All published articles of this journal are available on ScienceDirect.
Effect of Mixed Variation of Magnesium Carbonate and Bottom Ash for Stabilization of Subgrade Soils
Abstract
Introduction
Soft clay causes various problems in construction, especially in road construction. A road in Gunung Kidul Regency, D. I. Yogyakarta, is often damaged due to the clay soil. Such road damage can be prevented by stabilizing the subgrade layer using cement, lime, bitumen, fly ash-bottom ash (FABA), or other chemicals. Bottom ash is a solid waste generated from coal combustion in coal-fired power plants. It can be used as an additive in various construction applications, including soil stabilization. Magnesium carbonate is an alkaline additive used for stabilization. It is a fine powder containing alkaline chemical compounds formed through the reaction between magnesium salt and sodium bicarbonate.
Methods
This research investigated the effect of variations in the magnesium carbonate and bottom ash mixture for subgrade stabilization on soil properties such as the bearing capacity and the development of roads in Gunung Kidul Regency. Laboratory testing was conducted with a centralized mixing method using mixtures of two materials: 0% or 1.5% magnesium carbonate (MgCO3) and 0-15% bottom ash with 5% increments based on the dry weight of the soil. The testing parameters included the California bearing ratio (CBR) and the swelling potential.
Results
The results showed a significant effect of the mixes on increasing the CBR of the subgrade to comply with the requirement of CBR > 6% with CBR unsoaked of 5.17% to 47.17% and CBR soaked of 3.49% to 21.20%.
1. INTRODUCTION
The plastic nature of soft clay is due to the presence of clay minerals such as montmorillonite and smectite in its composition. These clay minerals can absorb water into their structure through ionic bonds, resulting in changes in the overall soil volume [1]. The volume changes that occur in clay soils can cause various problems in construction and other civil engineering applications. For example, when soft clay is used as a subgrade, extreme volume changes can cause shifting and deformation, damaging the road surface. To mitigate these problems, the subgrade can be stabilized by adding chemical stabilization agents that strengthen the subgrade soil. Subgrade stabilization is especially necessary in areas with high clay content, especially in areas that experience frequent heavy rainfall and/or high elevated groundwater levels. The stabilization process is performed directly on the original soil without the need to remove or replace it. The main objective of stabilization is to increase the life of pavements, embankments, curbs, shoulders, and roadbeds while significantly improving the technical properties of the soil, including the reduction of plastic deformation [2]. The soil stabilization approach should be tailored to the dominant clay mineral type, considering the differences between expansive clays (such as smectite) and non-expansive clays (such as kaolinite). Kaolinite is one of the most commonly encountered clay types worldwide and has been the subject of extensive research in stabilization experiments, providing a solid basis for evaluating alternative stabilization materials [3]. Soil stabilization is often achieved by adding cement, lime, bitumen, fly ash-bottom ash (FABA), or chemicals, such as magnesium carbonate (MgCO3).
Magnesium carbonate is a fine powder that contains alkaline compounds. It is formed by the reaction between magnesium salt and sodium bicarbonate and is used as a soil stabilization mixture [4]. Soil stabilization requires assessing its technical and environmental performance in a range of conditions, including soil type, soil water content, and binder content [5]. This is because magnesium carbonate has a high binding ability. Magnesium carbonate can accelerate crystal formation during the soil hydration process, making the soil layer impermeable. Another material that can be used for soil stabilization is bottom ash. Bottom ash is a type of solid waste produced from the process of burning coal in coal-fired power plants [6]. Bottom ash consists of solid particles, such as ash grains, burned coal crust, and other minerals. Bottom ash has a coarse texture and is generally gray to dark brown in color. As a solid waste, bottom ash must be properly managed in accordance with applicable environmental regulations and standards. In previous research, the use of bottom ash as the use of bottom ash as a stabilization material is still rarely used. Bottom ash is used as an additive material for stabilizing the soil. Stabilizing the soil by adding bottom ash improves soil strength and reduces swelling and shrinking [7, 8]. Coal bottom ash is an interesting material for soil stabilization. In another research, an increase in the California bearing ratio (CBR) of the soil with a large addition of bottom ash with longer curing and the increase in CBR value is affected by the chemical composition of pozzolanic bottom ash, which is able to fill soil voids that initially contain air and water and can provide bonds between soil grains which cause the soil to become more compact [9].
This study aimed to examine the effect of variations in the mixture of magnesium carbonate and bottom ash for the stabilization of the road subgrade in the Gunung Kidul area. Mixtures with defined ratios of magnesium carbonate and bottom ash were created. Then, physical and mechanical soil tests were conducted to determine the optimal mixture concentration to improve the stability of the road subgrade in the Gunung Kidul area. The use of magnesium carbonate and bottom ash is expected to be more environmentally sustainable and become an alternative to subgrade stabilization, which has often used additives such as cement, which is not good for the environment.
2. MATERIALS AND METHODS
2.1. Research Location
The soil samples ware taken from the Karangmojo-Semanu Road area, Gunung Kidul, D. I. Yogyakarta. The research was conducted at the Soil Mechanics Laboratory, Department of Civil and Environmental Engineering, Gadjah Mada University.
2.2. Material
1. The soil samples used in this research were collected from Karangmojo - Semanu Road, Gunung Kidul Regency, D. I. Yogyakarta. The samples were taken from disturbed conditions at a depth of + 50 - 100 cm from the top soil surface using a hoe. The soil samples were dried utilizing sunlight. Then, the soil samples were pounded with a wooden hammer to get the soil to pass a No. 4 sieve.
2. Magnesium carbonate is an additive used for soil stabilization and compaction. This material is a fine powder containing alkaline chemical compounds that can be obtained from chemical stores. Magnesium carbonate (MgCO3) is formed through a chemical reaction between magnesium salt and sodium bicarbonate.
(1)
Magnesium carbonate can be used in mixtures for soil stabilization. This is because it has a high binding ability. During the soil hydration process, magnesium carbonate can accelerate the formation of crystals, making the soil layer impermeable to water.
3. The bottom ash used in this study came from the combustion of coal from PT Pupuk Sriwijaya (PUSRI) Palembang and passed through a no.100 sieve. According to [10] concerning the Implementation of Environmental Protection and Management, bottom ash is a waste from burning coal that remains at the bottom of the furnace. While it is considered non-hazardous (non-B3), it must still be managed to meet all relevant standards and technical requirements. In the context of clay soil stabilization, bottom ash can be used as a filler [7]. The function of bottom ash in clay soil stabilization is to fill the gaps between clay soil particles, thereby increasing the density and stability of the soil. Using bottom ash as filler, clay soil can become denser and sturdier. The chemical composition of bottom ash, which was analyzed using energy-dispersive X-ray fluorescence (ED-XRF), is reported in Table 1. The table shows that the main component was SiO2 with a value of 62.73%; other components included Al2O3, Fe2O3, and CaO are 23.80%, 11.00%, and 12.70% respectively (Figs. 1-3).
Components | SiO2 | Al2O3 | Fe2O3 | CaO | SO3 | K2O | TiO2 | SrO | TiO2 | MnO | BaO |
---|---|---|---|---|---|---|---|---|---|---|---|
Bottom Ash | 62.73 | 17.52 | 13.22 | 3.45 | - | 1.17 | 1.25 | 0.15 | 0.11 | 0.16 | - |
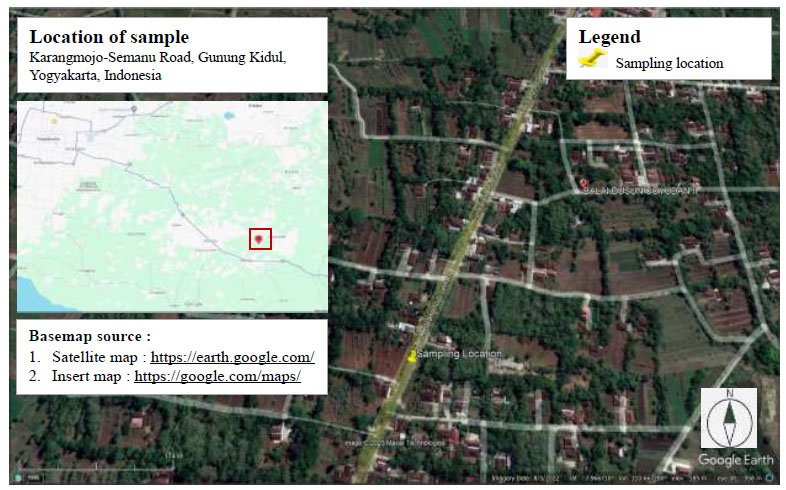
Soil sampling location near Karangmojo – Semanu road, Gunung Kidul, D. I. Yogyakarta.
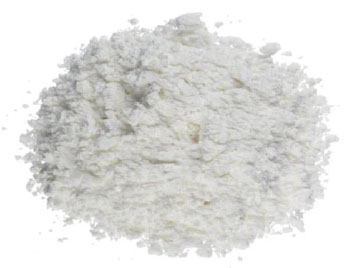
Magnesium carbonate.
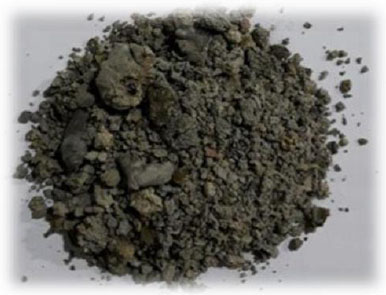
Bottom ssh.
Mixing Design | Magnesium Carbonate (MgCO3) | Bottom Ash |
---|---|---|
Base soil | 0% | 0% |
BA5 | 0% | 5% |
MG15 | 1.5% | 0% |
MG15BA5 | 1.5% | 5% |
MG15BA10 | 1.5% | 10% |
MG15BA15 | 1.5% | 15% |
2.3. Physical and Mechanical Property Tests
1. Water content (ASTM D 2216-98)
2. Specific gravity (Gs) (ASTM D 854-02)
3. Atterberg limit (ASTM D 4318-17e1 and D 427-98)
4. Standard sieve tool (ASTM D 421-58) and hydrometer (ASTM D 422-63)
5. Proctor standard (ASTM D 698-00a)
6. California bearing ratio (CBR) (ASTM D 1883-99)
7. Unconfined compressive strength (UCS) (ASTM D 2166)
8. Swelling potential (ASTM D 4546-03)
2.4. Mixing Design
This experimental research uses magnesium carbonate mixed with bottom ash to stabilize soft clay soil. The study focused on one factor, namely the effect of the addition of magnesium carbonate and bottom ash on soil stabilization. The application of 1.5% magnesium carbonate is based on research that has been done before [4]. The mixtures tested in this study are summarized in Table 2.
3. RESULTS AND DISCUSSION
We analyze the data obtained from the tests in the form of index properties and mechanical soil data. Specifically, we analyze the data obtained from CBR testing to determine the optimum design in accordance with the minimum requirement of CBR > 6 for the subgrade.
3.1. Index Properties
The soil characterization was carried out in the laboratory. The results reported in Table 3 indicated that the soil was soft clay with a water content of 23.804% and a specific gravity of 2.492. The liquid limit was 65.75%, the plastic limit was 36.19%, the shrinkage limit was 10.05%, and the plasticity index was 28.56%. The soil grain analysis and the hydrometer test revealed that the soil contained #200 fine grains (92.008%). Based on the soil, the American Association of State Highway and Transportation Officials (AASHTO), A-7-5 clay and a moderate to poor subgrade soil. According to the Unified Soil Classification System (USCS), the soil sample was an organic loam with medium to high plasticity (OH). Based on these characteristics, this soil type is unfavorable for use as a subgrade material.
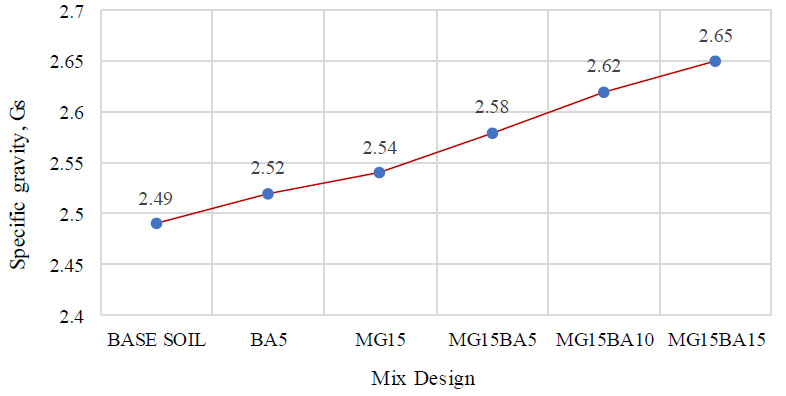
Specific gravity results for clay stabilization with magnesium carbonate and bottom ash.
Parameters | Test Result |
---|---|
Water content [%] | 23.80 |
Specific gravity (Gs) | 2.49 |
Liquid limit (LL) [%] | 65.75 |
Plastic limit (PL) [%] | 36.19 |
Shrinkage limit (SL) [%] | 10.05 |
Plasticity lndex (PI) [%] | 28.56 |
Percentage finer #200 [%] | 92.01 |
Clay fraction (<0.002 mm) [%] | 24.25 |
Activity (PI/C) | 1.16 |
Classification (AASHTO/USCS) | A-7-5/OH |
Max dry density (MDD) [gr/cm3] | 1.29 |
Optimum moisture content (OMC) [%] | 30.7 |
CBR soaked [%] | 5.16 |
CBR unsoaked [%] | 3.49 |
Swelling Potential [%] | 2.35 |
3.2. Specific Gravity
The specific gravity values of the base soil sample and the mixes are shown in Fig. (4). The base soil had a specific gravity of 2.49. The graph shows that the specific gravity experienced an upward trend with the addition of magnesium carbonate and bottom ash. Adding 1.5% magnesium carbonate and 0% bottom ash (MG15BA0) results in a specific gravity of 2.54, while adding 0% magnesium carbonate and 5% bottom ash (MG0BA5) results in a specific gravity of 2.52. The highest specific gravity was obtained with sample MG15BA15 at 2.65. These results demonstrate that the addition of 1.5% magnesium carbonate and 5%, 10%, and 15% bottom ash increases the specific gravity of the soil.
3.3. Atterberg Limit
The Atterberg limit test revealed that the liquid limit of the soil decreased with the addition of magnesium carbonate and bottom ash. The sample with 1.5% magnesium carbonate and 15% bottom ash (MG15BA15) achieved the lowest liquid limit at 59.75%. The addition of 1.5% magnesium carbonate and 5%, 10%, and 15% bottom ash caused a significant decreasing trend in the plastic limit, with the lowest value of 33.76% in the MG15BA15 sample. The lowest plasticity index (PI) was also achieved by sample MG15BA15. This research is in agreement with that conducted by [7]. The Atterberg limit results are summarized in Fig. (5).
3.4. Density
The effect of blend variation on OMC (Optimum Moisture Content) values showed that the use of 1.5% magnesium carbonate and an increasing percentage of bottom ash used showed a regular downward trend in OMC values. However, the OMC value at the highest bottom ash percentage variation was 1.354% with sample MG15BA15. However, different results were shown for MDD (Maximum Dry Density) values; the results showed a decrease in MDD values as the percentage of bottom ash increased with an MDD value of 26.23%. This indicates that an increase in the optimum moisture content of the soil will occur when the percentage of bottom ash is added, and an increase in the optimum moisture content is always followed by a decrease in MDD (maximum dry density).
3.5. Unconfined Compressive Strength (UCS)
In the unconfined compressive strength test, the samples were formed using a mold with maximum density and mixed using the optimum moisture content determined from the Proctor test, which was previously conducted. The treatment was applied for one, three, and seven days. Fig. (6) shows that the UCS increased for soft clay stabilized using 1.5% magnesium carbonate and 5%, 10%, and 15% bottom ash. The highest UCS was achieved by the MG15BA15 sample. For the original soil sample, the initial UCS of 0.06 kg/cm2 increased to 0.09 kg/cm2 after one day of curing. The UCS increased again after seven days of curing to 0.28 kg/cm2. This trend shows that by increasing the curing age, the UCS. For the MG15BA10 sample, the UCS increased to 0.21 kg/cm2 after seven days of curing. Something similar was obtained [11] in his research on bottom ash in clay soil.
3.6. California Bearing Ratio (CBR)
CBR testing was conducted under two conditions: unsoaked and soaked. CBR testing in unsoaked conditions was carried out for one, three, and seven days, in soaked conditions, it was carried out for four days with the samples soaked for seven days before soaking. This test was conducted to determine the CBR, which is the ratio between the original and soil penetration loads. According to the Road Pavement Design Manual No.02/M/BM/2017 published by the Ministry of Public Works and Housing (PUPR), the minimum recommended CBR value for road subgrade is CBR > 6%. Fig. (7) shows that adding 1.5% magnesium and 5%, 10%, or 15% bottom ash significantly increased the CBR. Initially, the CBR of the base soil samples was 5.16% in unsoaked conditions and 3.49% in soaked conditions. These soils are unsuitable as base soils because their CBR is under 6%, with magnesium carbonate and different levels of bottom ash achieving higher CBR values. The highest CBR was achieved by sample MG15BA15 in both unsoaked conditions at 48.17% and soaked conditions at 21.20%. These results indicated that soil can be used as a subgrade material in accordance with the minimum requirement of CBR > 6%. This research is in agreement with that conducted [9].
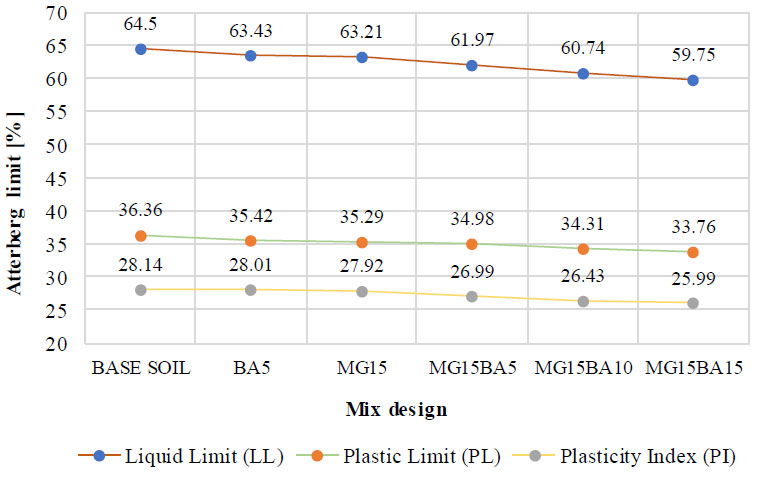
Atterberg limit results for clay stabilization with magnesium carbonate and bottom ash.
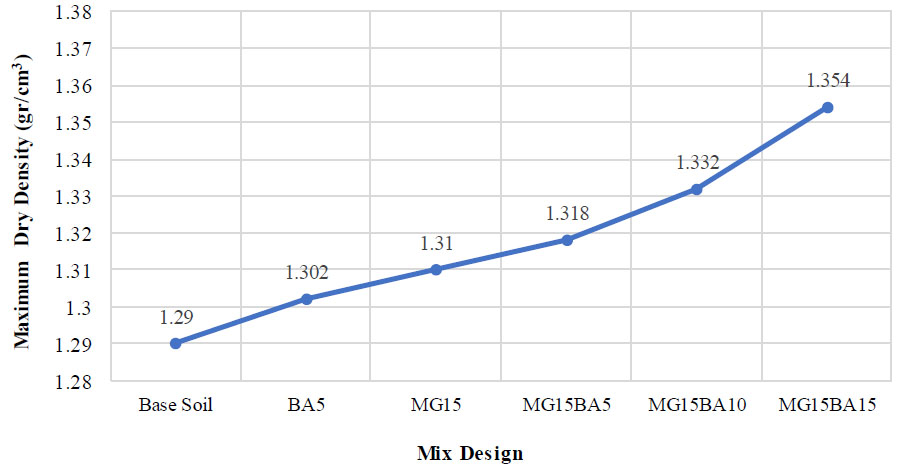
Maximum dry density (MDD) results in clay stabilization with magnesium carbonate and bottom ash.
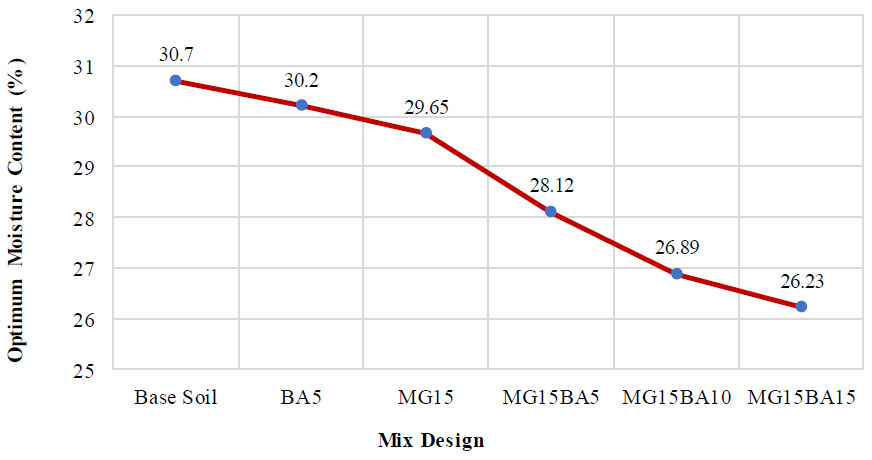
Optimum moisture content (OMC) results in clay stabilization with magnesium carbonate and bottom ash.
3.7. Swelling Potential
Swelling potential tests are conducted to determine the percentage change in height during soaking relative to the original test object. This study conducted swelling potential tests using samples soaked for four days and buried for seven days. After mixing the sample with magnesium carbonate and bottom ash, the results showed a decreasing trend in the clay soil’s height. The swelling potential of the base soil was 1.59% after one day of soaking and 2.35% after four days. Sample MG15BA15 had significantly lower swelling potential, with one day of soaking amounting to 0.005% and four days of soaking amounting to 0.05%. These results indicated that adding 1.5% magnesium carbonate and 5%, 10%, or 15% bottom ash for soil stabilization can reduce soil swelling (Figs. 8-10) [12-17].
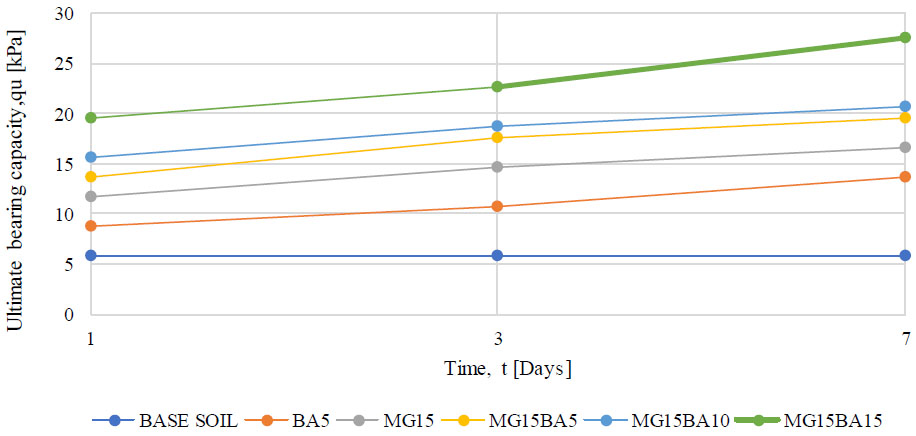
UCS results for clay stabilization with magnesium carbonate and bottom ash.
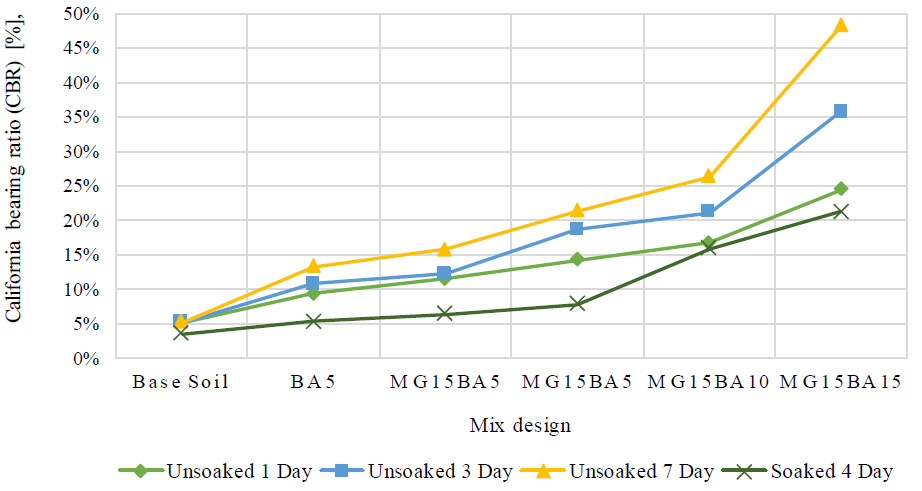
CBR results for clay stabilization with magnesium carbonate and bottom ash.
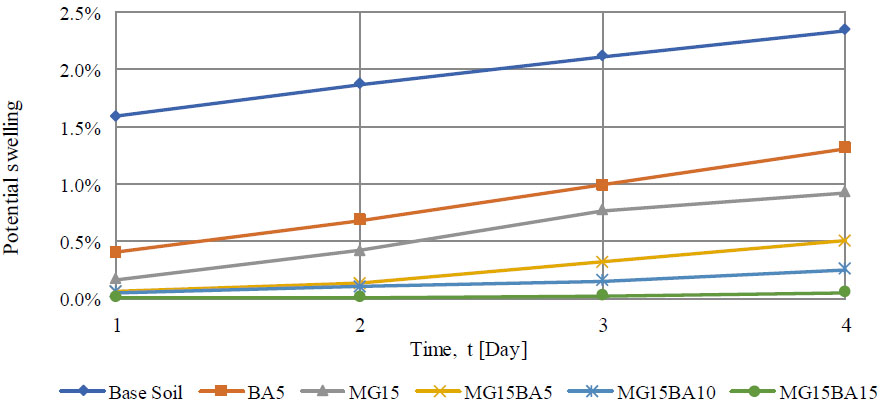
Potential swelling results from clay stabilization with magnesium carbonate and bottom ash.
CONCLUSION
This research investigated the feasibility of using magnesium carbonate and bottom ash for soft clay stabilization. The results of the physical property tests showed that magnesium carbonate and bottom ash could improve soil properties such as the specific gravity and the Atterberg limit. The test results also showed an increasing trend along with the addition of magnesium carbonate and bottom ash. The mechanical properties test results showed that the addition of magnesium carbonate and bottom ash increased the strength of the subgrade, especially the California Bearing Ratio (CBR), with the highest value of 47.17%, and decreased the potential swelling value of the soil to 0.005%. As a result, the subgrade exceeds the requirements of the road subgrade, which is CBR > 6%. Therefore, this study indicated that magnesium carbonate and bottom ash can be used as subgrade stabilization materials for soft clay soil. This research can also still be developed with the addition of bottom ash percentage to determine the maximum percentage addition that can be used by considering environmental impacts.
LIST OF ABBREVIATIONS
AASHTO | = Association of State Highway and Transportation Officials |
BA | = Bottom Ash |
CBR | = California Bearing Ratio |
FABA | = Fly Ash – Bottom Ash |
LL | = Liquid Limit |
MDD | = Maximum Dry Density |
OMC | = Optimum Moisture Content |
PL | = Plastic limit |
PI | = Plasticity Index |
SL | = Shrinkage Limit |
USCS | = Unified Soil Classification System |
AVAILABILITY OF DATA AND MATERIALS
The data and supportive information is available within the article.