All published articles of this journal are available on ScienceDirect.
Evaluation of the Properties of Fiber-Reinforced Pervious Concrete Pavement Incorporating Glass Powder and Kaolin
Abstract
Introduction
Pervious concrete has been significantly helpful in water quality control and preventing surface runoff through easy infiltration and percolation of water. A developing country such as Nigeria is prone to flooding, and promoting pervious concrete will significantly mitigate this problem. However, structural issues are associated with pervious concrete, such as weak bonds and durability concerns due to the infiltration of deleterious materials.
Methods
The study incorporates glass powder, kaolin and sisal fiber to improve the performance of pervious concrete. Glass powder and Kaolin were incorporated as supplementary cementitious materials at 0, 10, and 20% and sisal fiber-reinforced at 0, 1, and 2%. The pervious concrete mixtures at 28 days were subjected to water absorption, permeable voids, and compressive and split tensile strengths.
Results
The results indicate that the fiber-reinforced pervious concrete with glass powder and Kaolin met the strength requirements. However, the strength resulting from incorporating Kaolin is much higher; hence, Kaolin is preferable in times of strength in fiber-reinforced pervious concrete. Nonetheless, an equal 10%-10% combined use of kaolin and glass powder and 1% sisal fiber proves an alternative to obtaining strength values within ACI specification.
Conclusion
These research findings will enhance the performance of pervious concrete, an eco-friendly and responsible approach to managing rainwater.
1. INTRODUCTION
Pervious concrete, called permeable or porous concrete, consists of open-graded aggregates bonded by a cementitious matrix. It allows for the easy passage of air and fluid from the contact layer to underlying layers called the aquifer [1, 2]. Pervious concrete has eco-friendly potential, and traffic safety makes it suitable for parking lots and road pavements [3-6]. It has a significant purpose in managing stormwater and controlling the quantity of water [7]. The use of pervious concrete can help promote rapid infiltration of water. Pervious concrete also has several other advantages, including the ability to reduce noise, reduce heat, conserve native ecosystems, recharge groundwater, and protect tree development [7-11]. Furthermore, beyond its functional advantages, pervious concrete offers unique advantages in architectural design. Architects are integrating pervious concrete into their projects for its aesthetic appeal. The porous nature of pervious concrete permits innovative designs that incorporate green spaces, such as rain gardens and bioswales, into urban settings. Moreover, the customizable color and texture options available with pervious concrete offer architects a versatile material for creating distinctive and environmentally friendly pavements, plazas, and facades [12]. However, it has some shortcomings, such as debris blocking the water pathway, thereby reducing the hydraulic conductivity. The weak bond between aggregates also results in rapid deterioration due to cracking, excessive wearing, and permanent deformation, i.e., creep could occur due to cyclic and heavy loads. In addition, there are durability concerns due to the infiltration of deleterious materials, reducing the concrete's structural integrity [1]. However [13], reported that pervious concrete has a higher durability of 30-50% more than conventional concrete.
A developing country like Nigeria experiences intense rainfall compounded by inadequate residential and industrial layout planning in most urban regions. Implementing effective Environmental Protection Agency (EPA) standards makes it difficult. The country is prone to perennial flooding occasioned by high surface runoff and uncontrolled urbanization, which affects groundwater recharge. The possibility of improving the safety of the road through reduced runoff is of great importance to pavement engineers' hence, the use of pervious concrete can be applied in this regard. The groundwater table is affected significantly because of this. With a projection of about 2.5 billion population increase by 2050 due to urbanization and population growth, there will be an expansion of urban areas and impervious surfaces [14], which will consequently affect the groundwater table. Pervious concrete will help maintain the groundwater level that would have otherwise been significantly affected if, with growing urbanization, most areas were covered with impermeable cement concrete [15].
Even though pervious concrete is considered an environmentally friendly material, the conventional materials used in its production do not align with this trend due to its properties and usage [16]. Cement, for example, is a common binder in the production of pervious concrete, and the activities associated with cement production cause significant environmental damage, including ecosystem disruption and soil, air, and water contamination. The environmental impact of cement production may be limited by the employment of other constituents acting as Supplementary Cementitious Materials (SCMs). The sources of these constituents can be from the calcination of agricultural waste, naturally occurring earth deposits, and industrial by-products [17]. These materials include rice husk ash, cassava peel ash, blast furnace slag, fly ash, metakaolin, glass powder, quarry powder, calcite, etc. Utilizing these constituent materials as SCMs will contribute significantly to furthering the environmental sustainability of pervious concrete. According to [16] and [18], incorporating these materials into pervious concrete can improve certain properties while negatively impacting others to differing extents based on factors such as the type, source, content, and characteristics of the waste. Furthermore, more sustainable, clean, and green construction could be achieved by incorporating waste materials into pervious concrete [19].
Glass waste is one of the most valuable materials as regards the new ideologies of reusing materials after their primary service life [20-22]. This is because of its applicability in partial or total replacement of concrete/ mortar constituents – such as sand replacement in road infrastructure [23], as binder mixed with Cement [24, 25], and as coarse aggregate – due to its availability in different sizes ranging from a few micrometers to few centimetres [26]. In several European countries, the amount of waste glass collected exceeds that produced by over 80% [27], and a considerable fraction of this waste glass is recycled. Despite this, the waste glass that is not reusable is a rising problem that needs to be curbed sustainably. Using this waste glass in construction as building materials – either as a full or partial replacement – is a sustainable solution as it reduces the demand for conventional materials and clears the environment of non-biodegradable waste [26]. Glass is comparatively similar to conventional SCMs in chemical composition and phase [28, 29]. With a silica content of over 70%, glass powder possesses pozzolanic properties as much as traditional SCMs such as silica fume [30]. Similarly, Kaolin is a very reactive pozzolanic material that shows desired characteristics when utilized in concrete alongside other SCMs. It improved the durability properties of concrete in coastal/marine areas affected by sulphate infiltration [31].
Concrete is brittle, and even before recent years, when the mechanism of reinforcing brittle matrices with fiber started being understood scientifically, fibers have been applied to make mortar/concrete challenging [32]. Intro- ducing fibers as secondary reinforcement in pervious concrete could improve the matrix's mechanical performance [33, 34]. Fibers ameliorate concrete's tensile strength, toughness, ductility, and durability [35]. Various fibers have been incorporated in cement composite due to their crack-bridging action and ductility. Commonly used fibers include metallic, mineral, polymeric, and vegetable fibers. Using vegetable fibers such as sisal, jute, coconut, wood and bamboo as reinforcing material has shown good prospects [32, 33]. According to [36], over four million tons of sisal fiber are produced annually across the globe due to the ease of cultivating sisal plants. This study used sisal fiber as secondary reinforcement in pervious concrete.
Despite the fact that pervious concrete is regarded as an environmentally benign material, the standard materials used in its production do not follow the same trend due to its properties and usage [14]. According to [37], huge amount of non-biodegradable construction wastes have been generated with enormous pressure on landfills. One such waste is glass. Previous studies have incorporated waste glass cullet as aggregate in previous concrete, while this study incorporates waste glass powder as SCM. Another motivation for the study is the promotion of an underutilized natural occurring material known as kaolin. Kaolin is readily available in Ire Ekiti, Ekiti State, Nigeria, and can be incorporated as SCM in pervious concrete. This study is focused on conducting a preliminary investigation on the effect of incorporating both waste glass powder and kaolin as SCMs in pervious concrete. The study also considered the incorporation of sisal fibers to improve the bond between the aggregate and binders in pervious concrete. This will provide an insight into the fundamental properties of pervious concrete containing both SCMs and sisal fiber since at the moment, there is a paucity of literature on the combined effect of these three materials on the performance of pervious concrete. These pervious concrete specimens have been tested for permeable voids, water absorption, and compressive and split tensile strengths. This study will help promote sustainability by reducing the required quantity of Portland cement, reducing greenhouse effects. The possibility of incorporating the binary blend of glass and kaolin powder as partial replacements for Cement in producing pervious concrete. In addition, the reinforcing effect of varying contents of sisal fiber in enhancing the bond strength between the binder and aggregate of pervious concrete was also evaluated.
2. MATERIALS, METHODS AND TESTING
2.1. Materials
The materials used are shown in Fig. (1). The cement used was grade 42.5N Dangote brand, available in the Ado-Ekiti local market. Coarse aggregate passing through a sieve size of 19 mm and retained on an 8 mm sieve was sourced from a local quarry in Ado Ekiti. The Glass was obtained from Federal Polytechnic, Ado Ekiti, and it was crushed to powder as presented in Fig. (1b). The sisal fiber, shown in Fig. (1b), was purchased from a local market in Ado Ekiti and cut to 30 mm. Kaolin is a naturally available material in Ire, Nigeria and is shown in Fig. (1c). A superplasticizer adhering to (ASTM C494/C494M-17) standards was utilized to enhance the workability of the concrete mix. Advanced Chemical Technology supplied it in Ikeja, Lagos, Nigeria. As previously reported by [34]. The gradation curve of the binders is presented in Fig. (2), while the specific gravity and chemical composition are shown in Table 1. From Fig. (2), it was observed that the cement used in the study and the incorporated SCMs (Glass powder and kaolin) had similar particle size distribution.
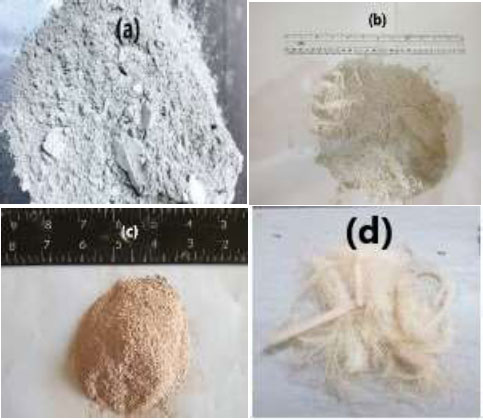
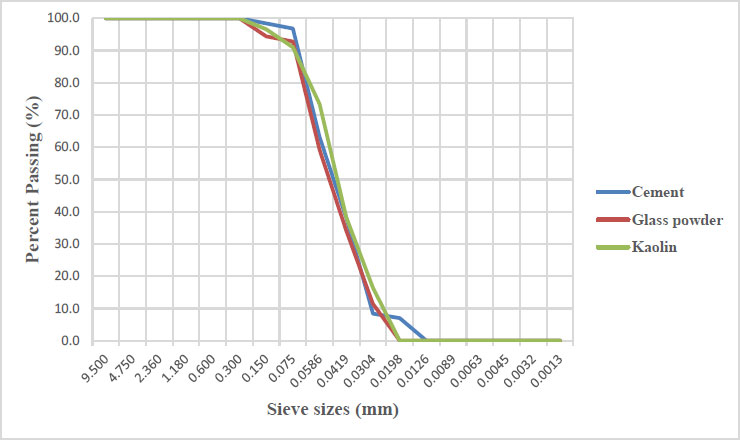
Oxides | Composition (%) | ||
---|---|---|---|
Glass Powder | Kaolin | Cement | |
SiO2 | 77.46 | 46.87 | 20.11 |
CaO | 0.04 | 11.07 | 57.80 |
Al2O3 | 3.74 | 34.50 | 10.25 |
Fe2O3 | 1.51 | 3.08 | 2.53 |
MgO | 0.00 | 0.00 | 4.50 |
K2O | 0.16 | 0.76 | 0.32 |
SO3 | 0.35 | 0.81 | 2.57 |
Specific gravity | 2.97 | 2.33 | 3.09 |
2.2. Study Methods
A 30-litre capacity pan mixer was used to mix the chosen previous concrete materials. The batching of the created concrete samples was done according to Table 2. The aggregate was introduced to the pan and blended for 30 seconds. Next, approximately 5% of the binder and a small amount of water were added to the mixture and blended for 1 minute to coat the aggregate particles. When fiber was used, it was added and mixed for 1 minute. Subsequently, the remaining amount of binder, water, and superplasticizer was added to the mixer and mixed for 1 to 2 minutes to ensure proper blending. After mixing, the pervious concrete was placed in 100 mm cube molds and cylindrical molds measuring 200 mm in height and 100 mm in diameter. The mixture was placed in 3 layers, and each layer was compacted using a compaction rod. Following compaction, the concrete samples were wrapped in plastic and kept at room temperature. After 24 hours, the molded samples were demolded and then allowed to cure for the required number of days before testing.
Test No. | Glass Powder (%) | Kaolin (%) |
Cement (%) |
POP Fiber (%) | Total Binder (kg/m3) | Coarse Aggregate (kg/m3) | Water (kg/m3) |
HRWRA (kg/m3) |
---|---|---|---|---|---|---|---|---|
0G10K2F | 0 | 10 | 90 | 2 | 420 | 1554 | 134.4 | 8.4 |
10G20K2F | 10 | 20 | 70 | 2 | 420 | 1554 | 134.4 | 8.4 |
0G10K0F | 0 | 10 | 90 | 0 | 420 | 1554 | 134.4 | 8.4 |
10G0K0F | 10 | 0 | 90 | 0 | 420 | 1554 | 134.4 | 8.4 |
20G10K0F | 20 | 10 | 70 | 0 | 420 | 1554 | 134.4 | 8.4 |
20G10K2F | 20 | 10 | 70 | 2 | 420 | 1554 | 134.4 | 8.4 |
0G20K1F | 0 | 20 | 80 | 1 | 420 | 1554 | 134.4 | 8.4 |
20G20K1F | 20 | 20 | 60 | 1 | 420 | 1554 | 134.4 | 8.4 |
10G20K0F | 10 | 20 | 70 | 0 | 420 | 1554 | 134.4 | 8.4 |
0G0K1F | 0 | 0 | 100 | 1 | 420 | 1554 | 134.4 | 8.4 |
10G10K1F | 10 | 10 | 80 | 1 | 420 | 1554 | 134.4 | 8.4 |
20G0K1F | 20 | 0 | 80 | 1 | 420 | 1554 | 134.4 | 8.4 |
10G0K2F | 10 | 0 | 90 | 2 | 420 | 1554 | 134.4 | 8.4 |
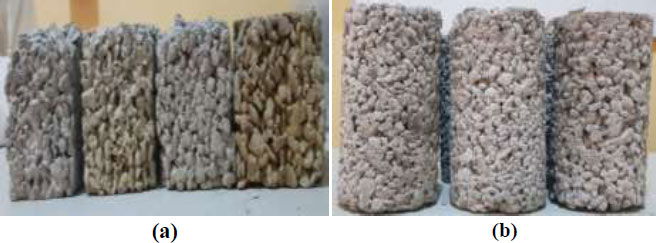
2.3. Testing
2.3.1. Compressive Strength
A compression machine with a load capacity of 1500 kN was utilized to evaluate the compressive strength. The tests were carried out at 28 days in accordance with the guidelines provided in (ASTM C349-18). The results were expressed as an average of three specimens. The compressive strength was computed by dividing the greatest crushing load in Newtons (N) by the effective area in millimeters (mm2), using Eq. (1). Cube samples of fiber-reinforced pervious concrete are presented in Fig. (3a).

2.3.2. Split Tensile Strength
The Split tensile strength test was carried out at 28 days using a control compression machine in accordance with (BS EN 12390-6). Eq. (2) calculated the split tensile strength of the specimens tested after recording the maximum splitting load for each test. The results were expressed as an average of three specimens. Cylindrical samples of fiber-reinforced pervious concrete are presented in Fig. (3b).

Ft =Tensile Strength (N/mm2)
P = Failure Load (N)
D = Cylinder's Diameter (mm)
L = Cylinder's Length (mm)
2.3.3. Permeable Voids and Water Absorption
To comply with (ASTM C642-21), the water permeability characteristics of the concrete were assessed using permeable voids and water absorption tests. Three 200 mm by 100 mm cylindrical specimens were cured in water for 30 days. The weight is measured after the soaked specimens' surfaces are dried after eliminating the surface moisture with a towel (W30). The specimens are then placed in an oven at a constant temperature of 105±50 oC until they attain a consistent weight (Wod). The percentages of permeable voids are then calculated using Eq. (3):

Where V is prism specimen volume.
Next, the specimens that have been oven-dried are completely submerged in water to conduct the initial surface absorption (ISA) and final water absorption (FWA) tests. The specimens are removed from the water immersion after 30 minutes and 96 hours, and their weight is measured to determine the mass gained for ISA and FWA, respectively. Equations 4 and 5 were used to calculate the ISA and FWA values:


Where W30min represents the weight of the surface dried specimen after being immersed for 30 minutes, and W96h is the weight of the surface-dried specimen after being immersed for 96 hours.
3. RESULTS AND DISCUSSION
3.1. Compressive Strength
The study has indirectly evaluated the bond strength between aggregate under uniaxial compression. According to [1], the compressive strength of pervious concrete is usually low. This has necessitated researchers to employ different approaches to improve the strength of pervious concrete. Fig. (4) shows the results of the compressive strengths of pervious concrete specimens. It can be seen that there is a variation in the values of the compressive strength. The highest compressive strength of 8.031 MPa at 28 days was obtained with mix 0G0K1F. For this mix, Cement was the only binder. According to a study by [38-42], the amount of cement paste in the pervious concrete mixture is directly related to the increase in compressive strength. This can also be attributed to the 1% sisal fiber in the mix. A previous study by [7] using a similar aggregate size and higher cement content without fiber achieved a lower compressive strength of 7.20 MPa. However, considering the SCM mix, the highest compressive strength of 7.37 MPa was observed with mix 10G10K1F. The mix is a ternary blend containing an equal percentage of glass powder and Kaolin at 10% each. Mixes 0G10K0F and 0G10K2F containing 0% glass powder, 10% kaolin, and sisal fiber increased from 0% to 2%, and the compressive strength increased from 5.07 MPa to 5.42 MPa. The increased strength observed could be attributed to incorporating sisal fiber into the mix. Comparing mix 0G10K0F with combination 10G0K0F, the compressive strength reduced from 5.07 MPa to 2.62 MPa. From this result, it could be inferred that adding 10% of Kaolin as a binary blend in pervious concrete is more effective on compressive strength than adding 10% glass powder.
According to [43], the compressive strength of pervious concrete can range from 3.5 to 28 MPa. Therefore, samples 0G10K2F, 0G10K0F, 0G0K1F, and 10G10K1F with compressive strength of 5.424, 5.07, 8.031 and 7.368 MPa, respectively, are within the ACI specification. Generally, from the results obtained, it could be inferred that the best form for incorporating kaolin and glass powder as SCM in pervious concrete is 10% each. Fig. (5) depicts the relationship between the compressive strength and fiber content within the cementitious content. It can be seen that as fiber content increases, the glass powder causes a significant decrease in compressive strength. In contrast, the Kaolin causes a decrease and increases in compressive strength as the fiber content increases. Furthermore, it can be seen that the strength results from incorporating Kaolin are much higher than that of glass powder. Hence, incorporating Kaolin as a supplementary cementitious material in fiber-reinforced pervious concrete is preferable regarding strength. A similar study by [44] also reported a 15% increase in compressive strength by incorporating metakaolin in pervious concrete, which corroborated the findings of this study.
3.2. Split Tensile Strength
The most prevalent methods for determining the tensile behaviour of concrete are flexural strength and splitting tensile strength tests. However, it is preferable due to the sensitivity of splitting tensile test to concrete micro-cracks. Fig. (6) depicts the results of the split tensile strengths of pervious concrete specimens. It can be seen that the split tensile strength of mix 10G20K0F (0.35 MPa) is the lowest, and mix 0G10K2F (2.69 MPa) was the highest. A split tensile strength of 1.5 MPa was obtained by [7] using a similar aggregate size and higher cement content. This study has observed a 44% increase in split tensile strength with 2% sisal fiber and 10% kaolin compared to the previous study by [7], where SCM and fiber were not incorporated. From these results, it can be inferred that the high split tensile strength could be attributed to the presence of Kaolin and sisal fiber. A close look at the mix constituent containing 10% kaolin without glass powder and fiber (0G10K0F) also gave a high split tensile strength, further reiterating Kaolin's positive influence on fiber-reinforced pervious concrete. A comparison amidst mix 0G0K1F, mix 0G10K0F and mix 10G0K0F with split tensile strengths of 1.93 MPa, 2.113 MPa and 1.149 MPa, respectively, indicates that either the presences of Kaolin or sisal fiber can positively influence the tensile behaviour of pervious concrete. Furthermore, comparing mix 0G10K0F and mix 10G0K0F gave split tensile strengths of 2.113 MPa and 1.149 MPa, respectively. This result indicates that incorporating Kaolin in the pervious concrete mix is preferable to incorporating glass powder in enhancing the split tensile strength. However, mix 0G20K1F containing 20% kaolin gave low split tensile strength even with 1% sisal fiber. From this, it could be inferred that increasing kaolin content beyond 10% is not advisable for improved split tensile strength. Fig. (7) depicts the relationship between the split tensile strength and fiber content within the cementitious content. It can be seen that as fiber content increases, the split tensile strength decreases with increasing glass content. However, for Kaolin, there is variability in the split tensile strength.
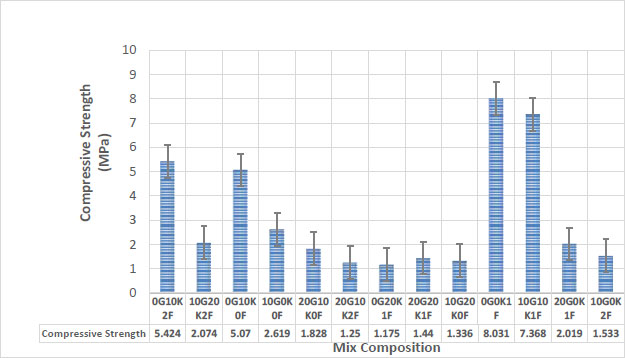
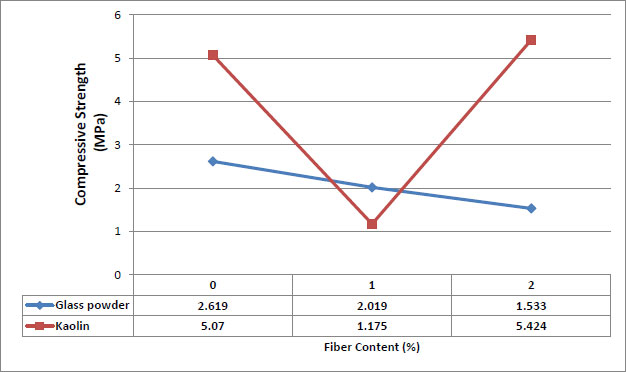
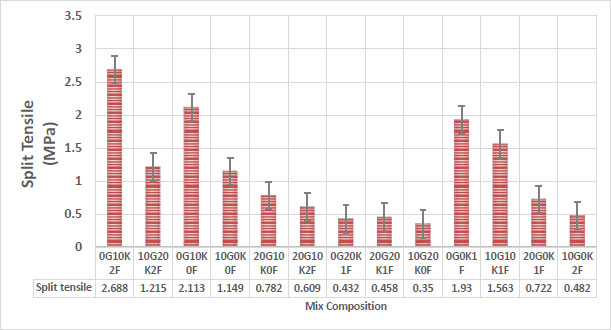
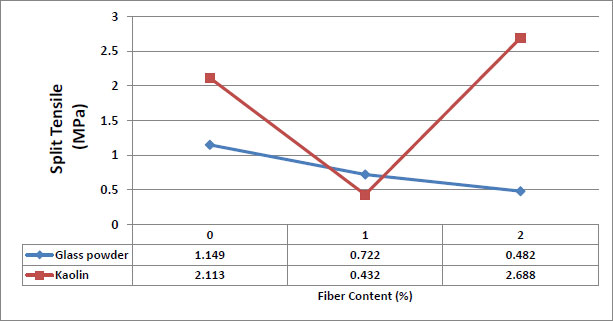
3.3. Water Absorption and Permeable Voids
The initial surface absorption, final water absorption, and permeable voids are presented in Fig. (8). The highest final water absorption of 6.58% was observed for sample 10G0K2F. In comparison, the least value was 3.9% observed for mix composition 0G10K0F. The ability of pervious concrete to absorb water is closely related to its larger pore size, which enhances connectivity and increases porosity. A comparison between samples 0G0K1F and 0G20K1F indicates that Kaolin reduced the water absorption of pervious concrete reinforced with the same sisal fiber content. The influence of sisal fiber content was evaluated using samples 20G10K0F and 20G10K2F; it was observed that the water absorption reduced when the fiber content was increased from 0% to 2%. This implies that the percolation of water through the concrete can be impaired with the presence of fiber. Sample 10G10K1F with final water absorption of 6.13% compared to 0G0K1F, the 6.29% also indicates reduced workability due to glass powder and Kaolin acting as supplementary cementitious material.
Similarly, increased glass powder content from 10% to 20% and kaolin content from 10% to 20% without sisal fiber was observed to reduce water absorption. This may be attributed to reduced porosity since water absorption is closely related to porosity. Furthermore, comparing the water absorption capacity of pervious concrete containing either glass powder or. Kaolin as observed in samples 0G10K0F (3.9%) and 10G0K0F (5.9%) indicates that incorporating Kaolin has more influence in reducing water absorption of the concrete. According to [45], previous research has identified that the presence of supplementary cementitious material reduces the porosity of concrete. One of the essential characteristics that should be exhibited by pervious concrete is the ability to
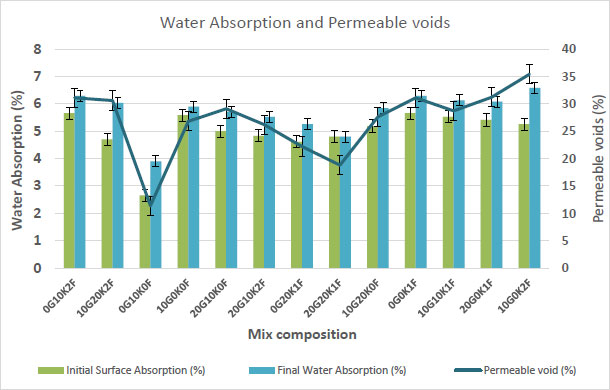

percolate water through its voids. Fig. (8) depicts the results of pervious concrete specimens' water absorption and permeable voids. The permeable void content is in the range of 11.4–35.4% for pervious cement concrete specimens. The highest permeable voids were recorded for 10G0K2F, and the lowest was sample 0G10K0F. The water absorption results were observed, and that of permeable voids followed a similar trend since the w/c ratio for the mix was the same. Therefore, the permeable void variations come from the cement paste, glass powder, Kaolin and sisal fiber content volume.
3.4. Correlation between the Properties of Fiber-reinforced Pervious Concrete
The relationship between compressive strength, water absorption and permeable voids of fiber-reinforced pervious concrete pavement was analysed and shown in Fig. (9). From the Figure, it can be seen that there was no clear relationship between compressive strength and water absorption of the fiber-reinforced pervious concrete pavement. According to [46], the strength of concrete cannot be evaluated by water absorption; hence, the compressive strength of fiber-reinforce pervious concrete did not depend upon water absorption.
Furthermore, it can be seen that a linear correlation exists between the permeable voids and water absorption. This linear correlation is indicated by the high correlation coefficient of 0.9639, indicating that the water absorption significantly influences the permeable void. The resulting fitting equations for the correlations are shown in Equations 6 and 7, respectively.


Where Fc is the compressive strength, w is the water absorption and Pv is the permeable voids.
3.5. Cost-Benefit Analysis
In the cost-benefit analysis of this study, the glass powder material, being a waste, has no cost value. However, in preparing the waste material to be reusable, the cost incurred in transporting, crushing, and sieving to the required particle sizes was ₦2.00 per kg. This cost was used for the cost-benefit analysis. Using the mixture design in Table 2, the cost of the concrete mixture was calculated using the unit cost of materials given in Table 3. The cost was obtained from local suppliers, which is the prevailing cost at the time of the research. In addition, Microsoft Excel was used to compute the corresponding costs of each mixture systematically, and is presented in Table 4.
S/N | Material | Cost |
---|---|---|
1 | Cement | 15 |
2 | Coarse aggregate (Granite) | 7 |
3 | Sisal fiber | 35 |
4 | Waste glass powder | 2 |
5 | Water | 0.05 |
6 | Kaolin | 1.5 |
7 | HRWA | 1.2 |
Mix | Glass Powder (₦) | Kaolin (₦) |
Cement (₦) |
Fiber (₦) |
CA (₦) |
Water (₦) |
HRWRA (₦) |
Total (₦) |
Cost Saving (%) |
---|---|---|---|---|---|---|---|---|---|
0G10K2F | 0.00 | 63.00 | 5,670.00 | 1,481.76 | 10,878.00 | 6.72 | 10.08 | 18,109.56 | 0 |
10G20K2F | 84.00 | 126.00 | 4,410.00 | 1,481.76 | 10,878.00 | 6.72 | 10.08 | 16,996.56 | 5.24 |
0G10K0F | 0.00 | 63.00 | 5,670.00 | 0.00 | 10,878.00 | 6.72 | 10.08 | 16,627.8 | 7.29 |
10G0K0F | 84.00 | 0.00 | 5,670.00 | 0.00 | 10,878.00 | 6.72 | 10.08 | 16,648.8 | 7.17 |
20G10K0F | 168.00 | 63.00 | 4,410.00 | 0.00 | 10,878.00 | 6.72 | 10.08 | 15,535.8 | 13.38 |
20G10K2F | 168.00 | 63.00 | 4,410.00 | 1,481.76 | 10,878.00 | 6.72 | 10.08 | 17,017.56 | 5.12 |
0G20K1F | 0.00 | 126.00 | 5,040.00 | 740.88 | 10,878.00 | 6.72 | 10.08 | 16,801.68 | 6.32 |
20G20K1F | 168.00 | 126.00 | 3,780.00 | 740.88 | 10,878.00 | 6.72 | 10.08 | 15,709.68 | 12.41 |
10G20K0F | 84.00 | 126.00 | 4,410.00 | 0.00 | 10,878.00 | 6.72 | 10.08 | 15,514.8 | 13.50 |
0G0K1F | 0.00 | 0.00 | 6,300.00 | 740.88 | 10,878.00 | 6.72 | 10.08 | 17,935.68 | 0.00 |
10G10K1F | 84.00 | 63.00 | 5,040.00 | 740.88 | 10,878.00 | 6.72 | 10.08 | 16,822.68 | 6.21 |
20G0K1F | 168.00 | 0.00 | 5,040.00 | 740.88 | 10,878.00 | 6.72 | 10.08 | 16,843.68 | 6.09 |
10G0K2F | 84.00 | 0.00 | 5,670.00 | 1,481.76 | 10,878.00 | 6.72 | 10.08 | 18,130.56 | 0 |
It was observed that both glass powder and kaolin cause significant changes in the total cost of concrete. The highest cost saving of 13.50% was observed in the mixture containing 10% glass powder, 20% kaolin, and 0% fiber. Still, since the mixture of 10G10K1F can be used for structural works (its compressive strength is within the ACI specification), the saving made was 6.21%.
CONCLUSION
This study investigates the effects of glass powder and Kaolin on the properties of pervious concrete. Based on the results, the following conclusions have been drawn:
(i) Using glass powder and Kaolin as supplementary cementitious materials in fiber-reinforced pervious concrete indicates that the strength resulting from Kaolin is higher than glass powder.
(ii) The results indicate that adding 10% of Kaolin as a binary blend in pervious concrete is more effective on compressive strength than adding 10% glass powder.
(iii) The results indicate that Kaolin and sisal fiber can positively influence the tensile behaviour of pervious concrete. However, increasing kaolin content beyond 10% is not advisable for improved split tensile strength.
(iv) When compared with Kaolin, the water absorption capacity of pervious concrete containing glass powder will allow more water percolation.
(v) The water absorption capacity is reduced with the presence of sisal fiber. For future studies, further experiments relating to water properties for a more comprehensive understanding of the material's behavior and performance under different water-related conditions are recommended.
(vi) The permeable void content is in the range of 11.4–35.4% for pervious cement concrete specimens. This variation comes from the volume of cement paste, glass powder, kaolin, and sisal fiber.
ABBREVIATIONS
EPA | Environmental Protection Agency |
SCMs | Supplementary Cementitious Materials |
CONSENT FOR PUBLICATION
Not applicable.
AVAILABILITY OF DATA AND MATERIALS
The data and supportive information are available within the article.
FUNDING
None.
CONFLICT OF INTEREST
The authors declare no conflict of interest, financial or otherwise.
ACKNOWLEDGEMENTS
The authors would like to acknowledge Afe Babalola University, Ado Ekiti, Nigeria, for its support in promoting research output.