All published articles of this journal are available on ScienceDirect.
Strength of Lightweight Structural Concrete Acting under Imposed Load
Abstract
Background:
Expanded polystyrene granules (EPG) can be used as an aggregate for producing lightweight concrete (LWC). EPG was used to make LWC with a density of 1326kg/m3 and 1337kg/m3, while the EPG concrete without fiber had a density of 1320kg/m3. Due to the low strength and brittleness of EPG LWC, the need to improve the properties of this concrete type is necessary.
Objective:
The aim of this paper was to research and investigate possible ways of enhancing the mechanical properties of EPG LWC. Hence, the investigation of this research work focuses on the use of chopped basalt fiber (BF) and steel fiber (SF) separately as dispersed reinforcement in EPG concrete to improve the compressive strength of EPG LWC.
Methods:
A general review from previous researchers on similar research was conducted, and then the experimental method was used to investigate the effect of BF and SF on the compressive strength of EPG LWC. Nine EPG concrete series were produced and tested. Compression testing was used to measure the compressive strength of the concrete sample. The density was determined by mass volume.
Results:
The results show the effect of BF and SF in the EPG concrete. The EPG reinforced with BF obtained its maximum compressive strength when 1.5% BF was incorporated in the EPG concrete and while EPG concrete reinforced with SF obtained its maximum compressive strength when 1% SF was included in the EPG concrete.
Conclusion:
Based on the results, the amount of fiber added to the EPG concrete affects not just the compressive strength but also the concrete density.
1. INTRODUCTION
Lightweight concrete (LWC) has a density of less than 1900 kg/m3; it is composed of ordinary river sand (or lightweight sand), water, Ordinary Portland cement (OPC), and lightweight coarse aggregates [1]. During the last two decades, there has been an increase in the research and application of LWC and lightweight aggregate (LWA) for high-rise buildings, floating structures and large-span concrete structures [2-6]. In the construction industry, both LWC and LWA are used to achieve significant mass and weight reduction, especially for structures built in seismic zones. LWC has various advantages, including reducing foundation dead loads, high strength-to-weight ratio, fill material for sandwich construction and a wide range of other construction related applications.
LWA | Solid Density (kg/m3) | Bulk Density (kg/m3) | Water Absorption (%) |
Part. Porosity (%) |
---|---|---|---|---|
Expanded polystyrene granules (EPG) | 900-1050 | 5-15 | 50 | 95 |
Expanded Glass | 2200-2600 | 175 - 875 | 4 - 22 | 35 -85 |
Expanded Clay | 2400 - 2600 | 300 - 900 | 2 - 20 | 40 - 75 |
Saw Dust | 300 - 700 | 120 - 200 | 10 - 35 | 35 - 55 |
Pumice | 1500 - 2000 | 450 - 880 | 20 - 30 | 40 - 90 |
Perlite | 2200 - 2400 | 30 - 150 | 10 - 30 | 80 -95 |
Despite the many benefits of LWC, its application has been limited as load-bearing structural components [3]. The brittleness of LWC is significantly higher than conventional concrete at the standard mix ratio. Also, when compared to conventional concrete, LWC has a low deformation capability [7].
The brittleness of LWC is a major concern to structural engineers, this shortcoming has stirred further research on increasing the strength of LWC while maintaining its light weight [8]. LWAC can be defined as low-density concrete consisting of LWA, such as expanded clay (EC) [9-11]. LWA offers reduced dead load; hence it can drastically lessen earthquake damage to structures. Cement is a major constituent in lightweight aggregate concretes (LWAC) ; consequently it contributes to its mechanical and durability properties. (Table 1) shows some selected properties of LWA.
Rapid advancement in developing suitable structural materials which are low-weight, high-strength, and multifunctional nanocomposites has been studied by previous literature [12].
The effects of polystyrene granules in concrete vary depending on the kind of concrete (polymer-based or cement-based), the quantity, and the type of polystyrene used, etc. Generally, increasing the dosage of polystyrene will result in a decrease in its mechanical properties. Prior experimental research has shown that thermally treated polystyrene enhances concrete behavior, especially its workability, shrinkage, thermal conductivity, and density [13].
Fiber reinforced concrete (FRC) is known to have higher energy-absorbing ability than normal concrete (NC); they have great “ductility or inelastic deformation capacity,” but their weight is often a concern. FRC shares some key similarities with autoclaved aerated lightweight concrete (AALWC), like the adaptability of LWAC, the reliability of FRC, and the versatility of precast concrete panels. Fiber-reinforced lightweight concrete (FRLWC) has potential application for precast concrete panels; they can be used either in low or high rise structures [15-17].
The research works of various authors identified several demerits and structural problems associated with LWC. Previous studies have looked at the usage of fiber-reinforced polymer (FRP) as reinforcement material in concrete [18-22]. These studies have established the efficacy of several FRP systems in achieving the required results. Yet, very few research exists on strengthening EPG with dispersed hybrid fibers like chopped basalt fiber (BF) and short steel fiber (SF). This research seeks to address some of the identified challenges by enhancing the mechanical properties of this type of concrete. Hence, the investigation focuses on the use of BF and SF independently as dispersed reinforcement in EPG concrete to improve its compressive strength (fc). SF reinforced concrete and BF reinforced concrete will be investigated. The strain and stress rates were obtained from previous studies, while the effective properties of LWC were obtained using fc test [23].
2. MATERIALS AND METHODS
For this research paper, various tests were undertaken to ascertain the compressive strength of lightweight expanded polystyrene by comparing chopped steel fiber (SF) and basalt fiber (BF) as dispersed reinforcement in lightweight expanded polystyrene concrete. For every concrete mix set, the following materials were used to produce lightweight expanded polystyrene concrete.
The following experimental materials were used:
- Portland cement of 4.78 kg was used as a binding agent. Portland cement CEM I 42.5 N was obtained from “Maltsovsky” Plant in Fokino District, Bryansk Region of Russia. The chemical compositions of Portland cement are presented in Table 2.
Table 2.Chemical compositions of Portland cement in percentage (%).SiO2 Al2O3 Fe2O3 K2O CaO MgO SO3 P2O5 TiO MnO Na2O 21.90 4.86 3.3 0.56 65.77 1.15 2.1 - - - 0.36
- Quartz sand of 3.15 kg was used as fine aggregate with 0.6-0.8mm fraction having a round shape, with a low content of clay inclusions and inclusions of soft rocks. The resulting quartz sand underwent additional enrichment and drying. It has a moisture content of up to 0.2% [24]. This quartz sand was obtained from “Tyutchevo” Plant in Naro-Fominsky District in Moscow Region, Russia. The physical properties of quartz sand are presented in (Table 3). This type of sand is used in the construction industry as fillers; they have high anti-erosion ability, and are used to make acid-resistant concrete and mortar [25].
Table 3.Physical properties of quartz sand.Physical Property Value Size of Grain, [mm] 0.5-1.0 Bulk density (compacted), [kg/m3] 1430 Hardness (on the Mohs scale) 7 Crushability 0.3 Humidity, [%] 1.7
- EPG of 0.075kg was used as primary coarse aggregate with a 5-8mm fraction
- Water 1.85 litters
For dispersed reinforcement, the following quantities were used independently:
- 42 grams of chopped SF with a diameter of 1 mm, 25mm length (Fig. 1).
- 42 grams of chopped BF with a diameter of 15 micro meters, 25mm length (Fig. 2).
A total of nine (9) EPG concrete cube specimens were produced for each given composition. One (1) was a control specimen without dispersed FRP, while four (4) were reinforced with dispersed BF, and four (4) batches were reinforced with dispersed SF.
Each series consists of three (3) EPG concrete cube specimens, where 0% FRP is the control specimen without dispersed fiber reinforcement. Then the batches consisting of FRP were reinforced individually with 0.5%, 1%, 1.5 and 2% fibers accordingly. The
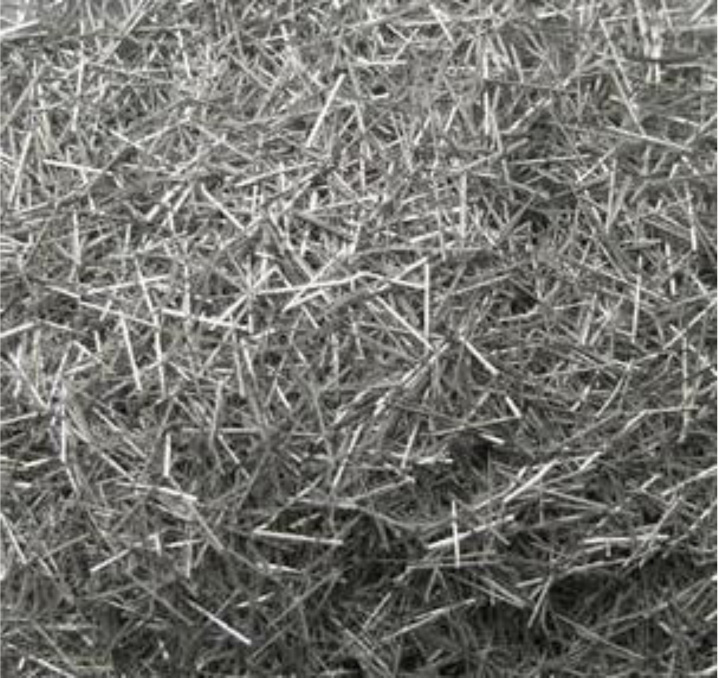
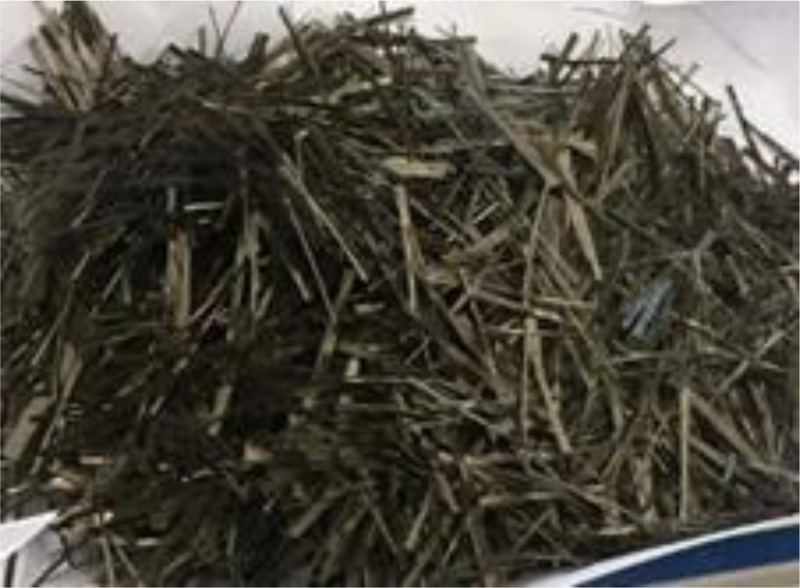
According to the previous study [27], the influence of fibers on concrete characteristics is dependent on the dose of fibers in the concrete mix and its length. Similarly, researchers have demonstrated that for achieving optimal mechanical properties, the ideal dosage of basalt fibers should be between 0.3 and 0.8 percent of the total volume of the concrete mix [28]. However, for this research, BF and SF content varied between 0% to 2%; this was informed by the presence of more variables in this research, hence capturing understudied BF and SF content varations.
Concrete's fc is determined by a variety of parameters, including the water-cement ratio, cement strength, concrete material quality, quality control throughout production, etc. The fc of concrete refers to its ability to carry stresses on its surface without cracking or deformation. When an object is compressed, it shrinks in size, and when it is tensioned, it grows in length [29].
3. RESULTS AND DISCUSSION
From Table 4, it can be observed that an increase in EPG leads to a reduction in water absorption of concrete; at 28 days of curing, the density of 0% was 1320 kg/m3 but increased to 1326 kg/m3 and 1337 kg/m3 for 2% BF & SF, respectively. EPG with BF & SF also formed part of the aggregate and acted as a filler, thus having a fewer voids as compared to concrete without EPG [30]. The expanded polystyrene granules can be used for non-structural elements in low weight concrete work, consequently reducing environmental pollution by reusing waste materials; they can be used to considerably reduce cracks, and improve the acoustical and thermal properties of a structure [31, 32].
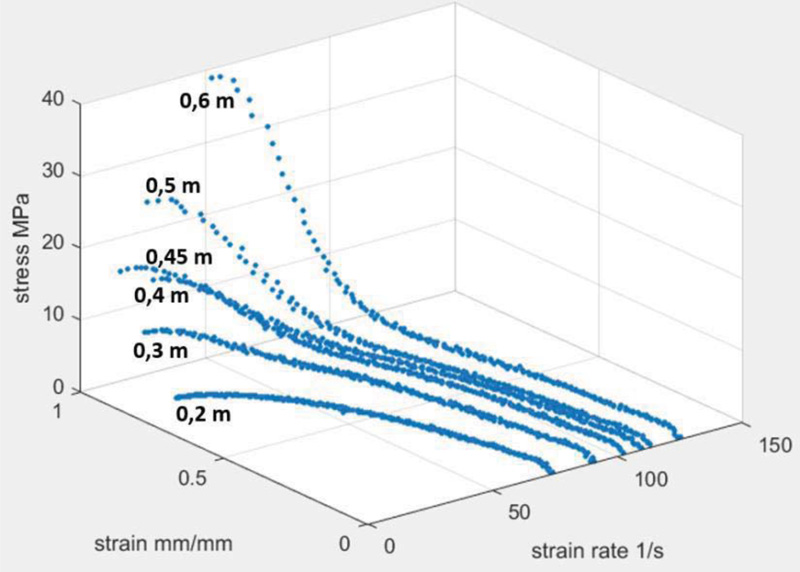
From the experiment work of [33], EPG deformation behavior was shown to be greatly influenced by the elastic modulus, plateau stress, and density. Fig. (3) summarizes the results of their findings. During compression, the strain rate does not remain constant, however, it has only a little impact on the foam properties. The impact tests to stress–strain results can be obtained from the sample dimensions by converting conventional force–displacement data.
The results in Table 4 and Fig. (4) show that EPG concrete reinforced with dispersed BF grew in the
CONCLUSION
From the experimental investigations, it can be concluded that as the amount of dispersed hybrid fibers was raised, the compressive strength of the EPG concrete improved to a point. According to the results, there are limits on the amount of BF and SF that should be incorporated in the EPG concrete mixture to obtain desirable results. The compressive strength test indicates that increments in the compressive strength of concrete were a result of higher steel fiber and basalt fiber contents. Hence this research affirms that steel fiber and basalt fiber percentages of 0.5%, 1.0% and 1.5% yield the best results. As expected, the concrete cubes reached full strengths after 28 days in the curing tank. From the results obtained, we can also see that 1% to 1.5% of BF and SF content gave higher compressive strength values compared to the other percentages of BF and SF under consideration within this study.
LIST OF ABBREVIATIONS
EPG | = Expanded Polystyrene Granules |
LWC | = Lightweight Concrete |
BF | = Basalt Fiber |
SF | = Steel Fiber |
OPC | = Ordinary Portland Cement |
LWA | = Lightweight Aggregate |
CONSENT FOR PUBLICATION
Not applicable.
AVAILABILITY OF DATA AND MATERIALS
The data and supportive information is available within the article.
FUNDING
None.
CONFLICT OF INTEREST
The authors declare no conflict of interest, financial or otherwise.
ACKNOWLEDGEMENTS
Declared none.