF) |
Cube | 0 (normal no-fines concrete) | 5 |
2 | 0.25 | 15 | ||
3 | 0.5 | 15 | ||
4 | 0.75 | 15 | ||
5 | 1 | 15 | ||
6 | 1.25 | 15 | ||
7 | 1.5 | 15 | ||
8 | 1.75 | 15 | ||
9 | 2 | 15 | ||
Total number of specimens | 125 | |||
10 | 0.3 (NF) 0.4 (NF) 0.5 (NF) 0.6 (NF) 1 (SF) |
Cylinder | 0 (normal no-fines concrete) | 5 |
11 | 0.25 | 15 | ||
12 | 0.5 | 15 | ||
13 | 0.75 | 15 | ||
14 | 1 | 15 | ||
15 | 1.25 | 15 | ||
16 | 1.5 | 15 | ||
17 | 1.75 | 15 | ||
18 | 2 | 15 | ||
Total number of specimens | 125 | |||
19 | 0.3 (NF) 0.4 (NF) 0.5 (NF) 0.6 (NF) 1 (SF) |
Prism | 0 (normal no-fines concrete) | 5 |
20 | 0.25 | 15 | ||
21 | 0.5 | 15 | ||
22 | 0.75 | 15 | ||
23 | 1 | 15 | ||
24 | 1.25 | 15 | ||
25 | 1.5 | 15 | ||
26 | 1.75 | 15 | ||
27 | 2 | 15 | ||
Total number of specimens | 125 | |||
Total number of specimens (cubes, cylinders and prisms) | 375 |
5. RESULTS AND DISCUSSION
5.1. Compressive Strength
The compressive strength test protocol represents the most common approach to characterize concrete capacity and is particularly simple in execution. In the present study, all cubic specimens listed in Table 3 were subjected to a standard compression test. To this aim, the cubic samples were manufactured using cast iron moulds with a leak-resistant metal base plate. To prevent leaking of cement paste from the mould, the seams between the portions of the mould were lightly coated with mould oil.
For the experimental setup, as shown in Fig. (3a), the compressive strength of each sample was calculated as:
![]() |
(1) |
Where P is the applied load, and A is the resisting compressive area of the specimen.
Major experimental outcomes are proposed in Table 4 and Fig. (4).
More in detail, experimental results are listed in Table 4, with evidence of the percentage of embedded fibers and coarse aggregate gradation (A-G). Additionally, compressive strength results for silica fume-based no-fines concrete cubes (i.e., without reinforcing fibers) are also mentioned in Table 4.
As confirmed by preliminary analyses, no-fines concrete was presently investigated with partial silica fume-based replacement (with 7.5% dosage). As a result, such an unreinforced reference composition still confirmed the mechanical benefit of partial replacement by silica fume.
From the listed comparative results, it can be observed that the addition of embedded fibers generally improves the compressive strength of silica fume-based no-fines concrete solutions. Also, it can be seen from Table 4 and Fig. (4) that nylon fibers offered improved compressive performances compared to cubic samples with steel fibers.
In percentage terms, it is thus of interest to assess the compressive strength increase based on various arrangements of embedded fibers only. Typical results are shown in Fig. (5), where the percentage variation Δ is calculated from reinforced samples toward the unreinforced silica fume-based composition.
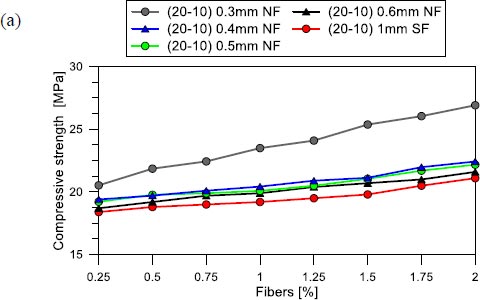
A-G (mm) | Fibers (%) | Fiber Diameter and Material | ||||
---|---|---|---|---|---|---|
0.3 mm NF | 0.4 mm NF | 0.5 mm NF | 0.6 mm NF | 1 mm SF | ||
(20-10) | 0 | 17.8 (no fibers) | ||||
(10-5) | 0 | 16 (no fibers) | ||||
(20-10) | 0.25 | 20.53 | 19.4 | 19.22 | 18.7 | 18.4 |
(10-5) | 0.25 | 18.35 | 17.2 | 17.14 | 17 | 16.6 |
(20-10) | 0.5 | 21.86 | 19.71 | 19.77 | 19.2 | 18.8 |
(10-5) | 0.5 | 19.57 | 17.5 | 17.8 | 17.5 | 16.8 |
(20-10) | 0.75 | 22.44 | 20.1 | 19.9 | 19.7 | 19 |
(10-5) | 0.75 | 20.36 | 18.12 | 18.06 | 18 | 16.9 |
(20-10) | 1 | 23.5 | 20.43 | 20.09 | 19.9 | 19.2 |
(10-5) | 1 | 21.03 | 18.8 | 18.7 | 18.3 | 17.1 |
(20-10) | 1.25 | 24.1 | 20.9 | 20.5 | 20.4 | 19.5 |
(10-5) | 1.25 | 22.37 | 19.29 | 19 | 18.5 | 17.3 |
(20-10) | 1.5 | 25.38 | 21.13 | 21.05 | 20.7 | 19.8 |
(10-5) | 1.5 | 23.82 | 19.5 | 19.2 | 18.7 | 17.6 |
(20-10) | 1.75 | 26.05 | 21.98 | 21.7 | 21 | 20.5 |
(10-5) | 1.75 | 24.03 | 19.76 | 19.5 | 19 | 18 |
(20-10) | 2 | 26.92 | 22.43 | 22.18 | 21.6 | 21.1 |
(10-5) | 2 | 24.4 | 20.02 | 19.98 | 19.78 | 18.5 |
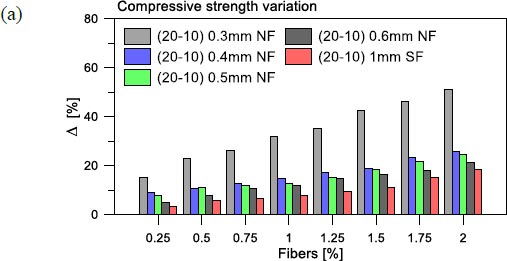
As expected, the strength increase was typically measured as proportional to the amount of embedded fibers. Most importantly, partially more pronounced benefits were noted from using nylon fibers rather than steel fibers, even under the maximum dosage of 2% (among the examined configurations). In terms of the diameter of reinforcing fibers, the experimental results for 0.3 mm diameter nylon fibers showed improved capacities compared to other arrangements.
Compared to the literature, the experimental trends in Fig. (5) show a rather optimistic potential for fiber embedment. For SCC samples, for example, the compressive strength [29] increased up to 25%, respectively, based on the addition of hybrid recycled steel-polypropylene fibres. In a study [30], SCC from granite sawing waste was mixed with polypropylene fibres (in small amounts), increasing the compressive strength to around 22%. Positive mechanical effects were also observed [31] when including fibers in SCC samples for up to a volume of 2-3%, with increased compressive strength. The optimal mix of 0.5% long steel fibers with 1.0-1.5% short fibers was associated [32] with a significant increment of SCC compressive strength. Several research studies in this regard have proven that the major benefit is represented by the capacity of fibers to bridge cracks efficiently rather than increasing concrete porosity [31, 32].
5.2. Splitting Tensile Strength
The splitting tensile strength was estimated through the indirect method (cylindrical tensile strength), i.e., the Brazilian protocol. After positioning each cylinder, as shown in Fig. (3b), in the testing machine, the ultimate load at the failure was recorded, and the tensile strength was calculated as:
![]() |
(2) |
Where P is the applied load, D is> the diameter of each specimen, and L is its length.
The corresponding results are summarized in Table 5 and Fig. (6). From the experimental outcomes in Table 5, it can be observed that for all dosages of nylon fibers (in (20-10) coarse aggregates gradation), the recorded range of strength is in the range of 3.85 to 5.4 MPa, with a maximum peak at the dosage of 2% of fibers. In the case of steel fibers, the corresponding tensile strength varied from 3.51 MPa to 4.5 MPa. From the reported comparisons, it is thus clear that the use of nylon fibers at all diameters (0.3 mm - 0.6 mm range, in the present study) and doses (0.25% - 2% interval, for the present study) can efficiently increase the splitting tensile strength of silica fume-based no-fines concrete. As also observed in terms of compressive strength analysis, among various diameter and dosage combinations, the strongest benefit from nylon fibers was found for 2% dose and 0.3 mm diameter.
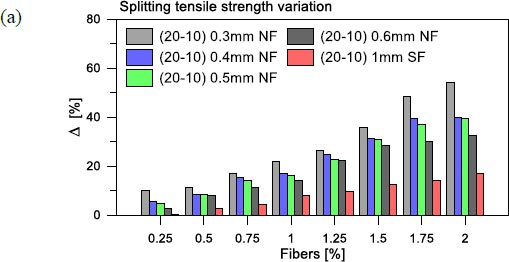
A-G (mm) |
Fibers (%) |
Fiber Diameter and Material | ||||
---|---|---|---|---|---|---|
0.3 mm NF | 0.4 mm NF | 0.5 mm NF | 0.6 mm NF |
1 mm SF |
||
(20-10) | 0 | 3.5 (no fibers) | ||||
(10-5) | 0 | 2.9 (no fibers) | ||||
(20-10) | 0.25 | 3.85 | 3.7 | 3.67 | 3.6 | 3.51 |
(10-5) | 0.25 | 3.1 | 3.07 | 3.03 | 3 | 2.96 |
(20-10) | 0.5 | 3.9 | 3.8 | 3.8 | 3.78 | 3.6 |
(10-5) | 0.5 | 3.4 | 3.37 | 3.3 | 3.24 | 3 |
(20-10) | 0.75 | 4.1 | 4.03 | 4 | 3.9 | 3.65 |
(10-5) | 0.75 | 3.5 | 3.38 | 3.38 | 3.3 | 3.1 |
(20-10) | 1 | 4.27 | 4.09 | 4.06 | 4 | 3.78 |
(10-5) | 1 | 3.64 | 3.56 | 3.56 | 3.5 | 3.18 |
(20-10) | 1.25 | 4.43 | 4.37 | 4.3 | 4.28 | 3.83 |
(10-5) | 1.25 | 3.78 | 3.7 | 3.69 | 3.65 | 3.21 |
(20-10) | 1.5 | 4.75 | 4.6 | 4.58 | 4.5 | 3.93 |
(10-5) | 1.5 | 3.8 | 3.78 | 3.75 | 3.72 | 3.26 |
(20-10) | 1.75 | 5.2 | 4.88 | 4.8 | 4.55 | 4 |
(10-5) | 1.75 | 4 | 3.98 | 3.9 | 3.87 | 3.42 |
(20-10) | 2 | 5.4 | 4.9 | 4.88 | 4.63 | 4.1 |
(10-5) | 2 | 4.2 | 3.99 | 3.95 | 3.91 | 3.48 |
The analysis of percentage variation of splitting tensile strength for various fibers embedment arrangements, compared to unreinforced silica fume-based no-fines concrete samples, can be seen in Fig. (6).
The analysis of comparative results shows that nylon fibers at maximum dosage (2%) with 0.3 mm diameter can be more than twice effective compared to steel fibers (based on selected configurations).
It has been demonstrated by literature studies that the addition of fibers to SCC samples can efficiently increase their structural stability [33]. The splitting tensile strength of steel fiber-reinforced SCC samples containing a significant amount of marble powder increased by up to 16% [33]. The splitting tensile load was found to increase by 11% in an investigation [34] when coconut fibers were added to standard concrete. From comparative experiments reported previously [35], sisal fibers at doses of 1-4% were shown to increase the splitting tensile strength of concrete up to 3% when discarded coconut shells were used as coarse aggregate. SCC samples with 3% roselle fibers resulted in a 22% increase in splitting tensile strength [36]. Also, in these cases, it was generally observed that in samples subjected to increasing tensile loads, the corresponding stresses could be efficiently transferred to the embedded fibers, thus preventing the spread of macro-cracks. Micro-cracks are indeed connected by fibers, which can interrupt the possible propagation of new fractures [33].
5.3. Flexural Strength
In conclusion, a series of flexural strength tests were carried out to evaluate the bending capacity of the assembled silica fume-based no-fines concrete samples. The flexural strength was traditionally determined by applying a two-third point loading, as in Fig. (3c). The imposed vertical load was increased monotonically up to failure, and the corresponding flexural strength could be calculated as:
![]() |
(3) |
Evidence of experimental tests is proposed in Table 6 and Fig. (7).
A-G (mm) |
Fibers (%) |
Fiber Diameter and Material | ||||
---|---|---|---|---|---|---|
0.3 mm NF | 0.4 mm NF | 0.5 mm NF | 0.3 mm NF | 1 mmSF | ||
(20-10) | 0 | 5.2 (no fibers) | ||||
(10-5) | 0 | 4.2 (no fibers) | ||||
(20-10) | 0.25 | 5.4 | 5.37 | 5.28 | 5.24 | 5.207 |
(10-5) | 0.25 | 4.34 | 4.32 | 4.27 | 4.25 | 4.205 |
(20-10) | 0.5 | 5.45 | 5.4 | 5.37 | 5.42 | 5.23 |
(10-5) | 0.5 | 4.4 | 4.38 | 4.35 | 4.3 | 4.22 |
(20-10) | 0.75 | 5.58 | 5.52 | 5.48 | 5.47 | 5.29 |
(10-5) | 0.75 | 4.5 | 4.45 | 4.4 | 4.38 | 4.3 |
(20-10) | 1 | 5.72 | 5.65 | 5.58 | 5.51 | 5.3 |
(10-5) | 1 | 4.57 | 4.5 | 4.46 | 4.4 | 4.38 |
(20-10) | 1.25 | 5.79 | 5.74 | 5.69 | 5.63 | 5.38 |
(10-5) | 1.25 | 4.65 | 4.61 | 4.58 | 4.51 | 4.4 |
(20-10) | 1.5 | 5.8 | 5.86 | 5.76 | 5.7 | 5.4 |
(10-5) | 1.5 | 4.76 | 4.7 | 4.64 | 4.6 | 4.5 |
(20-10) | 1.75 | 6 | 5.93 | 6 | 5.85 | 5.55 |
(10-5) | 1.75 | 5 | 4.8 | 4.77 | 4.73 | 4.67 |
(20-10) | 2 | 6.4 | 6.2 | 6.3 | 5.92 | 5.65 |
(10-5) | 2 | 5.29 | 5 | 4.81 | 4.81 | 4.71 |
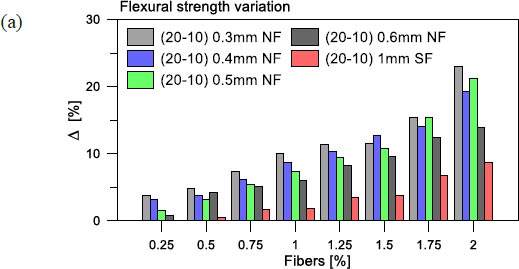
Especially in terms of percentage variations, it can be seen in Fig. (7) that the flexural strength improvement increases with dosage (up to 2%, in the present study) and with a decrease in the diameter of fibers, thus resulting in maximum benefits to the 0.3 mm diameter nylon fibers. Differing from compressive strength and splitting tensile strength trends, such a benefit was quantified in the order of 20% in optimal conditions, which was significantly smaller than previous evidence. In any case, present experimental outcomes suggested the mechanical benefit of reinforced silica fume-based no-fines concrete solutions. Under optimal arrangements, as shown in Table 5, the flexural strength was measured at around 6.4 MPa for nylon fibers.
In this regard, it must be noted that the fiber type can strongly affect the flexural strength of concrete solutions [37]. The modulus of rupture may be thus possibly improved further by mixing different plant-based natural fibers with concrete to optimize earlier experimental evidence. Most importantly, embedded fibers have an intrinsic capacity to stop any fracture propagation, which prevents the development of major cracks [38, 39] and can result in SCC flexure strength improvement of up to 7-55% compared to unreinforced concrete solutions [38]. In this regard, present experiments provide evidence of possible major benefits from fiber embedment in silica fume-based no-fines concrete solutions, which suggest further investigation for proper mix optimization.
CONCLUSION
An experimental study was carried out to assess possible mechanical benefits deriving from the embedment of reinforcing fibers in silica fume-based no-fines concrete solutions. From the experimental analysis of a total of 375 cubic, cylindrical and prismatic samples characterized by various fiber arrangements, it was found that the strength properties of silica fume-based (7.5% dosage) no-fines concrete could be significantly increased by the use of embedded fibers. The strength increased by increasing the percentage of fibers.
Major benefits were observed in compression, splitting tensile, and flexural testing protocols by the use of nylon fibers with small diameters rather than steel fibers.
For the examined configurations, the maximum dosage (2%) of nylon fibers with a minimum diameter (0.3 mm) resulted in a ≈52% increase in compressive strength, ≈50% in splitting tensile strength, and ≈25% in flexural strength compared to normal no-fines concrete.
Moreover, the maximum increase in strength for samples with reinforcement of steel fibers (2% and 1 mm in diameter) was measured at ≈18% for compressive strength, ≈20% for splitting tensile strength, and ≈12% for flexural strength compared to silica fume-based no-fines concrete samples. Overall, under similar setup and testing protocols, the optimal 2% dosage with 0.3 mm diameter of nylon fibers offered, compared to 1 mm in diameter steel fibers, a strength increase of up to ≈32% in compressive value, ≈30% in splitting tensile capacity, and ≈13% in flexural strength.
Based on present experimental outcomes and encouraging results in terms of mechanical efficiency for no-fines concrete solutions based on embedded reinforcing fibers, further studies will be carried out to further optimize the composition and include additional key performance indicators, such as the weight variation of mixes, their cost, the impact of fibers on concrete microstructure, etc.
CONSENT FOR PUBLICATION
Not applicable.
AVAILABILITY OF DATA AND MATERIAL
The data and supportive information are available within the article.
FUNDING
None.
CONFLICT OF INTEREST
Chiara Bedon is a member of the editorial advisory board of the journal The Open Civil Engineering Journal.
ACKNOWLEDGEMENTS
Declared none.