All published articles of this journal are available on ScienceDirect.
Mechanical Properties of Mortar with Anadara Granosa Waste as Partial Sand Replacement
Abstract
Introduction:
In order to create a cleaner and more sustainable environment, cockle shell waste created from the local fisheries trade is used to produce construction materials, which meet the needs of a developing sustainable construction sector. The use of cockle shell waste as construction materials can help both the environment and the community. Though, the use of this waste as a partial replacement for fine aggregate (sand) in mortar has received little attention.
Aims:
the current study aims to investigate the influence of Anadara granosa (cockle shell) as a fine aggregate substitute on the mechanical properties of mortar namely compressive strength, flexural strength, and dynamic modulus elasticity.
Methods:
In this study, the cockle shell is crushed to fine particles and then integrated as fine aggregate replacement in various ratios of 10, 20, 30, and 40%.
Results:
The result indicated that integrating 10% crushed cockle shell into mortar enhances its compressive strength, flexural strength, and modulus elasticity when compared to the control mortar.
Conclusion:
Conclusively, success in utilizing cockle shells as sand in mortar can help to reduce environmental problems and produce sustainable construction material.
1. INTRODUCTION
Generally, cockles or also known as Anadara granosa [1], are a type of bivalve shellfish that grows well in a muddy coastal environment. The most common natural spat production throughout the year is on the west coast of Peninsular Malaysia in Selangor and Perak [2]. Malaysia’s cockle production is projected to rise in 2025, with production reaching 150,000 metric tonnes [3]. Cockleshell is a food-based solid waste and the shells are known to be waste with no economic value and mostly dumped in landfills without prior treatment [4]. Mohamed, Yusup, & Maitra [5], have cautioned that the increasing amount of cockles available will contribute to the increasing amount of discarded shells. This situation will lead to several problems that can have detrimental effects on the environment and society as cockle shell wastes that are dumped and left untreated will likely cause a foul odour and unpleasant view of the surroundings [6, 7]. A large-scale of amount of cockle shells waste can result in the opening of more widespread waste disposal areas. These issues may have a detrimental effect on the quality of life of those living in the vicinity of these areas and contribute to environmental pollution [8].
Many scientists, engineers, and doctors have recently focused their attention on blood cockle shell waste as a better deal of aragonite calcium carbonate (CaCO3) [9]. Cockle shells contain 95-99% CaCO3, which can be used as a filler in concrete [10]. In the civil engineering field, research has explored the potential use of cockle shells as cement coarse and fine aggregate in concrete. Othman, Bakar, Johari, and Don [11], has investigated the influence of cockle shell ash as cement replacement in concrete. They found that the compressive strength and flexural strength of concrete decreased when cockle shell ash was used as cement replacement. Meanwhile, Ramakrishna and Sateesh [12] studied the effect of cockle shells as mixing ingredients in concrete. They concluded that the substitution of natural coarse aggregate with crushed cockle shell with 25% crushed cockle shell resulted in an enhancement in compressive strength.
In the past, investigation on the effect of using crushed cockle shells as sand replacement in water-cured cement-based construction material has also been carried out by researchers from South-East Asian countries. Earlier, Ab Wahab & Hassan [13], reported that the inclusion of a 2% crushed cockle shell with an average size of 0.07 mm as a sand replacement reduces the compressive strength of concrete. On the other hand, a few researchers Muthusamy et al. [14] and Mat Aris et al. [15] have reported the use of a suitable percentage of crushed cockle as sand replacement increases the strength performance of concrete. Mat Aris et al. [15] also discovered that incorporating up to 20% crushed cockle shell as sand replacement contributes to the strength enhancement of lightweight aggregate concrete. Another researcher, Sainudin et al. [16], recently reported that combining 10% crushed cockle shell with a size passing sieve of 2 mm as sand replacement increases the compressive strength of water-cured cement brick.
Extensive literature and research reports only discuss the effects of cockle shells on the short-term compressive strength of concrete when curing in water. Clearly, there is little research on the performance of air-cured mortar containing crushed cockle shells as sand replacement. Therefore, the attentiveness on the effect of employing cockle shells as a partial sand replacement on the compressive strength, flexural strength, and dynamic modulus elasticity of mortar subjected to air curing in tropical climate countries is looked for.
2. MATERIALS AND METHODS
2.1. Materials
Four main ingredients were used in this study to produce the mortar specimen which were Ordinary Portland Cement (OPC), water, sand, and cockle shells. River sand with a passing sieve size of 1.18 mm was used as fine aggregate. The fineness modulus, moisture content, specific gravity, water absorption, and bulk density of the river sand employed in this investigation were 2.99, 1.00%, 2.71, 1.25%, and 1475 kg/m3, respectively. For the cockle shells (CS), the waste was collected from a dump site. The CS was treated before being used as sand replacement. First, the CS was washed with water to remove any undesirable particles. Then, the CS was oven-dried for 24 hours at 105 ±5 °C. After that, a crusher machine was used to crush the CS. A crushed cockle shell (CCS) was then sieved until it had a passing size of 2.36 mm. The physical properties of CCS were also investigated. The fineness modulus, moisture content, specific gravity, water absorption, and bulk density of CCS were 4.26, 0.73%, 2.91, 3.24%, and 1545 kg/m3, respectively. Fig. (1) illustrated the river sand and cockle shells used in this study.
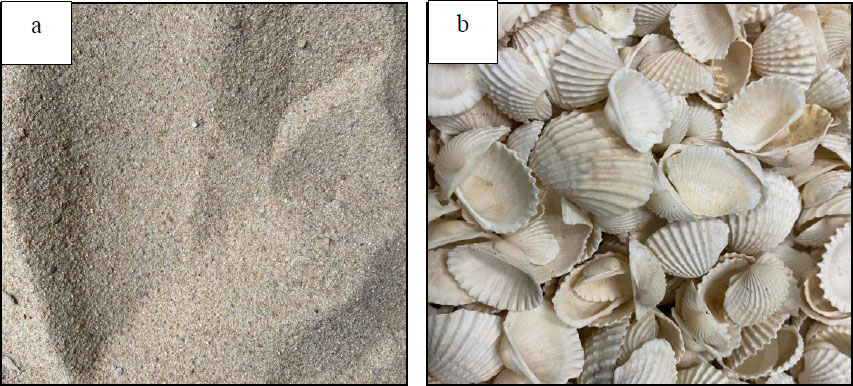
Mixes | Cement | Water | Sand | Cockle shell |
---|---|---|---|---|
C0 | 240 | 163 | 550 | 0 |
C10 | 240 | 163 | 495 | 55 |
C20 | 240 | 163 | 440 | 110 |
C30 | 240 | 163 | 385 | 165 |
C40 | 240 | 163 | 330 | 220 |
2.2. Mix Proportions
The mix proportions utilized in this investigation are displayed in Table 1. The mix comes in five different ratios: C0, C10, C20, C30, and C40. The fine aggregate in C0 was formed entirely of river sand. CCS was substituted for sand in the amounts of 10%, 20%, 30%, and 40% to create C10, C20, C30, and C40.
2.3. Testing Methods
The compressive strength test and flexural strength test were conducted in compliance with ASTM C109 [17], and ASTM C348 [18]. While, for the dynamic elasticity modulus, ultrasonic pulse velocity (UPV) testing was used in accordance with ASTM C 597-09 [19]. The calculation for dynamic elastic modulus was based on the suggestions made by Safi et al. [20]. In this study, cubes each sized (50 x 50 x 50) mm3, and prisms each sized (40 x 40 x 160) mm3, were made. Air curing was used for curing the specimens. Then, the specimens were tested at 7, 28, 60, and 90 days of mortar age.
The experimental results were statistically analyzed using Design Expert 7.0 software to establish the possible relationship between factors and response used. The response surface methodology (RSM) model was used to validate the projected data against the actual data acquired. A 3D graph and equation can be generated using historical data analysis. The ANOVA regression yields the relationship between factors and response.
3. RESULTS AND DISCUSSION
3.1. Compressive strength
The finding for the compressive strength of mortars containing CCS as partial sand replacement for 7, 28, 60, and 90 days of age are shown in Fig. (2). According to the graph, the compressive strength for mortar with 0% CCS recorded the highest strength at 7 days, and the strength decreased as the percentage of CCS increased. However, at 28, 60 and 90 days of age, mortar specimens with CCS exhibited higher compressive strengths compared to control mortar. The use of coarser CCS than sand may result in an improvement in mortar strength. Varhen et al. [21] also reported that coarser crushed seashells may enhance the mechanical properties of concrete. Mortar specimens containing 10% CCS as a sand replacement had the highest strength value at 28, 60, and 90 days when compared to other series of CCS mortar. However, excessive cockle shell replacement reduces concrete strength. Evidently, in this study, it was found that all series of mortars with CCS have met the target strength (15 MPa) at 28 days, with the strength ranging from 17.52 MPa to 22.21 MPa for air-cured mortars. Furthermore, as curing time increased, the compressive strength of mortar with various percentages of CCS increased. The compressive strength improved with longer curing ages due to the continuous formation of calcium silicate hydrate (CSH) gel product [22].
3.2. Flexural strength
Fig. (3) depicts the flexural strength of all mortar specimens at 7, 28, 60, and 90 days. It was found that the strength of the control mortar and a series of mortars incorporating CCS increased as the curing time increased. These findings show that CCS affected the flexural strength of the mortar. Flexural strength decreased steadily after 7 days as the percentage of CCS used as sand replacement increased, with values of 6.40, 6.34,6.17, 6.13, and 5.89 MPa for mortars containing 0, 10, 20, 30, and 40% CCS, respectively. At 28 days, the strength of the CCS-containing mortar was higher than that of the control mortar. Mortars containing 10, 20, 30, and 40% CCS had values ranging from 6.85 to 6.62 MPa, compared to 6.43 MPa for the control mortar. Nonetheless, the mortar mix containing 10% CCS had the highest flexural strength value at 28, 60, and 90 days of curing age. Similar to compressive strength results, an excessive percentage of CCS replacement can reduce the strength. This may be due to the properties of CCS higher in water absorption compared to rived sand can reduce the strength. Panda, Behera, and Jena [23] also reported that crushed seashell has a larger water absorption capacity than natural fine aggregates affecting their strength as well.
3.3. Dynamic Modulus Elasticity
The results on the dynamic elastic modulus of control mortar and CCS-mortars cured at 7, 28, 60, and 90 days are presented. The results of dynamic elastic modulus on CCS mortar specimens are shown in Fig. (4). Overall, the CCS affected the dynamic modulus of elasticity of the mortar. It is also realized that the mortar containing 10% CCS had exhibited the greatest dynamic elastic modulus as demonstrated for compressive and flexural strength. This may be due to the presence of 10% crushed cockle shells contributing to the densification of the mortar's interior structure. Furthermore, the dynamic elastic modulus value would improve as the curing age increased. However, in comparison to each age, the increment can be fairly slight. In terms of the relationship between compressive strength and dynamic modulus elasticity, Apostolopoulou, Bakolas, and Kotsainas [24] stated that mortars with higher compressive strength values would have a higher dynamic modulus of elasticity values, this is tied to the pore network structure of the mortar; a more compact system would result in a greater compressive strength but a less ductile material.
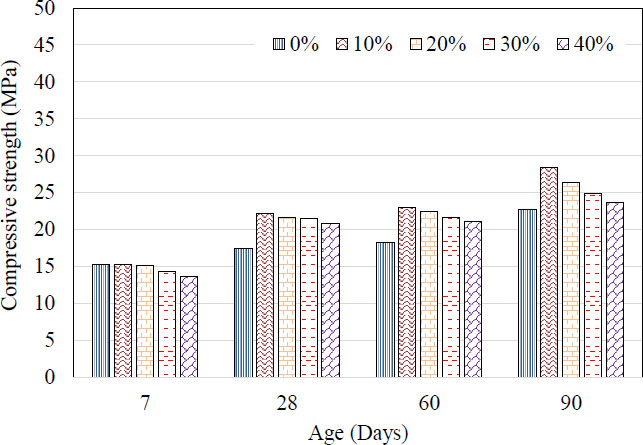
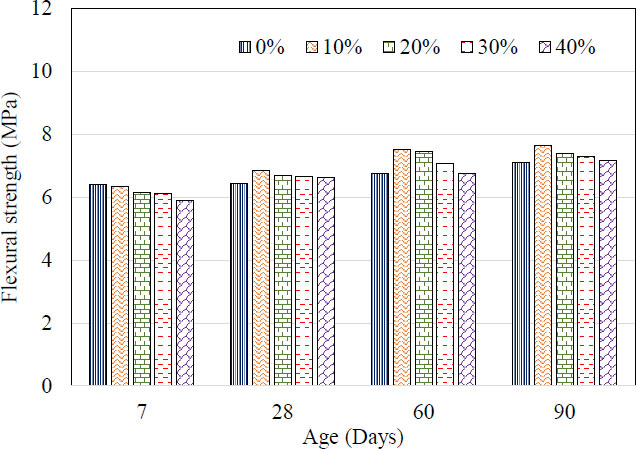
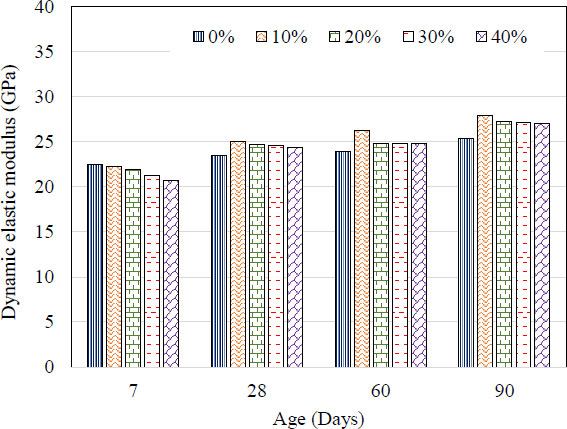
4. RESPONSE SURFACE METHODOLOGY (RSM) MODEL
4.1. Relationship between crushed cockle shell content and curing age on the compressive strength of CCS mortar using RSM
Fig. (5) illustrates each response surface plot relationship between the two factors, namely, curing age and CCS content, and the effects on compressive strength (i.e., response) for CCS mortars. The cubic equation as suggested by the RSM model would be the best fit for maximizing the relationships. The plots indicated that as the curing age increased, the compressive strength also increased. Longer curing time would allow a better hydration process, which then would aid in concrete densification and load-bearing capability. However, it became clear that as the CCS content in mortar increased, the compressive strength decreased. The surface plots also revealed that the inclusion of 10% CCS in the mortar enhanced the strength performance when compared to the control mortar and the other mortars containing 20%, 30%, and 40% CCS.
The regression models in the ANOVA provided evidence that the compressive strength of the mortar with CCS was significantly affected by the curing age and the alteration in the CCS content as can be seen presented in the following Table 2 for CCS mortar.
The significant value (p-value) reflects the degree of significance for a hypothesis test [25]. From the ANOVA, the p-value obtained was p < 0.01, indicating that the model was significant. The p-value also indicated that the model was statistically significant at a significance level of p < 0.5 [26]. If the p-value was more than 0.05, the model would then not be significant [27]. The results of the regression analysis also proved that the cubic relationship between compressive strength and the two variables was strong where R2 is 0.982. A high R2 value nearing one (1) would be recommended while an acceptable adjusted R2 agreement would be required [28].
Models | SD | R2 | Predicted R2 | p Value | Remarks |
---|---|---|---|---|---|
Linear | 2.18 | 0.77 | 0.686 | <0.0001 | - |
Quadratic | 2.04 | 0.835 | 0.678 | 0.1056 | - |
Cubic | 0.79 | 0.982 | 0.882 | <0.0001 | Suggested |
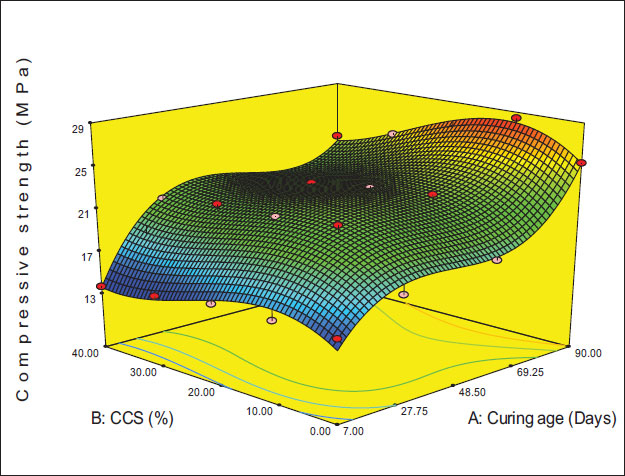
4.2. Relationship between crushed cockle shell content and curing age on the flexural strength of CCS mortar using RSM
Secondly, the relationship between the different percentage levels of CCS content and curing age for CCS mortar, and its effect on the flexural strength was examined in the present study. It was evident that the quadratic equation for air-cured mortar as suggested by the RSM model would be the best fit for maximizing the relationships (Table 3). Fig. (6) illustrates each response surface plot relationship between the two factors, namely, curing age and CCS content, and the effects on flexural strength for CCS mortars. The surface plots indicated that the flexural strength of CCS mortar increased when the curing age increased. This is because when the curing period was prolonged, the hydration process improved. Nevertheless, the flexural strength of mortar containing CCS as sand replacement became reduced when the percentage level of the content exceeded 10%. When compared to the control mortar and the other mortars with 20, 30, and 40% percentage levels of CCS content, as can be seen in the illustration of the surface plots, it was evident that substitution of 10% CCS as sand replacement in mortar enhanced the flexural strength performance.
Meanwhile, the results of the ANOVA provided evidence that the flexural strength of CCS mortar was significantly influenced by curing age and percentage levels of the CCS content as sand replacement. As presented in Table 3, the p-value obtained was p < 0.01, indicating that the model was statistically significant. The model likewise exhibited a significant relationship between flexural strength and the two factors, with R2 being found to be 0.897.
4.3. Relationship between crushed cockle shell content and curing age, on the dynamic modulus elastic of CCS mortar using RSM
Last but not least, the influence of varying levels of percentage of CCS content and curing age on the dynamic elastic modulus of CCS mortar was also examined in the present study. Fig. (7) illustrates each response surface plot relationship between the two factors, namely curing age and CCS content, and the effects on dynamic elastic modulus for CCS mortars. The cubic equation, as suggested by RSM, was the best fit for optimizing the relationship for CCS mortars. The surface plots provided evidence of the influence of curing age in enhancing the dynamic modulus of elasticity for CCS mortar. In other words, the modulus of dynamic elasticity increased when the curing age was prolonged. In addition, the longer the curing age, the better the hydration process of mortar. Nevertheless, when CCS was used as a substitute for sand, the dynamic modulus of elasticity dropped as the level of percentage of the CCS content was increased to 20%. It was evident as can be seen from the illustrated surface plots that substituting the sand with 10% CCS in mortar improved the modulus of dynamic elasticity performance in comparison to the control mortar and the other mortars with 20, 30, and 40% CCS content.
Models | SD | R2 | Predicted R2 | p Value | Remarks |
---|---|---|---|---|---|
Linear | 0.25 | 0.773 | 0.686 | <0.0001 | - |
Quadratic | 0.19 | 0.897 | 0.777 | 0.0045 | Suggested |
Cubic | 0.16 | 0.944 | 0.609 | 0.157 | - |
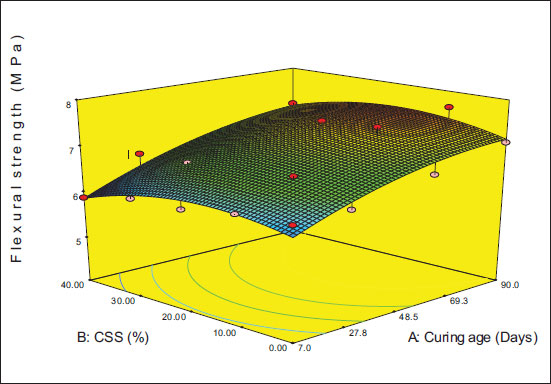
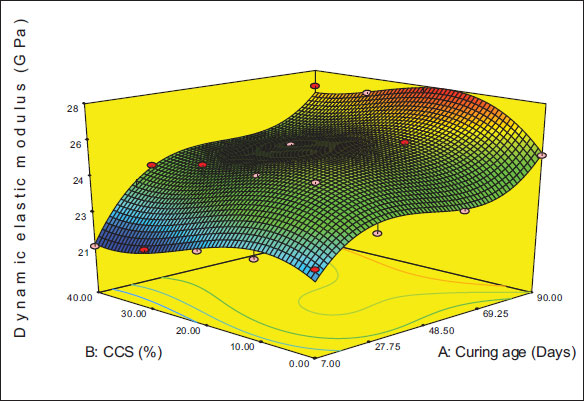
Models | SD | R2 | Predicted R2 | p Value | Remarks |
---|---|---|---|---|---|
Linear | 1 | 1 | 0.659 | <0.0001 | - |
Quadratic | 1 | 1 | 0.723 | 0.0596 | - |
Cubic | 1 | 1 | 0.798 | 0.0021 | Suggested |
The ANOVA results revealed that the curing age and CCS content had a significant impact on the dynamic modulus elasticity of mortars with CCS as sand replacement. The p-value was p < 0.01 as presented in Table 4, indicating that the model was significant. The R2 value obtained was 0.969, and the RSM model revealed a significant relationship between modulus elasticity and those parameters.
CONCLUSION
Air-cured mortar produced by integrating 10% crushed cockle shells contributes to the densification of the internal structure, resulting in the best value for compressive strength, flexural strength, and dynamic modulus elasticity of the hardened material. The prediction model confirmed the significant relationship between curing age and CCS content attributed to compressive strength (CS), flexural strength (FS), and dynamic modulus elasticity (DME) of CCS-mortar. The R2 calculated by RSM revealed a strong relationship between CS, FS, and DME in relation to curing age and CCS content, with a correlation coefficient of 0.982, 0.897, and 0.969, respectively. Success in producing sustainable mortar from the combination of crushed cockle shell waste as a partial fine aggregate replacement would contribute towards lesser seashell waste disposal at dumping areas and a sustainable river environment.
LIST OF ABBREVIATIONS
CS | = Compressive Strength |
FS | = Flexural Strength |
DME | = Dynamic Modulus Elasticity |
CSH | = Calcium Silicate Hydrate |
CONSENT FOR PUBLICATION
Not applicable.
AVAILABILITY OF DATA AND MATERIAL
The data obtained from the experimental work conducted at the laboratory in Universiti Malaysia Pahang.
FUNDING
This study was funded by Universiti Malaysia Pahang, Funder ID: Internal University Grant, Awards/Grant number: RDU213306.
CONFLICT OF INTEREST
Dr Ramadhansyah Putra Jaya5 is the executive guest editor of The Open Civil Engineering Journal.
ACKNOWLEDGEMENTS
Declared none.