All published articles of this journal are available on ScienceDirect.
Mechanical Performance and Durability of Date Palm Fibers Repair Mortar
Abstract
Background:
Concrete is the most widely used material in the world after water. However, concrete could be damaged under aggressive environments and many concrete structures require repair and frequent maintenance. Readymade mortars with and without synthetic fibers such as polypropylene and acrylic are often used as repair mortars. The partial replacement of cement by supplementary cementitious materials and the use of alternative fibers such as natural and agro-waste fibers could reduce the environmental impact of readymade mortars.
Methods:
This paper presents a comparative study between the performance of laboratory made and ready-made repair mortars. The laboratory repair mortars were based on date palm fibers and local mineral additions (slag and natural pozzolan). The volume ratio of date palm fibers addition was 0.75% and mineral additions content were fixed at 15% as cement replacement. Compressive strength, flexural strength, shrinkage and the bond strength by slant shear test and tensile strength of concrete by the pull-off method were investigated. The durability of the mortar was evaluated by water capillary absorption.
Results:
The results indicated that the addition of natural fibers and the substitution of cement by 15% of mineral additions improves the flexural strength but reduces the compressive strength of the fiber-reinforced repair mortar. The lowest values of total shrinkage, water capillary absorption and sorptivity were observed for repair mortars based on acrylic fibers compared to repair mortars with natural vegetables fibers.
Conclusion:
The mechanical and durability performances of laboratory made repair mortars were comparable to those of readymade mortars.
1. INTRODUCTION
Repair and rehabilitation of damaged reinforced concrete structures have increased widely due to aging infrastructure and aggressive environments. The nature and origin of degradations are multiple; they can appear during construction due to an accidental load or damage during the service life of the structure from chemical attacks [1-4]. In addition, many reinforced concrete buildings are more than 50 years old, and many of them require maintenance and repair work due to their state of degradation [4]. Repairing concrete structures requires good knowledge regarding the support to be repaired, the materials used for repair and the environment to which they will be subjected. The success of repair and the good adhesion of the repair mortar depend on the treatment of the substrate surface of the existing damaged concrete [5-9]. Repair mortar should fulfill the requirements of the mechanical, physico-chemical, and economic characteristics [3]. Repair mortars should be durable, have low shrinkage, and be less prone to cracking. They should also be sustainable and have a low environmental impact. Synthetic fibers, such as acrylic and polypropylene fibers, have been used to enhance the tensile and flexural strength and fracture energy of cementitious matrices and improve the bond strength at the interface [10-12]. Acrylic fibers, independently of their dimensions, seem to offer mortar similar physical, mechanical and durability performance as that of traditional synthetic fibers (glass and polypropylene) [13]. Fibrillated polypropylene fibers have been shown to increase the flexural and splitting tensile strength and porosity of self-compacting concrete, and this increase is more significant with the increase in the length of the fibers [14]. Other researchers have reported that polypropylene fibres do not significantly affect the mechanical properties of concrete when used simultaneously with steel fibres but make the concrete more ductile and cause delays in concrete failure [15].
Mohseni et al. [16] reported a slight increase in the compressive strength with polypropylene fibers compared to reference mortar. The 3-day compressive strength of geopolymer containing 0.05% PP fiber increased by 67.8% [17]. The highest increase in compressive strength was that of the composite material reinforced with 0.5 wt.% polypropylene. A higher amount of polypropylene fibers (>1 wt.%) presented an adverse effect on mechanical performance [18].
Natural fibers from agro-waste materials are renewable and widely available and could be an alternative to synthetic fibers in repair mortars as they are more environmentally friendly [11, 19, 20]. Natural sisal fibres have been found to reduce the compressive strength of concrete but increase post-cracking ductility with increasing sisal fibres content [21]. Various natural fibres from the Amazon rainforest have been shown to improve the flexural strength of the mortars and prevent the fragile behaviour of unreinforced samples [22]. Date palm fibres are reported to reduce shrinkage, flexural and compressive strength and thermal conductivity and offer better resistance against sulphuric acid attack [23-25]. Khakpour et al. [26] reported an increase in flexural strength of more than 60% in some cases when using the palm date fibers in mortars. The date palm fiber could significantly strengthen the tensile strength of structural adhesives. This increase in strength exceeded 60% in some cases [26].
The addition of palm date fibers in mortar specimens generally improves both the post-peak behavior and the ductility compared to plain specimens and delays the failure of the composite material [27].
Readymade repair mortars are based on cement, which produces significant amounts of CO2 emissions in the atmosphere, and its substitution by alternative mineral admixtures helps to produce green mortar with low environmental impact [9, 10]. Mineral admixtures, such as blast furnace slag, metakaolin, fly ash, and natural pozzolan, are used as cement replacement material in mortar and concrete to reduce their negative environmental impact. Natural pozzolan has been used in repair mortar and found to have a lower elastic modulus and significantly decrease the coefficient of capillary absorption [25-28]. Suzuki et al. [29] studied fly ash with different chemical compositions and proposed a correlation to predict compressive strength from the chemical composition.
Some researchers have used natural fibers to enhance the mechanical and durability properties of repair mortars. Natural fibres have also been used for repairing and strengthening cultural heritage buildings [30]. For example, date palm fibers are reported to lower the density and compressive strength of mortar but do not significantly affect the porosity and capillary absorption [13, 19, 31]. However, the combination of both natural fibers and cement replacement materials on the performance of repair mortar has rarely been investigated. In this work, a novel idea is proposed by combining date palm fibers, which are an agro-waste product, with either blast furnace slag, which is a by-product of the steel industry or natural pozzolan, which is a naturally available material to produce a greener and more sustainable mortar with less CO2 emission. This study aims to experimentally investigate the effect of natural fibers and two mineral additions, namely blast furnace slag (SL) and natural pozzolan (PN), on the properties of repair mortars. The properties investigated include compressive strength, flexural strength, tensile strength, shrinkage, bond strength, slant shear strength, and capillary water absorption. In addition, a comparative study was undertaken between the properties of the laboratory repair mortars and the ready mixed repair mortars with synthetic fibers.
2. MATERIALS AND METHODS
In this study, cement (C) type CEM II / B 42.5 with a fineness of 415.5 kg/m2 was used. Its chemical composition is given in (Table 1). The repair mortar was prepared in the laboratory and contained by weight of cement, either 15% blast furnace slag (SL) or natural pozzolan (PN). The SL used was a granulated blast furnace slag from a local steel factory, and PN was from a local quarry of volcanic rocks. Both PN and SL were ground in the laboratory to a fineness of 350 m2/kg. The particle size curves of cement, slag, and pozzolan are shown in Fig. (1). The particle size distribution was determined by the laser particle size method based on the deflection and scattering of a laser beam striking a particle according to ASTM B-822-10 standard [32]. The chemical compositions of these mineral additions are shown in (Table 2). A superplasticizer (SP) based on a polycarboxylate called MEDAFLOW 30 was used. For the purpose of comparison of formulated repair mortars, three commercial ready-made repair mortars were used. They were repair mortars without fibers called Granipan-R03 (GRA-R03), a polypropylene fibers mortar called Granipan F30 (GRA-F30), and acrylic fibers called MASTER EMACO S488 (MA-EM-S488). The water/binder (W/B) ratio was set at 0.5 for all mixtures to obtain a plastic mortar.
For the preparation of the repair mortar in the laboratory, two types of sands (S) of the nominal maximal size of 3 mm and 5 mm were used with 50%, respectively. The date palm fibers used were plant fibers of cellulose nature (Fig. 2). The chemical composition of sands and the characteristics of natural date palm fibers (DP) are shown in Tables 3 and 4, respectively.
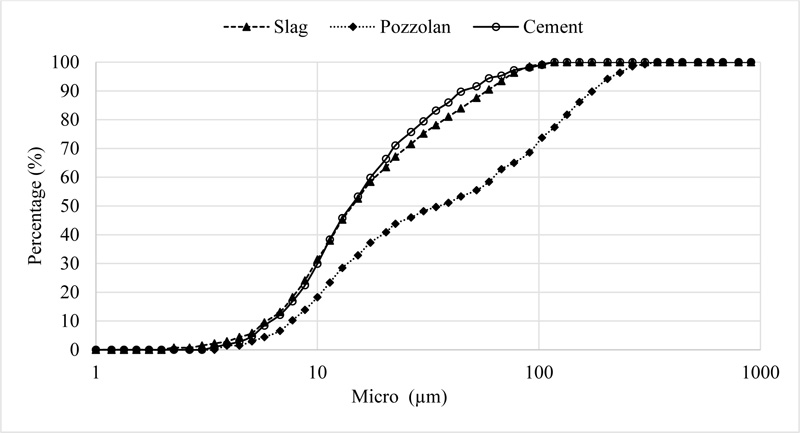
Element | SiO2 | Al2O3 | Fe2O3 | CaO | MgO | SO3 | K2O | Na2O | Cl | LOI |
---|---|---|---|---|---|---|---|---|---|---|
% | 16.37 | 3.90 | 2.73 | 66.04 | 1.37 | 2.68 | 0.57 | 0.13 | 0.015 | 10.56 |
Element | SiO2 | Al2O3 | Fe2O3 | CaO | MgO | Na2O | K2O | SO3 | TiO2 | MnO |
---|---|---|---|---|---|---|---|---|---|---|
PN | 47.37 | 16.3 | 11.84 | 12.68 | 6.56 | 3.20 | - | 0.19 | - | - |
SL | 40.10 | 6.00 | 2.00 | 42.20 | 4.70 | - | 1.20 | 0.15 | 1.20 | 2.60 |
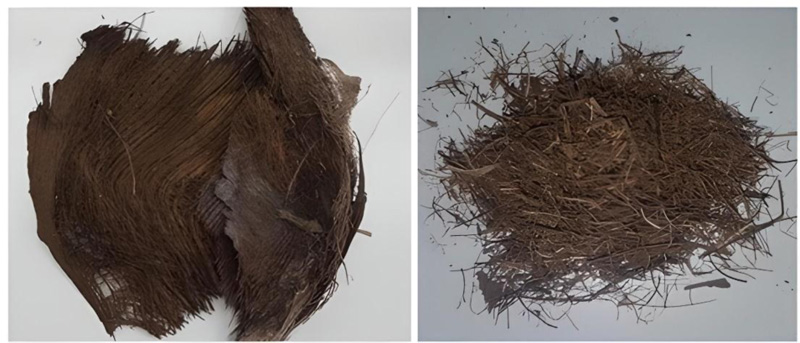
Fine Aggregates | SiO2 | Al2O3 | Fe2O3 | CaO | MgO | SO3 | K2O | Na2O | Cl | LOI |
---|---|---|---|---|---|---|---|---|---|---|
Sand 0/5 | 47.57 | 6.80 | 5.6 | 20.7 | 1.40 | 0.04 | 0.80 | 0.45 | 0.001 | 16.64 |
Sand 0/3 | 96.06 | 1.82 | 0.42 | 1.63 | 0.33 | 0.01 | 0.34 | 0.05 | 0.00 | 0 |
The concrete substrate mixture prepared in this study is of class (C25 /30). The details of the fives laboratory repair mortars mixtures prepared, including the control mix (MR), are given in Table 5.
Property | Date Palm Fibers |
---|---|
Diameter (mm) | 0.1 – 0.8 |
Length (mm) | 2 – 10 |
ρabs (g / cm3) | 1.3 – 1.45 |
Humidity (%) | 9.5 – 10.5 |
Absorption (%) | 96.83 – 202.64 |
Flexural strength (MPa) [20] | 240 ± 30 |
Mortar Mixtures | C (kg/m3) |
SL (kg/m3) |
PN (kg/m3) |
W (kg/m3) |
S (kg/m3) |
SP (%) |
DP (%) |
---|---|---|---|---|---|---|---|
MR (control) | 516 | 0 | 0 | 258 | 1548 | 1.2 | 0 |
MSL | 439 | 77 | 0 | 258 | 1548 | 0 | |
MPN | 439 | 0 | 77 | 258 | 1548 | 0 | |
MSLDP | 439 | 77 | 0 | 258 | 1548 | 0.75 | |
MPNDP | 439 | 0 | 77 | 258 | 1548 | 0.75 |
3. TEST METHODS
The mechanical performance of the repair mortar was assessed by the compressive strength and flexural tensile strength, which were performed according to EN 196-1 [33]. The durability was assessed by the water capillary absorption test, which was measured on cubic test specimens of 100x100x100 mm3 preconditioned according to the recommendations of the procedure of ASTM C1585-11 [34]. The test is a good indication of the porosity and water permeability of the material and hence its resistance to penetration of aggressive water environments. Before each test, specimens were removed from the container, wiped with a sponge, weighed and then returned to the container. The testing time used are as follows: 1min, 5min, 10min, 20min, 30min, 1h, 2h, 3h, 4h, 5h, 6h, 1 day and then every day for up to 8 days. Sorptivity values of the repair mortar mixtures were obtained from the results of the water capillary absorption.
Accessible porosity test was determined by weighing a specimen of concrete after immersion in water after saturation under vacuum. The specimen was maintained in saturation for 18±2 hours. After drying the specimens, samples were then weighed in water and air with a hydrostatic balance [35]. Accessible porosity to water, ɛ, is expressed as a percentage by volume according to Eq. (1).
![]() |
(1) |
The risk of cracking was assessed by shrinkage tests on prismatic specimens of 40mmx40mmx160mm, and the first measurement was taken after demoulding (24 hours) according to the procedure described in NF P 15-433 [36], and measurements were taken to 28 days. For the pull-off test, the support base concrete slabs used in this study were of grade C25/30. The pull-off test characterizes the bond of repair materials as the bond strength is compared to a minimal value for structural repair.
The surface of the base concrete slabs was treated by brushing. After cleaning with water, the repair mortar was applied manually over the entire surface at a thickness of 20 mm evenly. The cylindrical specimens were cast in Ø100 × 200 mm molds on a steel device to keep an inclination of 30°. After 28 days, the inclined surface was treated by brushing, then placed back into the molds and filled with the repair mortar (Fig. 3). The pull-off test was performed by applying a tensile force until failure in accordance with standard C1583 / C1583M - 13 (Fig. 4) [37].
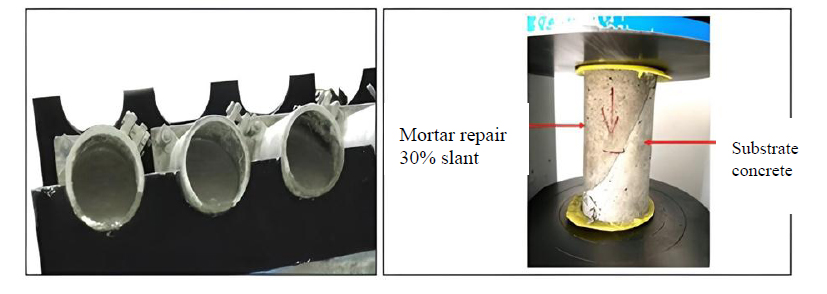
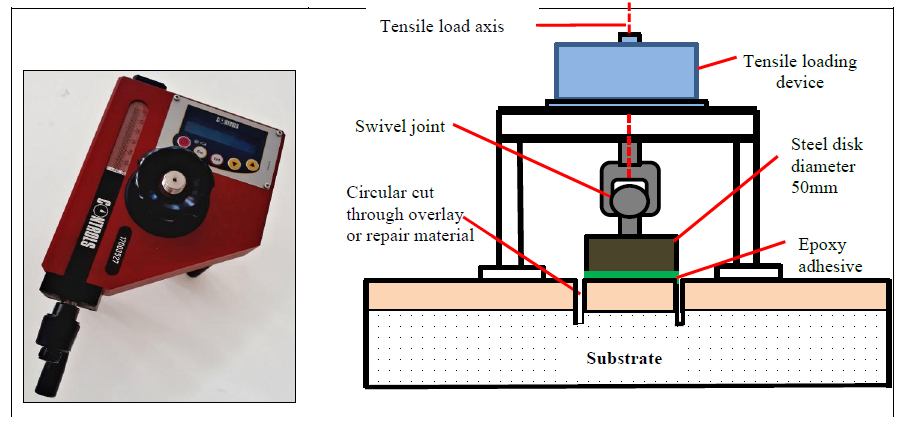
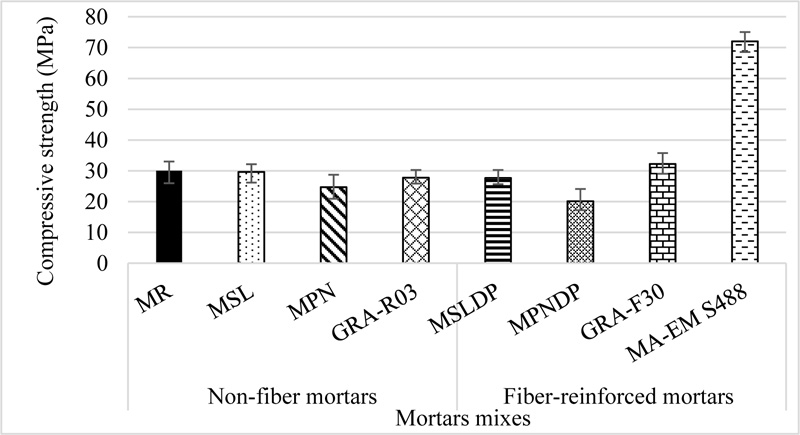
The slant shear test is a suitable method for evaluating adhesion under a combination of shear and compression in accordance with the standard ASTM C 882–05 [38]. The slant shear test is another type of bond test used to characterize the superficial cohesion of the substrate concrete. The composite cylindrical specimens were compression tested at 28 days after application of the repair mortar. The bond stress is calculated using the following equation:
![]() |
(2) |
F: failure load,
D: cylinder diameter (100 mm).
4. RESULTS AND DISCUSSION
4.1. Compressive Strength
Results of the 28-day compressive strength of the different repair mortar mixtures as a function of the fiber content are shown in Fig. (5). It can be seen from this figure that mortar control (MR) has developed the highest compressive strength value of 30 MPa compared to other non-fiber repair mortars. In the case of mortar containing 15% slag as cement replacement, comparable compressive strength to that of MR is observed. On the other hand, a reduction in strength of 8% and 18% is noticed for the non-fiber repair mortars GRA-R03 and MPN, respectively. Palod et al. [39] showed a comparable 28-day strength when slag was used as 20%, 30%, and 40% of cement substitution by achieving 97.94%, 95.9%, and 99.5% compressive strength of that of the control mix. This is because the slag hydration process is very slow. On the other hand, Pasupathy et al. [40] and Mehta and Siddique [41] reported that the structure of the slag-based geopolymer concrete (GPC) was denser than that of the ordinary Portland cement (OPC), indicating the higher strength of the geopolymer concrete. The interfacial transition zones (ITZ) of geopolymer concrete were denser and more uniform, and the mechanical integrity of GPC was enhanced by the particle roughness.
Similar compressive strength is obtained for repair mortar based on polypropylene fiber (GRA-F30) with MR. Repair mortar with natural pozzolan and fibers led to a remarkable drop in compressive strength of 33% compared to MR. This is due to the slow pozzolanic activity of natural pozzolan. In addition, natural pozzolan decreased the flowability of mortar which degraded the uniform fiber distribution, causing a drop in compressive strength. These results are in agreement with those obtained by Benmansour et al. [31], who reported a decrease in compressive strength with the increase in date palm fibers content. However, Soltan et al. [42] and Çomak et al. [43] reported that the natural fibers could improve the mechanical performance of a cementitious matrix as a 2% hemp fiber addition had a positive effect on the compressive strength of cement mortars. On the other hand, Benmansour et al. [31] reported that the density and compressive strength of mortar decreased with increasing date palm fibers content. The maximum compressive strength was obtained for mixes with 5% of date palm fibers. It should be noted that plant fiber, in general, presents a high variation in its mechanical, physical, and chemical properties due to the age of the plant and from where the fibers are extracted and the soil and climate conditions. The shape, morphology of the cross-section of the plant fibers, and their mechanical properties vary with their length [42]. Readymade repair mortar with synthetic fibers presented the highest compressive strength, especially the mortar based on acrylic fibers.
4.2. Flexural Strength
Flexural strength results, presented in Fig. (6), show that the incorporation of mineral additions (SL and PN) decreases the flexural strength by 18% and 22%, respectively, compared to control mortar. This may be attributed to the pozzolanic hydration process, which is low. It can be seen from this figure that the use of a non-fiber repair mortar GRA-R03 leads to a reduction of 21% compared to MR; these results are very comparable to those with mineral additions. In the case of fiber mortars, a slight increase in flexural strength was observed for mortars MSLDP and MPNDP in the order of 3% compared to MSL and MPN at 28 days, respectively, but the flexural strength did not reach that of reference mortar. This is probably due to the pozzolanic effect of additions, which develops less quickly at early ages and due to the contribution of date palm fibers to the reduction of cracking. A comparison of the failure of samples of non-fiber and that of fiber repair mortars shows that the latter has a more ductile character during failure, which would indicate that the sample remains, after failure, attached to the fibers. On the contrary, Kesikidoua and Stefanidoua [44] showed that the behavior of natural fibers (jute, coconut, and kelp) of the same length in cement mortars led to an increase in flexural strength.
Natural fiber composites are reported to increase tensile strength and energy absorption with increasing fiber length [24, 26]. Using repair mortar containing polypropylene fiber (GRA-F30) does not provide any significant increase in the flexural strength at 28 days. This may be due to the reduced slenderness of the fibers used. Flexural strength of 0.5% and 1% of polypropylene fibers mortar increased [16], and the 3-day flexural strength of geopolymer containing 0.05% polypropylene fibers also increased by 36.1% [17]. A slight increase of 10% in flexural strength at 28 days was observed for acrylic fiber repair mortar (MA-EM S488) compared to MR. This could be due to the dispersion of the fibers, the high fiber content or the type of fibers that has a better impact on the formation of the cement matrix, which limits the propagation of cracks. This is consistent with other research works [13]. Better dispersion of acrylic fibers obtained by dry pre-mixing improves the flexural strength [13]. The mechanical properties of natural fibers composites increased significantly with the addition of fibers as they have higher tensile strength than the matrices [24]. Gadri and Guettala [45] showed that the high roughness of surfaces improved flexural strength.
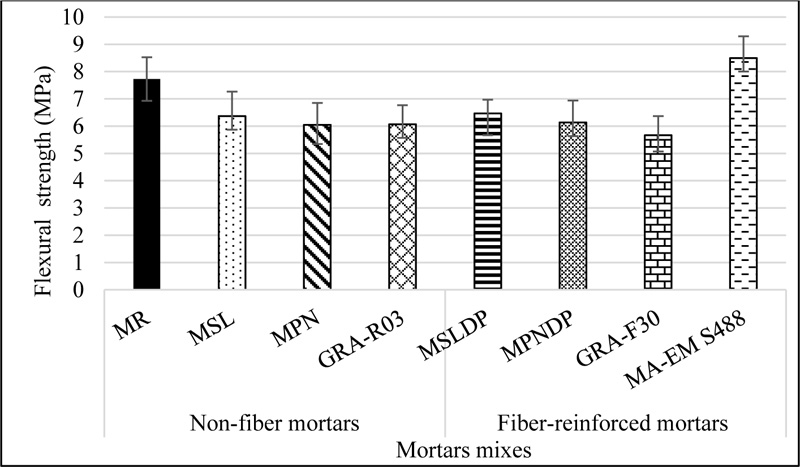
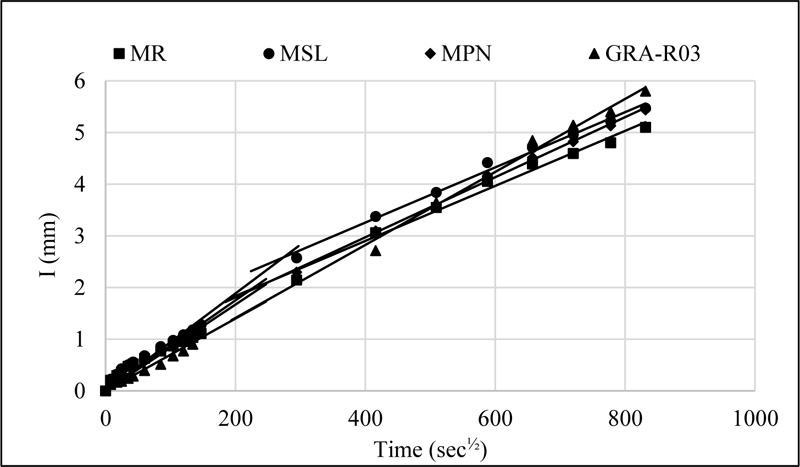
4.3. Capillary Absorption
As shown in Figs. (7 and 8), the capillary water absorption rate of the repair mortar samples increased rapidly at the start of the test and decreased as the water moved through the materials. The absorption at the start of the test corresponded to the faster filling of the large pores of the sample near the contact surface with the water and then diffused to capillaries of smaller diameters. The progression of water by capillary action in the mixtures is a function of the distribution of the capillary pores. The results showed that replacing cement with slag or natural pozzolan slightly increased the water capillary absorption rate compared to the reference mortar at early ages. This is due to the effect of the slag, which hydrates slowly and consequently influences the distribution of the pore size of the porous structure. As can be seen from Fig. (7), readymade non-fiber repair mortar (GRA-R03) exhibited a higher absorption coefficient compared to MR for large and small pores. In the case of fiber-repair mortars, lower absorption coefficient values were obtained with laboratory mortar containing slag and natural fibers (MSLPD) for large and small pores with a reduction of 36 and 43%, respectively compared to MR. A reduction of around 25 and 30% compared to MR for the mixtures of MPNPD for large and small pores, respectively, was reported. Water absorption of date palm fibers depends on the fibers' size and their chemical composition (cellulose), as the high cellulose content in the natural fibers leads to increased water concentration [31]. However, using readymade fiber mortars GRA-F30 and MA-EM S 448 led to a significant reduction in absorption coefficients of 51 and 36% for large pores and 55 and 32% for small pores compared to MR, respectively. The lowest coefficient values were given by repair mortar with synthetic fibers MA-EM-S488. This reduction may be attributed to the refinement of the formation of capillary pore with a denser interfacial area in the mixture, as reported previously [30]. Introducing natural, propylene, synthetic or natural fibers in mortars lower the water absorption coefficients compared to non-fiber mortars. This can be explained by the fact that water absorption depends on the specific surface area, the size and tortuosity with which a porous structure is connected and the relative average length of a fluid particle. The water absorption by capillarity of acrylic fibers reinforced mortars was higher than the plain mortar at 7 days, but a slight reduction was observed at 28 days. This behavior corresponds to the formation of pores containing the air that acts as a barrier, preventing the rise of water through the matrix and partially reducing the capillary pressure inside the pores [13]. Moreover, it can be concluded that adding polypropylene fibers to the geopolymer mixture decreased the water absorption in most samples, probably because the fiber particles filled some of the pores in the mixture and consequently reduced moisture absorption capacity [16].
Results of the sorptivity coefficients of the various repair mortars produced (Fig. 9) show the sorptivity coefficients. The incorporation of slag or natural pozzolan in the mixtures results in an increase of 6% of the initial sorptivity coefficients. This is due to the slow pozzolanic reaction, resulting in latent hydration and slower pore filling. On the other hand, the GRA-R03 mortar showed a 4% reduction in the absorption coefficient. A remarkable decrease in absorption coefficients at 28 days was observed for fiber mortars, ranging from 16 to 48% compared to reference mortar. Sorptivity depends on the progress of hydration and the interconnection of the capillary pores. However, Krobba et al. [20] showed that natural alfa fiber-reinforced mortar has a coefficient of sorptivity 12% higher than that of reference mortar. This can be attributed to the increase in the volume of pores by the inclusion of fibers. Small cracks were observed between the cement paste and coral sand particles for concrete reference, whereas when 15% of either fly ash (FA) or blast furnace slag (BFS) or 5% of metakaolin (MK) were used, the pozzolanic reaction of cementitious materials resulted in an improvement of the interface in ITZ at 28 days and a denser and homogenous microstructure and no cracks were observed at the ITZ between cement paste and aggregate [46].
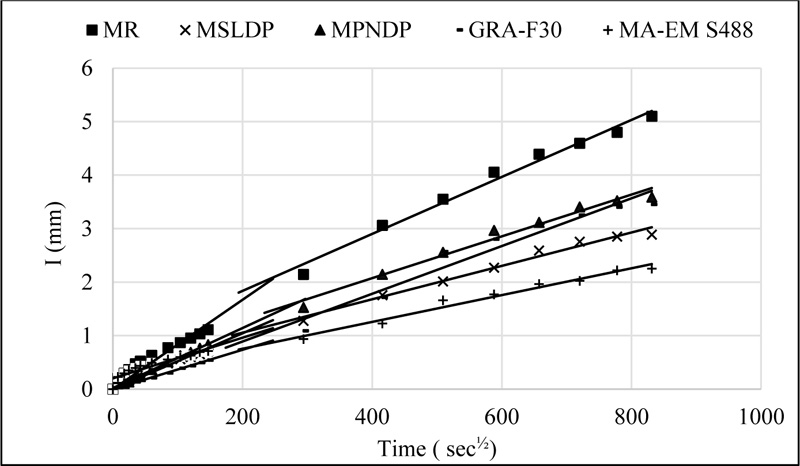
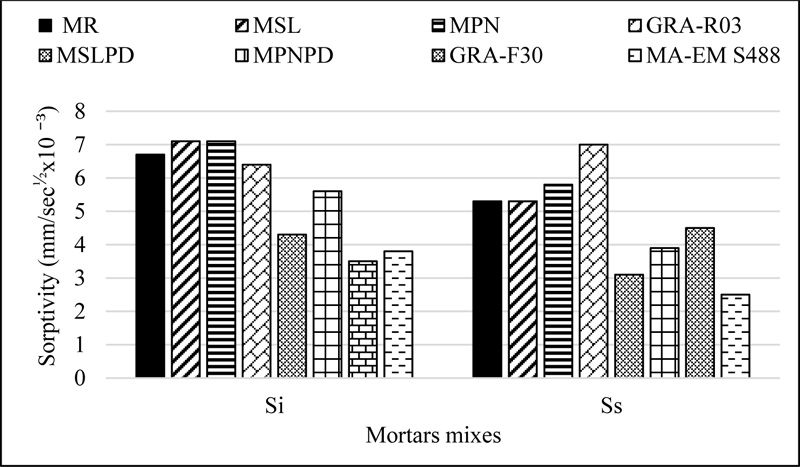
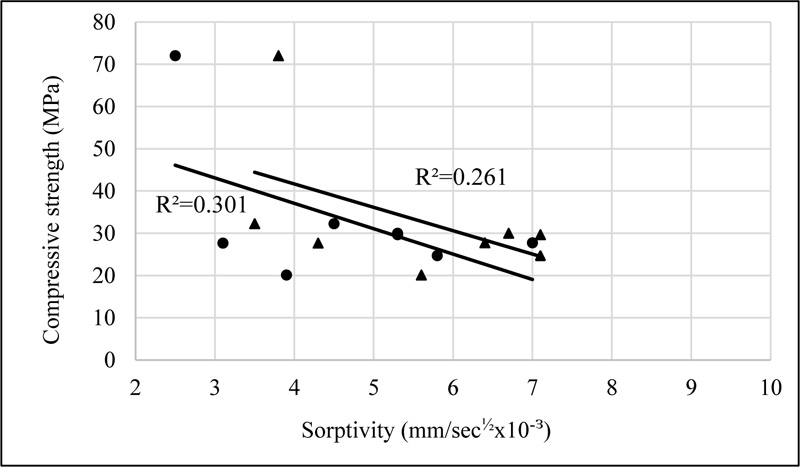
Relationships between the compressive strength and the sorptivity of small and large pores are shown in Fig. (10). There is a trend for the compressive strength to decrease with an increase in sorptivity. Nevertheless, the correlations obtained are poor, with regression coefficients (R2) of 0.261 and 0.301 for small and large pores, respectively.
4.4. Total Shrinkage
Fig. (11) shows the development of the total shrinkage for repair mortars. Substitution of 15% cement by slag and natural pozzolan resulted in a reduction in total shrinkage of 21% and 2% compared to MR, respectively. This can be attributed to the densification of the microstructure. In addition, slag and natural pozzolan are known to reduce the pore size and connectivity of voids, which slows down the water evaporation and restrains the shrinkage. Slag and natural pozzolan reactions are slower than cement, which ensures a surplus of water available for clinker reaction lowering the autogenous shrinkage. It has been reported that the use of slag in mixtures led to a reduction in shrinkage [39] and that the incorporation of 15% slag resulted in a 37.5% reduction in drying shrinkage values compared to reference mortar [46]. Furthermore, the hydration kinetics of slag mortars has a significant influence on autogenous shrinkage [47]. However, different tendencies were reported by other researchers. Hu et al. [48] reported that the autogenous shrinkage of cement mortars gradually increased with the decrease in the w/b ratio, which is more significant for samples containing fly ash and slag. Dellinghausen et al. [49] also reported that the partial replacement of cement with blast-furnace slag for concrete with an equal w/b ratio and curing period exhibited higher total shrinkage values compared to the same mixtures made with grey Portland cement. The incorporation of date palm fibers in the mixtures of MPNPD and MSLDP led to a slight increase of 3% and 7% in the total shrinkage compared to the reference mortar, respectively. This means that the inclusion of fiber bridges the shrinkage cracks of mortars. It was also found that the MA-EM S448 mortar exhibited a lower shrinkage than that of the mortars based on date palm fibers; this is probably due to the difference in the type of fibers. The use of fiber mortars stabilizes the shrinkage due to the shape and provides good adhesion of the fibers to the cement matrix, limiting the shrinkage. The reduction in shrinkage could be attributed to refined pore structure from secondary pozzolanic reaction and filler effect of mineral addition. It has been reported that the shrinkage of geopolymers containing 0.05% PP decreased by 38.6% [17]. Pereira-de-Oliveira et al. [13] showed that the incorporation of acrylic fibers in mortar allows a reduction and redistribution of cracks or even avoid them if a more large fibers volume is incorporated at the mortar mixtures. No cracking was observed for acrylic fibers dosage of greater than or equal to 1.17 kg/m3 (equivalent to 0.1% fiber volume). Fig. (12) illustrates the relationship between the compressive strength development and total shrinkage evolution at 28 days of the different repair mortars. This figure reveals that compressive strength and total shrinkage are roughly linearly related. A decrease in shrinkage was observed with increasing compressive strength with a determination coefficient, R2=0.588, which was in agreement with other research studies [50].
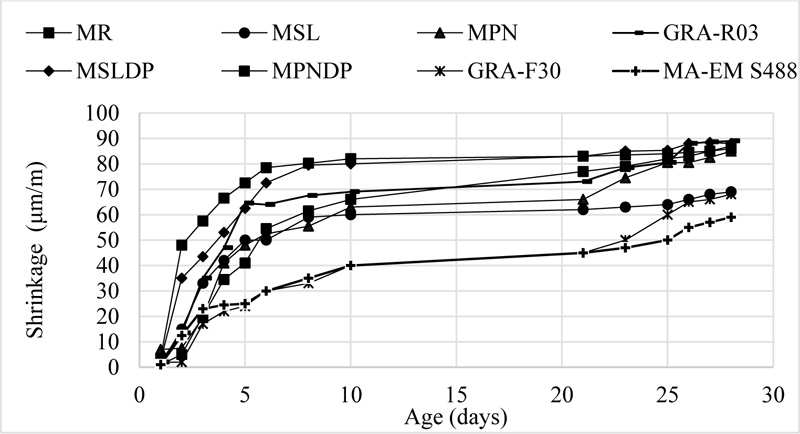
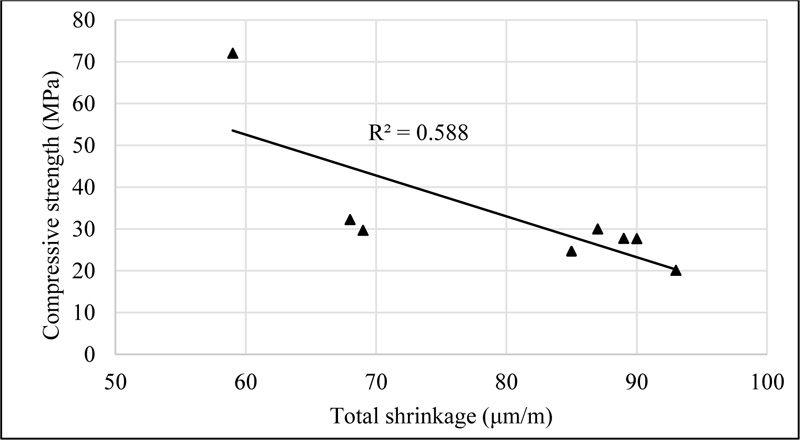
4.5. Pull-off
The results of the various bond strength tests performed on the experimental slabs are presented in Fig. (13), and the corresponding failure modes obtained by the direct traction adhesion test at the age of 28 days are presented in Fig. (14 and Table 6). The pull-off test is used to assess and compare repair mortars. The pull-off test is a convenient method for evaluating both the mechanical integrity of the concrete surface prior to repair and the repair bond strength [2]. The results obtained for non-fiber mortars showed that the reference mortar has the lowest average bond strength, as shown in Table 6 and illustrated in Fig. (13). A slight increase in the order of 15% and 11% in pull-off strength was observed for GRA-R03 mortars and mortars based on natural pozzolan without fibers compared to the control mortar. However, incorporating slag in the mixtures results in an increase in pull-off strength of 33% compared to MR. Ghafari and Naderi [51] reported that using mineral admixtures increased the bond strength of repair mortars. Mortars containing 20% NP have been reported to have a positive effect on the development of flexural bond strength [52]. The addition of natural date palm fiber in mortars based on slag or natural pozzolan did not provide any significant improvement in increasing bond strength (Table 7). The date palm fiber could significantly increase the adhesive strength from 21% to 65% when the length of the fibers increased from 0.5 mm to 20 mm [26]. On the other hand, using readymade repair mortars increased the bond strength by 18% and 33% for GRAF-F30 and MA-EM S448, respectively, compared to MR. The highest bond strength value was given by the repair mortar based on acrylic fibers. A comparison of the measured pull-off strength of the specimens with the quantitative bond strength quality proposed by Ozyildirim and Sprinkel [53] is shown in Table 8. It is very obvious that the strength level achieved by all the specimens falls under a “Good” bonding category since the measured bond strength ranges between 1.4 and 1.7 MPa, whereas the MSL, MSLDP, GRA-F30, and MA-EM S448 composite samples reach a strength value between 1.4 – 1.7 MPa that could be classified as “very good”. It can be seen from Fig. (13) that the failure mode of all fiber and non-fiber repair mortars occurred in the concrete substrate, except for the reference mortar and GRA-R03 mortar, where the failure mode occurred in the contact interface between the concrete and the repair mortar. This could be explained by the poor adhesion between the repair mortar used and the substrate due to inadequate preparation at the laboratory. It can be concluded that substrate surface preparation is necessary to ensure efficient bonding between concrete substrate surfaces and overlay materials [54]. In samples with no surface preparation, failure mode occurs at the interface [55].
Mortars mixes | MR | MSL | MPN | GRA-R03 | ||||
---|---|---|---|---|---|---|---|---|
Bond strength (MPa) | Failure mode | Bond strength (MPa) | Failure mode | Bond strength (MPa) | Failure mode | Bond strength (MPa) | Failure mode | |
1 | 1.66 | B | 1.5 | A | 1.45 | A | 1.68 | B |
2 | 0.62 | B | 1.53 | A | 1.31 | A | 1.68 | B |
3 | 1 | B | 1.88 | A | 1.48 | A | 1.20 | B |
4 | 1.09 | B | 1.46 | A | 1.33 | A | 1.52 | A |
5 | 1.64 | B | 1.58 | A | 1.06 | A | 1.21 | B |
Average | 1.20 | 1.59 | 1.33 | 1.38 |
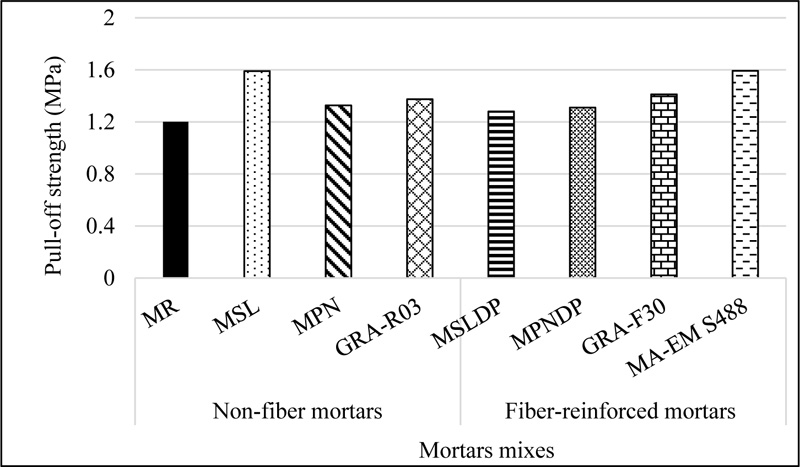
Mortars mixes | MSLDP | MPNDP | GRA-F30 | MA-EM S448 | ||||
---|---|---|---|---|---|---|---|---|
Bond strength (MPa) | Failure mode | Bond strength (MPa) | Failure mode | Bond strength (MPa) | Failure mode | Bond strength (MPa) | Failure mode | |
1 | 0.62 | A | 1.02 | B | 1.355 | B | 1.67 | B |
2 | 1.41 | A | 1.16 | B | 1.40 | A | 1.91 | A |
3 | 1.445 | A | 1.21 | A | 1.45 | A | 1.48 | A |
4 | 1.79 | C | 1.5 | A | 1.45 | A | 1.31 | A |
5 | 1.96 | A | 1.69 | A | 1.41 | A | 1.59 | A |
Average | 1.44 | 1.32 | 1.41 | 1.60 |
Bond quality | Excellent | Very Good | Good | Fair | Poor |
---|---|---|---|---|---|
Bond strength, T (MPa) | >= 2.1 | 1.7–2.1 | 1.4–1.7 | 0.7–1.4 | 0–0.7 |
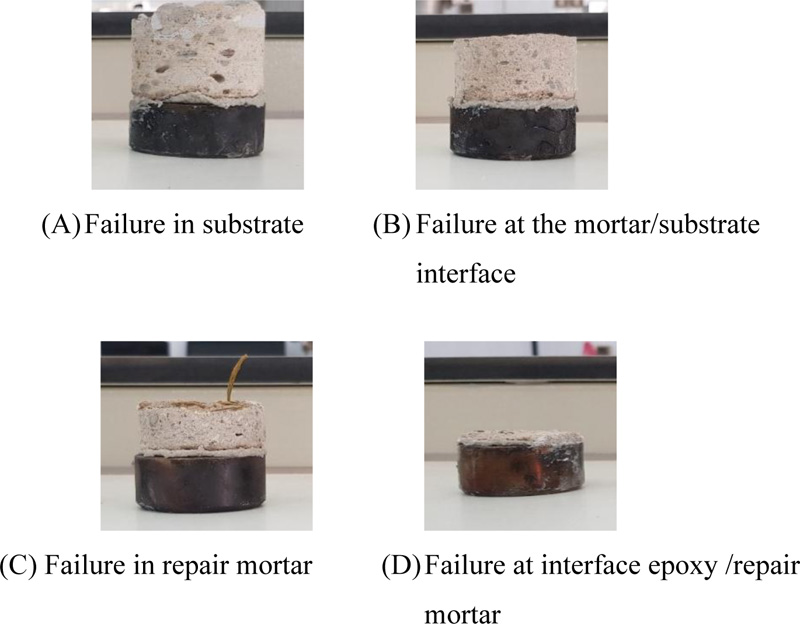
In order to predict the bond strength from the experimental values of compressive strength, a linear relationship exists between the bond strength and the compressive strength (Fig. 15). The correlation shows a poor correlation with a regression coefficient R2=0.389.
4.6. Slant Shear
The bond strength measured by the slant shear test method depends on the compressive strength of the repair materials and substrate mortar. The failure occurs on a slant surface when the compressive strength of the repair materials is less than the compressive strength of substrate mortar [56]. A higher strength of the existing concrete leads to a higher shear bond strength. A substrate surface treatment also has a beneficial impact on the shear bond strength [57]. The results of the slant shear of non-fiber and fiber repair mortars are illustrated in Fig. (16). Mortars with slag (MSL) and fiber mortars (MA-EM-S488) exhibit the highest stress of 9.82 MPa value with a slight increase of 8% compared to the MR. However, a slight decrease of 10% compared to MR is observed for mortars based on natural pozzolan. It is also noted that the lower bond strength by slant shear is given by non-fiber readymade repair mortars (GRA-R03), which represents only 72% of bond stress compared to MR. This could be explained by the poor adhesion of the interface between the repair mortar and the substrate surface. In comparison to control mortar, mortars made of polypropylene fiber and the MPNPD mortars had a reduction in bond strength of 11% and 7%, respectively. Indeed MSLDP mortars led to comparable bond than those of MR. MA-EM S448 mortar produces a similar bond strength compared to MR. These results show that the slant shear adhesion depends on several parameters, such as composition of mortar mixture, nature of fiber and its slenderness. It was observed that the slant shear test performed on the composite cylindrical specimens generated two failure modes for these composites studied (Fig. 17). All samples exhibited fracture at the concrete substrates away from the concrete-mortar contact surface with some slight cracks on the repair mortar and sometimes a splitting of the concrete at the level of the supports, with an exception for the mortar based on natural pozzolan and date palm fiber MPNDP, where a monolithic failure was observed with propagation of the crack through the repair mortar and the concrete substrate. Kenai et al. [58] showed that the mortar reinforced by 0.75% of date palm (MPNDP) enhanced the oblique shear strength, and mortar containing 15% slag (MSL) presented the highest bond slant shear strength. The introduction of vegetable fibers leads to a significant increase in a bond due to their structure [59]. The experimental values of compressive strength versus slant shear are shown in Fig. (16). A tendency was observed for the bond strength by slant shear to increase as strength increases. However, a poor correlation with a regression coefficient R2 of 0.068 value is reported.
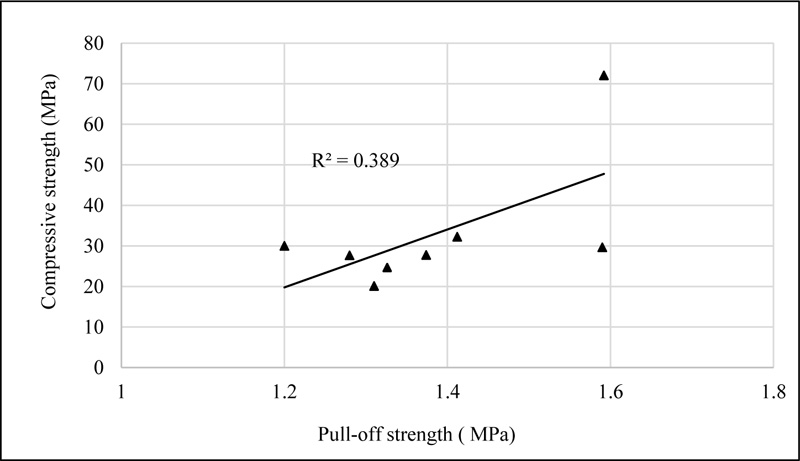
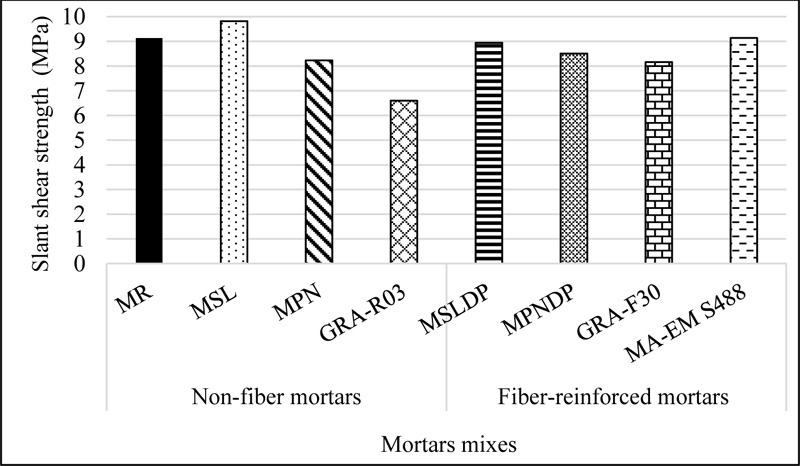
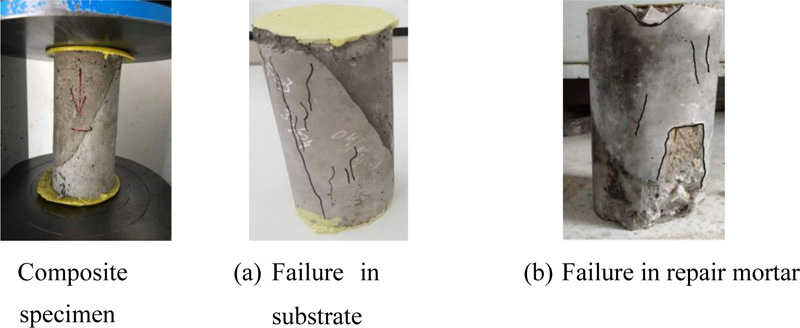
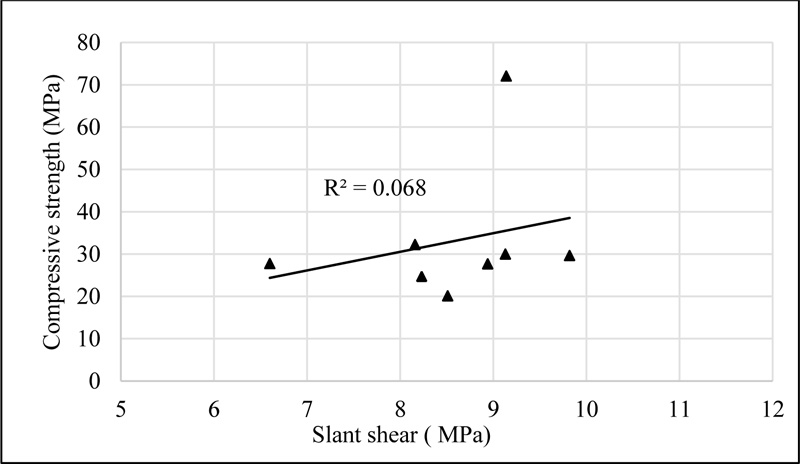
CONCLUSION
Based on the experimental study of repair mortar with 0.75% of palm fibers, 15% by weight of slag or natural pozzolan as cement replacement and a water/binder ratio of 0.5, the following conclusions could be given:
- Natural and agro-waste fibers are technically advantageous materials, sustainable, renewable and economical and could be used in the construction sector for various applications.
- A low-cost, sustainable and greener repair mortar using locally available natural fibers and mineral admixtures was developed with comparable performance to costly and non-environment friendly mortars with synthetic fibers.
- Natural fibers are most effective in improving the mechanical properties and durability of mortars, which could be applied to enhance the performance of repairs and reduce their cost.
- Physical characteristics of natural fibers (porosity, water absorption, fiber bundling, a distribution of mechanical properties, etc.) present additional challenges in the design and processing of natural fiber composites compared to composites using synthetic fibers.
- Absorption values were quite similar for slag mortar and acrylic fibers mortar, which presented the lowest absorption coefficient of 2.88 mm and 2.25 mm, respectively.
- Correlations between compressive strength and water capillary absorption, total shrinkage and pull-off were low.
- The addition of natural fibers in cement mortars decreases the total shrinkage and hence reduces the risk of cracking. The lowest value is given by the readymade acrylic fibers mortars.
- This study confirmed the benefit of using mineral addition and natural fibers materials as repair to improve the bond strength. Mixes with slag and date palm fibers had an average shear bond strength of 1.59 MPa and 1.44 MPa and slant shear strength of 9.82 MPa and 8.94 MPa, respectively.
- The mortar fabricated with local materials and date palm fibers gave a comparable performance to those readymade mortars with synthetic fibers and hence could be a more environment-friendly material and an alternative to the imported repair mortar in developing countries.
- This research could be extended by further examining other durability aspects, such as water, gas and chloride permeability and microstructural analysis using date palm fibers and other agro-waste fibers.
LIST OF ABBREVIATIONS
SL | = slag |
PN | = Pozzolan |
GPC | = Geopolymer Concrete |
OPC | = Ordinary Portland Cement |
ITZ | = Interfacial Transition Zones |
CONSENT FOR PUBLICATION
Not applicable.
AVAILABILITY OF DATA AND MATERIALS
The authors confirm that the data will be available upon request from the corresponding author [K.S].
FUNDING
This study is financially supported by the funding agency “Directorate-General for Scientific Research and Technological Development, Ministry of Higher Education and Scientific Research, Algiers, Algeria.
CONFLICT OF INTEREST
Said kenai is the editorial advisory board member of the journal Open Civil Engineering Journal.
ACKNOWLEDGMENTS
The authors would like to acknowledge the contribution of MSc students (Rezagui, M. Rekabi, M. and Chambit, I) in conducting the experimental work. They would also like to thank the funding agency “Directorate-General for Scientific Research and Technological Development, Ministry of Higher Education and Scientific Research, Algiers, Algeria” for financial support.