All published articles of this journal are available on ScienceDirect.
Compressive Strength of Chipped Rubber Aggregate Concrete: A Review
Abstract
Concrete is a widely used material for construction; therefore, it is necessary to identify materials that are economical, environmentally friendly, easily available, and prevent environmental damage while sourcing the materials, hence this is the aim of this study. The current study’s objective is to have a comprehensive study on the previous research identifying the effects of chipped rubber as concrete coarse aggregate and the compressive strength (ƒc) of the concrete and to identify areas of relevance for better sustainability to reduce the rate of waste rubber and degradation of the environment. To achieve the objectives of this study, a review of previous research works was conducted and analyzed. A comprehensive study on the ƒc of chipped rubber coarse aggregate concrete (RCAC) was studied by reviewing previous research. The addition of chipped rubber in concrete to a specific ratio can enhance or reduce the concrete ƒc. But a reduction in the rubber concrete’s ƒc can be seen when the rubber content ratio exceeded 20%. When the chipped tyre rubber is treated with coupling agents, an increase in the concrete ƒc can be seen. The use of chipped rubber in concrete production reduces environmental degradation and proves as a step toward the sustainable development goal (SDG). Chipped RCAC mixtures are weaker than regular concrete mixtures. RCAC, on the other hand, is more ductile and has a better energy dissipation pattern. The ƒc of concrete was found to be affected by substituting concrete aggregates with rubber.
1. INTRODUCTION
Presently, sustainability is a significant concern around the world, and cement and concrete technology has an impact on it. The construction sector, especially cement and concrete, is mainly accountable for 7% of total global CO2 emissions. Concrete competence of sustainable construction is distinguished by the use of industrial wastes to reduce the consumption of natural resources and energy, as well as environmental pollution. Sustainable concrete is more environmentally friendly due to the replacement of materials over nominal concrete.
The land is required for concrete construction. Materials for construction activities (aggregates, cement, waters, admixtures, etc.) sourced from quarry sites and borrow pits may result in the wholesale elimination of vegetation and vir-gin materials. It can also result in the displacement of populations and the loss of vital ecological resources and biodiversity on a national, regional, or global scale. Based on the foregoing, it became necessary to investigate and review the use of waste materials as concrete coarse aggregates to reduce the risks associated with natural coarse aggregate production and quarrying.
The aggregate manufacturing process has numerous significant environmental impacts. The most significant environmental impact of stone, aggregate, and mineral mining is air pollution caused by airborne emissions from both stack and disturbed areas at these mines. Natural aggregate deposit sources are being depleted, posing a threat to the environment and society. The rapid depletion of natural aggregates from source beds causes a variety of issues, including the loss of water-retaining strata, bank slides, exposure of water supply scheme intake wells, and decreasing underground water table levels, all of which cause negative agricultural effects and aquatic life disturbances.
A wide range of waste materials is thought to be feasible and even valuable additives for concrete. Among these are cellulose, fly ash, silica fumes, and wood particles. Rubber obtained from scrapped tyres is the most recent waste material studied due to its critical use in the construction field [1].
Rubber is an essential material used in many industrial sectors. An example of this sector is vehicle manufacturing, where the rubber is used in many applications like vehicle rubber tyres. Due to the high increase in automobile production from the manufacturers, the number of tyres being produced has increased rapidly, which led to the increase of waste tyres generated. Tyres are often split into two categories: truck tyres and automotive tyres, both of which are distinct from one another. More so, it affects the texture and shape of the concrete, as well as the properties of the concrete that are altered by adding a specific percentage of rubber. Considering the increase in the demand for concrete for construction, it became necessary to identify alternatives to concrete natural coarse aggregates for sustainability which will lead to a reduction in the demand for these natural coarse aggregates. It is also worth stating that the quantities of the basic mixture’s components vary between truck and car tyres, not just in design, size, and weight. Many of these tyres are only disposed of in landfills without treatment.
Up to ninety percent of mortars and concrete are made of aggregates which affect their qualities and properties [2, 3].
Disposal of waste tyres in landfills occupies a large land area. There is a pressing need for the disposal of waste tyres in a beneficial and environmentally friendly manner [4]. The number of tyres disposed of in landfills can be minimized by using the rubber content in the waste tyres to produce concrete by partial or full replacement of the concrete fine or coarse aggregate after the waste tyre rubber must have undergone some cleaning processes. Rubberized concrete mix is produced by the incorporation of rubber into the concrete mix [5, 6].
For many years, attempts by material scientists have been made to make concrete ductile. Because of the brittle nature of concrete, it appears that integrating natural tensile ductility into the material is the most basic and practical method for creating damage-tolerant concrete structures.
There have been several studies on the incorporation of rubber into concrete mixes, the results of which have shown that rubber incorporation can affect some of the concrete’s properties like sound absorption, energy dissipation, and ductility.
Depending on the size of the crumb rubber, the rubber can be utilized as an alternative aggregate in concrete mixes as:
(i) Coarse aggregate: In this type, tyres are prepared in two stages. In the first stage, rubber is cut to obtain pieces with a length of 100 to 230 mm, and in the second stage, rubber is produced in grains with a size of 13 to 76 mm, which can replace concrete coarse aggregates.
(ii) Fine aggregate: This rubber crumb type requires mills with special requirements at different temperatures since these two factors control the size of the produced grains, which range from 0.425-4.75 mm.
(iii) A partial cement replacement [7-14]: The size of grains of this type of rubber varies from 0.075 mm - 0.475 mm. To reduce grains’ size, a micro-milling process is required.
Every year, each person in the United States discards an average of one car tyre. This means that the United States, with a population of roughly 300 million people, must dispose of approximately 300 million tyres per year [15-17]. In the last few years, several novel applications for these tyres have emerged. Tyre-derived fuel for boilers and cement kilns [15] and tyre-derived aggregates for civil engineering projects [17] are two examples. However, not all tyres are disposed of in this manner. The remaining scrap tyres are disposed of using a variety of legal and illicit techniques (disposal of tyres in unpermitted areas).
Three different types of used tyres for concrete mix design have been investigated by Researchers investigated:
- Powdered Rubber: The rubber particles are less than 1 mm in diameter and are made up of crunch powder that has fallen from the waste rubber processing plant's machinery. Because of its size, this sort of rubber might be utilized as a concrete filler.
- Crumb Rubber: Rubber particles are highly irregular, ranging in size from 3 to 10 millimeters, and can be utilized to substitute fine aggregates.
- Chipped Rubber: This type of rubber is 25–30 mm in size and can be utilized to replace coarse particles in concrete.
In the last three decades, increasing attention has been paid to the use of tyre products as full or partial replacement natural concrete aggregates [18-24]. The implementation of rubber concrete in construction can minimize dependence on mineral aggregates, leading to sustainable construction in our environment. Existing studies have found that replacing natural aggregates with tyre rubber in concrete production can cause a decrease in concrete compressive strength (ƒc) [20]; the percentage reduction in strength compared to natural aggregate concrete (NAC) depends on the replacement ratio and gradation of rubber aggregates and can reach 85%. Based on test results, some studies [18, 20, 21, 23] concluded that:
(i) The ratio of aggregates to be replaced in rubber concrete should not be more than 10% of the total number of aggregates by volume (hereinafter in this article, the replacement ratio is specified by volume, unless otherwise specified) to avoid/reduce the negative impact on the strength of the rubber concrete; and (ii) compared to using tyre crumb rubber (sizes 10 mm to 76 mm) to replace coarse aggregates, and crumb rubber (sizes 0.425 mm to 4.75 mm) to replace small aggregates may result in less reduction in concrete strength at the same replacement ratio.
It is necessary to identify that some other studies [7, 25] reported a slight increase in the strength of rubber concrete at a relatively low replacement rate of aggregates with rubber particles (for example, less than 2.5% of the total amount of aggregates), which may be due to the optimization of the gradation of aggregates of such rubber concrete.
Concrete buildings with greater serviceability and safety can be easily obtained if the concrete behaves in tension like steel (extremely ductile) whilst preserving all other benefits (e.g., extreme, and high (ƒc).
The researchers [26] investigated the dynamic properties of rubberized concrete material. Due to the rubber's particular elasticity properties, rubberized concrete showed substantial advantages in decreasing or restricting vibration and impact effects.
The physicomechanical parameters of rubberized concrete with a 20 MPa initial ƒc have been studied [18]. In the rubberized concrete, rubber was used in 15%, 30%, and 45% of the total aggregates. The ƒc of rubberized concrete has generally reduced, according to the findings.
Rubberized concrete [13] could be used in the following situations:
- In places where vibration dampening is necessary, such as railway stations and machinery foundation pads.
- Pile heads, paving slabs, trench filling, and pipe bedding.
- In barriers, railway buffers, and bunkers, where blast or resistance to impact is required.
Gupta et al. [27, 28] investigated the impact of mixing micro silica and waste rubber on concrete mix properties. The impact resistance of concrete has also been investigated when fine particles were replaced with waste rubber fibers and the addition of silica fume with cement [29].
An experiment on rubberized concrete was carried out in the research work [19]. The study looked at the ƒc and flexural strengths (ƒf), as well as the impact resistance of rubberized concrete with various crumb rubber volumes.
Gravel, limestone, and granite are the commonly known sources of crushed stone, which are expensive, and not all countries have their deposits [30]. Therefore, in the bid to address the issue of sustainability that meets the United Nations Sustainable Development Goal (SDG), this paper reviews the effects of rubber in concrete as an aggregate to the ƒc of a concrete structural member. There is no detailed compiled extensive work on the subject of ƒc of rubber concrete structural elements; therefore, this review paper utilized the research of previous researchers on similar or close topics to analyze the effect of chipped rubber in concrete on ƒc of rubber concrete.
2. UNDERSTANDING SOME OF THE RUBBER CONCRETE AGGREGATED AND PREVIOUS WORKS ON RUBBER CONCRETE
This paper was prepared by a comprehensive review of works done by previous researchers, which paved the way for indebt understanding of the subject matter. The materials looked out for in the concrete mixes of the rubber concretes reviewed are as follows:
2.1. Expected Materials for Rubber Coarse Aggregate Concrete
To achieve the objective of this paper, the use of certain materials for concrete mixes was considered. Based on these materials, the results summarised and analyzed in the result section of this paper were obtained. The operational properties of concrete aggregates are determined by the chemical and mineral compositions, as well as water and frost resistance. Important characteristics of concrete aggregates also include the shape of grains, the nature of the surface, chemical composition, structure as well as economic indicators. The materials are discussed below as follows:
- Cement. Cement is an artificial inorganic hydraulic binder that is one of the main building materials. It forms a plastic mass when interacting with water, aqueous solutions of salts, and other liquids, which then hardens and turns into a stone-like body. Cement is mainly used for making concrete and mortars and it can gain strength in wet conditions, which is fundamentally different from some other mineral binders - (air lime), which harden only in the air. Cement is the main binder that coats the aggregate, developing a good bonding between them, thereby inducing the strength characteristics of previous concrete.
- Granites (Coarse aggregate). Granite (Fig. 1) is the material traditionally used in the construction of monuments. It is one of the hardest and most durable substances. It can withstand extreme weather conditions, which is one of the main reasons granites are used in the construction of monuments [31]. The chemical composition of granite is illustrated in Table 1.
- Chipped rubber (Coarse aggregate). The recycling of tyre aggregates (Fig. 2) includes several stages, such as a mechanical system (making small pieces), a cryogenic system (methods for cutting rubber into small pieces), removal of steel fiber (SF) stage, a screening and grinding step, and a cleaning step. During the cleaning step, the rubber particles are thoroughly cleaned with water and other cleaning agents such as ammonia solution, citric acid, etc. Based on the application, three categories of rubber are used in concrete: crushed or chipped tyres (size 12-50 mm), ground or powdered rubber (0.425-2 mm), and granular or crumb rubber (0.425-12 mm). In terms of chemical composition, tyre rubber granules contain more than 90% styrene-butadiene rubber (SBR) and carbon black, as well as a small amount of oxidized zinc and sulfur [34]. The weight loss of rubber at various temperatures was also investigated [34], and it was found that at temperatures of 40-125°C, 325-435°C, and 470-525°C, the weight loss is about 2, 35 and 55.3%, respectively. The specific gravity and elongation of rubber can reach 0.9–1.16 g/cm3 and 420%, respectively [35, 36]. The stiffness modulus of shred rubber tyre ranges from 0.47 to 2.7 MPa and depends on the direction of the load [37]. The percentage of rubber aggregates used in cement materials also varies from a minimum of 5% to a maximum of 100% [38, 39].
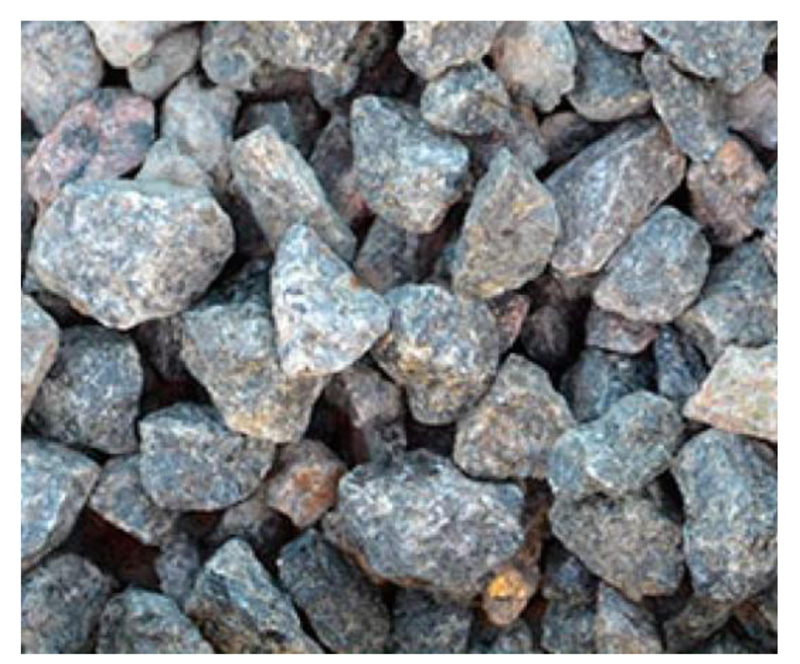
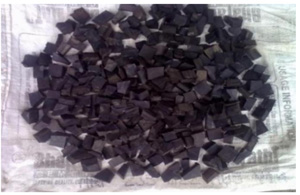
Waste tyre rubber is reduced in size or torn apart in the cracker mill process by being passed between spinning corrugated steel drums. This procedure creates particles of various sizes and shapes. The categorization of rubber waste tyres is illustrated in Table 2.
- Sand (Fine aggregate). Fine aggregates are natural sand particles from the land through the mining process, the fine aggregates consist of natural sand or any crushed stone particles that are ¼” or smaller. This product is often referred to as ¼”minus as it refers to the size, or grading, of this aggregate. Aggregates less than 4.75 mm in size are called fine aggregates; sand falls under fine aggregate [40]. Table 3 shows the chemical composition of the sand type called quartz sand which has been used as a fine aggregate for concrete by many researchers.
- Water. Tap or portable drinking water is widely used in a concrete mix. Clean portable water, free from suspended particles, chemical substances, biological elements, etc., is used both for mixing concrete and curing [42].
2.2. Review on the Compressive Strength (ƒc) of Rubber Coarse Aggregate Concrete
The research [20] used rubber to replace coarse or fine aggregate. In the research, the ratios for aggregate replacement were 25, 50, 75, and 100 percent. In the concrete mix, Edgar chips used were of 19-, 25-, and 38-mm sizes. They used Preston rubber that passed through a 2 mm sieve to replace fine aggregate. To produce the specimens for testing, over 200 cylinders with a diameter of 150 mm and a height of 300 mm were used. The analysis reported that utilizing the rubber as a substitute for coarse aggregate caused a loss in tensile strength (ƒt) by 50% and the ƒc by 85%, depending on the rubber content percentage. Whilst there was a 65% drop in ƒc when fine concrete aggregate was substituted with rubber. On the other hand, the concrete mixture showed a higher ability to absorb energy under tensile and compressive loads. Similarly, two rubber concrete mixes were studied [43]; the first contained fine rubber particles and the second - large rubber particles. In the results an ƒc loss of up to 50% was shown depending on the percentage of rubber compared to the control specimen mix.
According to the literature [21], when the rubber concentration in the concrete mix increased, the strength of the mix dropped. The research showed that the rubber quantity must be at most 20% of the total aggregate volume as, over this portion, a high decrease in the concrete strength was noticed.
In a study [44], rubberized concrete was obtained by replacing 15% of the volume of coarse aggregate with rubber in the form of two phases: tyre fibers and chips. The results illustrated a decrease in strength and stiffness; however, impact strength and crack resistance were improved. At peak load, the control concrete failed, while the deformation of the rubber concrete was significant without complete failure. The results illustrated that the rubber concrete with rubber fiber exhibited a lower stress concentration than with chipped rubber, indicating the ability of the rubber fiber mixture to withstand higher loads than with chipped rubber.
The use of crumb rubber to produce rubberized concrete mix has been conducted [45]. The study declared that for every 50 Ibs of rubber addition, the unit weight was reduced by nearly 6 pcf. They stated that incorporating rubber into the concrete mix decreased the strength and one of the reasons for this was the rise in air cavities inside the concrete mix when the rubber component was raised. The research illustrated that this effect could be minimized by including a de-airing material in the concrete mixer.
Table 1.
Name | SiO2 | Al2O3 | K2O | Na2O | CaO | FeO | Fe2O3 | MgO | TiO2 | P2O5 | |
---|---|---|---|---|---|---|---|---|---|---|---|
Percentage | 72.04% | 14.42% | 4.12% | 3.69% | 1.82% | 1.68% | 1.22% | 0.71% | 0.30% | 0.12% |
Type | Size | Application in Concrete |
---|---|---|
Shredded/chipped | Shredded Stage (1) Length: 300mm-430 mm Width: 100mm-230mm Stage (2) Length: 100mm-150mm Chip 13mm- 76mm |
Gravel replacement |
Crumb rubber | 0.425mm- 4.75mm | Sand replacement |
Ground rubber | 0.0075mm- 0.475mm | Cement replacement |
Fiber rubber | Length: 8.5mm-21.5mm | Reinforced fiber |
Fe2O3 | Al2O3 | SiO2 | CaO | K2O | MgO | Na2O | PP |
---|---|---|---|---|---|---|---|
0.07 | 0.67 | 98.9 | 0.33 | 0.025 | 0.21 | 0.08 | 0.44 |
Some factors that controlled rubberized concrete's loss in ƒc were outlined [7]. The first factor was the soft cement paste around rubber particles which caused quick cracks propagation around rubber particles during load application. The second factor was the lack of bond between cement paste and rubber compared to cement paste and natural aggregate. The third factor was the ƒc of the mix depending on the properties of the materials composing the mix. So, replacing one material with rubber particles reduced the overall l ƒc. The absence of a bond between the rubber and other materials was the fourth factor. In addition to the low specific gravity of rubber, rubber particles moved upward during the concrete mix's vibrating. The composition of the top layer in such a case would have a high concentration of rubber particles that reduced the ƒc because of the non-homogenous concrete mix.
Rubberized concrete mixed with and without coated rubber has been studied [46]. They elucidated that rubberized concrete mix using coated rubber with a silane coupling agent exhibited higher ƒc than without coated rubber because of the increased bond between rubber and cement due to rubber's improved interface.
The sizes, percentages in concrete, and varied surface textures of rubber particles were found to have a substantial impact on concrete strength qualities in numerous experiments. The ƒc is often reduced more when coarse aggregates are substituted with rubber than when fine aggregates are replaced [47-52]. The strength and efficient energy absorption of concrete containing coarse rubber particles are reduced [23]. It was discovered that substituting scrap tyre rubber for less than 5% of the volume of natural aggregates has no effect on the material's performance [26]. ƒc deteriorates more than bending and tensile strength [8, 53-55].
Another important issue with rubber concrete is the early cracking within the concrete due to the lack of proper bonding between the rubber and the paste matrix [7]. Due to the above demerits of rubber concrete, it has so far been mainly limited to non-structural applications in practice (e.g., landfills, and road bases).
Prior studies have shown that the mechanical properties of concrete change dramatically when tyre rubber is added to the mix due to the weak adhesion between both the rubber particles and the cement paste. Many researchers discovered that as the percentage of rubber aggregate increased, ƒc, flexural strength (ƒc), unit weight, and so on decreased. The size, shape, and surface textures of the aggregate, as well as the volume used, influence the compressive and tensile strength of rubberized concrete [56].
2.2.1. Treatment of Chipped Rubber for Chipped Rubber Coarse Aggregate Concrete
The research [5] studied the use of NaOH solution in the treatment of rubber is so valuable, especially in the case of using tyre rubber, not manufactured rubber particles. Their results showed an increase in the bond strength between rubber and cement, which led to an enhancement in strength.
Pre-treatment on the rubber particles, either natural or chemical, can be utilized to promote adhesion between the rubber particles and the cement matrix, increasing the ƒc of rubber create [5, 8, 26, 49, 54, 55, 57]. According to multiple studies [57, 58], rubber particles washed in water increased compressive strength by 16 percent compared to untreated rubber, whereas rubber particles treated with carbon tetrachloride increased ƒc much more (by more than 57 percent).
2.2.2. Adaptability and Impact Strength
The research [59] examined the toughness of a control concrete mixture and waste tyre rubber mixtures with 5 percent and 10 percent buff rubber by volume of coarse aggregate. Toughness is also known as energy absorption capacity and is typically defined as the area under the load-deflection curve of a flexural specimen. According to their findings, the two waste tyre rubber mixes were more durable than the control concrete mixture. However, due to the reduction in ƒc, the toughness of the waste tyre rubber mixture with 10% buff rubber (2 to 6 mm) was less than that of the waste tyre rubber mixture with 5% buff rubber. Based on their research into the utilization of rubber shreds, which came in two nominally different diameters (5.5 mm to 1.2 mm and 10.8 mm), 1.2 mm and 10.8 mm to 1.8 mm) and granular (about 2mm in diameter) rubber in mortar.
Mortar samples containing rubber shreds were able to sustain extra stress after the peak load [60]. Due to rubber shreds bridging cracks, the specimens did not break into two pieces underneath the failure flexural strain; however, specimens manufactured with granular rubber particles broke into two pieces at the failure load. This suggests that using rubber shreds rather than granular rubber tended to improve post-crack strength.
According to the literature [21], waste tyre rubber samples typically fail progressively as rubber content rises, and the failure mode shape of the test sample can be either conical or columnar (conical failure is gradual, whereas columnar is less of a collapse of shreds with two sizes that are, nominally, 5.5 mm to 1.2 mm and 10.8 mm to 1.8 mm (length diameter)). The samples exhibited elastic deformations at a rubber content of 60% by total aggregate volume, which the specimens retained after unloading.
Though research [61] suggested using rubberized concrete where vibration dampening was necessary, a study [62] discovered that when the rubber content increased, the dynamic modulus of elasticity and rigidity dropped, suggesting a much less rigid and less flexible material. They also noted that it appeared that concrete's dampening capacity—a measure of the material's power to reduce the amplitude of free vibrations within its body—seemed to decline with an increase in rubber content.
Compared to conventional concrete, rubberized concrete has been found to have better impact resistance and hardness [63-65]. While investigation [66] investigated the use of various percentages of rubber in concrete (5%, 10%, and 15%) by volume, it was discovered that as rubber content was increased, ƒc decreased.
A study was carried out on the performance of concretes with the same volume replacement of rubber wastes, which confirmed the decrease in ƒc [67]. A waste rubber volume of 15% results in a 50% decrease in ƒc. These researchers reported that low-dimension rubber waste results in lower strength loss and that rubber modification processes (mechanical grinding or cryogenic process) do not affect ƒc.
According to one study [68], concretes with a waste rubber volume of 15% have a 48.3% decrease in ƒc. While [7] confirmed the decrease in ƒc as rubber content increased. However, when 5% chipped rubber replaced the coarse aggregates, the ƒc increased slightly, most likely due to the better grading of the mixture.
2.2.3. Fiber Reinforced Chipped Rubber Coarse Aggregate Concrete
The behavior between fiber-reinforced polymer (FRP)-confined NAC and FRP-confined rubber concrete (FCRC) was compared in the research [25], and found that the enhancement of the ƒc of rubber concrete (with a replacement ratio of total aggregates being 7%) caused by the FRP confinement was approximately 30% higher than that of the corresponding FRP-confined NAC. The strength reduction of FCRC caused by the replacement of aggregates with crumb rubber was approximately 50% lower than that of unconfined rubber concrete with the same replacement ratio.
The study [69] conducted four tests on FCRC cylinders and reported that FCRC has higher confinement effectiveness and ductility than the corresponding FRP-confined NAC. A series of compression tests in which rubber concrete with a single replacement ratio was confined by carbon FRP was presented in a study [67], and research [68] also presented compression tests on six FCRC cylinders with a single replacement ratio. Both studies [70, 71] have again demonstrated the beneficial effects of FRP 90 confinement on the behavior of rubber concrete.
According to several investigations [18, 21], combining rubber aggregate with coarser grading resulted in greater losses in ƒc than the aggregate with a finer grain. However, several researchers have discovered the opposite pattern [13, 72].
Several researchers have reported that the incorporation of fiber-reinforced polymer (FRP) composites as reinforced concrete (RC) structural member external constraint can enhance both the axial strength and the deformation capacity of structural members [73, 74]. Naturally, one would expect the use of FRP composites in confining rubber concrete to have a similar effect mentioned above by reducing the weaknesses of rubberized concrete when used together in an FRP confining tube. Thus, the resulting FCRC columns, equipped with additional longitudinal reinforcement, have great potential for a wide range of structural applications of rubber concrete. In these FCRC columns, the FRP tubes also serve as corrosion-resistant concrete pouring molds, resulting in superior durability and lower construction costs. Therefore, FCRC columns are an attractive alternative to traditional bridge abutments and RC piles in harsh environments [75].
Another component of rubber tyres that can also be used in concrete production is steel wire. The steel wire, when recycled, produces steel fiber (SF). The SF is an economical alternative to industrial fiber for concrete. When compared to traditional concrete, recycled steel fiber reinforced concrete (SFRC) performs comparably to industrial SFRC, with improved ƒc, tensile strength (ƒc), and post-cracking behavior. Other research utilizing rubber and/or SF is available [76-81].
2.2.4. Sustainability Chipped Rubber Coarse Aggregate Concrete
Over half of the tyres that are changed each year, according to estimates, end up in landfills. By 2030, it is anticipated that 5 billion tyres will have to be replaced globally. Concrete made with tyre trash can assist to lessen some of its negative environmental effects [82].
Amongst the most important metrics for measuring environmental effects is carbon dioxide (CO2) footprint, which has a significant impact on the expansion of sustainable development. CO2 emission by each component over its life cycle was measured and advised in codes and other research for the construction industry [83].
All people are concerned about the effects that the proliferation of landfills for used tyres has on the environment. In addition to destroying the aesthetic appeal of cities, the storage of scrap tyre mounds in landfills creates an unsanitary environment where mosquitoes and other insects that spread various diseases can breed. Tyre disposal results in environmental hazards. Burning used tyres, a once-common method of trash management, results in emissions that put human health and the ozone layer in danger. Rubber tyre waste dumping in landfills is prohibited in several nations [84].
Among the advantageous characteristics of tyre chips [85], are their low density, high: thermal insulation, bulk permeability, durability, and bulk compressibility. Waste tyre chips are a less expensive option as concrete aggregate substitute other concrete coarse aggregates. An option that has been utilized with success is crumbly rubber. aggregate source for Portland cement and asphalt concrete (PCC).
3. BOND AT INTERFACIAL TRANSITION ZONE (ITZ)
Concrete waste is one of the major construction-related wastes produced during the demolition of old structures. In 2014, the United Kingdom generated 58 million tons of concrete waste. Similarly, China generates 0.2 billion tons of concrete waste each year [86]. Several researchers investigated the properties of recycled aggregate concrete (RAC) (concrete containing concrete waste) [87-89]. However, RAC showed a greater reduction in peak strength and modulus of elasticity than conventional concrete [90, 91]. The highly permeable adhered mortar of recycled aggregates (RA) and the higher amount of ITZ in RAC are responsible for the poor performance of RAC [92]. The ITZ is the region of cement paste at the aggregate boundary [86]. The increased ITZ in RAC is due to the old ITZ between the aggregate and the old, adhered mortar of RA, as well as the new interfacial transition zone between RA and new cement paste [93].
The ITZ bond between recycled rubber and its composite matrix is determined by the chemical and physical properties of both components. Mechanical coupling, molecular bonding, and thermodynamic adhesion are all methods of bonding. Physical, mechanical, and chemical interactions between aggregate and matrix occur during these processes. The physical and mechanical interactions are primarily determined by the roughness of the aggregate surface and the adsorption of voids. Chemical bonding, on the other hand, is based on molecular interactions such as dipole-dipole interactions, Van der Waals forces, and chemical interactions between the rubber and the composite matrix [94].
It is difficult to achieve a good bond in rubber composites. Rubber-binder adhesion is affected by the surface properties of the rubber aggregate, such as roughness, polarity, chemical composition, and surface free energy [95]. Contaminants at the ITZ interface can reduce adhesion as well [96]. On the microstructural scale, rubber is a cross-linked polymer with very low permeability and smooth surfaces [94]. As the polymer and filler fill the microstructure, the surface and interfacial region ranges are very small, typically over one polymer chain and with a radius of gyration of the order of 3-30 nm. Poor adhesion may result from the recycled rubber's low surface free energy and lack of polar functional groups [94] However, after recycling, the rubber surface chains remain a part of the cross-linked structure. The recycled rubber chains cannot be reactivated to achieve continuity or bonding with the matrix. As a result, even when polymers of the same composition are vulcanized, weak interfacial adhesion develops between binder and rubber aggregate [95].
4. COMPARISONS OF SOME EARLIER REVIEWS
Table 4 shows results from some of the previous works. It is seen that the addition of chipped rubber reduced the ƒc of the rubber concrete.
5. DISCUSSION
Most countries have problems with recycling rubber tyres. Even when recycled for use or reproduction, the emission produced is very harmful to living things. The use of waste rubber tyres in concrete as concrete has, in many ways, solved environmental problems. The quarrying of natural coarse aggregates has a much negative impact on ecology, therefore, the use of waste rubber reduces the increasing use of natural coarse aggregate, thereby minimizing the dumping of waste tyres and burning of waste tyres.
Economically, cheaper production of concrete is achieved by using chipped waste rubber tyres as concrete aggregate. Lightweight concrete can be achieved by using rubber tyre as concrete aggregate.
S/n | Ref. | Samples | Concrete Constituents Aggregates | ƒc, MPa | |||||
---|---|---|---|---|---|---|---|---|---|
Cement, Kg/m3 |
Sand, Kg/m3 |
Water | Coarse Aggregate | Curing Period, days | |||||
Chipped Rubber Kg/m3 | Granite, Kg/m3 |
7 | 14 | ||||||
1. | [53] | 447 | 629 | 214 | - | 1116 | 35 | ||
2. | [58] | sc | 5.6 | 6.72 | 2.52 | - | 15.12 | 20 | 30.9 |
Scr5 | 5.6 | 6.72 | 2.52 | 0.76 | 14.36 | 16.8 | 28.5 | ||
Scr10 | 5.6 | 6.72 | 2.52 | 1.52 | 13.6 | 15 | 23.8 | ||
Scr15 | 5.6 | 6.72 | 2.52 | 2.34 | 13.18 | 12.6 | 19.1 |
The use of chipped waste rubber tyres in concrete has a good strength impact in concrete when incorporated at specific percentages. Chipped waste rubber tyres with rough surfaces have increased bonding strength with concrete and other concrete additives and reinforcement fibers.
Comparing waste rubber tyre and other by-products, the recycling processes of other by-products are more intense as the collection of waste tyres are easily accessible and from the waste tyres, not only is the rubber valued in concrete production but the steel fibers in the tyres are used for concrete reinforcement.
CONCLUSION
In this paper, a comprehensive review on the ƒc of rubber Crete was done, and the following conclusions were drawn:
1 Increasing the quantity of rubber in the concrete mix leads to a decrease in the concrete density, and this density loss is greatly increased in the case of powdered rubber. Due to the reduction in density, rubber concrete can be referred to as lightweight concrete and be produced for many applications based on requirements.
2 When compared to normal concrete mixes, rubber concrete has a lower ƒc but when the fiber is added to the mix of rubber concrete at a specific ratio, an enhanced ƒc can be seen. If the substitution of total concrete aggregate quantity with rubber does not surpass 20%, the decrease in ƒc can be tolerated. Above this aggregate ratio, a high reduction in the ƒc is noticed.
3 Tyre rubber for concrete aggregate treated with any coupling agents can lead to a reduction in the loss of ƒc.
4 The use of tyre rubber in concrete can usher in a friendly environment to encourage the United Nations Sustainable Development Goal as the crude methods of discarding these waste automobile tyres (burning, landfill, discarding in rivers, bushes, and roadsides) will be prevented.
5 A few more researchers suggest that concrete with waste tyre rubber chips as aggregates has a higher energy-absorbing capacity known as toughness.
LIST OF ABBREVIATIONS
RCAC | = Rubber Coarse Aggregate Concrete |
SDG | = Sustainable Development Goal |
CONSENT FOR PUBLICATION
Not applicable.
FUNDING
This paper did not receive any funding neither did any of the authors.
CONFLICT OF INTEREST
The authors declare no conflict of interest, financial or otherwise.
ACKNOWLEDGEMENTS
Declared none.