All published articles of this journal are available on ScienceDirect.
Performance of Hybrid Asphalt Mixture through the Stability and Tensile Strength
Abstract
Introduction:
The stability and tensile strength of asphalt mixtures play a crucial role in pavement durability, primarily due to the challenges associated with cracking. This study investigates the utilization of a hybrid asphalt mixture comprising hybrid materials: Palm Oil Fuel Ash (POFA), garnet waste and sawdust to enhance the modified asphalt performance.
Aims:
The objective is to examine the hybrid materials’ influence towards the mechanical properties of the hybrid asphalt mixture, specifically focusing on the Indirect Tensile Strength (ITS) as well as the Marshall stability test.
Methods:
To achieve this, hybrid materials were finely ground and sieved to 25µm before being incorporated into the mixture. The Marshall mix design procedure was conducted, utilizing hybrid binders at concentrations of 0% (control), 3% 6%, and 9%. The effects of the hybrid asphalt mixture on stability, flow, stiffness, and ITS were assessed at the optimal binder content.
Results:
The findings indicate that the hybrid asphalt mixture reveals enhanced Marshall stability, stiffness, flow, and ITS values compared to conventional asphalt mixtures. Notably, hybrid asphalt mixtures with 6% binder concentration demonstrate the most significant enhancement in terms of Marshall stability and ITS.
Conclusion:
This correlation suggests that the incorporation of POFA, garnet waste, and sawdust as hybrid materials in the hybrid asphalt mixture possesses a positive effect on the overall mechanical properties of the pavement.
Highlights:
• POFA, garnet waste, and sawdust increased the stability of the hybrid asphalt mixture.
• POFA, garnet waste, and sawdust increased the tensile strength of the hybrid asphalt mixture.
• Hybrid asphalt mixture performs positively towards flow and stiffness.
1. INTRODUCTION
Performance evaluation of asphalt mixtures is crucial for ensuring the longevity and durability of road pavements. Recently, there has been growing interest in developing hybrid asphalt mixtures that incorporate various waste materials as alternative additives [1-3]. These hybrid materials offer potential benefits such as enhanced stability and improved tensile strength, among the primary factors determining the overall performance of asphalt pavements. However, the constant increase in traffic loads and environmental factors has led to a need for improved pavement materials. Hybrid asphalt, which combines different types of binders and modifiers, has arisen as a promising solution for improving asphalt pavement performance. Particularly, the Indirect Tensile Strength (ITS) of hybrid asphalt plays a crucial role in determining its resistance to cracking and fatigue [4]. This comprehensive study aimed to investigate and evaluate the stability as well as ITS properties of a hybrid asphalt mixture.
Previous studies have thoroughly investigated the mechanical properties of traditional asphalt mixtures. Nano-Charcoal shell Ash (NCA) was utilized by Jeffry et al. [5], and the optimum result of a 6% NCA content improved the tensile strength at the highest state. However, few studies have focused on the ITS of hybrid asphalt pavements. To address this research gap, the present study uses a comprehensive experimental methodology to evaluate and compare the ITS of hybrid asphalt mixtures with those of their traditional asphalt counterparts. The investigation involved sample preparation, laboratory testing using the appropriate equipment and procedures, and data analysis. By conducting systematic testing of ITS, this research intends to supply valuable insights into the potential challenges as well as benefits correlated with using hybrid asphalt pavements in real-world applications.
Previous studies examined using various waste materials to enhance the asphalt mixtures’ performance. For example, Maleka et al. [6] examined the ITS of asphaltic concrete 14 (AC 14) using Palm Oil Fuel Ash (POFA) as a filler, achieving varying degrees of success. Additionally, Rusbintardjo et al. [7] discovered that a binder compounded with POFA became more susceptible to temperature, indicating the need to consider the optimal dosage carefully. On the other hand, Raja Zulkefli et al. [8] determined that a 7% content of POFA in modified bitumen produced the best results, with the modified bitumen exhibiting increased hardness compared to conventional bitumen.
Recently, there has been an increasing interest in hybrid asphalt pavements as an innovative solution to enhance the performance of asphalt roads. Hybrid asphalt combines different binder types, such as polymer-modified binders, warm-mix asphalt additives, or recycled materials, to enhance the particular pavement properties. These hybridization techniques aim to address challenges, for instance, fatigue cracking, rutting, as well as aging, which are common problems faced by traditional asphalt pavements. By incorporating these modified binders or additives, hybrid asphalt pavements offer the potential for improved strength, enhanced durability, and reduced environmental impacts. Subsequently, Rahman et al. [9] studied the impact concerning three waste materials–tire rubber powder, waste cooking oil, as well as POFA–as partial replacements for bitumen in asphalt mixtures. Their results indicated that a 15% replacement ratio resulted in enhanced or equal performance concerning flow, stability, as well as rutting resistance. Furthermore, incorporating steel slag, fly ash, and polypropylene has been shown to enhance the stability and flow and improve the properties of asphalt concrete while reducing material costs [10].
Garnet waste, another potential additive, has been promised to replace river sand in the asphalt mixture. Muttashar et al. [11] highlighted the cost-effectiveness, environmental friendliness, as well as conservation of natural resources associated with using spent garnet as a sand replacement as high as 25%. Additionally, Huseien et al. [12] demonstrated that garnet waste could effectively replace as high as 25% of the aggregate in AC 14 asphalt mixtures without compromising performance. The performance of the garnet waste aggregate met the specifications of Aletba et al. [13], further supporting its potential as a replacement material. Similarly, Osuya and Mohammed [14] found that the incorporation of sawdust ash in asphaltic concrete enhanced its properties, with an optimum content of 15% sawdust ash leading to a significant increase in stability. Apart from that, the rheological properties of bitumen may be enhanced by incorporating a rice husk ash modifier, as demonstrated by Arabani and Tahami [15].
In a study by Korayem et al. [16], the ITS was enhanced by the filler addition of carbon powder to asphalt mixtures. When carbon powder was used as the filler, ITS values marginally increased for both the wet and dry specimens. Mixtures containing amorphous carbon powder demonstrated higher total Indirect Tensile Ratio (ITR) values, indicating improved moisture resistance in comparison to the control mixture. The rough surface of the carbon filler improved the bonding connection between the aggregates as well as bitumen.
ITS is a fundamental mechanical property used to evaluate the tensile behavior of materials, which includes asphalt pavements. Here, it is described as the maximum tensile stress that a material may endure before failure occurs when subjected to an indirect tensile load. Unlike direct tension tests, which are challenging to perform on asphalt pavements, the indirect tensile test provides a practical and reliable method for evaluating tensile strength. It involves applying a compressive load perpendicular to the plane of the specimen, inducing tensile stresses within the material. Furthermore, the resulting failure mode typically occurs by splitting or cracking across the sample, representing the tensile failure of the material.
This study investigates the hybrid asphalt mixture performance that utilizes three waste materials: POFA, garnet waste, and sawdust. This study is to examine the stability as well as tensile strength with regard to the hybrid asphalt mixture containing hybrid material. Ultimately, the successful implementation of hybrid asphalt mixtures can lead to reduced environmental impact, efficient waste management, and improved pavement performance, benefiting both the construction industry and society.
2. MATERIALS AND METHODS
2.1. Aggregate
Asphalt 60/70 was used during the research. To comply with the gradation requirement for Asphaltic Concrete 14 (AC 14), the coarse and fine aggregates retrieved from the quarry were mixed in accordance with the guidelines provided by the Malaysian Public Works Department [17]. The AC 14 gradation envelope restricts specifying the range of aggregate sizes selected, which can be observed in Fig. (1).
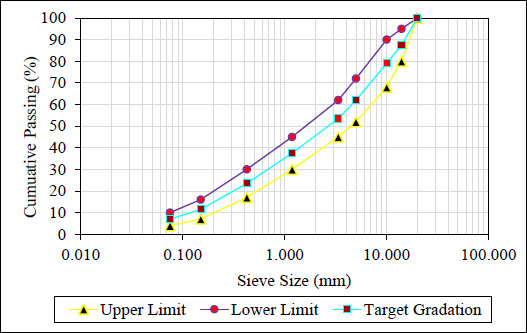
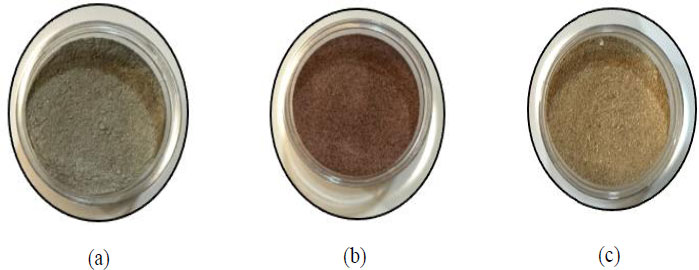
2.2. Hybrid Materials
The hybrid materials used in this research comprised three waste materials sources from agricultural and industrial sources: POFA, garnet waste, and sawdust (Fig. 2). POFA is produced through the combustion of palm oil biomass, for instance, empty fruit bunches as well as palm kernel shells, either in biomass power plants or through biomass disposal [18]. The garnet waste used in this research was a byproduct of the blasting pipe process carried out by Metallic Polymer Coating Sdn Bhd in Kemaman. Prior to use in hybrid asphalt mixtures, garnet waste was examined for the presence of mercury, and it was found to be safe for use [19]. As depicted in Fig. (2), the garnet waste exhibited a reddish-gray color and passed through a sieve size of 25µm. The sawdust used in this research was obtained as waste material from woodworking operations involving sawing, milling, and sanding of school furniture sourced from Cantuman Anggerik Sdn Bhd in Kemaman. Table 1 lists the characteristics of these hybrid materials.
Properties | POFA | Garnet Waste | Sawdust |
Particle size (µm) | 25 | ||
Bulk density (g/cm3) | 2.51 | 2.96 | 0.26 |
Specific gravity | 2.51 | 2.97 | 1.23 |
Moisture Content (%) | 6.1 | 0.4 | 5.02 |
2.3. Sample Preparation
Before incorporating POFA, garnet waste, and sawdust into the hybrid asphalt, a mechanical property test is conducted on the initial asphalt mixture. To modify the hybrid asphalt, varying percentages of POFA, garnet waste, and sawdust are prepared. These percentages include a control group at 0%, as well as 3%, 6%, and 9% for each waste material, determined based on the weight of the bitumen used in the mechanical tests. To facilitate the blending process, a high-shear mixer is used, operating at 1500 rpm and a 60°C temperature for 60 min duration. Using a speed of 1500 rpm ensures thorough dispersion of the hybrid materials within the asphalt mixture. The blending process itself takes place at 160°C temperature in accounting for the potential aging effects that occur within the asphalt at elevated temperatures. In ensuring the homogeneous as well as proper mixing of the waste materials with the asphalt, the mixing time is approximately 60 min.
2.4. Marshall Stability Test
To carry out the Marshall Stability Test, a 60/70 penetration grade asphalt is utilized as the primary material. To form the hybrid asphalt binder used in the mixture, waste materials are incorporated at varying proportions based on the weight of the binder. Consequently, these waste materials undergo a thorough blending process with the hybrid asphalt binder before being combined with the aggregates. Note that the selection of the bitumen content aligns with the requirements outlined in the Malaysian Standard Specification for Road Works, particularly for AC 14. To meet these specified requirements, the study options for five distinct bitumen contents are 4%, 4.5%, 5%, 5.5%, as well as 6%.
In the laboratory, the preparation and testing of hybrid asphalt mixture samples involve a series of systematic procedures. Initially, the aggregate, asphalt, and hybrid materials are meticulously combined and compacted at a controlled temperature of 180 ± 0.5°C. This compaction process is executed within a 101.6 mm inner diameter steel Marshall mould to maintain material integrity. To achieve compaction, the mixture is subjected to 75 blows on each side using a standard Marshall hammer. Following compaction, the specimens are delicately extracted from the mould and allowed to cool. To identify the bulk specific gravity, the specimens undergo a standardized measurement protocol outlined by the ASTM D2726 standard [20]. This procedure entails measuring the mass of the dry specimen in air, fully submerging the specimen in water for 3-5 min, and subsequently measuring the mass of the specimen in the air after surface drying. These measurements enable the calculation of the maximum theoretical specific gravity.
Subsequent tests involve assessing the flow characteristics as well as stability with regard to the specimens. The specimens are set in a testing machine and subjected to a constant rate of deformation until failure occurs after being submerged in a water bath for 40 min at 60°C, as illustrated in Fig. (3). The resulting stability values are expressed in terms of specimen flow. Additionally, critical parameters, for instance, Voids Filled with Asphalt (VFA), air voids, bulk density, stiffness, as well as Voids in the Total Mix (VTM), are determined. These measurements play a pivotal role in evaluating the properties of hybrid asphalt mixtures. Here, the testing procedures strictly adhere to the ASTM D6927 standard [21], using a CBR-Marshall testing machine for accurate and reliable results.
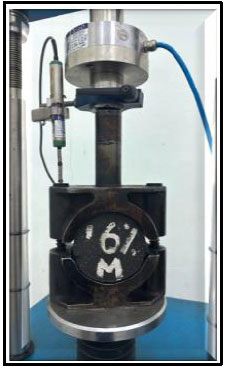
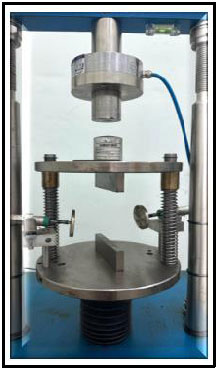
2.5. Indirect Tensile Strength (ITS) Test
The ITS test refers to a destructive method utilized to examine the resistance of asphalt mixtures against cracking due to ambient temperatures. In this study, the samples for the ITS test were prepared to use the Marshall Design Method, and the test itself was conducted following the guidelines outlined in ASTM D6931 [22]. The specimen height was determined, adhering to the required test method and rounding the values to the nearest 1 mm. The ITS test was conducted at 25°C under dry conditions. To apply the required compression, the Marshall specimens were loaded diametrically using steel strips mounted on a base equipped with perpendicular guide rods, as depicted in Fig. (4). The compression was applied for 50.8 mm/min at a constant rate. The mean ITS values from a total of six samples were assessed. Here, the maximum tensile strength accomplished was calculated utilizing (Eq. 1).
![]() |
(1) |
where
ITS = Indirect tensile strength, kPa
P = Peak load, N
D = Diameter of a specimen, mm
T = Thickness of a specimen, mm
Fig. (5) illustrates the step-by-step procedure for conducting the ITS test under both dry and wet conditions. The failure of the sample at the vertical diametral plane was observed and recorded at the peak load corresponding to the highest point. In the case of the ITS test under wet conditions, three specimens were first submerged in water for a 2 h duration at a temperature of 25°C. The test was then performed on the wet specimens. To assess the performance of the asphalt mixture, the ITR was calculated using (Eq. 2).
![]() |
(2) |
3. RESULTS AND DISCUSSION
3.1. Marshall Stability Characteristic
In this study, the hybrid asphalt mixture performance was examined by considering four different weight percentages of hybrid materials, namely POFA, garnet waste, and sawdust (0%, 3%, 6%, and 9%). Three Marshall specimens were assessed for each percentage in order to evaluate the effect of these hybrid materials on the asphalt mixture. Overall, 12 specimens were examined at an optimal binder content of 5%. The optimal binder content was high due to the binder absorption of the lightweight component by the POFA, garnet waste, and sawdust particles [23-25]. The purpose of conducting these tests was to analyze how adding hybrid materials influences the asphalt mixture performance. By varying the weight percentages of the hybrid materials, the study aimed to determine the optimal composition that would result in enhanced properties as well as performance characteristics of the hybrid asphalt mixture.
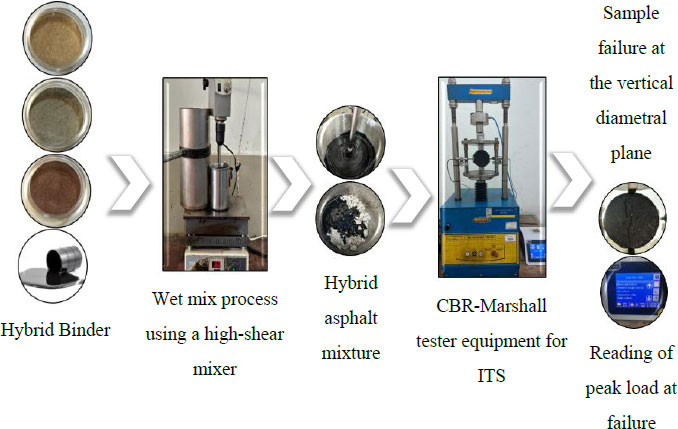
Table 2.
Parameter | Results of Hybrid Asphalt Mixture | JKR Specification (JKR 2008) | Conformity | |||
0% | 3% | 6% | 9% | |||
Stability, kN | 10.86 | 12.93 | 22.33 | 20.90 | > 8 kN | Pass |
Flow, mm | 3.49 | 3.58 | 3.74 | 3.97 | 2.0 – 4.0 mm | Pass |
Stiffness, kN/mm | 3.11 | 3.61 | 5.97 | 5.26 | > 2 kN/mm | Pass |
Void in Total Mix (VTM), % | 5.00 | 4.85 | 3.48 | 3.85 | 3.0 – 5.0% | Pass |
Void filled with Asphalt (VFA), % | 70.00 | 71.22 | 77.79 | 75.84 | 70 – 80% | Pass |
Table 2 introduces the Marshall stability test findings with regard to the hybrid asphalt mixtures containing hybrid materials. The parameters evaluated included stability (kN), flow (mm), bulk density (g/cm3), VTM (%), VFA (%), as well as stiffness (kN/mm). As can be observed, the hybrid asphalt mixtures indicate varying values ranging from 10.86 kN to 22.33 kN. All the properties comply with the specifications. The highest stability was 22.33 kN observed in the mixture with a 6% hybrid asphalt content. The rise in Marshall stability was connected to the occurrence of SiO2 from POFA [26], Fe2O3 from garnet waste [27], and CaO from sawdust [14] causing a stiffening effect due to their chemical composition. The high stability value of the hybrid asphalt mixture is potentially due to an increase in adhesive force between components of hybrid materials in the asphalt mixture [28]. High adhesive will cause the friction between the hybrid particles in the produced mixture to rise. Regarding flow, the recorded values range from 3.49 mm to 3.97 mm, indicating consistent flow properties across the different percentages of hybrid asphalt mixtures. The high flow value of the hybrid asphalt mixture could be attributed to the low workability of the produced mixture during the compaction process [29].
Generally, all mixtures exceeded the minimum limit of Marshall stability (8.0 kN), and the flow value was within the minimum limit of the JKR for the surface layer (2.0 - 4.0 mm). Due to the inclusion of hybrid content, mixtures have a higher stiffness and fewer air voids, which enhances the Marshall stability and flow values overall. This increases the resistance of the mixtures to rutting. Bulk density values range from 2.34 g/cm3 to 2.38 g/cm3, reflecting minimal variation among the mixtures. The VFA percentages ranged from 70.00% to 77.79%, while the VTM percentages ranged from 3.48% to 5.00%. These values fall within the standard range, indicating a good void distribution and filling characteristics of the hybrid asphalt mixtures. Lastly, the stiffness values range from 3.11 kN/mm to 5.97 kN/mm, with the highest stiffness observed in the mixture with 6% hybrid asphalt content. According to SEM analysis, the irregularly shaped and rough surface particles of POFA, garnet waste, and sawdust may increase the shear strength and the hybrid asphalt mixture stiffness [30-32].
The findings reveal that adding waste materials, such as POFA, garnet waste, and sawdust, to hybrid asphalt mixtures can have a positive impact on various properties. The mixtures exhibited acceptable stability, flow, bulk density, void distribution, and stiffness. Correspondingly, these findings indicate that hybrid asphalt mixtures meet the specified standards and can potentially offer sustainable and environmentally friendly alternatives for asphalt applications.
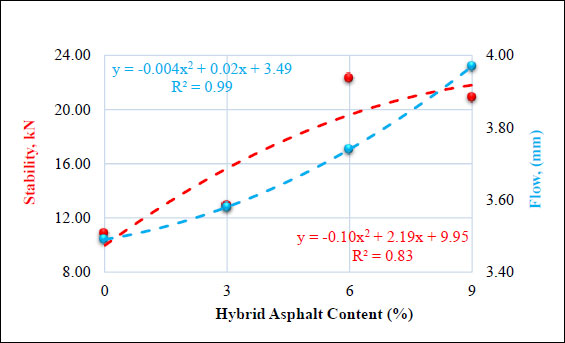
3.2. Correlation Analysis of Marshall Stability
Figs. (6-8) indicate the correlation graph of Marshall stability for hybrid asphalt between stability, flow, bulk density, and stiffness. The results of the correlation analysis for the use of hybrid asphalt containing waste material: POFA, garnet waste, and sawdust for modifying asphalt mixtures are summarized as follows. Note that the addition of hybrid materials significantly impacted the stability of the hybrid asphalt mixtures. The greatest stability value was observed with 6% hybrid asphalt, reaching 22.33 kN. The correlation equation for stability was y = -0.10x2 + 2.19x + 9.95, having a coefficient of determination (R2) of 0.83 (Table 3). This presents a strong correlation between the percentage of hybrid asphalt and the stability of the asphalt mixture.
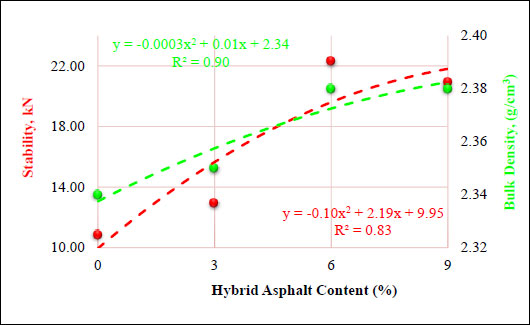
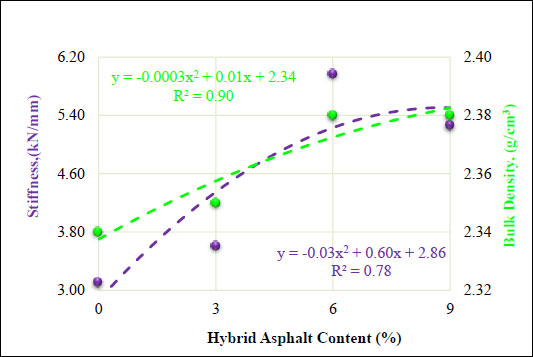
Table 3.
Parameter | Equation | Coefficient of Determination, R2 |
Stability (kN) | y = -0.10x2 + 2.19x + 9.95 | 0.83 |
Flow (mm) | y = -0.004x2 + 0.02x + 3.49 | 0.99 |
Bulk Density (g/mm3) | y = -0.0003x2 + 0.01x + 2.34 | 0.90 |
Stiffness (kN/mm) | y = -0.03x2 + 0.60x + 2.86 | 0.78 |
Hybrid Content % |
Optimum Asphalt Content |
Initial Weight (g) |
Final Weight (g) |
Total Loss of Weight (%) |
Requirement Specification | Conformity |
0 | 5 | 1255.20 | 1238.40 | 1.34 | < 20% | Fulfill |
3 | 1263.90 | 1247.82 | 1.27 | Fulfill | ||
6 | 1251.93 | 1249.59 | 0.18 | Fulfill | ||
9 | 1256.10 | 1252.33 | 0.30 | Fulfill |
Table 3 presents the equation as well as R2 of the hybrid asphalt mixtures containing hybrid materials. The percentage of hybrid asphalt affects how the mixture of hybrid asphalt flows. The modified asphalt mixture with 9% hybrid asphalt exhibited the highest flow value (3.97 mm), whereas the mixture with 3% hybrid asphalt had the lowest flow value at 3.58 mm. The flow equation was y = -0.004x2 + 0.02x + 3.49, having a R2 of 0.99. Thus, this proposes a robust relationship between the hybrid content and flow characteristics of the asphalt mixture.
With 6% and 9% hybrid content, the maximum bulk density value of 2.38 g/cm3 was recorded. These stability findings might be connected to the bulk densities of the mixtures. With an R2 of 0.90, the correlation equation for the bulk density was y = -0.0003x2 + 0.01x + 2.34. Note that the trends of the bulk density were similar to the trend of the stability. This indicates a moderate correlation between the hybrid content as well as the bulk density of the asphalt mixture. In addition, the stiffness value for the improved asphalt mixture with 6% hybrid content was 5.97 kN/mm. The stiffness equation has an R2 of 0.78 and was written as y = -0. 03x2 + 0.60x + 2.86. Hence, this shows a moderate relationship between the hybrid content as well as the stiffness of the asphalt mixture. In comparison to the conventional asphalt mixture, the performance of hybrid asphalt mixtures was generally improved.
3.3. Loss of Weight (LOW)
The Loss of Weight (LOW) of the specimens was determined by utilizing (Eq. 3), which calculates the LOW percentage relying on the initial as well as final weights of the specimens. Wi represents the average initial weight concerning three specimens prior to the test, whereas Wf expresses the average weight of the same three specimens after the test. By applying Eq. (3), the LOW percentage can be determined.
![]() |
(3) |
From Table 4, the hybrid asphalt mixture LOW initially decreased with increased hybrid content. At 0% hybrid asphalt content, the loss weight of specimens was approximately 1.34%. However, as the hybrid asphalt content increased to 3%, 6%, and 9%, the values of LOW decreased to approximately 1.27%, 0.18%, and 0.30%, respectively. These findings suggest that raising the hybrid asphalt content in the mixture led to a reduction in LOW, indicating improved durability and resilience against aging and environmental factors.
The table provides data on the relationship between hybrid asphalt content, stability, and LOW in an asphalt mixture. The stability values, ranging from 10.86 kN to 22.33 kN, indicate the resistance of the asphalt mixture to deformation under traffic loads along with environmental conditions. Increasing the hybrid asphalt content tends to lead to higher stability values, suggesting improved resistance to deformation and increased structural integrity of the asphalt mixture. In addition to stability, the table also displays the LOW percentages for each hybrid asphalt content percentage. The LOW percentages, ranging from 0.30% to 1.27%, provide insight into the extent of aging and deterioration in the asphalt mixture. Meanwhile, the LOW percentages do not strictly follow the same pattern as the stability values with increasing hybrid asphalt content. The general trend indicates that higher hybrid asphalt content reduces LOW, implying improved durability and resilience against aging and environmental factors.
In addition, Fig. (9) demonstrates the correlation between stability and LOW in hybrid asphalt content. The analysis of LOW in 0% control and hybrid asphalt mixtures reveals the LOW percentage impacting the stability of the mixtures. As illustrated in Fig. (9), the hybrid asphalt mixtures exhibit higher LOW in comparison to the control sample. Nevertheless, the hybrid asphalt mixture with 6% content demonstrates the lowest LOW. Similar findings are confirmed by Jeffry et al. [5] using a modified asphalt mixture comprising nano-charcoal coconut shell ash. Due to the diminished interaction between the used waste materials, the LOW in the hybrid asphalt mixture denotes a loss of adhesion between the aggregates and asphalt. Other than that, the stability of the asphalt mixtures is adversely affected by this increased LOW. Consequently, the hybrid asphalt mixture with 6% content exhibits good bonding between the aggregates and asphalt, which results in the maximum LOW as well as contributes to the overall stability of the hybrid asphalt mixture. It is worth mentioning that the requirement specification of this test, recommended by previous studies and ASTM D7064/D7064M [33], is 20% at the very most [34, 35].
Remarkably, as the hybrid asphalt content increases, the corresponding LOW percentages decrease. For example, the LOW percentages for 0%, 3%, 6%, and 9% hybrid asphalt content are 0.02%, 0.04%, 0.17%, and 0.26%, respectively (Table 5). This implies that a higher hybrid asphalt content in the mixture contributes to reduced aging and deterioration. The modified asphalt with a greater hybrid content exhibits enhanced resistance to oxidative and environmental factors, resulting in less LOW over time. Here, the result highlights the importance of incorporating an adequate amount of hybrid material: POFA, garnet waste, and sawdust, to enhance the long-term durability of the asphalt mixture
Fig. (10) illustrates the relationship between hybrid asphalt content, ITS, and LOW in a hybrid asphalt mixture. The ITS values and LOW percentages vary with different hybrid asphalt content percentages. As the hybrid asphalt content increases from 0% to 9%, there is a noticeable trend of increasing ITS values. For instance, the ITS values for 0%, 3%, 6%, and 9% hybrid asphalt content are 1058 kPa, 1207 kPa, 1469 kPa, and 1601 kPa, respectively. This suggests that a higher hybrid asphalt content leads to an improvement in the hybrid asphalt mixture tensile strength, which indicates enhanced resistance to cracking and improved performance.
Furthermore, there is a correlation between the ITS and the LOW percentages. Generally, as the ITS value increases, the LOW percentage decreases. The relationship can be observed in Fig. (10), where the hybrid asphalt mixtures with higher ITS values tend to have lower levels of aging and LOW. This is demonstrated by the decreasing LOW percentages as the ITS values increase from 1058 kPa to 1601 kPa. The improved tensile strength enables the asphalt to withstand external stresses, reducing its susceptibility to cracking and mitigating the aging process. Hence, the findings emphasize the importance of designing asphalt mixtures with higher tensile strength to ensure long-lasting performance and minimize deterioration over time.
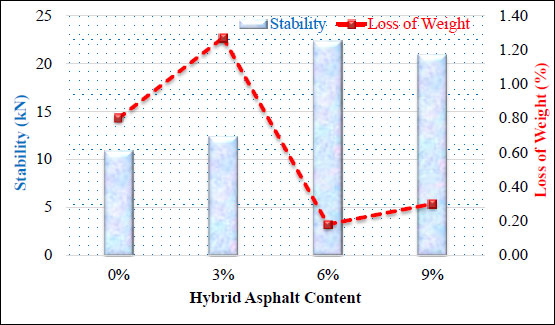
Hybrid Content % |
Optimum Asphalt Content |
Initial Weight (g) |
Final Weight (g) |
Total Loss of Weight (%) |
Requirement Specification | Conformity |
0 | 5 | 1257.20 | 1257.00 | 0.02 | <20% | Fulfill |
3 | 1250.24 | 1249.78 | 0.04 | Fulfill | ||
6 | 1253.85 | 1251.67 | 0.17 | Fulfill | ||
9 | 1254.80 | 1251.58 | 0.26 | Fulfill |
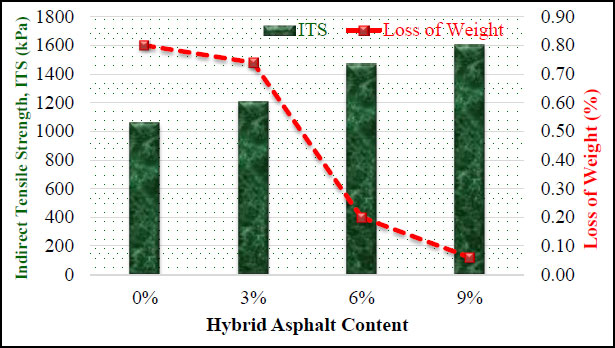
3.4. Indirect Tensile Strength (ITS)
One of the key characteristics concerning asphalt mixtures is their tensile strength, which is directly associated with fracture as well as deformation resistance. The tensile strength of the hybrid asphalt was measured at 25°C. Fig. (11) illustrates the failure crack for eight samples of dry and wet conditions with 0%, 3%, 6%, and 9% hybrid asphalt content. Fig. (12) presents the ITS values for various percentages of hybrid asphalt content of garnet waste, POFA, as well as sawdust in dry and wet conditions. Under dry conditions, as the hybrid asphalt content increased, there was a general trend for increasing ITS values. For conventional, at 0% hybrid asphalt content, the ITS was recorded as 1058 kPa, and it gradually increased to 1207 kPa, 1469 kPa, and 1601 kPa when the hybrid asphalt content reached 3%, 6%, and 9%, respectively. Under wet conditions, the correlation between the hybrid asphalt content as well as ITS values followed the same pattern. At 0% hybrid asphalt content, the ITS was 935 kPa, which increased to 1165 kPa at 3% hybrid asphalt content. Nevertheless, when the hybrid asphalt content was further enhanced to 6%, the ITS value increased significantly to 1388 kPa. Surprisingly, at a 9% hybrid asphalt content, the ITS increased to 1492 kPa, indicating the highest increment in performance compared to the 6% hybrid asphalt content.
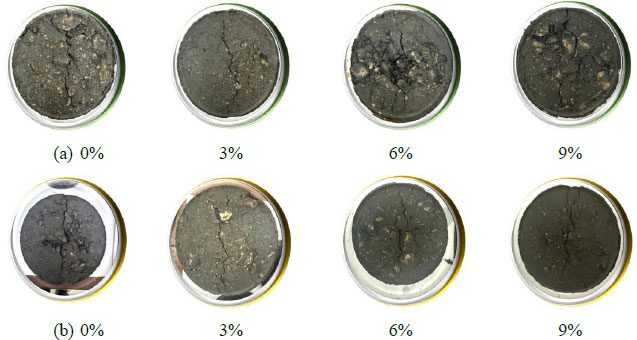
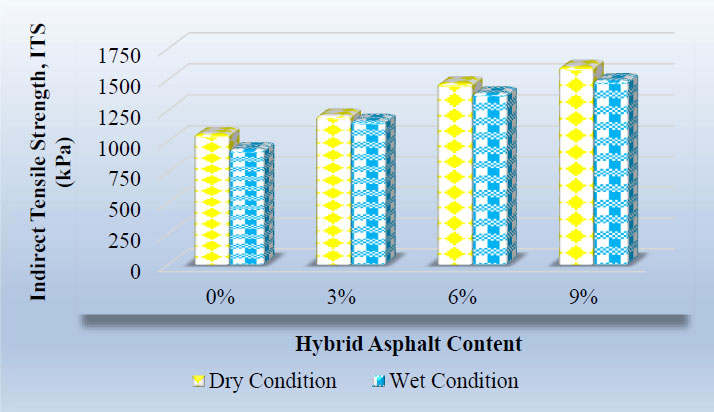
Based on the data given in Fig. (12), the conclusions can be drawn under dry conditions as follows, increasing the hybrid asphalt content tends to improve the ITS values, indicating an enhanced tensile strength as well as resistance to cracking. The outcomes suggest that the performance of the asphalt mixture was improved by the inclusion of hybrid asphalt. It was recorded that the utilization of three waste materials reduced the susceptibility of the mixture to moisture damage. Here, these outcomes can be attributed to the unique properties with regard to hybrid material, which enhance the bond with the asphalt and reduce the affinity of aggregates towards the water. As a result, the overall susceptibility to moisture damage is lowered [36]. Under wet conditions, the relationship between the hybrid asphalt content and ITS values is also consistent. Meanwhile, the 3% hybrid asphalt content improved performance compared to the 0% content. The 6% content exhibited even better performance. Subsequently, ITS increased when the hybrid asphalt content reached 9%. Overall, the outcomes of the ITS tests signify that the asphalt mixtures performed better in dry conditions compared to the modified and control mixtures in wet conditions. The reduced ITS values observed in the wet samples can be primarily attributed to the negative impact of water on the asphalt binder adhesion properties [37].
Further analyses and investigations are required to understand the specific mechanisms underlying these observations. Factors, such as the composition and properties of the hybrid asphalt and the interaction between the hybrid materials and moisture, could play a role in the variations observed under wet conditions. Overall, the data suggest that incorporating a moderate percentage of hybrid asphalt, approximately 6%, can enhance the tensile strength as well as resistance to cracking of the asphalt mixture, particularly under dry conditions. However, the effect of hybrid asphalt content on ITS under wet conditions requires further study to establish consistent trends and optimize the mixture design for different environmental conditions.
The correlation between the ITR as well as the dosage of hybrid materials is shown in Fig. (13). A greater ITR value was considered to denote high-performance asphalt mixtures, but a lower ITR value (< 80%) denoted failure criteria. At 0% hybrid asphalt content, the ITR is recorded as 88.4%. This value represents the baseline performance of the asphalt mixture without any hybrid asphalt addition. When the hybrid asphalt content is increased to 3%, the ITR value rises to 96.5%. In comparison to the performance of the asphalt mixture with 0% hybrid asphalt content, this shows an increase. This demonstrated that mixtures modified by hybrid materials lead to a reduction in the susceptibility to moisture damage. Continuing the trend, at 6% hybrid asphalt content, the ITR slightly decreases to 94.5%. Although there is a minor decline in performance in comparison to the 3% hybrid asphalt content, the ITR value remains higher than that of the 0% hybrid asphalt content. However, the most notable change occurs at 9% hybrid asphalt content, where the ITR drops significantly to 93.2%.
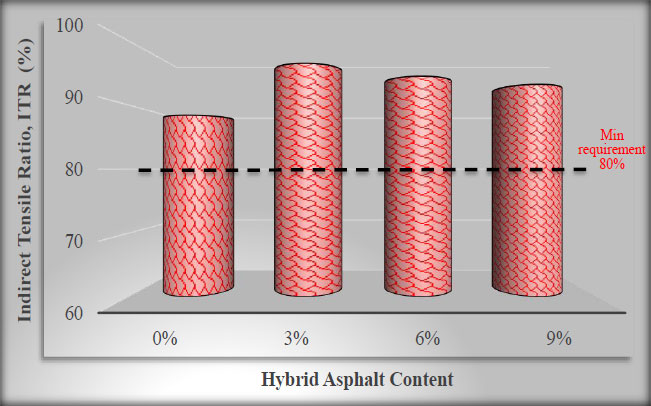
This suggests that the higher proportion of hybrid asphalt content positively affects the performance of the asphalt mixture. These outcomes might be explained by the wet process of blending, which enlarges the size of the garnet particles in the asphalt mixtures [24]. Garnet waste is one of the waste materials used in hybrid asphalt content. In summary, Fig. (13) demonstrates that incorporating a certain percentage of hybrid asphalt content (up to 3%) can enhance the asphalt mixture performance, as determined by higher ITR values. However, when the hybrid asphalt content exceeds 3% and reaches 9%, the performance declines, leading to a lower ITR value, which is in accordance with the results provided by Alemu et al. [38]. All the mixtures achieved an ITR value higher than the minimum requirement of 80%. Notably, the mixture incorporating 3% hybrid asphalt exhibited superior performance in terms of moisture susceptibility.
CONCLUSION
Hybrid asphalt mixture consisting of asphalt, aggregate and hybrid materials as per the ITS findings revealed improved strength values compared to the control asphalt mixture sample for both wet as well as dry conditions samples. The best endurance outcomes were shown to be 6% of hybrid asphalt content. According to the ITR, all values are greater than the minimal requirement, indicating that all samples meet the specifications. The 3% hybrid asphalt content achieved the greatest ITR value. Thus, compared to the AC 14 control asphalt mixture, the hybrid asphalt mixture can withstand fatigue, rutting deformation, as well as moisture susceptibility better. The hybrid asphalt mixture performed typically greater than the conventional ones in terms of Marshall stability, flow, as well as stiffness values. All findings from this study on the stability and tensile strength of hybrid asphalt mixtures are aligned with the results from previous studies, and each of the waste materials; POFA, garnet waste, and sawdust can be used as alternative modifiers in asphalt mixtures. The advantages of using all three waste materials represent promising strategies for achieving sustainability while improving the mixture performance.
LIST OF ABBREVIATIONS
ITS | = Indirect Tensile Strength |
POFA | = Palm Oil Fuel Ash |
ITR | = Indirect Tensile Ratio |
AC 14 | = Asphaltic Concrete |
NCA | = Nano-charcoal Shell Ash |
VFA | = Void Filled with Asphalt |
VTM | = Void in Total Mix |
CONSENT FOR PUBLICATION
Not applicable.
AVAILABILITY OF DATA AND MATERIALS
The data used to support the findings of this study are included in the article.
FUNDING
This study was funded by the Universiti Malaysia Pahang Al-Sultan Abdullah, Funder ID: Internal University Grant, Awards/Grant number: PGRS2303117.
CONFLICT OF INTEREST
The authors declare no conflict of interest, financial or otherwise.
ACKNOWLEDGEMENTS
The support provided by Universiti Malaysia Pahang Al-Sultan Abdullah for this study is highly appreciated.