All published articles of this journal are available on ScienceDirect.
Environmental Impacts of Jute Fiber-reinforced Mortars
Abstract
Background
Mortar is an essential material in the construction industry, serving as a binding agent in masonry. Integrating natural fibers into construction materials has gained significant attention due to their potential to enhance mechanical properties while promoting sustainability. However, mortar production involves processes that contribute to environmental impacts. In this research, jute fiber was selected as a reinforcement for mortar due to its potential to provide a sustainable and eco-friendly alternative to synthetic fibers, offering a promising solution for reducing the environmental footprint of construction materials.
Objective
This paper aims to investigate the mechanical properties and environmental impact of jute fiber mortar composites during the product stage with a cradle-to-gate approach, comparing their performance with that of traditional mortar used in Colombia.
Methods
The environmental performance of jute fiber-reinforced mortar (JFRM) was assessed using the CML-2001 methodology with OpenLCA software, alongside an Eco-audit tool to estimate the energy consumption and carbon emissions across the material, manufacturing, and transportation phases. Jute fiber (JF) was characterized through scanning electron microscopy (SEM). Additionally, the compressive strength of mortar incorporating jute fiber at 0%, 1%, and 2% by weight was evaluated after a 21-day curing period.
Results
Mortars modified with jute fiber (JF) show a reduction in compressive strength compared to plain composites, with decreases of approximately 15% for 1% JF and 21% for 2% JF. However, according to Colombian construction standards, composites with 1% JF still meet the minimum compressive strength requirements for plaster mortars. Additionally, these mortars offer excellent ductility and lower density than those without fibers. From an environmental perspective, the life cycle assessment results demonstrate that using 1% JF imposes a lower ecological burden than using 2%, with the Global Warming Potential (GWP) being the most significant impact category. While JF increases the GWP due to the emission of biogenic methane, the overall GWP impact rises by 2.8% and 3.9% with the addition of 1% and 2% JF, respectively. Furthermore, the eutrophication potential increases by 2.24% due to the use of fertilizers and insecticides in JF agricultural production. These findings suggest that the optimal balance between environmental impact and mechanical performance is achieved with 1% JF in the mortar.
Conclusion
Findings suggest that mortars reinforced with 1% jute fiber are suitable for cement composites due to their adequate physic-chemical properties and their positive effect from a sustainability standpoint.
1. INTRODUCTION
Jute is a long, soft, shiny vegetable fiber extracted from the bark of the plant Corchorus capsularis, family Malvacea [1], and to a lesser extent from tossa jute C. olitorius. Jute is one of the cheapest natural fibers and is second only to cotton in the amount produced and variety of uses [1]. It can be spun into coarse, strong threads. Jute fibers (JF) comprise around 65–70% cellulose, 13.6–20.4% hemicellulose, and 8% microfibril [2]. The jute plant may reach a height of 2.5 m and has a base stem diameter of 25 mm [3]. JF is environmentally friendly and has high tensile strength, good fire resistance, sustainability, and reusability. The fiber is 100% bio-degradable and recyclable. A hectare of jute plants consumes about 15 tonnes of carbon dioxide and releases 11 tonnes of oxygen [4]. The fabrication of JF composites involved several methods depending on the type, shape, and size.
Jute is predominantly harvested in equatorial, tropical, and sub-tropical regions, with extensive cultivation in India and Bangladesh. Other significant jute-producing countries include Myanmar, Nepal, China, Vietnam, Thailand, and Brazil [5]. Regarding fique and other fibers derived from the agave plant, Colombia is the primary producer with 17,500 hectares, Mexico with 12,000 hectares, and Cuba with 8,600 hectares.
The JF, also known as fique, is Colombia's national fiber. It is a hard, fine, shiny, white fiber known as Pita, Champadrao, or Cabuya. It is cultivated primarily in the central departments of Nariño, Cauca, Santander, and Antioquia. In Antioquia, it is famously referred to as “Oro Blanco” (white gold). The growth of coffee agriculture in the 20th century significantly boosted the production of fique sacks for packaging beans. Each year, Colombia produces between 22 and 24 thousand tons of Cabuya, with 8 to 12 thousand tons allocated to handicraft production, while the remaining is used for sacks. Ninety percent of coffee exports depend on fique sacks.
The construction industry has long sought ways to enhance the mechanical properties of mortar, with one sustainable approach being the incorporation of natural fibers, such as jute, into mortar mixtures. JF, known for being both biodegradable and abundant, offers an eco-friendly alternative to synthetic fibers, but opinions diverge on their effectiveness in improving mortar’s mechanical properties. Some studies suggest that jute fibers can bridge cracks and distribute stress more evenly across the mortar matrix, reducing the likelihood of sudden failure. In addition, JF has been reported to enhance mortar performance, particularly in terms of tensile and flexural strength, as evidenced by several studies that highlight their advantages in cement composites.
Further research underscores the benefits of JF in cement-based composites. JF is reported to yield improved compressive and tensile strength of cement-based composites [6, 7]. Ramakrishna and Sundararajan [8] found that adding JF, in varying amounts by weight of cement, significantly increased the impact resistance of plain mortar. Similarly, Chakraborty et al. demonstrated that incorporating jute fibers into the cement matrix not only increases the setting time and standard water consistency but also improves the physical and mechanical properties of cement mortar, particularly when the fiber content varies from 0.0 to 4% by weight of cement [9, 10]. Liu et al. [11] observed that fiber-reinforced concrete exhibited enhanced compressive and flexural strength when 30 mm long JF were mixed in at specific amounts (0.5-0.6 kg·m3), while Zakaria et al. [12] noted that jute yarn-reinforced concrete composites showed improved mechanical properties with varying cut lengths and volume contents. The authors in another research concluded that the presence of JF with more cement content strengthens the concrete to a greater extent [13]. Also, Sadiq et al. [14] tested lightweight cementitious composites containing different volume fractions of jute strands, and the results showed high toughness under flexural loading.
In other studies, Islam and Ahmed found that incorporating a small amount of JF positively influenced compressive strength while having no significant impact on the split tensile strength of concrete [15]. Similarly, Dayananda et al. [16] evaluated the compressive strength of concrete with different volume contents of jute fibers, approximately 10 mm in length, and discovered that the maximum compressive strength was achieved with a 0.4% fiber content. Kesikidou and Stefanidou [17] also found that JF, when used as additives at a 1.5% volume, contribute favorably to the strength and durability of mortars.
Further supporting the benefits of JF, Tiwari et al. [18] demonstrated that jute fibers increased both the compressive and tensile strength of concrete mixes, although these composites may not be suitable for use in coastal or marine areas. Research into high-performance concrete also showed that adding JF at 1% improves both mechanical and durability characteristics [19]. Other findings indicate that adding JF at 1% and 2% led to increases in compressive strength by 18% and 10%, respectively, compared to reference mortar samples at 28 days [20]. Moreover, Formisano et al. [21] conducted bending and compressive tests on hydraulic lime mortar reinforced with JF, concluding that fiber-reinforced mortars can be effectively utilized as building products. Gwon et al. [22] demonstrated that using 10-mm-long JF at a 2.0% volume fraction resulted in optimal rheological properties.
Additionally, studies on self-consolidating concrete (SCC) incorporating JF of a specific length (20 mm) at various volumetric fractions suggested that a reinforcement content of up to 0.25% is acceptable [23]. Meanwhile, Shrestha et al. [24] investigated the effect of using JF at varying percentages (0.5%-2% by weight of cement) on the compressive strength of concrete, reaching notable enhancements in strength, particularly with a 1% JF content.
Despite these advantages, some authors argue that the natural viability in JF properties, such as length, diameter, and strength, can lead to inconsistent results in mortar applications. The lack of standardization in JF production means that the mechanical properties of the resulting mortar can vary significantly.
Carvalho et al. [25] found that while the compressive strength of the matrix decreased with fiber addition, the modulus of elasticity was only slightly affected. Teixeira et al. [26] reported that using twisted jute yarns in mortars could create voids, leading to lower flexural strength. Majumder et al. [27, 28] also demonstrated that adding JF in different lengths and percentages to mortar mixes increased porosity, which consequently reduced the density and strength of the composite material.
The optimal fiber content and distribution within the mortar remain points of contention, as overuse of jute fibers can decrease workability and increase voids, potentially counteracting the benefits. Ensuring uniform distribution of jute fibers is challenging, and poor distribution can lead to localized weaknesses and inconsistent mechanical properties. When comparing various viewpoints, it is evident that while jute fibers can enhance the mechanical properties of mortar under certain conditions, their effectiveness is highly dependent on factors such as fiber treatment, content, lengths, and environmental conditions. Table 1 summarizes the literature review of the mechanical response of mortar composites modified with different doses and lengths of JF.
From an environmental perspective, Life Cycle Assessment (LCA) is a tool to assess the sustainability and ecological health indicators impacted by products, processes or services [29]. The environmental impact of construction materials is a growing concern, leading to a search for sustainable alternatives. Jute plants, for instance, contribute to environmental benefits. The plants have an average of 956.38 thousand tone leaves and 423.4 thousand tone roots yearly, which are rotten and mixed with the soil [30]. The jute root increases land fertility, preserves the ozone layer by absorbing CO2, and cleans the air by emitting O2 [31].
The LCA of jute fiber-reinforced cement-based materials generally shows a reduced environmental impact compared to traditional cement-based materials. This reduction is primarily due to the lower embodied energy and carbon footprint of jute fibers compared to synthetic fibers or additional cementitious materials. Studies like those by Merta et al. [32] confirm that the environmental footprint of cementitious composite with synthetic fibers is generally more significant than that of the composites with added natural fibers. Farinha C. B. et al. [33] also studied mortars with industrial wastes, replacing sand and cement with biomass ashes and textile fibers, and demonstrated that the reference mortars presented the highest environmental impact in all categories, while Khan M.B. et al. [34] found that incorporating JF into concrete decreases the environ- mental impact relative to alternate fiber types. Similar findings were found by Kathri et al. [35], showing that JF reduces the environmental impact (embodied carbon) with an optimal addition of 0.10% on concrete mixtures.
According to Santos et al. [36], LCA is essential for optimizing mortar, as these building materials play a significant role in modern construction and the lifespan of buildings. By developing mortars with a reduced environmental impact, the embodied energy in buildings can be significantly lowered. Using alternative materials, such as replacement or addition to conventional raw materials in mortar manufacturing, may represent an environmental benefit that LCA can quantify. While JF offers promising benefits for improving the mechanical properties and environmental sustainability of mortar, its effectiveness is highly contingent on careful consideration of fiber content, distribution, and treatment.
JF Content (%) | Length (mm) | Mechanical Response | References |
---|---|---|---|
1-4 | 12-38 | A substantial increase in tensile, flexural, and impact strength could be achieved by including short JF. | Mansur and Aziz (1982) [6] |
0.5-1.5 | 15 | An improvement in impact strength and increased flexibility under static loading was found. | Ramaswamy et al. (1983) [7] |
0.5-2.5 | 20-40 | The impact resistance was found to be 3–5 times higher than that of plain cement mortar. | Ramakrishna et al. (2005) [8] |
2-3 | 25 | The results show that the compressive strength decreases with the addition of fiber. | Carvalho et al. (2012) [25] |
0.5-4 | 5-20 | Jute reinforcement with 1% increases the cold crushing strength and flexural strength. | Chakraborty et al. (2013) [10] |
0-8 | 9 | The ultimate flexural strength of the composite increases with an increase in volume fractions of jute strands. | Sadiq et al. (2015) [14] |
1.5 | 10 | The addition of JF enhances strength in cement mortars by around 16%. | Kesikidou and Stefanidou (2019) [17] |
0.25-2 | 5-15 | A pseudo-ductile behavior was found for JF contents of 1%; however, the composites exhibited stress about 25% less than the unreinforced one. | Formisano et al. (2020) [21] |
1-2 | - | Composites with JF performed well in shrinkage and resistance compared to reference mortar. | Nayak et al. (2022) [20] |
1 | 15 | JF is used as yarn-propitiated voids that act as cracking propagators, which may be responsible for the lower flexural strength. | Teixeira et al. (2022) [26] |
0.5-2 | 5-30 | The mechanical properties of samples with JF content deteriorated in compressive and flexural strength, but the mixtures failed in a ductile manner. | Gwon et al. (2023) [22] |
0.5-2 | 5-30 | The addition of fibers increases porosity and reduces density, reducing the composite material's flexural and compressive strength. | Majumder et al. (2023) [28] |
This research examines the ecological and mechanical impacts of jute fiber-reinforced mortar (JFRM) compared to traditional mortar commonly used in Colombia. By adopting a cradle-to-gate approach, the research emphasizes the significance of understanding both the environmental footprint and the mechanical performance of JFRM. The environmental impact was assessed through an eco-audit calculation, focusing on energy consumption and carbon footprint, complemented by a CML-2001 assessment using OpenLCA 2.2 software. Additionally, the mechanical properties of the mortar were evaluated through compressive strength tests conducted at 21 days of curing. To further enhance the understanding of the material's performance, JF was characterized using scanning electron microscopy (SEM) and energy dispersive X-ray spectroscopy (EDX), providing insights into the microstructural characteristics and the possible bonding between jute and cement.
This research is crucial as it explores a sustainable alternative to conventional building materials and strives to contribute valuable knowledge on integrating natural fibers in construction. This could potentially lead to reduced environmental impact and improved mechanical properties in mortar applications.
2. MATERIALS AND METHODS
Commercial Colombian JF were washed to remove impurities and dried at 80°C for 24h. The fibers were cut by hand with a length of approximately 20 mm. The water content of the fiber was obtained using a RADWAG PMC 210/WH moisture analyzer at 105°C with an uncertainty of 1 mg, and the density was measured using an analytic scale with a sensibility of 0.02 g. Portland cement type I and light grey granite sand were utilized for the composites. Mortars were produced with a cement/sand/water ratio of 1:1:0.4, incorporating JT additions of 1 and 2% by weight of cement.
3. EXPERIMENTAL
The preparation of composites followed the ASTM C109/109-16 standard, using steel molds of 2 in x 2 in x 2 in. The cement paste was mixed with sand in a Hobart mixer at 139 rpm until the materials were fully homogenized, after which water was gradually added to the mixture. After 150 seconds of mixing, a 25 mm deep layer was filled, and compacted with 32 strokes in 4 stages of 8 strokes each, all completed within 10 seconds. The process was repeated for the second layer, and any excess material was removed. The samples were then placed in a humid chamber for 24 hours, followed by dry curing in an environment with approximately 76% relative humidity and a temperature of 22ºC for up to 21 days.
A scanning electron microscope (SEM) using the JEOL JSM2490 CV, equipped with energy dispersive X-ray (EDX) spectroscopy (OXFORD INCAPentaFET-x3), was employed to conduct morphological observations on JF fibers. EDX was used to perform an elemental analysis of the JF.
After 21 days of curing, each specimen's density and compressive strength were determined. Compressive strengths were evaluated according to Colombian standard NTC 220 using an INSTRON 5582 testing machine at a 2 mm/min rate. Triplicate samples were prepared for each composite, and the average value was reported. For comparison, additional samples without natural fiber were also tested after 21 days of curing.
It was carried out as an initial assessment of the energy demands and carbon emissions of the product for the materials and processes necessary to make mortar admixtures and transport them. A bill of materials was created from material data previously published in the literature. An assessment of energy (MJ) and CO2 (kg) emissions from material, manufacturing, and transpor- tation to the gate (Eco-audit) was performed.
The LCA assessment compared the environmental performances of ready-for-use mortar composites with and without JF based on ISO 14040 and ISO 14044 [37]. The LCA process involves four phases: (1) defining the goal and scope to establish the assessment context and identify the environmental aspects and boundaries; (2) conducting an inventory analysis to quantify the energy, water, and materials used and their emissions; (3) assessing the potential human and ecological impacts of these factors; and (4) interpreting the results to identify the most sustainable option while considering the assumptions involved [33].
The environmental sustainability of mortars was quantified at the product stage. A cradle-to-gate environmental estimation was conducted using OpenLCA software (version 2.20). Five impact categories from Leiden University were analyzed according to the Institute of Environmental Sciences (CML-Centrum voor Mili- eukunde Leiden) methodology [33]. The functional unit produced one cubic meter of mortar composites ready for use.
4. RESULTS & DISCUSSION
4.1. Characterization of JF
JF exhibited an average density of 1250 kg/m3, lighter than the JF reported in literature, 1480 kg/m3 [38]. Water content was an average of 16.26 ± 1.97%, slightly higher than the reported before [3, 39-41]. SEM results show that untreated JF has a rough and porous surface, leading to an effective surface area for bonding the fiber to the matrix (Fig. 1). It has been found that the rough surface improved the mechanical interlocking at the interface [39]. An average diameter of JF obtained by SEM was around 187.94 ± 19.6 μm. This value is close to the one reported by Song et al. [3].
The composition of JF can vary based on factors such as weather conditions, soil type, flood season, and extraction methods [40]. Energy-dispersive X-ray (EDX) analysis reveals that JF primarily contains oxygen (O), carbon (C), and significant amounts of calcium (Ca) Fig. 2a, b. These findings are consistent with previous studies [42].
4.2. Mechanical Properties of Mortars
The interface between JF and the mortar paste exhibited strong adhesion, leading to improved cohesion compared to mortars without JF. After reaching the ultimate compressive load, samples containing JF showed minimal physical separation between the damaged sections, suggesting a potential beneficial effect of the natural fiber in maintaining structural integrity [28]. Table 2 summarizes the mechanical properties of the studied composites, presenting the mean values of three specimens of compressive strength (MPa), elastic modulus (GPa), density (kg/m3), and compression toughness index (CTI). The CTI was determined by dividing the area under the stress strain of each curve until the corresponding vertical deformation when the load drops to 0.85 times the ultimate load compared to that of pure mortar [43]. The index is dimensionless and ranges from zero to one. Fig. (3) shows the behavior under compressive loads for mortar with 0, 1, and 2% JF at 21 days. The curves show that adding JF allows a soft descending until failure.
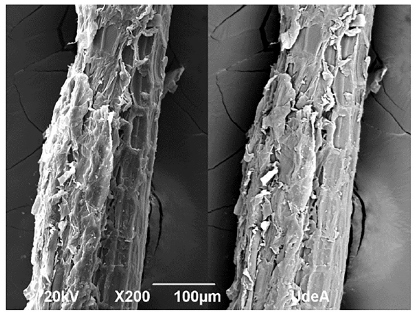
SEM image of a JF.
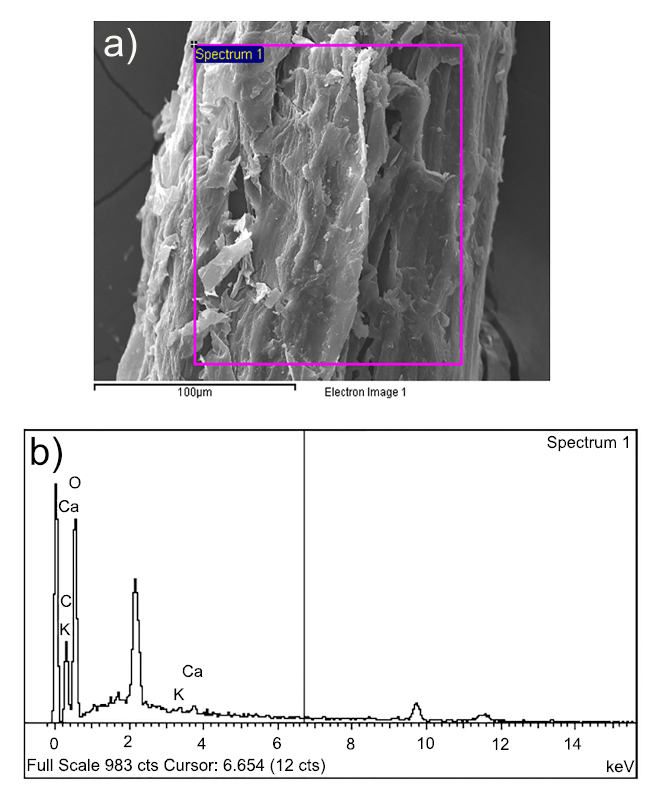
SEM micrograph of a JF from a) external wall and b) EDX results.
Mix | % JF | Max. Stress (MPa) | Elastic Modulus (GPa) | Density (kg/m3) | CTI |
---|---|---|---|---|---|
M-0 | 0 | 19.23±2.76 | 1.27±0.43 | 1991.19±18.86 | 1 |
M-1 | 1 | 16.31±2.33 | 0.94±0.89 | 1984.76±26.89 | 1.78 |
M-2 | 2 | 15.16±0.68 | 0.68±0.37 | 1972.03±15.60 | 3.59 |
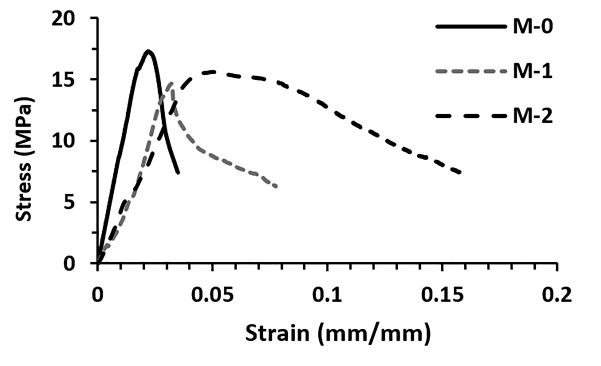
Strain-stress curves for mortar with additions of 0, 1, and 2% of JF.

Compressive strength (black data series) and density (grey data series) for mortar with additions of 0, 1, and 2% JF.
Adding JF reduces the matrix's elastic modulus. As a result, the toughness of the composite increases as the JF content increases, indicating a higher capacity to absorb the energy of the composite [25]. These fibers act as barriers that resist the opening and propagation of cracks, effectively distributing the stress across a larger area and delaying the failure of the composite. The toughening of the composite can be explained by the intersection of the microcracks formed on the matrix, which creates a bridging effect. This bridging has been seen before on mortars modified with natural fibers [44-46]. The presence of discontinuous fibers in the matrix reduces the unstable propagation of macrocracks and permits a ductile post-peak behavior [44]. The CTI significantly increases with the increase of fiber content, exhibiting the energy absorption capacity of the composites.
According to the results, adding JT reduces the maximum peak stress, ranging from 15 to 22% for 1 and 2% of JF, respectively. The elastic modulus was decreased by about 26 to 46% for the exact mixes. The inclusion of JF reduces the workability of the mixture [44], and its porosity could be related to insufficient compaction, leading to the reduction of the composite's elastic properties.
Fig. (4) shows the compressive strength and density as a function of JF content. Generally, the compressive strength of mortars increases with curing time but decreases as JF content rises. This pattern has also been observed in concrete modified with JF [47]. During the initial days of curing, strength develops rapidly before slowing down. The mortar with 1% JF content added performed similarly to the control sample, while the mortar with 2% JF content showed significantly lower strength. The decrease in compressive strength may be attributed to additional voids created by the inclusion of the reinforcing material [48]. Also, it can be attributed to the fact that JF functions more as a filler than a binder within cement paste [47]. As the JF content increases, the surface area increases, resulting in less bonding cement. However, after 21 days of curing, the mortar containing 1% JF shows a slight decrease in strength, suggesting a possible pozzolanic reaction between JF and cement hydration products.
Additionally, the study notes a reduction in the workability of the mortar with higher JF content, which can give challenges during the application and handling of the material. The reduced workability, likely due to the fibrous nature of JF, could lead to difficulties in achieving uniform mixing and compaction, further affecting the mortar's overall quality and mechanical performance. These findings are consistent with those reported by Elinwa and Mahmood [49]. According to Colombian building codes and standards for structural masonry, mortars modified with 1% of JF achieved compressive strength values exceeding the minimum requirements for mortar composites (NSR-2010). The random orientation of fibers tends to provide more uniform behavior but less pronounced improvements. The results suggest that while there are trade-offs regarding mechanical properties, JF-modified mortars can still meet standards for plaster mortar applications.
4.3. Environmental Impacts of Mortars
4.3.1. Energy and Carbon Footprint of Mortars
A volume of 1 m3 was considered for each mix. The material phase used an embodied energy and carbon footprint for primary production of each component of the composites, as shown in Table 3. The origin of the raw material was the same place as the construction site. For the production phase, embodied energy and carbon footprint were used to process each component and manufacture the mortars using the mechanical mixer. The electrical consumption of the mixer was 0.12 KW of power during 5 min. The eco-data for manufacturing can be seen in Table 4 [51]. The transportation phase of raw materials was assessed by considering a base of 100 km distance. A 32-metric ton truck was used for all assessments with an embodied energy of 0.94 MJ/kg and a carbon footprint of 0.067 kgCO2/metric ton/km [1].
Fig. (5) shows the embodied energy results for the mix conditions. The more significant energy contribution is related to the material used to make the composites, followed by the manufacturing and transport phases. The results show that introducing the JF as an addition does result in a slight increase in embodied energy and carbon emissions. Energy demand for material has increased by nearly 1.23 and 2.46%, adding 1% and 2% of JF, respectively. The material phase demonstrates the most significant environmental impact compared to other stages, indicating that the Eco-Aware design should prioritize material selection. This sustainable material can be achieved by replacing cement or aggregates with low-energy materials like natural fibers.
Material | Embodied Energy (MJ/kg) | Carbon Emission (kgCO2/kg) |
---|---|---|
Jute fiber | 0 | 0 |
Mortar (Cement-Sand Mix) | 1.33a | 0.208a |
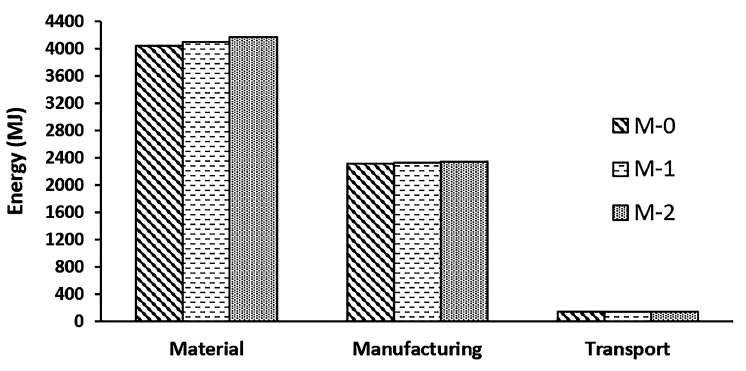
Embodied energy for mortar with additions of 0, 1, and 2% of JF.
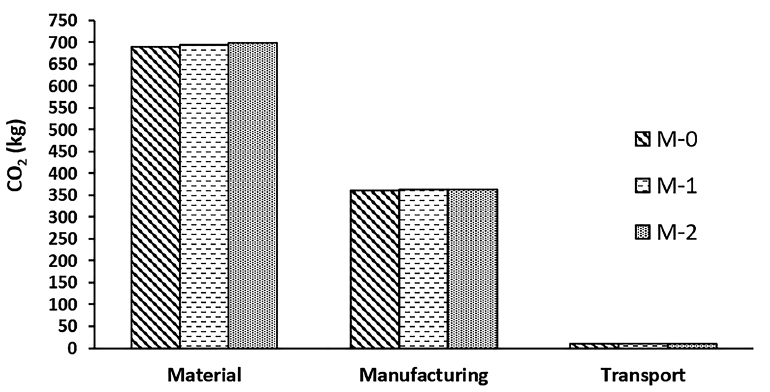
Carbon emission for mortar with additions of 0, 1, and 2% of JF.
Similarly, carbon emissions are increased by 0.53 and 1.07% using 1 and 2% of JF, respectively (Fig. 6). JF has the advantage of its renewable nature and high output in local sourcing. Also, the effect of a modified cement matrix with JF causes a more flexible behavior, which can be an advantage in absorbing energy in lightweight structures. There is also room to improve JFRM's environmental behavior by replacing the cement content in the mix.
4.3.2. Environmental Impact of Mortars
A volume of 1 m3 was considered for each mortar condition. The production process of mortars begins with the reception of raw materials, including sand, cement, and JF. The transportation of these materials was accounted for using a 28-ton truck over a standard distance of 100 km. The raw materials are then mechanically mixed in the previously specified proportions using an industrial mixer, with water added to produce the mortar mix (both with and without JF). The environmental impact was assessed across five categories: Abiotic depletion potential (ADP), acidification potential (AP), eutrophication potential (EP), global warming potential (GWP), and ozone depletion potential (ODP). The system boundaries of raw materials and processing are illustrated in Fig. (7). Taking into account the following assumptions:
- In this research, a “cradle-to-gate” boundary was considered; thus, the construction, maintenance, and end-of-life stages were not considered.
- The production of raw materials was not considered.
- The production of the raw materials was considered considering distance within the city of Medellín.
- The idemat 2023 database was used for data collection, which could present some uncertainty because of the lack of specific site data.
Environmental impact results are summarized in Table 5. The primary impact is associated with the GWP, the total climate change impact for all the greenhouse gases as a function of CO2 that would have the same effect over 100 years [52]. Adding JF to the mortar mix slightly increases the GWP values compared to the reference composite. 2.8 and 3.9% increase for 1% and 2% of JF, respectively. The main contribution of GWP in all cases is due to the cement production from the calcination of limestone and the combustion of fossil fuels, which is in concordance with previous studies [33, 36, 52]. JF increases the GWP due to the emission of biogenic methane. Fig. (8) shows the comparison between cement and JF GWP impacts, exhibiting the significant contribution of cement to the impact.
Due to the use of fertilizers and insecticides in the agricultural production of JF, eutrophication potential increases by almost 2.24%. The use of chemicals in agriculture production increases soil phosphorous and nitrogen levels, leading to freshwater eutrophication [53, 54]. During the processing of JF, the emissions are mainly caused by the energy consumption for decortication and fiber opening. However, the impact of artificial fiber production is usually three times higher [34].
The EP impact exhibits a small increment of 2.24% when JF was added. The EP is significantly influenced by cement and sand materials [33]. The excessive concentration of nutritional elements in aquatic systems, such as nitrogen and phosphorous, decreases water's oxygen. Cement shows a higher impact in this category. According to the results, the effect of ODP does not significantly influence the environmental sustainability of mortar with and without JF [55]. The same trend is observed with AP results, showing cement and sand with more relevance in this impact and a slight increase of the overall AP value when using JF, from 1.63 to 1.90 for 1 and 2% of JF, respectively.
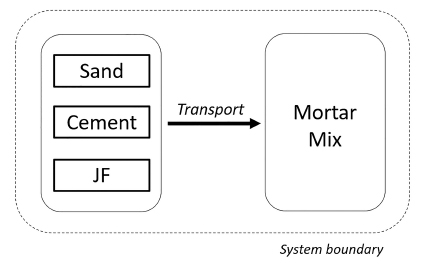
Life cycle assessment and system boundary.
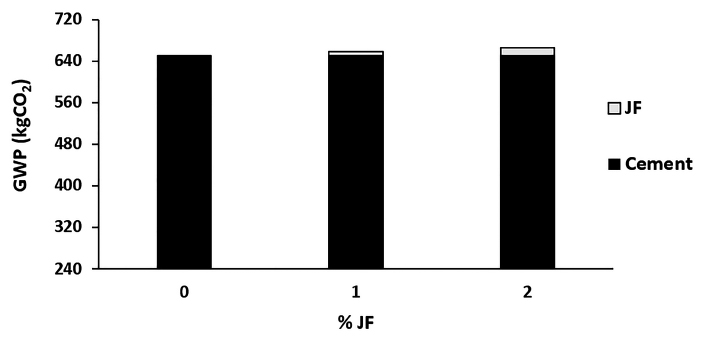
Global warming potential impact for mortar with additions of 0, 1, and 2% of JF.
Mortar | Environmental Impact Category | ||||
---|---|---|---|---|---|
ADP kg Sbeq |
AP kg SO2eq |
EP kg PO42-eq |
GWP 100a kg CO2eq |
ODP kg CFC11eq |
|
M-0 | 1.82e-7 | 1.603 | 0.181 | 653.575 | 3.178e-5 |
M-1 | 3.958e-6 | 1.629 | 0.185 | 671.848 | 3.178e-5 |
M-2 | 8.023e-6 | 1.633 | 0.185 | 679.066 | 3.179e-5 |
CONCLUSION
In this experimental program, the characterization of JF and its effect on the compressive strength of mortar were determined. Mortars modified with JF are suitable for cement composites due to their adequate physic-chemical properties. The following conclusions can be drawn:
1. Based on the SEM/EDX analysis and supported by findings in the literature, it is evident that jute fibers (JF) are composed primarily of oxygen (O) and carbon (C), which are typical constituents of organic fibers. The presence of significant amounts of calcium (Ca) suggests that these fibers may have undergone interaction with cementitious materials, leading to potential improvements in bonding within the mortar matrix.
2. Mortars modified with JF exhibit a reduction in compressive strength compared to plain composites, with decreases of about 15% for 1% JF and 21% for 2% JF. Despite this reduction, composites containing 1% JF still satisfy the minimum compressive strength requirements for plaster mortars as outlined in Colombian construction standards.
3. The dynamic modulus of elasticity of mortars appears unaffected by JF substitutions except at 2% by weight after 21 days of curing. This finding is consistent with the observed composite failure, which was similar across all mixtures tested.
4. The additions of JF add a little environmental burden to the whole life cycle assessment of mortar composites. According to the Eco-Audit, the material phase indicates higher carbon emissions and embodied energy. OpenLCA results suggest that for the main impact category, GWP, an increase of 2.8 and 3.9% was found for the 1% and 2% addition of JF, respectively.
5. Mortar containing 1% JF achieves optimal results from an environmental and mechanical point of view. Because of its ease, quality, and economic advantages, using JF as an alternative to conventional raw materials could represent an environmental benefit within the circular materials economy.
AUTHOR CONTRIBUTION
H.G: Writing the Paper; C.J.A: Data Collection; A.A.Z: Data Analysis or Interpretation;.
LIST OF ABBREVIATIONS
ADP | = Abiotic Depletion Potential |
AP | = Acidification Potential |
CML | = Centrum Voor Milieukunde Leiden |
CTI | = Compression Toughness Index |
EDX | = Energy Dispersive X-Ray Spectroscopy |
EP | = Eutrophication Potential |
GWP | = Global Warming Potential |
JFRM | = Jute Fiber-Reinforced Mortar |
JF | = Jute Fiber |
LCA | = Life Cycle Assessment |
ODP | = Ozone Depletion Potential |
SEM | = Scanning Electron Microscopy |