All published articles of this journal are available on ScienceDirect.
Mechanical Properties of Stone Mastic Asphalt Incorporating Glass Fiber
Abstract
Aims:
To study the mechanical properties of stone mastic asphalt incorporating glass fiber.
Background:
Asphalt may become cracked, degraded, or otherwise flawed because of the combination of SMA surfaces and general degradation. SMA, when combined with glass fibre, has the potential to bring about advancements in the road industry.
Objective:
The use of glass fibres to enhance the mechanical characteristics of Stone Mastic Asphalt.
Methods:
Marshall stability test, Resilient modulus test, Dynamic creep test, and Abrasion test.
Results:
The presence of fibre may increase the performance of the apparent Stone Mastic Asphalt, and a composition including 3 percent glass fibre results in improved stability and stiffness.
Conclusion:
A quantity of glass fibre equal to three percent is the optimal proportion to be used in the process of increasing the mechanical characteristics of SMA. The performance of glass fibres with a lower volume per unit is better than those with the largest volume per unit.
1. INTRODUCTION
To a certain degree, the structure of the pavement can support the loads. However, improper pavement that leads to surface deformations, cracks, and potholes is the cause of a growing number of accidents that have happened. Because of the lack of friction between the car's tyres and the surface, an unanticipated acceleration of the vehicle occurred as a result [1-16]. The solution to this problem is to make the road more durable and strong, just as it is necessary to improve the attributes of the material that is used in the construction of transportation buildings.
To improve the functionality of road pavement, researchers and engineers have been looking at a variety of different approaches. Stone Mastic Asphalt (SMA) is one of the acceptable materials for pavement design to be used in highly travelled roads owing to the exceptional performance of the pavement structure [2, 7, 8]. This makes it one of the materials that can be used in the construction of roads. Because it contains a high proportion of broken aggregates, SMA increases the surface's skid resistance, making it safer for motorists and pedestrians, especially on wet pavements [3, 17, 18]. Additionally, compared to HMA mixture (traditional dense-graded) pavements, this kind of surface may increase the performance life by 30–40 percent and give stronger resistance to rutting brought on by large axle loads [4, 19, 20].
The primary objective of using these various modifiers and fillers is to accomplish the goal of enhancing the quality and performance of the paving mixture to achieve the desired results given the existing circumstances and to produce a safe road surface for motorists and other drivers. In addition, these modifications lessen the negative effects that roads have on the surrounding environment, such as the volume of noise from traffic and the overall cost of repairing and maintaining road constructions, and they make it possible to make use of natural resources [5, 21, 22].
Melts are the starting point for the production of glass fibres, which may then be created in a wide variety of compositions by altering the proportions of the raw materials used, such as substituting sand for silica, clay for alumina, calcite for calcium oxide, and colemanite for boron oxide. Because of this, distinct kinds of glass fibres display diverse qualities, such as resistance to alkali or high mechanical characteristics, by using varying percentages of silica or other sources. Products made of glass fibre are divided into categories based on the many kinds of composites in which they might be used. This work may result in the development of novel ways for enhancing the performance of fibres in asphalt pavement [6, 7, 23]. It is possible that adding glass fibre to the mixes will provide an improvement in the performance of SMA Mixtures; this may be investigated. As a result, the mechanical characteristics of SMA composites that include glass fibres are presented in this work. In addition to that, the purpose of this research is to encourage sustainability via the use of waste material that can preserve the long-term stability of SMA.
Thus, this study also intended to produce innovative contributions of the fundamental reason why the conventional asphalt binder greatly suffer from the aging process will be revealed. This will provide guidance and reference for the industry to construct better and more durable pavement in the future.
2. MATERIALS AND METHODS
2.1. Asphalt Binder
Asphalt binder that was used in this study was penetration 60-70 modified with 0-5% glass fiber at increments of 1%. Table 1 summarizes the physical properties of the asphalt binder [8].
Test | Description | Standards |
---|---|---|
Softening Point (°C) | 52.3 | ASTM D36 |
Penetration (mm) | 65.0 | ASTM D5 |
Penetration Index | +0.1 | ASTM D5 |
Ductility | 140.0 | ASTM D113-17 |
Storage Stability | 0 | ASTM D6930-19 |
2.2. Glass Fiber
The glass fiber used in this study is illustrated in Fig. (1).
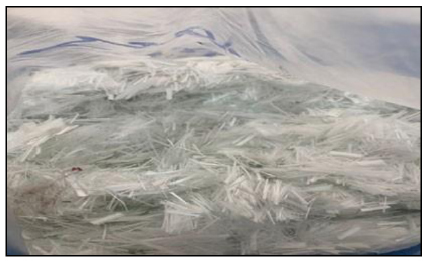
2.3. Specimen Preparation
To establish the specimens' identities, each specimen was processed using a Marshall Compactor machine. There were a total of fifty strikes delivered to each side of the specimen throughout the compacting process, with each of the samples receiving a total of fifty blows. The percentages of Glass Fiber contents that were employed in this research were 0%, 1%, 2%, 3%, 4%, and 5% by weight. These percentages were determined using the weight of the whole sample. The results of analysing the impacts of the combined Glass Fiber will be presented. The granite crush aggregates have been dried out and sieved into a precise size range, with a nominal size of 20 millimeters, following a standard specification (SMA 20). The next step in the procedure is the preparation of the materials and the testing of the aggregates. These tests include the Sieve Analysis, the LA Abrasion Value test, and Marshall Mix. These samples were then subjected to the Dynamic Creep test to evaluate their mechanical properties.
2.4. Abrasion Resistance
The Los Angeles Abrasion Machine is used to calculate the breakdown of compacted specimens in this research process. PFC, LRA, and hot-mix cold-laid consistency is measured in percent of weight loss (cantabro loss), which is related to the quantity and nature of the asphalt binder [9, 12].
The specimens were dried for two days at room temperature. Then, the specimens are stored at a test temperature of 25°C, for at least three hours before being tested. After the specimens have been stored for the requisite amount of time, weigh them (M0) and place them into the Los Angeles drum without abrasion loads (ball) as soon as possible. Next, the drum is rotated at a speed of between 188 and 208 rad/s for 300 revolutions.
Weight the specimen after a test (M1). For each specimen, the stone loss or attrition resistance is computed.
2.5. Volumetric Properties
Marshall equipment was used to determine the volumetric properties of the asphalt mixture. Among the parameters obtained from this test are stability, flow, and density [10, 11]. To perform this test, three compacted asphalt mixture specimens were prepared for each binder content. Then, those specimens were placed transversely to the load actuator. The load was applied until the specimen broke. Finally, the value of stability and flow were recorded. This test was conducted in accordance with ASTM Specification for Road Works (ASTM D6927–06).
Before the tests were performed, the samples were stored for six hours at a temperature of 25 degrees Celsius. After the specimens had been stored for the allotted amount of time, they were brought to the machine in Los Angeles where they were weighed before the steel balls were added. After that, the drum was rotated for a total of three hundred times without the presence of a steel ball at a speed that ranged from 188 to 208 rad/s when it was turned on [9, 11]. The evaluation of the stiffness properties of modified SMA was accomplished via the use of a dynamic creep test.
2.6. Dynamic Creep
Dynamic creep test was the test that was performed to assess permanent deformation by repeating the axial stress loading cycles and monitoring the axial strain [13, 14]. At various stress levels and temperatures, this test was conducted using Universal Tensile Machine (UTM) on cylindrical mixture specimens that were in vertical position. High temperatures may cause irreversible deformation of asphalt mixtures. Hence, this study carried out the test at temperatures of 40°C. The idea of the dynamic creep test used was parallel to the other repeated shear test, at a constant height with different positions of the samples. The repeated axial stress pulses were applied and LVDTs were used to evaluate the vertical deformation. At low viscosity, the samples become less stiff. This condition was more vulnerable to slip from traffic stresses. For almost 2 hours, specimens with a diameter of 100 mm and a loading force of 100 kPa were exposed to 3600 loading cycles. Before the test started, all specimens 91 were placed in a room at a specific temperature to make sure the sample was tested at a constant temperature.
3. RESULTS AND DISCUSSION
3.1. Abrasion Resistance
According to Fig. (2), the lowest abrasion value occurred at 2% glass fiber modification. The trend is consistent throughout the number of revolutions from 0, 100, 200, and lastly 300. This shows that the existence of glass fiber can provide sufficient resistance for SMA due to wearing from vehicle tire. From the graph, it also shows the optimum proportion is, followed by one percent after three hundred rotations. This study demonstrates that incorporating glass fibre into Stone Mastic Asphalt (SMA20) improves the mixture's cohesiveness and abrasion, allowing it to better withstand higher pressures caused by traffic loads at 1 and 2 percent glass fiber, respectively when compared to the control mixture, which contained 0 percent glass fiber. However, the addition of more than 2% glass fiber may not provide any significant impact on the abrasion resistance of SMA.
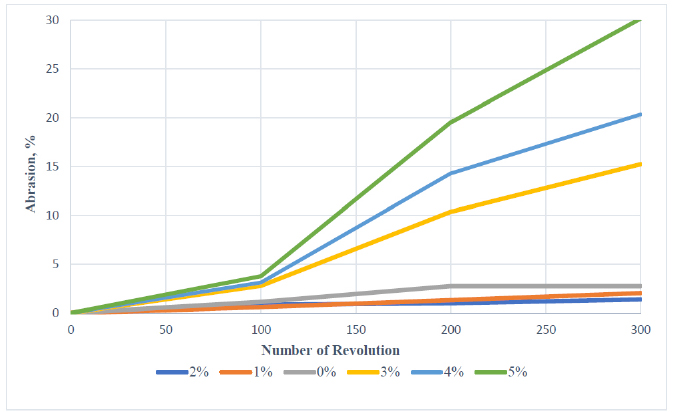
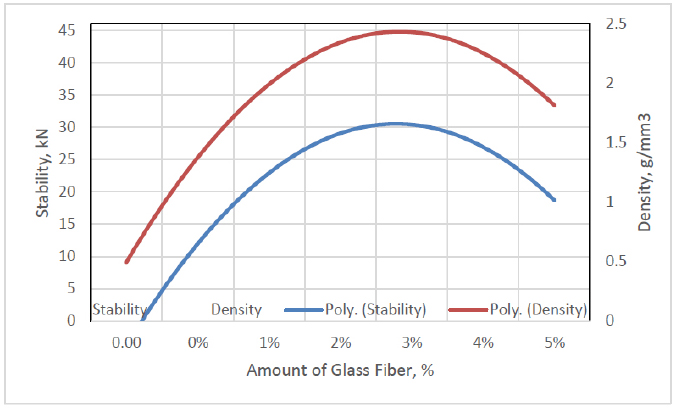
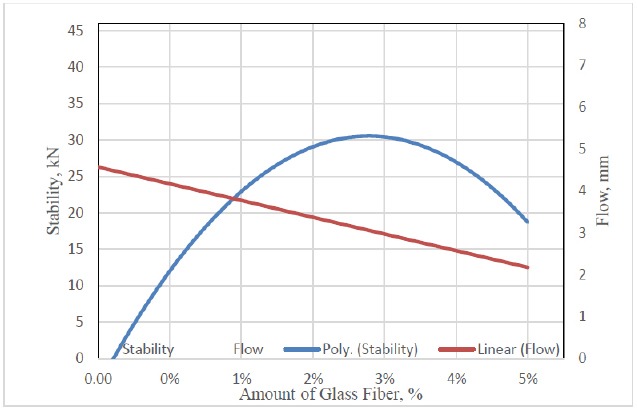
3.2. Volumetric Properties of modified SMA
3.2.1. Stability
The data for stability vs density for an SMA20 asphalt mixture that contains anywhere from 0 to 5 percent glass fibre are shown in Fig. (3). According to the graph, the quantity of fibre that constitutes 4% of the total has the highest possible value for both stability and density. There was a distinct pattern for both metrics, which showed that the stability and density would climb to a peak level at the quantity of fibre equal to 3 percent before beginning to decrease. There is evidence that suggests that increased stability and density lead to increased resistance to deformation. When there is no fibre present at all, the highest density is 2.14 g/mm3 and the greatest stability is 9450 N. However, when there is 4 percent of fibre present, the maximum stability is 45,000 N, and the maximum density is 2,206 g/mm3. The increase in density is around 2 percent, but the increase in stability is approximately 80 percent. On the other hand, increasing the quantity of fibre by more than 4 percent did not result in an increase in any of the metrics. There is strong evidence that increasing the quantity of fibre used in the SMA mixture to 4 percent was more beneficial in improving the material's density and stability. The values of flow versus stability are shown in Fig. (4). It was clear that increasing the quantity of fibre used led to an increase in flow value. This was shown visually. According to the Malaysian Public Work Department for Roadworks (JKRSPJ, 2008), the flow should not be more than 4 mm. However, the increment is still within the limit although it has increased.
3.2.2. Flow
Figs. (5 and 6) exhibit the flow performance of asphalt mix at varying percentages of the quantity of fibre. When increasing the quantity of fibre, the modified SMA20 combination generated flow values that were inconsistent with one another. The flow values fell somewhere in the range of around 2 mm to 4 mm. Flow values for surfing and pavement under heavy traffic category should be in the range of 3 mm to 5 mm, as specified by the Malaysian Public Work Department Roadworks standard (JKRSPJ, 2008). As a result, every specimen used in this investigation met the criteria established for the standard. Fig. (5) shows that there is a correlation between the amount of glass fibre in the sample mix and the rise in the density of the samples. The sample with the highest percentage of glass fibre has the lowest bulk density of 2.03 g/mm, but the sample mix that contains 4% glass fibre has the highest density of 2.206 g/mm. According to the suggestions made by JKR in 2008, the option with the greatest bulk density was picked. It is possible to estimate the amount of air that is present between the aggregate particles in a complete mix. As can be seen in Figs. (5 and 6), the flow rate experiences a little drop when there is an increase in the proportion of glass fibre. The sample that included 5 percent glass fibre had the lowest value for VFA, which was 0.617 percent, while the sample that had 1 percent glass fibre had the highest value, which was 0.996 percent. This demonstrates that the glass fibre particles, when coupled with bitumen, do not fill the gaps between the aggregates. As a result, there are an increased number of voids that are not filled with bitumen.
3.2.3. Stiffness
The values of the SMA mixture's stiffness are shown in Figs. (7 and 8) and vary according to the quantity of fibre content. Theoretically, a combination of asphalt with a higher stiffness will have a more excellent resistance and more extended durability. Damages to the surface of flexible pavements like ravelling and bleeding will be substantially less severe if the asphalt is mixed to a firmer consistency. Based on the graphs, it can be seen that increasing the percentage of fibre added to the SMA mixture to three percent results in maximum stiffness. Compared to the control specimen, which only has 15 KN/mm of stiffness, the value of stiffness at a 3 percent quantity of fibre is around 30 KN/mm. It seems that the inclusion of NS resulted in a stiffness improvement of the asphalt mixture that was fifty percent more than before.
3.3. Dynamic Creep
Fig. (9) illustrates the impact of 3600 strain cycles of dynamic creep with loading strain caused by the glass fibre mixed asphalt binder when the temperature was 40 degrees Celsius. The values of strain are lowest for the percentages of glass fibre content that are 1 percent, 2 percent, and 3 percent when compared to the value for 0 percent of glass fibre content. The glass fibre content showed the greatest amount of strain at 4 percent, while it was at its worst at 5 percent. At 3600 cycles, the strain value decreased by 81% compared to when there was 0% glass fibre content and the temperature was 40°C. The resistance to creeping in SMA mixes is directly correlated to the strain per cycle. The higher the resistance, the lower the strain per cycle. The addition of glass fibre to asphalt mixes generates an optimal combination of glass fibre and asphalt cement, which ultimately results in greater compressive and tensile strength.
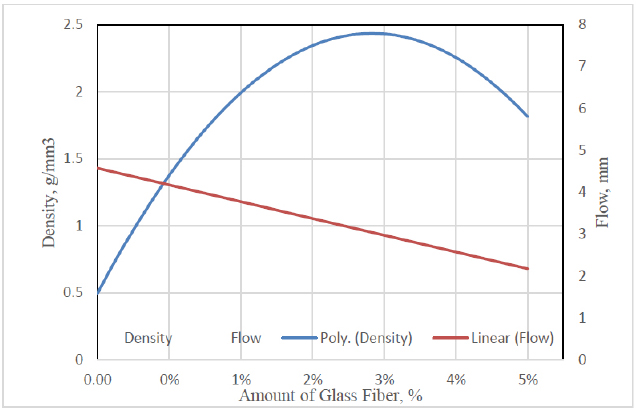
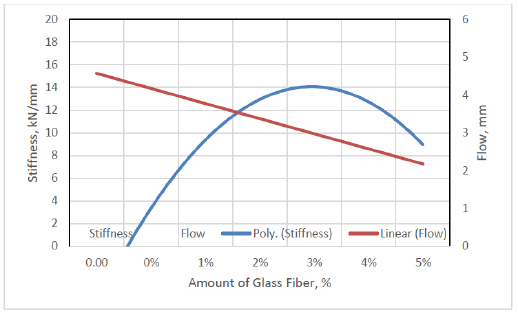
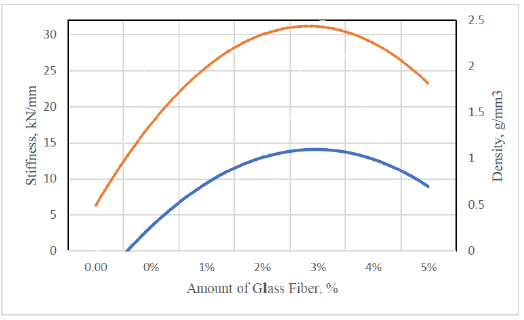
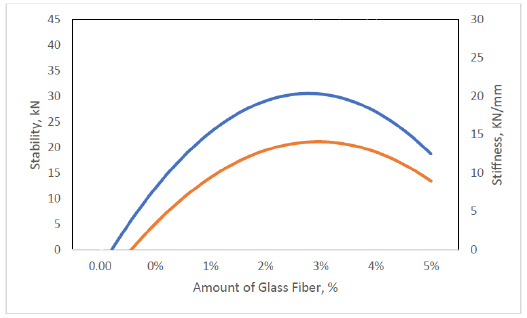
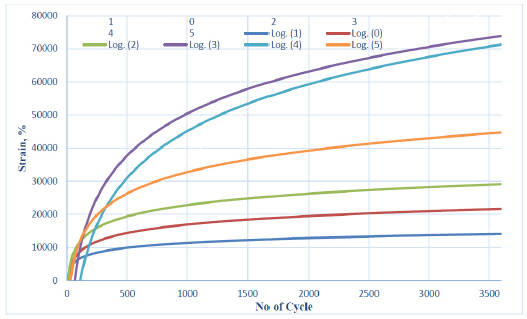
CONCLUSION
According to the research goals, the use of glass fibres to enhance the mechanical characteristics of Stone Mastic Asphalt has been fulfilled. This conclusion can be drawn from the findings of the study, which demonstrate that the objectives have been met. The performance of glass fibres with a lower volume per unit is better than those with the largest volume per unit. In terms of abrasion resistance and volumetric properties, 2% modified glass provides the highest abrasion resistance, stability, density, and stiffness. This occurs due to the accumulation of greater extra confining forces within a reduced volume of fibres. In addition, from the dynamic creep test, 4% modified glass fibre provide the highest shear strength of the mixes was noticeably enhanced due to the encasing of the bottom samples. According to the findings, a quantity of glass fibre equal to three percent is the optimal proportion to be used in increasing the mechanical characteristics of SMA.
CONSENT FOR PUBLICATION
Not applicable.
AVAILABILITY OF DATA AND MATERIALS
The data and supportive information are available within the article.
CONFLICT OF INTEREST
Dr. Ramadhansyah Putra Jaya is the Executive Guest Editor of The Open Civil Engineering Journal.
FUNDING
This study was funded by University Malaysia Pahang, Funder ID: UMP Internal Grant, (Grant Number: PDU213206).
ACKNOWLEDGEMENTS
Declared none.