All published articles of this journal are available on ScienceDirect.
Effect of Magnetized Water on Partially Replaced Aggregate with Silica Sand in Concrete
Abstract
Introduction
The study aimed to investigate the impact of “Magnetized water” on the mechanical properties of M30-grade concrete partially replaced by silica sand.
Methods
Two different grades of silica sand were utilized as fine aggregate, with 25% and 50% replacement rates. The concrete was prepared using a W/C ratio of 0.41 and a specific amount of superplasticizer. The water was magnetized using a 10000 Gauss magnetic fluid enhancer, resulting in “magnetized water.”
Results
Magnetization resulted in a 10% improvement in the workmanship of the concrete, as well as a 5% reduction in water usage with additive dosage.
Conclusion
The compressive strength of concrete with silica sand was 10% higher than that of conventional concrete, and the addition of magnetized water further increased to 20% of compressive strength and the slump increased by 10%.
1. INTRODUCTION
The swift global population growth is leading to an increase in water usage. The agricultural industry, which stands at the top in terms of water consumption, utilizes approximately 70 to 75% of the water supply annually. The industrial sector consumes about 20% more water than the agricultural sector. Concrete production technology relies heavily on water as it uses up to 1 billion tonnes of water per year [1]. The type of water utilized significantly influences the quality of the concrete mix. While potable water is the preferred choice, it is not always feasible, and therefore “magnetized water” is considered the best substitute [2-5].
Magnetized water is the water that has been exposed to a powerful magnetic field, which alters some of its characteristics. The chemical composition of the water remains the same, and the changes in properties are usually not observed on a macroscopic level. At the nanoscale, water is not uniformly distributed and can exist as small clusters or bundles, depending on the temperature, applied pressure, and pre-existing force. The density of water can be influenced by two main forces: the hydrogen bond and the “Van der Waal's force,” which involves the disruption of other intermolecular forces and molecular repulsion. The magnetic effect of this force can persist in a water sample for up to three hours [6].
The “PERMAG N406” is a magnetic device that produces a strong magnetic field. Water can be moved through the device at a decent pace either by gravity or mechanical pumping. The magnetic field generated by this device causes the clusters present in water to break apart and reduces the bond angle between the water molecules. This process helps with the hydration of cement in concrete [7] by breaking down large water clusters into smaller ones or single water molecules.
Silica sand can be a beneficial addition to concrete when it is used as a substitute for fine aggregate. Previous research studies have explored the possibility of reducing the amount of cement and water by adding magnetic water to the mixture. In this study, the water-cement ratio and cement content are maintained constant to compare the concrete made with silica sand and magnetized water. The concrete made with no silica sand and normal water, as well as the concrete made with silica sand and normal water, is also compared [8]. The results demonstrated that there was a reduction in water and admixture in various mixes. Concrete made with magnetized water had a favourable slump value with less water and admixture [9]. The objective of this study was to explore the advantages and disadvantages of blending silica sand and magnetized water at different ratios in concrete mixtures [10].
2. RESEARCH SIGNIFICANCE
The study consists of two primary concepts. Firstly, the researchers have replaced river sand with silica sand in the experiments. Secondly, magnetized water is used instead of tap water to mix the concrete. The key objective of this study is to investigate the impact of using both “Magnetized water” and “Silica sand” on M30-grade concrete. The main goals of this research paper are to reduce water consumption, improve the workability of fresh concrete, enhance the mechanical properties of concrete, and optimize the dosage of superplasticizer. This initiative plays a significant role in combating global warming and decreasing industrial-scale pollution, while also contributing to the conservation of natural resources. The electricity required for magnetization is minimal, and incorporating industry by-product silica sand into concrete reduces the cost per cubic meter of concrete by 10%.
3. METHOD (EXPERIMENTAL PROCEDURE)
3.1. Description of Materials
3.1.1. Cement
For the research, Ordinary Portland Cement (OPC) of 43-grade, which adhered to the IS: 8112-1989 standard, was utilized. The cement utilized was of high quality, without any lumps, and had a balanced chemical composition. The specific gravity of the cement was 3.12, the normal consistency was 31%, and the initial setting time was 50 minutes, while the final setting time was 176 minutes.
3.1.2. Coarse Aggregates
The materials used in the research included crushed angular aggregates with diameters both above and below 20 mm. The coarse aggregates utilized were free from any organic matter or other waste materials and were dry and moisture-free. The specific gravity of the coarse aggregates was 2.66.
3.1.3. Fine Aggregates
For the research, good-grade river sand was selected, which was free from salt and biological debris. The fine aggregate used had a specific gravity of 2.606 and a fineness modulus of 4.57%. The fine aggregate complied with Zone 1 requirements.
3.1.4. Silica Sand
The study used two different grades of silica sand, namely (30-40) grade and (50-60) grade. The specific gravity of the silica sand was 2.653 for the (30-40) grade and 2.456 for the (50-60) grade. The silica sand was graded according to the standards set by the American Foundry Society (AFS) [6, 11], which is the organization responsible for procuring and grading the raw material. The silica sand supplied to both the glass and foundry industries was almost identical [12], but the glass sector requires higher-quality silica sand than the foundry sector [13]. The silica sand used in foundries typically contains more silt than the one used in the glass industry [14, 15]. Fig. (1) illustrates the two grades of silica sand used in the study.
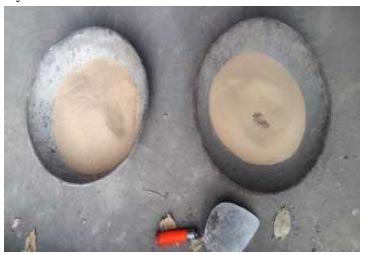
3.1.5. Magnetized Water
The magnetic device PERMAG N406 was attached to a hose pipe to create magnetized water by running regular tap water through it. The device produces a strong magnetic field between 9500 Gauss and 10000 Gauss (1 Tesla) while the water flows through it. To enhance magnetization [16], the magnetised water is recirculated for about 30 to 45 minutes. However, for simplicity and optimization purposes, water cycling through the device was not employed in this investigation. A pH value test and total hardness test were conducted on the magnetized water [17, 18], and their results are presented in Table 1. Fig. (2) illustrates the magnetic device used in this study.
S.No. | Name of the Test | Normal Water | Magnetized Water |
---|---|---|---|
1 | pH value test | 6.98 | 7.28 |
2 | Total hardness | 54 mg/l | 38 mg/l |
The magnetic device is not only used in the construction industry but also in other sectors, including agriculture, vehicles, and refrigeration. This gadget helps to eliminate hardness and chlorine from water, which in turn prevents the corrosion of plumbing fittings and reinforcement in concrete structures [11]. PERMAG is made of high-quality rare-earth magnets and strontium ferrite permanent magnets that are arranged in a particular pattern to ensure a high perpendicular magnetic flux field to the application region. The arrangement and strength of magnets, as well as the velocity of the fluid, cause molecular structural modifications in the water's minerals such as calcium and magnesium [19]. To deliver optimal results, the magnetic field is effectively insulated to prevent stray field emission.
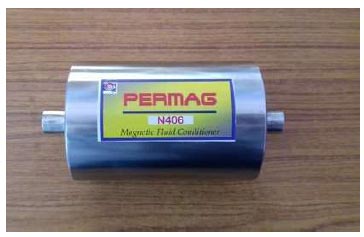
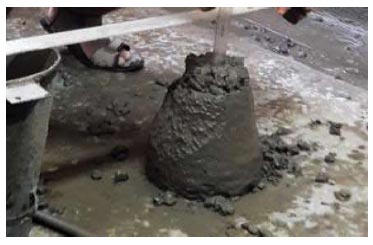
3.1.6. Slump Test
To measure slump loss, a slump cone with a top diameter of 100 mm, a bottom diameter of 200 mm, and a height of 300 mm is used. The concrete mix is poured into the slump cone in three stages and is tamped more than 25 times using a round-edged tamping rod for each layer. After filling the slump cone, the surface is leveled, and the cone is gently removed. If the obtained slump and its value are correct, the mix is considered acceptable. In case the obtained slump is zero, the test is repeated after optimizing the water-cement (W/C) ratio. The slump value is illustrated in Figs. (3 and 4).
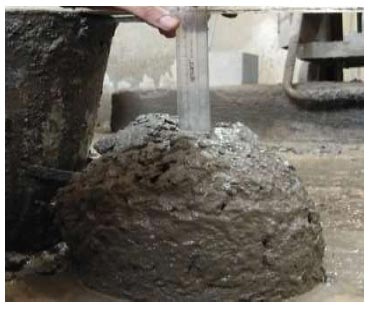
4. ANALYTICAL PROCEDURE
4.1. Data
- Grade of concrete: M30
- W/C ratio: 0.41
- Cement: OPC 43 grade
- Admixture: Dynamon PC 803PP
- Admixture type: Water reducing and workability enhancing
- Specific gravity of cement: 3.12
- Specific gravity of river sand: 2.606
- Specific gravity of coarse aggregate: 2.66
- Specific gravity of Silica sand (30-40): 2.653
- Specific gravity of Silica sand (50-60): 2.646
- Target Strength: 38.25 N/mm2
4.2. Mix Proportion and Mix Design (per m3 Concrete)
For this research, silica sand in the (30-40) and (50-60) grades was employed. Fine aggregates were substituted with graded silica sand by 0%, 25%, 50%, and 75%, respectively. The mixes in Table 2 include admixture dosages of 1%, 1.1%, and 1.2% (percentage with respect to weight of cement). As indicated in Figs. (5 and 6), the concrete is prepared to achieve the desired strength in accordance with IS: 10262 - 2019.
Mix No. | W/C Ratio | Cement (kg/m3) |
Silica Sand (30-40) (kg/m3) | Silica Sand (50-60) (kg/m3) | Fine Aggregates (kg/m3) | Coarse Aggregates (kg/m3) |
---|---|---|---|---|---|---|
1 | 0.41 | 400 | 0 | 0 | 697 | 1152 |
2 | 0.41 | 400 | 177 | 0 | 523 | 1151 |
3 | 0.41 | 400 | 0 | 177 | 523 | 1151 |
4 | 0.41 | 400 | 355 | 0 | 348 | 1151 |
5 | 0.41 | 400 | 0 | 354 | 348 | 1151 |
6 | 0.41 | 400 | 532 | 0 | 175 | 1151 |
7 | 0.41 | 400 | 0 | 531 | 175 | 1151 |
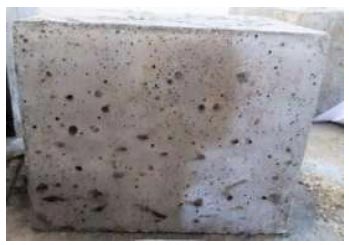
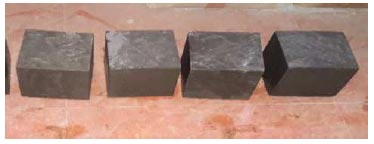
5. RESULTS AND DISCUSSION
The following mix proportions were utilized: M30 with a W/C ratio of 0.41, Mix-1 with 0% silica sand as a reference, Mix-2 with 25% silica sand (30-40), Mix-3 with 25% silica sand (50-60), Mix-4 with 50% silica sand (30-40), and Mix-5 with 50% silica sand (50-60). The cubes, cylinders, and beams experienced compressive strength, split tensile strength, and flexural strength tests at 7 and 28 days of age.
5.1. Slump Test Results
The mix with the lowest slump value was Mix 1, which was prepared using tap water and 0% silica sand, resulting in a slump value of 90 mm. The mix with the highest slump value was Mix 2, which was made using magnetized water and 25% silica sand (30-40 grade), resulting in a slump value of 120 mm [20]. Table 3 presents the results of all other tests conducted. It was observed that the use of magnetic water for the concrete mix led to a 5% increase in the slump value [21, 22]. During the mixing phase of the concrete, several issues arose when it was altered by 75%. These issues included poor workability, segregation, the formation of pores on the concrete cubes, and a decrease in the weight of the concrete cubes. Since the quality of the concrete cubes was not up to the mark, the test result for a replacement rate of 75% had to be rejected in order to proceed with the investigation.
5.2. Compression Test Results
Magnetized water had some positive effects on the concrete, according to the results of the 7-day compressive strength test. When magnetized water was utilised instead of potable water, the 7-day compressive strength of 25% substituted concrete significantly increased from 32.1 N/mm2 to 38.8 N/mm2 [18]. Strength increases were also aided by the use of silica sand [23-29]. In cases of 100% and 50% replacement of silica sand the percentage improvement in strength is lower than 25% replacement. Compressive strength, split tensile strength, and flexural strength all exhibit a similar pattern as studied in previous papers [30, 31]. It is evident from the results of the 28-day compressive strength test that magnetized water provides better strength as compared to conventional concrete. The silica sand concrete (30–40 grade) prepared with magnetised water had the highest 28-day compressive strength [32]. When 50% Silica sand (30-40 grade) concrete was mixed with magnetised water, the compressive strength increased from 50.82 N/mm2 to 57.1 N/mm2 [33, 34]. Concrete made of silica sand exhibited a strength increase of 5%, and when silica sand and magnetised water were combined the strength increased by 10 to 15% [35]. Concrete's ability to resist cracking can be considerably increased when magnetic water is used [36]. Table 4 displays the complete outcomes. The results of a compression test are shown in Fig. (7).
S.No. | Percentage Replacement | Slump Value (Normal Tap Water) in (mm) |
Slump Value (Magnetic Water) in (mm) |
Percentage Water Quantity Saved for Achieving the Required Slump |
---|---|---|---|---|
1 | 0% | 90 | 100 | 0 |
2 | 25% (30-40) | 100 | 120 | 11.1 |
3 | 25% (50-60) | 95 | 102 | 5.6 |
4 | 50% (30-40) | 105 | 115 | 6.5 |
5 | 50% (50-60) | 98 | 108 | 7.8 |
S.No | Percentage Replacement | Compressive Strength (Normal Water) in (N/mm2) | Compressive Strength (Magnetic Water) in (N/mm2) | ||
---|---|---|---|---|---|
7 days | 28 days | 7 days | 28 days | ||
1 | 0% | 28.20 | 38.26 | 28.70 | 46.47 |
2 | 25% (30-40) | 32.10 | 44.80 | 38.80 | 47.10 |
3 | 25% (50-60) | 33.14 | 41.60 | 39.16 | 52.10 |
4 | 50% (30-40) | 40.84 | 50.82 | 42.35 | 57.10 |
5 | 50% (50-60) | 35.12 | 41.88 | 37.20 | 46.32 |
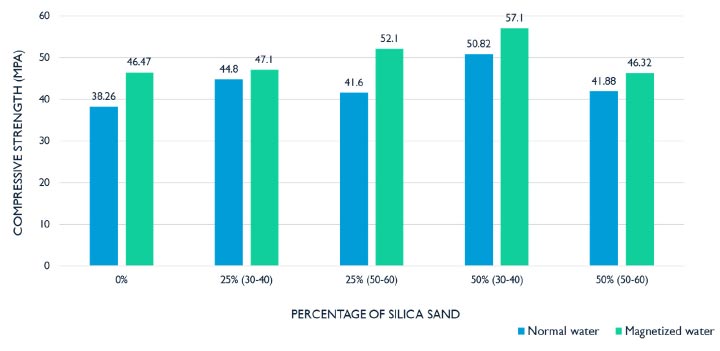
S.No | Percentage Replacement | Split Tensile Strength (Normal Water) in (N/mm2) | Split Tensile Strength (Magnetic Water) in (N/mm2) |
||
---|---|---|---|---|---|
7 days | 28 days | 7 days | 28 days | ||
1 | 0% | 2.34 | 3.24 | 2.56 | 3.54 |
2 | 25% (30-40) | 2.38 | 3.87 | 2.44 | 3.91 |
3 | 25% (50-60) | 2.68 | 3.73 | 2.85 | 4.12 |
4 | 50% (30-40) | 3.12 | 4.05 | 3.27 | 4.67 |
5 | 50% (50-60) | 3.24 | 4.17 | 3.36 | 4.29 |
5.3. Split Tension Test Results
According to concrete prepared with magnetized water and 50% silica sand (30–40 grade), the split tensile strength was 4.67 N/mm2 [21, 37]. With the usage of magnetized water, the split tensile strength of the concrete is marginally higher than that of concrete prepared with potable water. However, silica sand increased the concrete's split tensile strength [38]. Table 5 displays the test results. Split tensile test results are shown in Fig. (8).
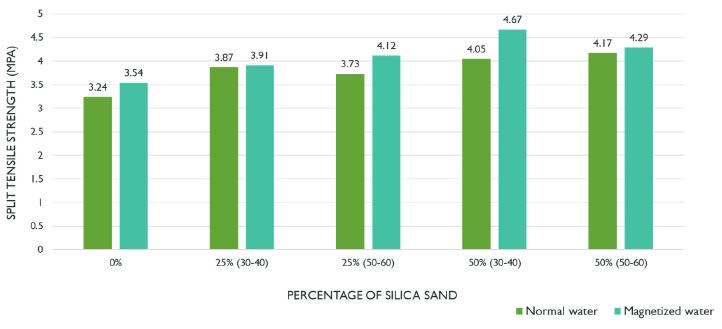
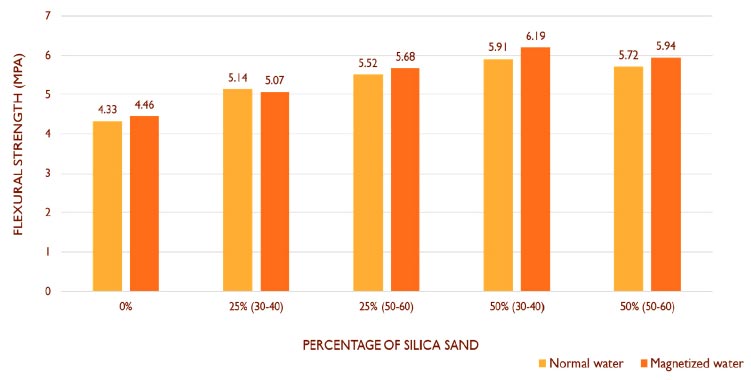
S.No | Percentage Replacement | Flexural Strength (Normal Water) in (N/mm2) |
Flexural Strength (Magnetic Water) in (N/mm2) |
||
---|---|---|---|---|---|
7 days | 28 days | 7 days | 28 days | ||
1 | 0% | 3.17 | 4.33 | 3.41 | 4.46 |
2 | 25% (30-40) | 3.68 | 5.14 | 3.53 | 5.07 |
3 | 25% (50-60) | 4.03 | 5.52 | 4.06 | 5.68 |
4 | 50% (30-40) | 4.47 | 5.91 | 4.64 | 6.19 |
5 | 50% (50-60) | 4.23 | 5.72 | 4.36 | 5.94 |
5.4. Flexural Strength Test
The concrete made with magnetized water and 50% silica sand (30-40 grade) has the highest flexural strength, which is 6.27 N/mm2 [39, 40]. Table 6 displays the complete test results. Flexural strength findings are shown in Fig. (9).
5.5. Practical Applications
The utilization of magnetized water in concrete enhances its workability and slump, consequently reducing the water demand for concreting. This improvement in workability is particularly crucial in regions such as deserts and cold climates. The replacement of silica sand plays a significant role in increasing the slump and reducing the porosity of concrete, factors that adversely affect its strength and density (Anexxure- Supp).
CONCLUSION
The strength parameters, durability, workability, and other properties of M30 grade concrete made specifically using magnetized water and silica sand as a substitute for potable water and river sand are discussed and the results from the various tests conducted on “Magnetized water concrete” and “Non-magnetized water concrete” are obtained.
The following conclusions are made based on the analysis:
1. The magnetization method has been effectively used, and the impact will endure for three hours in the water sample.
2. Silica sand concrete exhibited an average 10% increase in compressive strength when compared to conventional concrete. The addition of magnetized water and silica sand to the concrete resulted in an average of 20% increase in compressive strength.
3. In comparison to conventional concrete, silica sand concrete has shown a 3% increase in split tensile strength.
4. The use of magnetized water and Silica sand in concrete has been shown to improve the mix's quality.
5. The amount of additives and water demand decreased by 5%,
6. The slump value of all concrete mixes made with magnetized water increased by 10% on average,
7. 25% replacement of silica sand resulted in the highest slump value of a 20% increase.
LIST OF ABBREVIATIONS
OPC | = Ordinary Portland Cement |
AFS | = American Foundry Society |
W/C | = Water-cement |
AVAILABILITY OF DATA AND MATERIALS
The data is available with the corresponding author [P.P], on request from the reader the data will be shared.