All published articles of this journal are available on ScienceDirect.
Optimization of Multiple Helical Fillets Surface to Suppress Rain-wind Vibration of Stay Cables: A Wind Tunnel Investigation
Abstract
Aims:
To develop a new cable surface for control rain wind induced cable vibration of stay cable.
Background:
Stay cables are light and vulnerable structures. Therefore, it can be easily excited by wind or rain wind interaction. Stay cables wrapped with a single helical fillet have been proposed so far. However, these countermeasures could prevent cable vibration well, especially in dry conditions.
Objective: Therefore, the objective of this research is to develop a new cable surface to control not only RWIV but also dry galloping of stay cable.
Methods:
A wind tunnel test will be used to investigate the RWIV characteristics and its new countermeasure.
Results: First, a rain wind-induced vibration of circular stay cable was reproduced in a wind tunnel environment. The effect of upper and lower water rivulets was examined to understand their role on RWIV better. A rainfall simulator was employed to generate artificial rainfall for two different wind tunnel experiments. Finally, to control the RWIV of stay cables, novel multiple helical surface fillets were used. The upper and lower rain rivulets can play a significant role in energizing the RWIV. It was also found that the multiple helical surface fillets can suppress the cable vibration well both in wet and dry conditions.
Conclusion:
Multiple helical fillets cable surface could successfully prevent both the RWIV and dry galloping. To fabricate helical fillet cable to control cable vibration, 04 to 12 fillets with sizes ranging from 3mmx7.5mm to 5mmx7.5mm and a pitch of 2.95D-4.78D (D: cable diameter) are the most influential parameters and suggested herewith for practical application.
1. INTRODUCTION
Rain-wind vibration of stay cables was first noticed in the Koehbrand Bridge in the 1970s in Germany. Later, during the erection time of the Meiko-Nishi cable-stayed bridge, RWIV of the stay cable was confirmed again [1, 2]. Numerous researchers reported the occurrence of RWIV in their research output [1-13]. The RWIV most occurred in cable-stayed bridges rather than another type of cable-supported bridges [3]. Several investigations using wind tunnel tests and field observations have already been carried out to reveal the mechanism of RWIV. However, some RWIV characteristics, such as the water rivulet's geometry and the bottom rivulet's function, are still yet to be determined. Further, it is also necessary to develop a new cable surface that can better control the cable vibration due to RWIV. RWIV was primarily discovered under moderate rain and wind interaction [1]. The generating process of RWIV was then modeled using a wind tunnel [2]. The importance of the rai33n rivulet downside of the stay cable in the galloping excitement was discovered to some extent. It was found that the rain rivulet's appearance depends on wind speed. The rain flow would exceed the gravity and frictional forces to produce the upper rain rivulet whenever the wind is strong enough. The lower rain rivulet stabilizes the vibration, yet the upper rain rivulet generates aerodynamic force, accelerating RWIV. Therefore, the upper rain rivulet is primarily responsible for RWIV.
Though Hikami and Shiraishi [1, 2] pointed out some vital role of rain rivulets at the cable surface in exciting the galloping excitation of cable, several other potential RWIV mechanisms have also been identified during the last few years [2-16]. In the beginning, the galloping theory was the most popular and widely used theory to study and explain RWIV [5, 6]. Then, RWIV was classified as a specific vortex-driven vibration caused by a combination of the Karman-vortex and the axial-flow along the cable [7]. Tanaka [8] discovered that when rain and wind interact at a certain angle of attack and rainfall intensities, the top and bottom rivulets form on the cable surface. The formation of rivulets changes the cable cross-section, and a variation in the cable's aerodynamics occurs. This change in aerodynamics mainly comes in terms of a decrease in drag and lift force coefficients with the increase in the angle of attack. This situation of aerodynamic forces generates negative aerodynamic damping, leading to Den Hartog galloping instability. The rain rivulets will vibrate after the cable starts shaking with the same frequencies. When this oscillation is coupled with the cable's flexural oscillation, it might cause aerodynamic instability, which amplifies the vibrations [8]. Further research revealed that RWIV is a vortex-induced vibration created by vortex shedding at low wind speeds, which differs from the standard Karman vortex [9, 10]. Gao et al. [14] suggested the bubble burst as a potential mechanism for the excitation of rain wind-induced vibrations. Chang et al. [15] discovered that the position and regular oscillation of the upper rain rivulet causes RWIV, and numerous countermeasures are evaluated for efficacy [15]. It was also found that small-diameter helical surface fillets have a certain level of efficiency against RWIV though it has poor performance against vortex-driven or dry galloping [16].
Previous research has shown that the upper rain rivulet influences cable galloping excitation. However, the exact form of the rivulet and how it moves during cable oscillation are yet to be determined. Furthermore, additional investigation is needed to clarify the function of the lower rivulet in RWIV generation. More importantly, the performance and efficacy of helical surface fillets to suppress RWIV are required for further detailed investigation. Therefore, the aim of this work is to better understand the role of the upper rivulet and lower rivulet in RWIV. Realistic artificial rainfall is simulated in a wind tunnel using a rainfall simulation to reproduce artificial rivulets on the cable surface. The wind's attack angle varies for a wide range of values. Finally, a parametric study on multiple helical surface fillets is carried out to optimize RWIV responses and dry galloping of stay cable.
2. MATERIALS AND METHODS
2.1. RWIV Experiment Conditions
Testing was conducted at Yokohama National University (Japan) in its wind tunnel facility. The wind tunnel has a working area of 1.3m × 1.3m (width x height). The possible highest wind speed is about 20 meters per second. The cable models in these experiments were supported by a spring system that allowed vertical vibrations as a one-degree-of-freedom system, as demonstrated in Fig. (1). The flow angle and inclination angle may vary with the cable's attitude. A homogeneous flow with a turbulence intensity of 0.6 was employed. A set of water nozzles were set at the wind tunnel ceiling to produce rainfall within the wind tunnel (Fig. 1). The wind speed and the rainfall volume varied from 7 to 15 m/s and from 35 mm/h to 50 mm/h, respectively. The angle of the cable is determined by the angles (α, β and β*), as shown in Fig. (1). The inclination angles (a) are 25° and 40°, whereas the flow angles (β) varied from 0° to 60°. Table 1 summarizes the essential parameters of the wind tunnel setup. Experiments were conducted with two different diameters of cable viz., 158mm and 110mm. The length of the cable model was 1.5 meters. Table 1 also shows the structural frequency and damping ratios calculated from free vibration testing. The damping ratio varies from 0.13% to 0.22%. The highest wind speeds were limited to 20 m/s, corresponding to a Reynolds number of approximately 2.1×105 for non-yawed angles. An accelerometer produced by Kyowa Electronic Instruments Co. LTD was used to capture the cable amplitude. The cable model vibrations were captured for 60 seconds at a sampling frequency of 50Hz.
Cable diameter: D (mm) | 110 & 158 |
---|---|
Cable length (mm) | 1,500 |
Rain condition (mm/h) | 35-50 |
Inclined angle α (°) | 0°to 60° (@15°) |
Flow angle β (°) | 25°& 40° |
Mass per unit (kg/m) | 8.15 (for diameter 110 mm) 9.86 (for diameter 158 mm) |
Fundamental frequency (Hz) | 0.78 – 0.9 |
Damping ratio of model | 0.13%-0.22% |
3. RAIN-WIND-INDUCED CABLE VIBRATION CHARACTERISTICS
3.1. Reproduction of RWIVs
Figs. (2-6) depict the RWIVs of cable at various wind angles. In these figures, reduced wind speed and reduced amplitude are defined by U/fD and A/D. In which A, U, D, and f are the vibration amplitude (m), wind speed (m/s), cable diameter (m), and model natural frequency (Hz), respectively. According to past experimental data [1-6, 17-21], RWIVs took place only for specific wind speeds and cable’s orientations. In the present work, vibration amplitude, i.e., more than or around 1.5 times of cable diameter (D), is observed for cable diameters 110mm and 158 mm. RWIV is mainly observed for flow angle (β) of 25°. For a larger flow angle of 40°, no significant amplitude vibration is observed. In both cases (110mm, β=25° and 158mm, β=25°), the RWIV occurred for an inclination angle of 15°, 30°, and 45°, where non-dimensional amplitudes of vibration above 1.5D are observed. Stay cable may gallop rapidly and divergently when rain wind-induced vibration forms. The highest amplitude that could be recorded in this experiment is roughly 2D because of the limitation of the supporting system. The current findings discussed here are also consistent with the findings of another study [17].
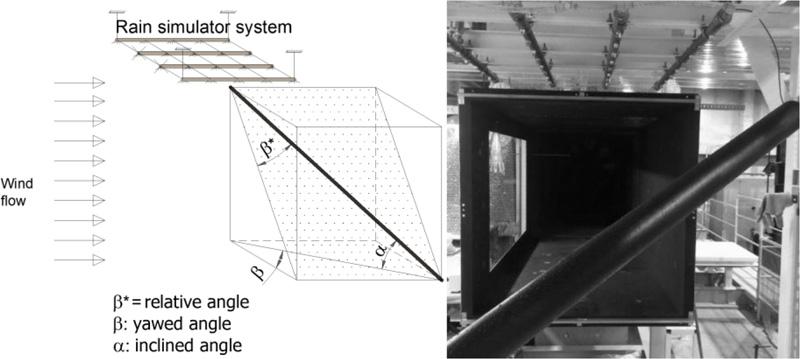
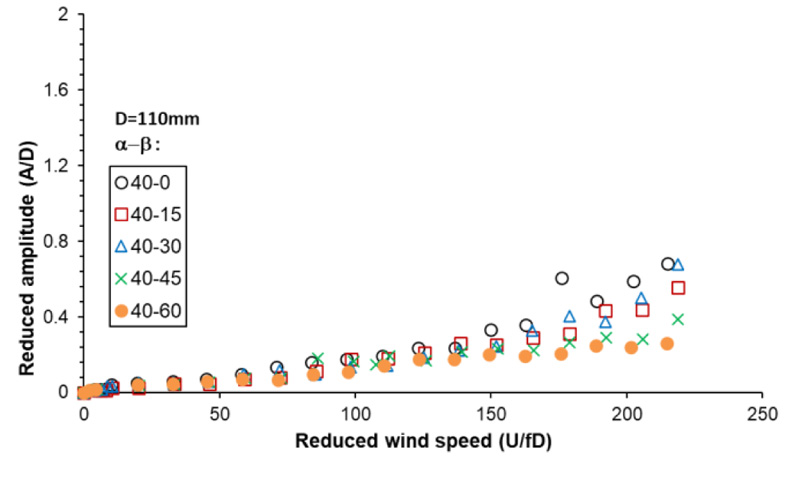
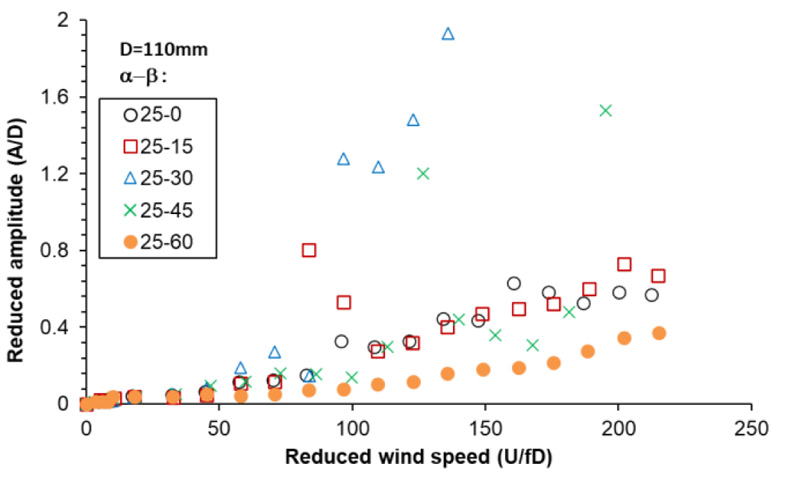
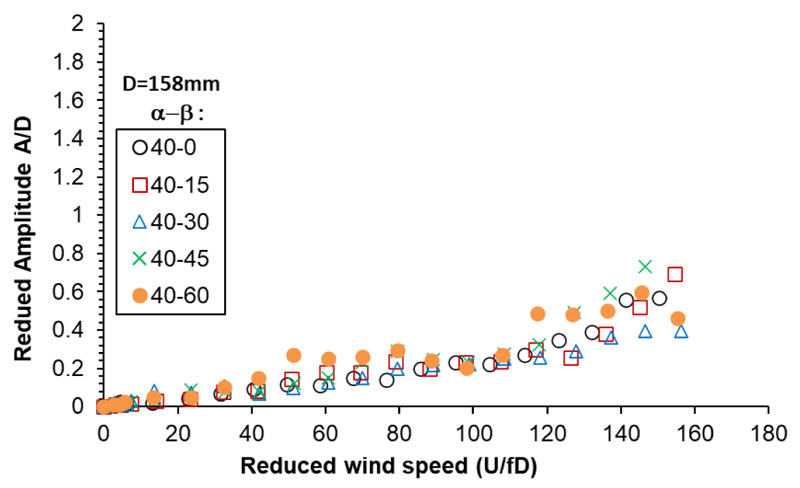
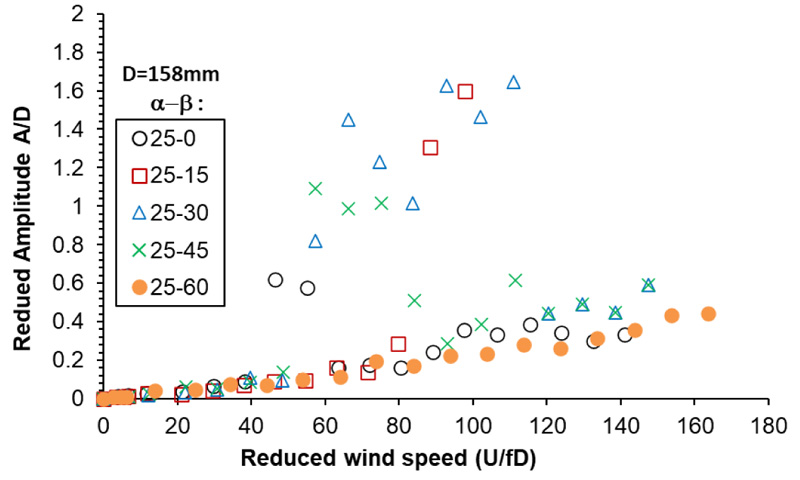
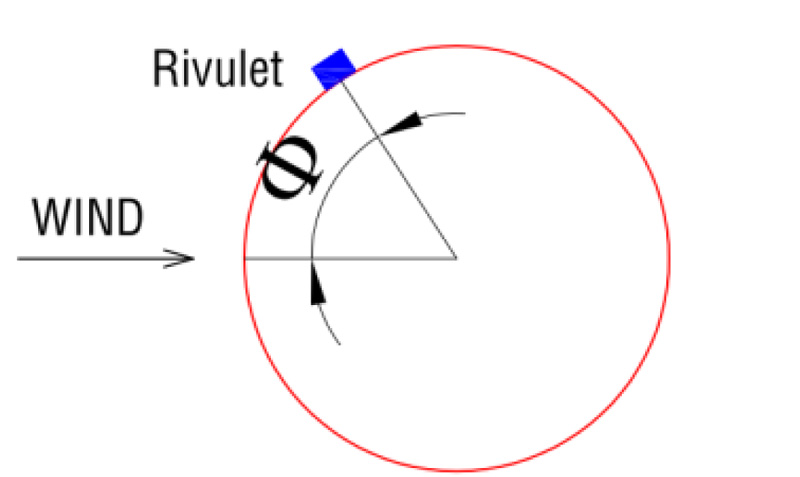
Figs. (2-5) show that the cable exhibits RWV for a specific range of wind speed and decreases again beyond that limit. The cable vibrates strongly with large amplitudes for a reduced wind speed ranging from 57 to 111 with a flow angle of 25° and an inclination angle of 30°. However, cable vibrations decrease rapidly with reduced speeds greater than 111. In conclusion, it can be said that rainfall may be advantageous in suppressing cable vibration for strong wind. Nevertheless, it instigates cable vibration for a specific moderate range of wind speeds (8-15 m/s).
3.2. Role of Upper Rain Rivulet in RWIV
The formation of RWIVs is vital and dependent on the upper rain rivulet [2-5]. Therefore, this part will explicate the role of upper rivulets on RWIV for a wide range of wind speeds. (Fig. 6) shows the relative position of the upper rain rivulet on the cable model surface. In this illustration, f is the relative angle of the rain rivulet that can vary from 0 to 90 degrees.
The yellow dashed lines in Figs. (7-15) portray the formation of the upper rivulet on the cable surface. The cable diameter for these cases was 158 mm, and the flow angle was 25° with an inclination angle of 30°. These images were captured during the time of cable vibration. There were no rivulets on the cable surface for a wind speed of 0 m/s.. An upper rain rivulet formed on the cable surface at a relative angle of 45° (Fig. 8) when the wind speed reached 5.4 m/s (Reduced wind speed U/fD=39.6). However, significant vibration was observed as the wind speed was not high enough.
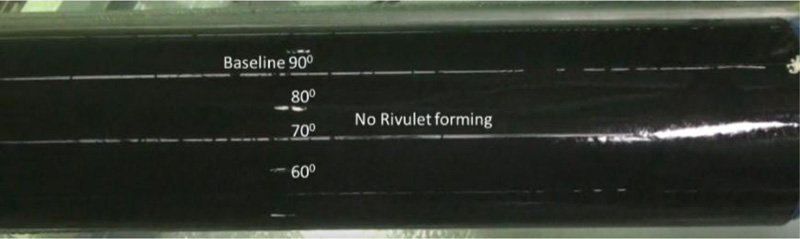
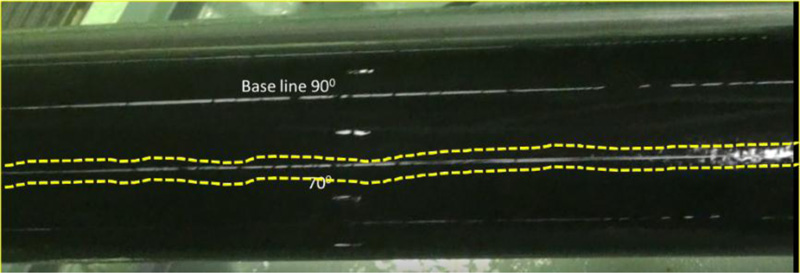
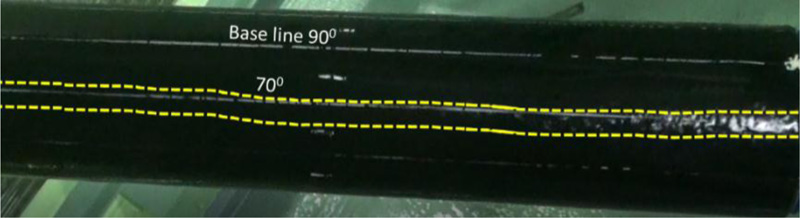
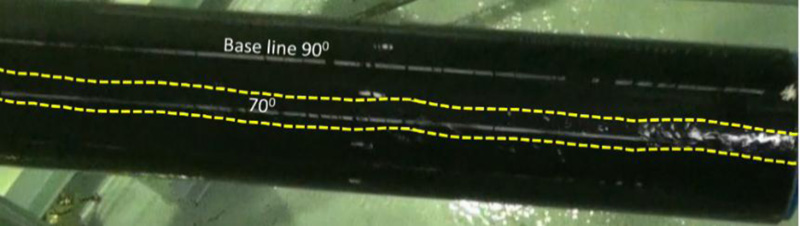
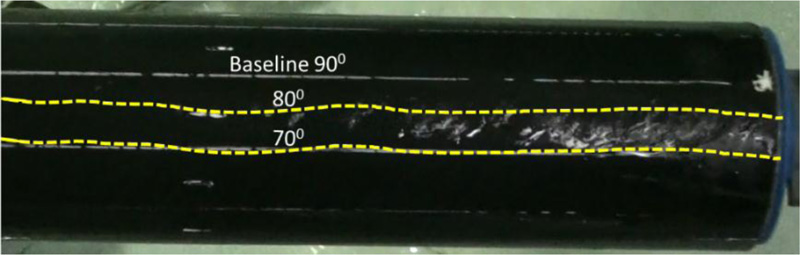
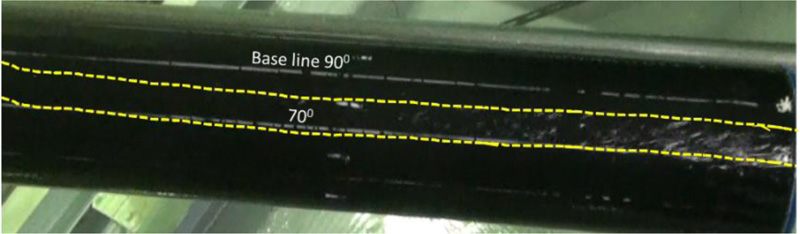
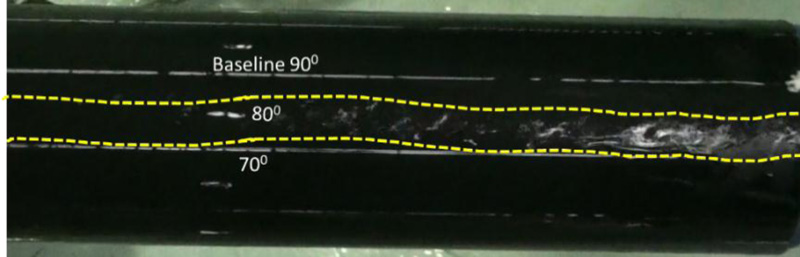
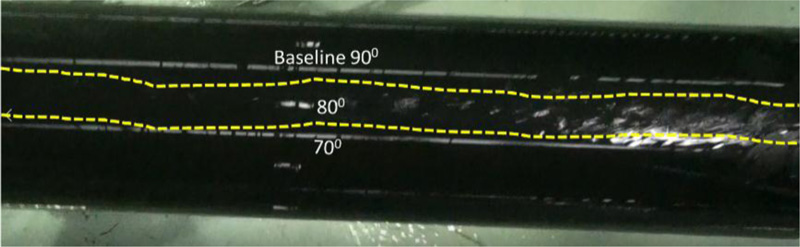
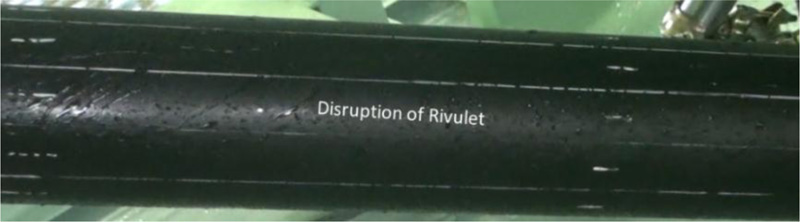
As wind speeds increase from 7.8 m/s (U/fD=57.3) to 15.12 m/s (U/fD=111), the upper rain rivulet continues to run on the cable surface and widens gradually in its width. In this wind speed range, the cable starts vibrating with significant amplitude. The position of water rivulets varies between 65-85 degrees from the stagnation point during these large-amplitude vibrations (Figs. 9-14). As the wind speed increases further, the rivulet disappears, and the divergent type vibration diminishes (Fig. 15). The critical position of the rainwater rivulet we found in the present study also has good coherence with the findings of Matsumoto et al. [18]. Matsumoto et al. [18] found the critical angle between 68-75°, while in the current study, it was between 65°-85°. The discrepancy in the higher range of rivulet position between these two experimental investigations might be due to differences in rainfall intensities or cable characteristics.
Furthermore, by recording the rain rivulets during wind tunnel experiments, it was observed that the artificial rivulet vibrates in synchronization with the same frequency of cable vibration [19]. This indicates that a self-excited vibration mechanism is involved in RWIV, which is responsible for big amplitude vibration [20]. In brief, forming an upper rain rivulet at the critical position angle between 65°-85°, together with moderated wind speeds (8-15m/s), can provide sufficient excitation force to generate RWIVs [21].
3.3. Role of Lower Rain Rivulet in Generating RWIV
Past literature has revealed that upper rain rivulet can cause a change in the cable's aerodynamic characteristics, which might excite RWIV [2, 4, 6]. In contrast, the lower rain rivulet generates damping forces that reduce cable motion and stabilize the vibration. Generally, the lower rain rivulet forms at an angle ranging between 10°-40° [2]. Lower rain rivulets cannot move to the upper position due to the equilibrium of wind, friction force, and gravity. However, lower rain rivulets may shift to higher positions, such as 45°, 60°, or 135°, when the cable surface is modified with the helical fillet. As a result, examining the impact of a lower rain rivulet is also critical for a complete comprehension of rain wind-induced vibration mechanism or proposing its countermeasures.
According to past research by Bosdogianni [6], lower rain rivulet forms had little effect on cable responses. As a result, an artificial rivulet of roughly 0.05Dx0.05D was used to imitate the lower rain flow in the current work, as shown in Fig. (16). The lower rain rivulet was made of usual wood, and it was attached to the cable on the lower side. The rivulet position angle (Υ), which was varied from 0° to 180° @ 15°, is used to investigate the influence of rivulet position angle on RWIV (Fig. 16). Table 2 lists the experimental parameters, and (Fig. 17) displays the effect of lower rain rivulet on cable response. The cable model vibrated divergently with an amplitude of 0.8D-1.2D at a reduced wind speed of 100 and a lower rivulet angle of 45° and 135°. However, minimal oscillations were observed for other positions of the lower rivulet, and in some cases, the amplitude of vibration was even smaller than the cable with no artificial rivulet. Therefore, this investigation shows that the lower rain rivulets have both positive and negative effects on galloping instability. In conclusion, the upper rain rivulet contributes to RWIVs, but the lower rain rivulet also plays a vital role in cable vibration. In rare circumstances, a lower rain rivulet may stimulate RWIVs without an upper rain rivulet.
Experimental Parameters | Values |
---|---|
Damping ratio | 0.11% |
Flow angle x Inclined angle | 30°x25° |
Model mass (kg) | 11.1 |
Fundamental frequency (Hz) | 0.95 |
Rivulet locations | From 0° to 180° |
4. RESULTS AND DISCUSSION
4.1. Optimization of Multiple Helical Fillets for Stay Cable to Control RWIV
A single helical fillet on stay cables is commonly used in several bridge projects. According to field measurements, wind or rain-wind-induced cable vibration can be mitigated to some extent by adding a helical fillet on the cable surface. Consequently, various wind tunnel studies have alreadybeen performed to develop a single helical fillet surface. Nevertheless, further investigation is still required to produce an efficient countermeasure that is effective both for RWIV and dry galloping of stay cable. Stay cables with small helical fillets showed considerable amplitude vibrations, as Kleissl et al. [22] reported. Aside from that, Gu et al. [17] found that the pitch of helical wire is the effective parameter for reducing the RWIV in stay cables. Vo et al. [23] found that a single spiral fillet wrapped in a cable can reduce cable vibration in no rain conditions for certain yawed angles [24]. However, the efficacy of helical fillet in mitigating RWIV and dry galloping is yet to be thoroughly examined. This part aims to optimize the parameters of multiple helical surface fillets to control cable vibration due to wind and rain. As illustrated in Fig. (18), a cable model with multiple helical fillets was fabricated using an HPDE tube and extra rubber-fillets (Table 3).
To ensure the suppression of both the RWIV but dry galloping, each experiment was conducted both in wet and dry conditions. Because the case of wind angle 25°x 30° was identified as a crucial wind attack direction for RWIV in the previous discussion, this orientation was chosen for the current tests. For these experiments, a cable with a diameter of 158mm was employed. Various types of multiple helical fillets were investigated to maximize the range for suppressing RWIV. The efficiency of the 02, 04, 06, and 12 helical fillets was examined. The original (counterclockwise) and reverse (clockwise) winding direction were also tested. The sizes of helical fillets vary from 5mm x 7.5mm, 2mm x 7.5mm, and 3mm x 7.5mm. The size of the fillet must be big enough to disrupt rain rivulets while also enhancing stability against dry conditions.
Number of Helical Fillets | Winding Direction of Multiple Helical | Sizes of Helical Fillet S= HxB (mm) |
Winding Pitch P (mm) |
---|---|---|---|
2, 4, 6, 12 | Anti-clockwise (original) | 2mm × 7.5mm | 3.86D |
3mm × 7.5mm | 3.86D | ||
5mm×7.5mm | 3.86D | ||
12 | Anti-clockwise (original) | 5mm×7.5mm | 3.86D |
2.95D | |||
4.78D | |||
12 | Clockwise (reverse) | 5mm×7.5mm | 3.86D |
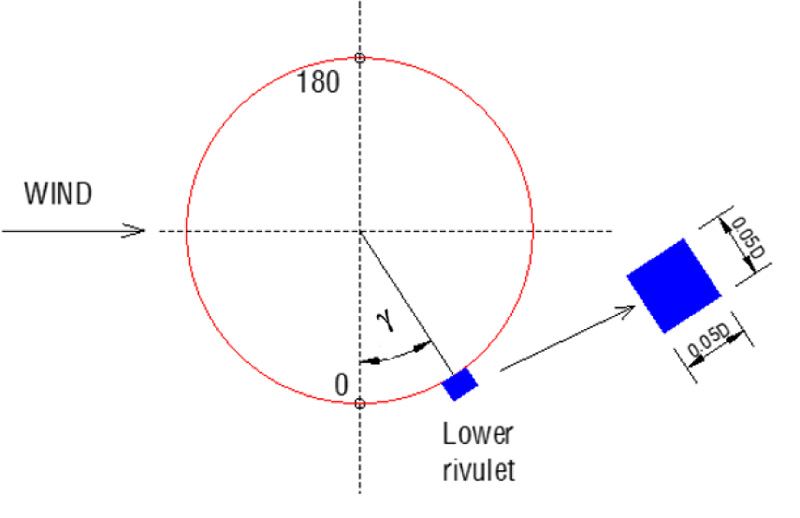
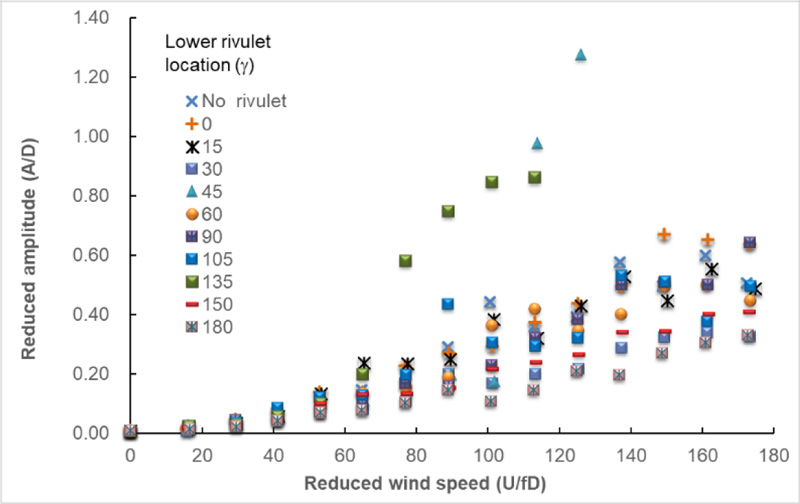
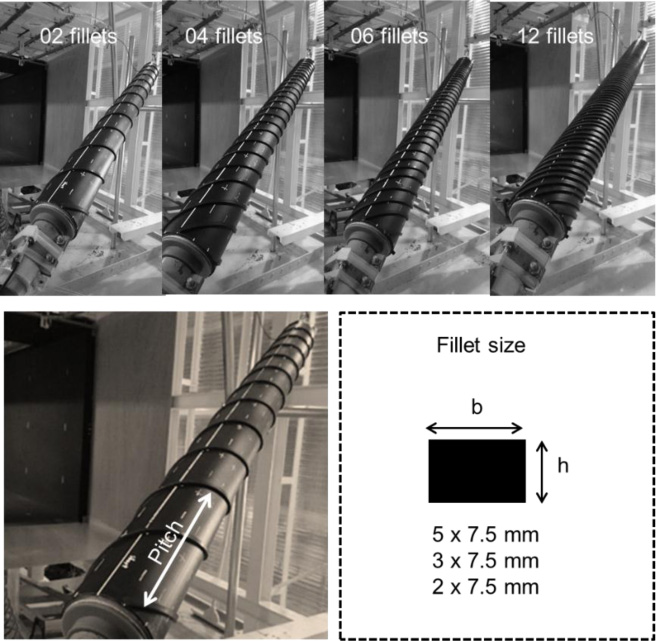
Furthermore, the helical fillet with a 27° winding angle had a lower drag force than other angles [24]. Consequently, the 3.86D winding pitch, which corresponds to a winding angle of 27°, was chosen for the reference cases. In addition, the effects of the pitch of 2.95D and 4.78D were also examined. The optimal helical fillet surfaces may be evaluated by comparing winding direction, pitch, and fillet size. Table 3 shows the details of the optimization parameters considered in the present study.
4.2. Number of Helical Fillets Effect
Different models were used to investigate the influence of the number of fillets on RWIV and dry galloping. Fig. (19) show the influence of the number of helical fillets on cable vibration. The cases of fillets 02, 04, 06, and 12 with a pitch of 3.86D and a dimension of 5mmx7.5mm were examined. RWIV was completely suppressed in cases with 04, 06, and 12 fillets, while two fillets displayed slightly higher vibrations with roughly 0.8D of amplitude. Figs. (20-21) also illustrate the influence of the number of fillets with smaller size fillets. The mitigation efficacy decreases slightly when the fillet size is reduced from 5mmx7.5mm to 3mmx7.5mm. The efficiency of 04, 06, and 12 helical fillets in the case of 3mmx7.5mm remains the same as in the same 5mmx7.5mm case. The 12 helical fillets are the most effective countermeasure to noticeably suppress the vibration. When the size of the fillets was reduced to 2mmx7.5mm, the efficacy to suppress vibration decreased significantly and can partially mitigate RWIV only. From the above discussion, the number and size of fillets have significant influences on mitigating cable vibration.
4.3. Winding Pitches Impact
The winding pitch is one of the most crucial factors to consider that has a considerable influence on the cable aerodynamic force and mitigation mechanism [25, 26]. Several pitches were used in this experiment to see how pitch distance affected the aerodynamic reactions. The pitches utilized were 3.86D (610mm), 2.95D(465mm), and 4.78D(755mm). In addition, the number of helical fillets was kept at 12 fillets. As demonstrated in Fig. (22), winding pitches have a minor impact on mitigation efficacy for 12 fillets. All the current pitches successfully reduced the galloping amplitude in the present experimental study. Even though the damping ratio of the cable was relatively low in the present testing, the considerable vibration was wholly suppressed in both dry and wet conditions. As a result, the pitch does not significantly influence efficiency. However, it is important to note that a pitch value of 610mm (3.86D) is the suggested pitch value since it has a lower drag coefficient than the other cases [24]. The pitch distance might have an influence on the vibration for the lower number of fillets, which has not been investigated here.
4.4. Impact of Helical Fillets Size
According to the above discussion, the number of fillets and their size are strongly correlated. To better understand the size impact, several types of fillets were compared for the 12 fillets case. The relationship between fillet size and vibration amplitude is shown in Fig. (23). Except for the size of 2x7.5 mm, RWIV and dry galloping were wholly suppressed in all other circumstances. Based on the physical observation, a 2 mm thick fillet could not stop the development of upper rain rivulets, and some water ascended over the helical fillet. This might have badly altered the cable's aerodynamic characteristics, resulting in a more significant reaction than in the other cases. On the other hand, the suppression of RWIV was unaffected by the winding direction. When the winding direction was reversed, the efficiency level was more or less like the original case.
4.5. Comparison of Multiple Helical Fillets Surface and Bare Circular Surface Cable
This section examines the efficacy of multiple helical fillets under a range of wind attack angles and cable orientations. Flow angles of 9°, 25°, and 40° were paired with the inclination angles varying from 0° to 60° to provide a diverse type of cable behaviors. The experiment was also carried out both in wet and dry conditions. Fig. (24) compares a bare circular cylinder with the circular cylinder with multiple helical surface fillets (12) [25, 26]. As can be seen that the multiple helical fillets have exemplary behavior over the bare circular cables in suppressing both the RWIV and dry galloping. It is worth noting that as the multiple successfully suppresses the vibration of the cable even under a low damping ratio (present experimental setup), this will even perform better for higher damping ratios.
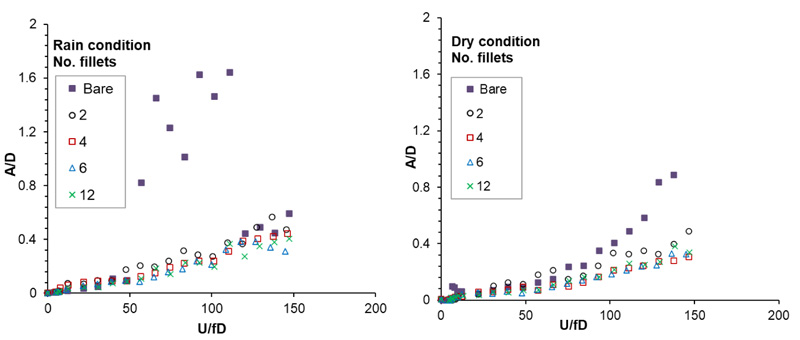
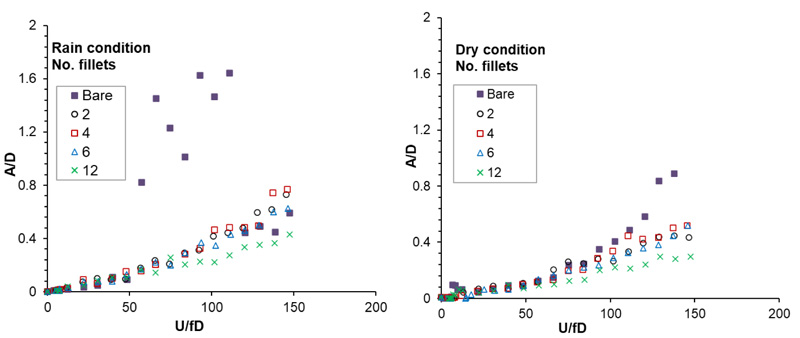
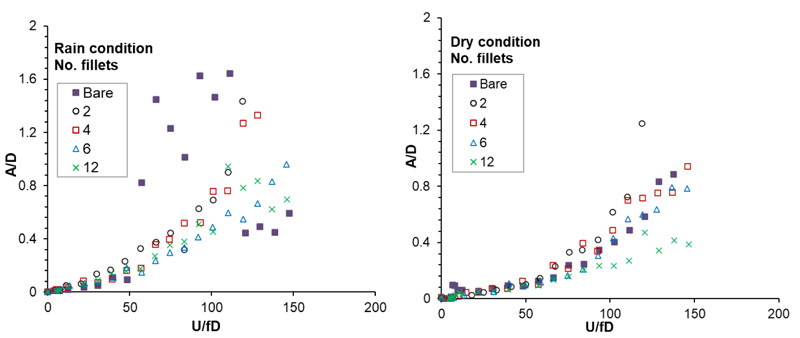
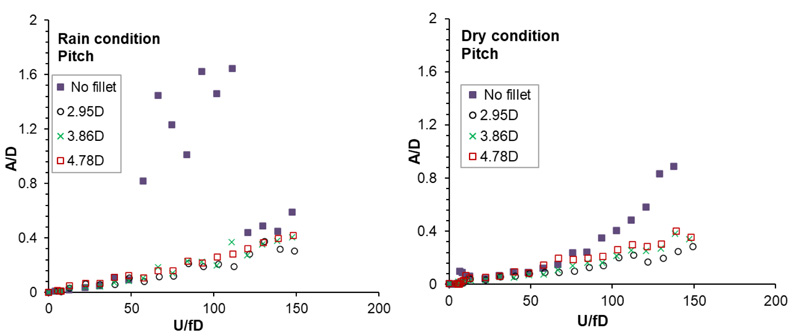
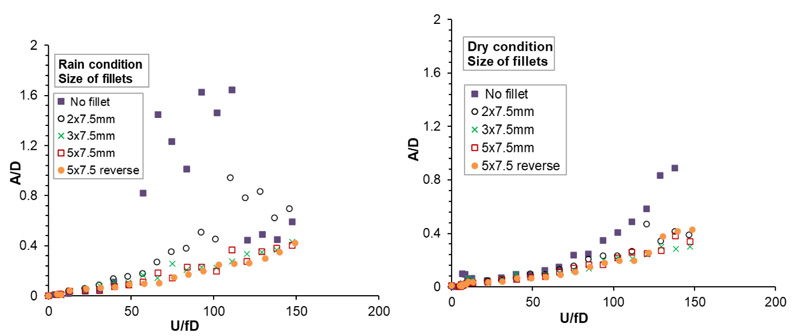
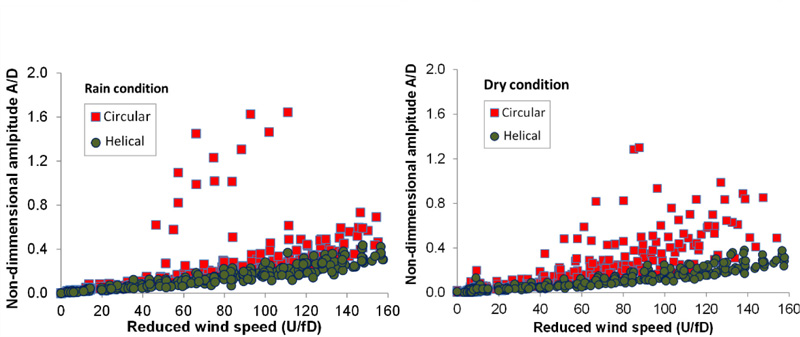
CONCLUSION
This study investigated the RWIV of stayed cables through wind tunnel tests. The tests with a smooth cable surface showed that the cable could vibrate with considerable amplitude in some specific conditions of upper water rivulet position (65°-85°), wind speed range (8-15m/s), flow (25°), and inclination angles (15° to 45°). The amplitudes were dramatically decreased as the wind speeds exceeded this range due to the disruption of the rain rivulet.
In an attempt to understand the role of upper and lower rain rivulets on RWIV, the shape and position of rivulets were investigated. The critical positions of the upper rivulet were found in the range of 65°-85°. They are critical in generating large cable vibrations in rain-wind conditions. Significantly, the lower rain rivulet can excite cable vibration for some specific cases. The critical position of the lower rain rivulet on the cable surface was found at 45° and 135°.
Based on the present wind tunnel investigation, multiple helical fillets cables could successfully prevent both the RWIV and dry galloping. To fabricate helical fillet cable to control cable vibration, 04 to 12 fillets with sizes ranging from 3mmx7.5mm to 5mmx7.5mm and a pitch of 2.95D-4.78D are the most influential parameters and suggested herewith for practical application.
CONSENT FOR PUBLICATION
Not applicable.
AVAILABILITY OF DATA AND MATERIALS
Data supporting the findings of the article are available within the paper.
FUNDING
This work was supported by The University of Danang, University of Science and Technology, code number of project: T2022-02-51.
CONFLICTS OF INTEREST
The authors declare no conflict of interest, financial or otherwise
ACKNOWLEDGEMENTS
The authors are grateful to The University of Danang, University of Science and Technology for financial support, and Yokohama National University-Japan for the wind tunnel experiments.